The Siemens SINAMICS family has a rich product line, as shown in the figure below, from the V series, G series to the S series, with a variety of products to choose from.
V series: V20 and V90, a very cost-effective inverter and servo motor.
G series: G120C, G120, G120X, G120XA, G120D, G130, G150 and other general frequency converters and fan pump frequency converters as well as cabinet frequency converters.
S series: S110, S210, S120 and other mid-to-high-end servo motors.
2 G120 inverter
The G120 inverter is a standard general-purpose inverter in the SINAMICS family. The application model or environment is shown in the figure below. When selecting the G120, be sure to choose a higher power level when starting under heavy load.
The basic components of the G120 inverter are divided into 3 parts, as shown in the figure below.
The basic components of the G120 inverter are divided into 3 parts, as shown in the figure below.
There are two series of power units, PM240-2 and PM250. PM250 has power feedback capability, while PM240-2 does not. PM240-2 has a power range from 0.37Kw to 250Kw, with 7 sizes in total, and a voltage range from single-phase 200V, three-phase 200V, three-phase 380V-480V, and three-phase 500V-690V, which can basically meet most process requirements.
There are many control units to choose from, which can be roughly divided into CU230P-2, CU240E-2, CU240E-2F, and CU250S-2. In terms of communication bus protocols, each of these three types can be divided into three categories, namely Modbus/USS, Profinet, and Profibus (some drives have CAN bus), such as CU240E-2, CU240E-2 PN, CU240E-2 DP, and CU250S-2 CAN.
For the operation panel, there are two types to choose from, BOP-2 and IOP-2. The BOP panel can only display two lines of characters, while the IOP panel can display more and supports switching between Chinese and English. Both panels can be installed on the cabinet door.
3 CU250S-2
For inverters that need to be connected to encoders for closed-loop control, only the CU250S-2 control unit can be selected. The following figure shows the encoder type and interface. The controller has 3 encoder interfaces, one of which is DRIVE-CLiQ, which is a Siemens communication protocol.
1 is that this encoder is used for both position control and speed control;
2 is an encoder for position control, but no encoder for speed control;
3 is one encoder for position control and another encoder for speed control.
4 Debugging Software
G120 can be debugged on TIA software or Starter software. Debugging on TIA requires the starterdrive component plug-in, and the debugging interface is in Chinese. It is more convenient to adjust parameters in starter software, but the interface is in English.
5 Examples
This case takes a horizontal axis of a stacker as an example. The driver of the asynchronous motor is connected to two encoders. One is an incremental encoder at the rear end of the motor, and the other is a laser scale encoder installed on the trolley.
The encoder at the rear end of the motor is used for speed control, and the laser ruler is used as a position control encoder. When configuring the drive, pay attention to several points.
When configuring the drive, be sure to check the basic positioner function. Enabling this function requires authorization. If there is no authorization, the ready indicator on the drive will continue to flash red, but it will not affect the use of this function.
The following IO configuration includes the motor configuration, which can be configured normally. The key point is the configuration of the encoder parameters, because you can configure an encoder for speed control and position respectively. Note that you should check the two encoders, check the first encoder as the motor encoder, and determine which interface the two encoders are connected to. In this case, the 1024-line incremental encoder is on the rear side of the motor.
Click on the detailed parameters of the 1024 encoder and change the absolute value subdivision to 2.
For the position control encoder, this case chooses an AMS 307i laser encoder from Leuze. The principle is shown in the figure below.
We can find in its manual that the encoding is Gray code, 24 bits, resolution 0.1mm, and power supply voltage 18-30V. We fill it into the configuration of the driver encoder 2 according to this parameter.
Then in the mechanical parameter configuration, configure the gear ratio. When configuring the parameters, you need the parameters of the reducer, the parameters of the mechanical wheel and the parameters of the encoder.
After the drive parameters are configured, you can enable, jog, run in speed mode, run in positioning mode, and modify the control loop parameters when necessary in the control panel.
The data exchange between Siemens inverter and Siemens PLC based on Profibus or Profinet communication bus is carried out through messages. There are corresponding messages for speed control and position control. Of course, you can also configure the message format yourself after configuring the free message.
