All controlled variables are converted to DC instead of AC through mathematical transformation. The goal is to independently control torque and flux. There are two methods of field oriented control (FOC):
Direct FOC: The direction of the rotor magnetic field (Rotor flux angle) is directly calculated by the flux observer.
Indirect FOC: The direction of the rotor magnetic field (Rotor flux angle) is obtained indirectly by estimating or measuring the rotor speed and slip.
Vector control requires knowledge of the position of the rotor flux and can be calculated through advanced algorithms using knowledge of the terminal currents and voltages (using a dynamic model of the AC induction motor). However, from an implementation perspective, the demand on computing resources is critical.
Vector control algorithms can be implemented in different ways. Feedforward techniques, model estimation and adaptive control techniques can all be used to enhance response and stability. 3. Vector Control of AC Motors: A Deeper Look At the heart of the vector control algorithm are two important transformations: the Clark transform, the Park transform and their inverse operations. Using the Clark and Park transforms, the rotor current can be controlled to the rotor area. Doing so allows a rotor control system to determine the voltage that should be supplied to the rotor to maximize torque under dynamically changing loads. Clark Transformation: The Clark mathematical transformation modifies a three-phase system into two coordinate systems:
Where Ia and Ib are components of the orthogonal datum planes, and Io is the unimportant homoplanar part
Figure 5: Relationship between three-phase rotor current and rotating reference frame
4. Park transformation: Park mathematical transformation converts a bidirectional static system into a rotating system vector
The two-phase α, β frame representation is calculated by the Clarke transformation and then input to the vector rotation module, where it is rotated by an angle θ to conform to the d, q frame attached to the rotor energy. According to the above formula, the conversion of the angle θ is achieved.
Basic structure of field-oriented vector control of AC motor
The Clarke transformation uses three-phase currents IA, IB and IC, where the currents of IA and IB in the fixed coordinate stator phases are transformed into Isd and Isq, becoming elements in the Park transformation d, q. The currents Isd, Isq and the instantaneous flow angle θ calculated by the motor flux model are used to calculate the electric torque of the AC induction motor.
Figure 6: Basic principle of vector control of AC motor
These derived values are compared with reference values and updated by a PI controller.
Table 1: Comparison of scalar and vector control of electric motors An inherent advantage of vector-based motor control is that the same principle can be used to select the appropriate mathematical model to control various types of AC, PM-AC or BLDC motors respectively.
Vector Control of BLDC Motors
BLDC motors are the main choice for field-oriented vector control. Brushless motors using FOC can achieve higher efficiency, with the highest efficiency reaching 95%, and are also very efficient at high speeds. 1. Stepper motor control
Figure 7 Stepper motor control usually uses bidirectional drive current, and its motor steps are achieved by switching windings in sequence. Usually there are three drive sequences for this stepper motor: ① Single-phase full-step drive: In this mode, its windings are energized in the following order, AB/CD/BA/DC (BA means that the energization of winding AB is in reverse direction). This sequence is called single-phase full-step mode, or wave drive mode. At any one time, only one phase is energized. ② Two-phase full-step drive: In this mode, both phases are energized together, so the rotor is always between two poles. This mode is called two-phase full-step, which is the normal drive sequence for two-pole motors and can output the maximum torque. ③ Half-step mode: This mode combines single-phase stepping and two-phase stepping to energize: single-phase energized, then two-phase energized, then single-phase energized..., so the motor runs in half-step increments. This mode is called half-step mode, and the effective step angle of each excitation of the motor is reduced by half, and its output torque is also lower. All three modes can be used for reverse rotation (counterclockwise), but not in the opposite order. Usually, stepper motors have multiple poles to reduce the step angle, but the number of windings and the drive order remain unchanged. 2. General DC motor control algorithm General motor speed control, especially the motor using two circuits:
Phase angle control
PWM chopping control
① Phase angle control Phase angle control is the simplest method for general motor speed control. The speed is controlled by changing the firing angle of the TRIAC. Phase angle control is a very economical solution, but it is not very efficient and is prone to electromagnetic interference (EMI).
Figure 8: Phase angle control of universal motors Figure 8 shows the mechanism of phase angle control, which is a typical application of TRIAC speed control. The phase shift of the TRIAC gate pulse generates an effective voltage, which produces different motor speeds, and a zero-crossing detection circuit is used to establish a timing reference to delay the gate pulse. ②PWM chopping control PWM control is a more advanced solution for universal motor speed control. In this solution, the power MOSFET or IGBT switches on the high-frequency rectified AC line voltage, thereby generating a time-varying voltage for the motor.
