What is a brushless motor (also called BLDC)? Before you learn about brushless motors, I think it is necessary to first understand what a motor is.
According to the analysis of the Baidu Encyclopedia entry, "A motor (commonly known as: motor) refers to an electromagnetic device that converts or transmits electrical energy based on the law of electromagnetic induction. It is represented by the letter M in the circuit. Its main function is to generate driving torque as a power source for electrical appliances or various machines." Because of its high efficiency and good operability, motors are currently widely used in various real-life application scenarios such as automobiles, industrial equipment, medical equipment, household appliances (such as air conditioners and refrigerators), electric motorcycles, etc. It can be said that the use of motors is everywhere in our lives. According to the type of motor power supply and the principle of rotation, we can divide motors into the following two categories: DC motors and AC motors
DC motors (direct current motors) can be divided into brushed DC motors and brushless DC motors according to their structure and working principle. According to the waveform of the induced electromotive force inside the motor, the motor can be divided into brushless DC motors (BLDC) and permanent magnet synchronous motors (PMSM).
Brushed motors are traditional products with relatively stable performance. The disadvantage is that the commutator and brushes are in contact, and the service life is very short and requires regular maintenance and renewal. In contrast, brushless DC motors consist of a motor body and a driver, and operate in an automatic control mode. They are better than brushed motors in terms of motor service life and performance efficiency.
From the perspective of current drive, brushless DC motors can be divided into sinusoidal wave drive and square wave drive. Generally, motors driven by square waves are called brushless DC motors (BLDC), and motors driven by sinusoidal waves are permanent magnet synchronous motors (PMSM).
Brushless DC motors have similar basic structures to permanent magnet synchronous motors, and the main difference is that the controller current is driven in a different way.
How does a brushless DC motor (BLDC) work? The "BL" in BLDC motor means "brushless", which means the "brush" in DC motor (brush motor) is gone. The role of brushes in DC motor (brush motor) is to energize the coils in the rotor through the commutator. So how does the BLDC motor without brushes energize the coils in the rotor? It turns out that BLDC motors use permanent magnets as rotors, and there are no coils in the rotor. Since there are no coils in the rotor, there is no need for a commutator and brushes for energizing. Instead, there are coils as stators.
The above is a schematic diagram of the operation of a BLDC motor. Schematic diagram of the operation of a BLDC motor. BLDC motors use permanent magnets as rotors. Since there is no need to energize the rotor, brushes and commutators are not required. The power to the coils is controlled from the outside.
The magnetic field created by the fixed permanent magnets in a DC motor (brushless motor) does not move, and it rotates by controlling the magnetic field generated by the coils (rotors) inside it. The number of revolutions is changed by changing the voltage. The rotor of a BLDC motor is a permanent magnet, and the rotor rotates by changing the direction of the magnetic field generated by the surrounding coils. The rotation of the rotor is controlled by controlling the direction and magnitude of the current to the coils.
Why learn about brushless DC (BLDC) control? DC motors can be designed as brushed or brushless motors, but brushless DC motors (BLDC) are usually the first choice for most applications. Unlike synchronous motors, brushless motors do not require additional loading of the starting winding, and they will not oscillate or lose steps when the load changes suddenly.
BLDC uses electronic commutators to replace carbon brushes, which is more reliable, quieter, more efficient, and has lower power consumption and longer product life. In terms of long-term cost performance, BLDC is the best choice.
In addition, BLDC motors have the following advantages:
1. Good external characteristics, able to output large torque at low speed, so that it can provide large starting torque;
2. Wide speed range, full power operation at any speed;
3. High efficiency and strong overload capacity, making it an excellent performer in the traction system;
4. Good regenerative braking effect, because its rotor is made of permanent magnet material, the motor can enter the generator state during braking;
5. Small size and high power density;
6. No mechanical commutator, fully enclosed structure, can prevent dust from entering the motor, high reliability;
7. Simpler drive control than asynchronous motors.
How is BLDC controlled? The driving mode of brushless DC motor can be divided into multiple driving modes according to different categories, mainly including the following:
1. According to the driving waveform: square wave driving, this driving mode is easy to implement and easy to realize the motor position sensorless control;
2. Sinusoidal driving: This driving mode can improve the motor operation effect and make the output torque uniform, but the implementation process is relatively complicated. At the same time, this method has two modes: SPWM and SVPWM (space vector PWM), and the effect of SVPWM is better than SPWM.
Common BLDC brushless DC motors use non-sinusoidal stator windings, the back electromotive force is trapezoidal, and the generated current is also trapezoidal, so rectangular pulsation will appear, which will lead to low-speed oscillation and generate audio noise. The BLDC control method using sinusoidal waves (that is, permanent magnet synchronous motor) uses sinusoidal current drive to reduce torque pulsation, which is particularly suitable for use in low torque or quiet environments. Therefore, BLDC can also be operated through PMSM sinusoidal vector control.