The CU250S-2 controller performs position control and can configure 111 messages. The message contents are as follows.
In actual applications, there is no need for individuals to parse the words or bits in the message. You can use the function block sina_pos developed by Siemens. The block interface provides basic positioning functions such as enable, jog, and positioning.
The position and speed are sent to the inverter via PLC messages, and the inverter can respond to the action to achieve fast and accurate positioning of the trolley.
For stacker or vertical warehouse applications, you can consider using a frequency converter plus an encoder.
Previous article:Comparison of performance characteristics, advantages and disadvantages of three types of compressors: reciprocating, screw and centrifugal
Next article:How to realize forward and reverse rotation of DC motor
Recommended ReadingLatest update time:2024-11-16 16:55
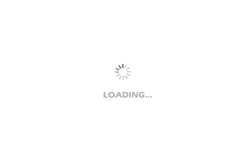
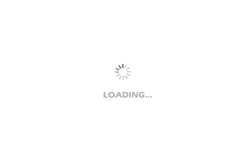
- Huawei's Strategic Department Director Gai Gang: The cumulative installed base of open source Euler operating system exceeds 10 million sets
- Analysis of the application of several common contact parts in high-voltage connectors of new energy vehicles
- Wiring harness durability test and contact voltage drop test method
- Sn-doped CuO nanostructure-based ethanol gas sensor for real-time drunk driving detection in vehicles
- Design considerations for automotive battery wiring harness
- Do you know all the various motors commonly used in automotive electronics?
- What are the functions of the Internet of Vehicles? What are the uses and benefits of the Internet of Vehicles?
- Power Inverter - A critical safety system for electric vehicles
- Analysis of the information security mechanism of AUTOSAR, the automotive embedded software framework
Professor at Beihang University, dedicated to promoting microcontrollers and embedded systems for over 20 years.
- Innolux's intelligent steer-by-wire solution makes cars smarter and safer
- 8051 MCU - Parity Check
- How to efficiently balance the sensitivity of tactile sensing interfaces
- What should I do if the servo motor shakes? What causes the servo motor to shake quickly?
- 【Brushless Motor】Analysis of three-phase BLDC motor and sharing of two popular development boards
- Midea Industrial Technology's subsidiaries Clou Electronics and Hekang New Energy jointly appeared at the Munich Battery Energy Storage Exhibition and Solar Energy Exhibition
- Guoxin Sichen | Application of ferroelectric memory PB85RS2MC in power battery management, with a capacity of 2M
- Analysis of common faults of frequency converter
- In a head-on competition with Qualcomm, what kind of cockpit products has Intel come up with?
- Dalian Rongke's all-vanadium liquid flow battery energy storage equipment industrialization project has entered the sprint stage before production
- Allegro MicroSystems Introduces Advanced Magnetic and Inductive Position Sensing Solutions at Electronica 2024
- Car key in the left hand, liveness detection radar in the right hand, UWB is imperative for cars!
- After a decade of rapid development, domestic CIS has entered the market
- Aegis Dagger Battery + Thor EM-i Super Hybrid, Geely New Energy has thrown out two "king bombs"
- A brief discussion on functional safety - fault, error, and failure
- In the smart car 2.0 cycle, these core industry chains are facing major opportunities!
- The United States and Japan are developing new batteries. CATL faces challenges? How should China's new energy battery industry respond?
- Murata launches high-precision 6-axis inertial sensor for automobiles
- Ford patents pre-charge alarm to help save costs and respond to emergencies
- New real-time microcontroller system from Texas Instruments enables smarter processing in automotive and industrial applications
- About RX62T PWM output problem
- [GD32F310 Review] ADC Configuration and Use
- How to display animation?
- Sinlinx A33 development board Linux kernel waiting queue poll --- blocking and non-blocking
- Embedded Qt-Simple Network Surveillance Camera
- Can miniusb be used?
- Xi'an Sitan Instrument Co., Ltd. Recruitment
- 15% off on NI's popular data acquisition products
- Auto Repair Crankshaft Position Sensor Signal and Waveform Analysis Method - Oscilloscope
- MicroPython Hands-on (27) - WeChat Mini Program for the Internet of Things