Control system design is a basic skill that every industrial control engineer must master, and IO inventory, which we often call point counting, is the first task to be done.
The number of control system points is usually provided by the design institute. The system points are the sum of the instrument I/O points, electrical I/O points and the communication points between the control system and other systems. Accurately counting the electrical and instrument I/O points can avoid the problem of inconsistent coordination between the electrical and instrument professions. Accurate system points can provide a basis for the user to decide on the control system brand and system cost.
Control systems usually involve automated control contents such as thermal detection, analog control, sequential control and logical control. The points are obtained from the statistical results of five aspects: AI analog input points, AO analog output points, DI switch input points, DO switch output points and the communication points between the control system and other systems.
1. How to calculate the AI input points of the automatic control system
AI refers to the analog input signal entering the control system. AI input signals that can be directly input into the system from the field include thermocouples (J, K, T, N, E, R, S and B-grade thermocouples), thermal resistance signals (Cu50, Cu100, Pt100 and Pt50-grade), standard current signals (4-20mA, 0-20mA), standard voltage signals (1-5V, 0-5V and 0-10V) and pulse signals; if other forms of signals need to be sent to the system, they must be converted into 4-20mA or 1-5V using signal isolators, current transmitters, voltage transmitters and other signal conversion equipment before being sent to the DCS system.
(1) Statistics of thermocouple AI input points
A single assembled thermocouple or a single armored thermocouple is calculated as one AI point. A double assembled thermocouple or a double armored thermocouple needs to be calculated as two AI points if the system displays the two sensor temperatures of the same measuring point, and calculated as one AI point if only one temperature of the measuring point is displayed. A single multi-point thermocouple or a multi-point thermocouple is often used to monitor the temperature of different parts of the same measuring point. If the thermocouple has several measuring points, the AI input of several thermocouples is calculated.
(2) Statistics of thermal resistor AI input points
The statistical method for the number of thermal resistor AI input points is the same as that for the number of thermocouple AI input points.
(3) Statistics of standard current and voltage AI input points
Each 4-20mA, 0-2mA, 0-5V, 1-5V or 0-10V signal sent into the system is counted as one AI point, and the corresponding range of the input signal is counted at the same time. Since two-wire transmitters (including temperature transmitters, pressure transmitters, level transmitters, flow transmitters, etc.) involve DC24V power supply, it is best to count the AI points separately to facilitate system integration wiring.
Special note: Field instruments such as pressure gauges, bimetallic thermometers, glass rotor flow meters, etc. displayed on site are not included in the system point calculation.
2. How to calculate AO output points
AO refers to the analog output signal of the control system that controls the on-site execution equipment. AO output generally has five types: 4-20mA, 0-20mA, 0-5V, 1-5V and 0-10V. 4-20mA is the most commonly used AO output of DCS system. AO output is usually connected to electric actuators, pneumatic actuators, frequency converters, power regulators and industrial control modules. Usually, each controlled object corresponds to one AO output, and the number of AO output points is the same as the number of controlled devices.
3. How to calculate the DI input points
DI refers to the switch input signal entering the control system. DI input must be a passive contact, TTL or CMOS level signal. After DI enters the DCS system or PLC, it is usually connected to DC24V or DC48V query voltage.
The professional DI input of the instrument usually comes from the alarm contacts of on-site electric contact pressure gauges, electric contact bimetallic thermometers, electric contact water level gauges, liquid level switches, flow switches, flame detection, electric contact water level gauges and other instruments. Each alarm contact is calculated as a point DI input when connected to the system.
4. How to calculate DO output points
DO refers to the switch output signal of the control system that controls the field equipment, which is usually connected to other electrical equipment of different voltage levels through an intermediate relay. Instrument professional DO output is often used to control external indicator lights, solenoid valves, sound and light alarms, electrical controls and multi-turn electric actuators, contactors and other equipment.
The number of DO output points required for the system to control different devices is different. The following are the I/O points of common controlled objects:
(1) Switch type electric actuator: Each actuator has one AI input point for valve position feedback 4-20mA, two DO output points for valve forward/reverse control, two DI input points for valve open position/valve closed position signal, and two DI input points for valve open over torque/close over torque fault signal.
