How does PLC control servo motors?
Before answering this question, we must first understand the purpose of servo motors. Compared with ordinary motors, servo motors are mainly used for precise positioning. Therefore, what we usually call servo control is actually the position control of servo motors. In fact, servo motors also have two other working modes, namely speed control and torque control, but they are less used.
Speed control is generally achieved with a frequency converter. Using a servo motor for speed control is generally used for fast acceleration and deceleration or precise speed control, because compared with a frequency converter, a servo motor can reach thousands of revolutions within a few millimeters. Since the servo is closed-loop, the speed is very stable. Torque control mainly controls the output torque of the servo motor, also because the servo motor has a fast response. Applying the above two types of control, the servo drive can be regarded as a frequency converter, which is generally controlled by analog quantity. The most important application of servo motors is positioning control. Position control has two physical quantities to control, namely speed and position. To be precise, it is to control how fast the servo motor reaches where and stop accurately. The servo drive controls the speed and distance of the servo motor by the frequency and number of pulses received. For example, we agree that the servo motor rotates once every 10,000 pulses.
If the PLC sends 10,000 pulses in one minute, the servo motor will complete one circle at a speed of 1r/min. If it sends 10,000 pulses in one second, the servo motor will complete one circle at a speed of 60r/min. Therefore, the PLC controls the servo motor by controlling the pulses sent. Sending pulses in a physical way, that is, using the transistor output of the PLC is the most common way, and low-end PLCs generally use this method. The mid-to-high-end PLC transmits the number and frequency of pulses to the servo drive through communication. For example: Profibus-DP CANopen, MECHATROLINK-II, EtherCAT, etc. These two methods are just different in terms of the channels of implementation, but the essence is the same, and it is the same for our programming. This is what I want to tell you, to learn the principles and apply them to other cases, rather than learning for the sake of learning.
There is a big difference in programming. Japanese PLC uses instructions, while European PLC uses function blocks. But the essence is the same. For example, to control the servo to an absolute positioning, we need to control the PLC output channel, pulse number, pulse frequency, acceleration and deceleration time, and know when the servo driver completes positioning, whether it hits the limit, etc. No matter which PLC, it is nothing more than the control of these physical quantities and the reading of motion parameters, but the implementation methods of different PLCs are different.
How to design a servo system?
Previous article:Causes and solutions for inverter low voltage tripping
Next article:About the maintenance method of PLC external wiring
Recommended ReadingLatest update time:2024-11-16 09:40
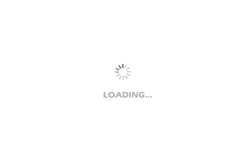
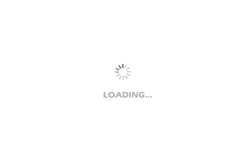
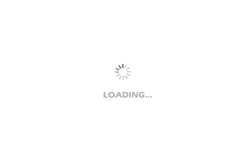
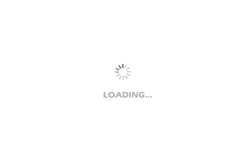
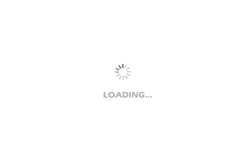
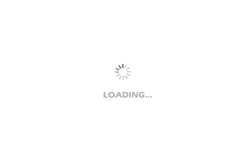
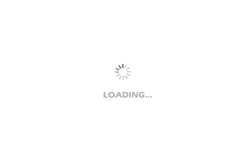
- Popular Resources
- Popular amplifiers
- Huawei's Strategic Department Director Gai Gang: The cumulative installed base of open source Euler operating system exceeds 10 million sets
- Analysis of the application of several common contact parts in high-voltage connectors of new energy vehicles
- Wiring harness durability test and contact voltage drop test method
- Sn-doped CuO nanostructure-based ethanol gas sensor for real-time drunk driving detection in vehicles
- Design considerations for automotive battery wiring harness
- Do you know all the various motors commonly used in automotive electronics?
- What are the functions of the Internet of Vehicles? What are the uses and benefits of the Internet of Vehicles?
- Power Inverter - A critical safety system for electric vehicles
- Analysis of the information security mechanism of AUTOSAR, the automotive embedded software framework
Professor at Beihang University, dedicated to promoting microcontrollers and embedded systems for over 20 years.
- Innolux's intelligent steer-by-wire solution makes cars smarter and safer
- 8051 MCU - Parity Check
- How to efficiently balance the sensitivity of tactile sensing interfaces
- What should I do if the servo motor shakes? What causes the servo motor to shake quickly?
- 【Brushless Motor】Analysis of three-phase BLDC motor and sharing of two popular development boards
- Midea Industrial Technology's subsidiaries Clou Electronics and Hekang New Energy jointly appeared at the Munich Battery Energy Storage Exhibition and Solar Energy Exhibition
- Guoxin Sichen | Application of ferroelectric memory PB85RS2MC in power battery management, with a capacity of 2M
- Analysis of common faults of frequency converter
- In a head-on competition with Qualcomm, what kind of cockpit products has Intel come up with?
- Dalian Rongke's all-vanadium liquid flow battery energy storage equipment industrialization project has entered the sprint stage before production
- Allegro MicroSystems Introduces Advanced Magnetic and Inductive Position Sensing Solutions at Electronica 2024
- Car key in the left hand, liveness detection radar in the right hand, UWB is imperative for cars!
- After a decade of rapid development, domestic CIS has entered the market
- Aegis Dagger Battery + Thor EM-i Super Hybrid, Geely New Energy has thrown out two "king bombs"
- A brief discussion on functional safety - fault, error, and failure
- In the smart car 2.0 cycle, these core industry chains are facing major opportunities!
- The United States and Japan are developing new batteries. CATL faces challenges? How should China's new energy battery industry respond?
- Murata launches high-precision 6-axis inertial sensor for automobiles
- Ford patents pre-charge alarm to help save costs and respond to emergencies
- New real-time microcontroller system from Texas Instruments enables smarter processing in automotive and industrial applications
- MSP430 G2553 Launchpad implements capacitance measurement
- [GD32L233C-START Review] 12. Button - External Interrupt
- [Qinheng RISC-V core CH582] Environment configuration and lighting test
- Design and implementation of image cropping circuit based on FPGA
- MSP430 Launchpad MSP430g2452 SHT10 Temperature and Humidity Sensor
- Establishment of RF chip/modem chip design team
- F28335 uses external SRAM for program simulation
- Looking for experts in Helmholtz coil magnetic field
- How to use the VGA_SYNC_N signal in the VGA of DE1-SOC?
- CCS Tips: Remove the prompt when burning DSP/BIOS