Figure 9: PWM chopping control of a general purpose motor
The switching frequency range is usually 10-20KHz to eliminate noise. This universal motor control method can achieve better current control and better EMI performance, therefore, higher efficiency.
Previous article:EV Drive Motor Insulation System 800V EV Motor Insulation System Challenges
Next article:Which type of electric motor is widely used in industrial production?
Recommended ReadingLatest update time:2024-11-16 17:55
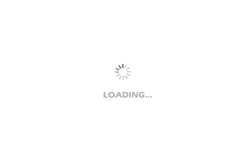
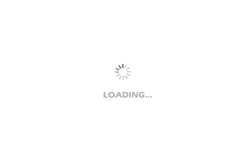
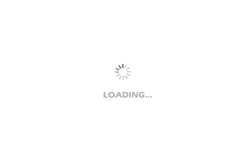
- Huawei's Strategic Department Director Gai Gang: The cumulative installed base of open source Euler operating system exceeds 10 million sets
- Analysis of the application of several common contact parts in high-voltage connectors of new energy vehicles
- Wiring harness durability test and contact voltage drop test method
- Sn-doped CuO nanostructure-based ethanol gas sensor for real-time drunk driving detection in vehicles
- Design considerations for automotive battery wiring harness
- Do you know all the various motors commonly used in automotive electronics?
- What are the functions of the Internet of Vehicles? What are the uses and benefits of the Internet of Vehicles?
- Power Inverter - A critical safety system for electric vehicles
- Analysis of the information security mechanism of AUTOSAR, the automotive embedded software framework
Professor at Beihang University, dedicated to promoting microcontrollers and embedded systems for over 20 years.
- Innolux's intelligent steer-by-wire solution makes cars smarter and safer
- 8051 MCU - Parity Check
- How to efficiently balance the sensitivity of tactile sensing interfaces
- What should I do if the servo motor shakes? What causes the servo motor to shake quickly?
- 【Brushless Motor】Analysis of three-phase BLDC motor and sharing of two popular development boards
- Midea Industrial Technology's subsidiaries Clou Electronics and Hekang New Energy jointly appeared at the Munich Battery Energy Storage Exhibition and Solar Energy Exhibition
- Guoxin Sichen | Application of ferroelectric memory PB85RS2MC in power battery management, with a capacity of 2M
- Analysis of common faults of frequency converter
- In a head-on competition with Qualcomm, what kind of cockpit products has Intel come up with?
- Dalian Rongke's all-vanadium liquid flow battery energy storage equipment industrialization project has entered the sprint stage before production
- Allegro MicroSystems Introduces Advanced Magnetic and Inductive Position Sensing Solutions at Electronica 2024
- Car key in the left hand, liveness detection radar in the right hand, UWB is imperative for cars!
- After a decade of rapid development, domestic CIS has entered the market
- Aegis Dagger Battery + Thor EM-i Super Hybrid, Geely New Energy has thrown out two "king bombs"
- A brief discussion on functional safety - fault, error, and failure
- In the smart car 2.0 cycle, these core industry chains are facing major opportunities!
- The United States and Japan are developing new batteries. CATL faces challenges? How should China's new energy battery industry respond?
- Murata launches high-precision 6-axis inertial sensor for automobiles
- Ford patents pre-charge alarm to help save costs and respond to emergencies
- New real-time microcontroller system from Texas Instruments enables smarter processing in automotive and industrial applications
- During the STM32 hardware simulation debugging process, the system stops at a certain point and does not run further.
- Please help me solve my doubts if you know how to use 6N317 chip
- Morris Chang: China's semiconductor manufacturing lags behind Taiwan by five years
- 【XMC4800 Relax EtherCAT Kit Review】01- Unboxing Photos---Kangaroo Brother
- Isolation and filtering of electromagnetic waves
- Designing Accurate and Versatile Li-ion Battery Testing Solutions
- Find library component modifications
- Please recommend a 485 automatic transceiver chip, 3.3V version.
- Which environment setup tutorial should I watch? -- ESP series development environment setup video navigation directory
- CC2640R2F-Q1 uses low-power Bluetooth technology to transform car access control systems