(2) Switch-type multi-turn electric actuator (AC380V power supply): For each actuator, the valve position feedback 4-20mA is calculated as 1 AI input point (if there is no feedback signal, the AI point is not calculated), the valve forward/reverse control is calculated as 2 DO output points, the valve open position/valve closed position (limit switch) is calculated as 2 DI input points, and the actuator over-torque/over-torque fault signal is calculated as 2 DI input points.
(3) Modulating electric actuators: Each actuator valve position feedback calculates 1 AI input point, valve control signal calculates 1 AO output point, and actuator fault alarm signal calculates 1 AI input point (fault alarms are common in intelligent electric actuators. If there is no fault alarm signal, the AI points are not calculated)
(4) Modulating multi-turn electric actuator: For each actuator, the valve position feedback is calculated as 1 AI input point, the actuator 4-20mA control signal is calculated as 1 AO output point, the ESD emergency control signal is calculated as 1 DO output point (ESD emergency control signals are common in intelligent multi-turn electric actuators. If this function is not available, the DO point is not calculated), and the opening torque/closing torque alarm signal is calculated as 2 DI input points.
(5) Inverter: Each inverter frequency feedback calculates 1 AI input point, the frequency given signal calculates 1 AO output point, the run/stop given command calculates 1 DO output point, the inverter fault alarm calculates 1 DI input point, the fault reset calculates 1 DO output point, and the inverter operation status calculates 1 DI input point.
If the inverter is connected to the DCS system via communication, only one communication point needs to be calculated, and no other points need to be calculated.
(6) If the system is connected to external devices such as solenoid valves, indicator lights, contactors, etc., calculate 1 DO output point for each device (if multiple devices share a control signal, it is usually accomplished by adding intermediate relay contacts, and only 1 DO output needs to be calculated).
5. How to calculate the control system points in electrical engineering
(1) System points of conventional electrical control
The simplest motor control circuit requires 2 DI input points and 1 DO output point. Each circuit operation status (from the contactor auxiliary contact) calculates 1 DI input point, the start/stop control signal (connected to the contactor coil) calculates 1 DO output point, and the fault signal (from the thermal relay or motor protector overload signal) calculates 1 DI input point.
If the motor circuit requires current display and local/remote control, in addition to calculating 2 DIs and 1 DO, the current signal (from the current transmitter) calculates 0-3 AI input points (small power motors usually do not need to monitor current, so the AI input points are not calculated; high power three-phase motors have several phase currents that need to be sent to the DCS for display, so several AI input points are calculated. Each 0-5A current signal must be converted into a 4-20mA signal through a current transmitter and sent to the control system, up to 3 points); if the motor needs to be controlled in multiple locations, the control location selection switch calculates 1 DI input.
To facilitate your understanding, the following figure is the electrical secondary control schematic diagram of the GGD electrical cabinet, field operation box and control system.
Functional description of the motor control secondary circuit: The stop button on the electrical cabinet and on-site operation box can stop the motor in any state; the control location selection switch can select "this cabinet control", "on-site control" and "automatic control", and the start button in the corresponding position of the selection switch can start the motor; when the selection switch is in "automatic control", the motor start/stop operation can be performed on the system.
Description of electrical components: In the secondary schematic diagram, 1SS is the stop button on the electrical cabinet, and 1SS1 is the stop button on the on-site operation box; 1SB is the start button on the electrical cabinet, and 1SB1 is the start button on the on-site operation box; DO is the system start/stop control output contact; 1HR5 is the power indicator light; 1HR is the run indicator light on the electrical cabinet, and 1HR1 is the run indicator light on the on-site operation box; 1HG is the stop indicator light on the electrical cabinet, and 1HR1 is the stop indicator light on the on-site operation box; 1KK is the operating ground switch; 1KH is a thermal relay; 1KM is a contactor; 1KA is an intermediate relay; 1FU is a secondary circuit fuse.
Previous article:SCADA, DCS and PLC in one article
Next article:Siemens S7-1200PLC with parameter programming and without parameter programming
Recommended ReadingLatest update time:2024-11-16 09:50
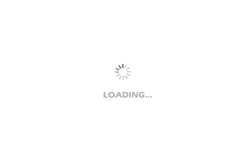
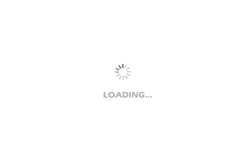
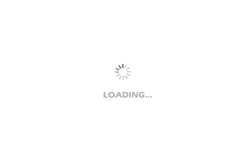
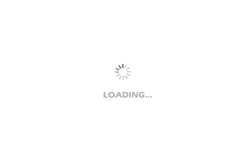
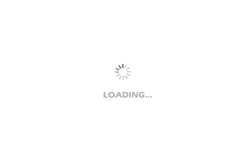
- Popular Resources
- Popular amplifiers
- Huawei's Strategic Department Director Gai Gang: The cumulative installed base of open source Euler operating system exceeds 10 million sets
- Analysis of the application of several common contact parts in high-voltage connectors of new energy vehicles
- Wiring harness durability test and contact voltage drop test method
- Sn-doped CuO nanostructure-based ethanol gas sensor for real-time drunk driving detection in vehicles
- Design considerations for automotive battery wiring harness
- Do you know all the various motors commonly used in automotive electronics?
- What are the functions of the Internet of Vehicles? What are the uses and benefits of the Internet of Vehicles?
- Power Inverter - A critical safety system for electric vehicles
- Analysis of the information security mechanism of AUTOSAR, the automotive embedded software framework
Professor at Beihang University, dedicated to promoting microcontrollers and embedded systems for over 20 years.
- Innolux's intelligent steer-by-wire solution makes cars smarter and safer
- 8051 MCU - Parity Check
- How to efficiently balance the sensitivity of tactile sensing interfaces
- What should I do if the servo motor shakes? What causes the servo motor to shake quickly?
- 【Brushless Motor】Analysis of three-phase BLDC motor and sharing of two popular development boards
- Midea Industrial Technology's subsidiaries Clou Electronics and Hekang New Energy jointly appeared at the Munich Battery Energy Storage Exhibition and Solar Energy Exhibition
- Guoxin Sichen | Application of ferroelectric memory PB85RS2MC in power battery management, with a capacity of 2M
- Analysis of common faults of frequency converter
- In a head-on competition with Qualcomm, what kind of cockpit products has Intel come up with?
- Dalian Rongke's all-vanadium liquid flow battery energy storage equipment industrialization project has entered the sprint stage before production
- Allegro MicroSystems Introduces Advanced Magnetic and Inductive Position Sensing Solutions at Electronica 2024
- Car key in the left hand, liveness detection radar in the right hand, UWB is imperative for cars!
- After a decade of rapid development, domestic CIS has entered the market
- Aegis Dagger Battery + Thor EM-i Super Hybrid, Geely New Energy has thrown out two "king bombs"
- A brief discussion on functional safety - fault, error, and failure
- In the smart car 2.0 cycle, these core industry chains are facing major opportunities!
- The United States and Japan are developing new batteries. CATL faces challenges? How should China's new energy battery industry respond?
- Murata launches high-precision 6-axis inertial sensor for automobiles
- Ford patents pre-charge alarm to help save costs and respond to emergencies
- New real-time microcontroller system from Texas Instruments enables smarter processing in automotive and industrial applications
- [XMC4800 Relax EtherCAT Kit Review] + Getting started with DAVE, quickly build your own webserver
- Banknote number recognition system based on ARM.pdf
- My knowledge of computers
- [Sipeed LicheeRV 86 Panel Review] 7-Waft Graphical Interface Development Test (Part 2)
- Wifi controlled LED screen
- IIoT opens up more possibilities beyond the factory floor
- Recommended one: [Lingsheng] MCU code automatic generator (automatic programming tool)
- Learning 3D visualization scene hierarchy from scratch (1)
- What are the differences and connections between compilers and integrated development environments?
- [RISC-V MCU CH32V103 Review] ---Advanced Wiki---Practical debugging methods