At present, most of the BLDCs we have seen have relatively unified control methods, mainly using 6 MOSFETs to form a full-bridge circuit, and combined with control circuits and drive circuits. In terms of hardware, it mainly includes the following sections: full-bridge drive circuit, Hall feedback circuit, current sampling circuit, etc. In terms of software implementation, square wave or sine wave (PMSM) control can be used.
How to learn brushless DC motor (BLDC)? Learning motor drive is a very large category. Before learning, you must be familiar with certain analog-to-digital and mixed analog-to-digital circuit foundations, learn basic motor principle knowledge, basic algorithms, and software implementation of controllers. When learning motor control and regulation (electrical regulation), the focus is on learning the current loop and speed loop process design, which involves the use of specific PID regulators and requires mastering PID algorithms. When designing motor speed regulation, what you often learn is sensor algorithm control, and the most commonly used one is sensorless design. You must understand all of the above. Motor control is a difficult industry in embedded systems. If you can have a thorough understanding of motors and master them well, it will still be very popular.
Due to limited space, the following lists some of the knowledge and skills you need to master when learning motors for your reference: 1. Working principle of brushless DC motor (BLDC) I won’t go into detail about this. After all, the most important thing for getting started with each skill is the understanding of the theoretical basic concepts. 2. Learn the difference between BLDC with Hall position sensor and without Hall position sensor①
At present, BLDC with position sensor is more widely used. Because it can accurately sample the rotation position of the rotor, it can operate more stably and reliably, and the control method is relatively simple. Therefore, it is widely used in many projects.
Application field: Especially suitable for large load and static start. For example, electric vehicles, electric bicycles, electric vehicles, high-speed railways, etc. have been widely used. Of course, after all, multiple sensors on the motor increase the complexity and cost of the motor manufacturing process. At the same time, Hall also has a certain probability of aging and other problems, which has a certain impact on the entire life of the motor.
② Due to the above-mentioned disadvantages of the position motor, the positionless motor has a simple process without sensor and is safer and more reliable, so it is also widely used in many occasions.
It is used in some complex and harsh environments and light loads, such as fans, air conditioning compressors, and automotive cooling fans. However, since the position is calculated based on the back electromotive force of the motor, it is unreliable. Moreover, when the motor is stationary, since there is no back electromotive force, the position of the rotor is more difficult to determine. Therefore, it is not suitable for the motor to be used under static conditions.
③ In summary, the driver of the motor with position is relatively simple, the motor is relatively complex, and it can be started at rest. The advantage of the motor without position control is that the motor is simple and the controller is complex. It is suitable for light load, non-zero speed start or start at a certain speed of the motor.
Finally, it is on this basis that we learn the design of the Hall position sensor part.
3. Basic part of motor (motor) control
① The rotor and stator sampling design part of the motor: how to integrate, the working principle and characteristics of the outer rotor and inner rotor, and how to implement the design;
② Understanding of square wave and sine wave. Choose according to the actual or project application. At present, the square wave motor technology is relatively mature, and the sine wave control method is relatively complex, but there is more room for future use, mainly used in high-performance motors.
③ The relationship between voltage, speed, torque and power. Learn the concepts, calculation formulas and mutual relationships of various motor parameters. Such as the relationship between voltage and speed, and the relationship between the current and speed of the motor, efficiency, and how to adjust the speed, etc.
4. How to achieve voltage speed regulation in BLDC Taking the three-phase bldc square wave position sensor motor as an example, we build the driver circuit in a full hardware way.
You need to master the following points:
① Design of three-phase bridge circuit: selection and design of MOSFET; design of MOSFET charging and discharging circuit;
② Selection and explanation of half-bridge drive circuit;
③ Explanation of bootstrap charging circuit: How to realize bootstrap capacitor charging?
④ How to realize complex logic circuit in the front stage of half-bridge drive? It is divided into the following aspects: Ø How to realize motor forward rotation in full hardware? Ø How to stop the motor? Ø How to realize the charging of the self-collecting capacitor? Ø How to realize the commutation of the motor according to the logic signal of the Hall? Ø How to realize the speed regulation of the motor?
5. Motor debugging part. Be familiar with the specific debugging methods and steps of Hall circuit, digital circuit, half-bridge circuit, charging circuit, bridge circuit, motor complete machine, etc.
Previous article:Based on ON Semiconductor's 4KW 650V industrial motor drive solution
Next article:8 Key Factors for Precise Motion Control in Servo Control
Recommended ReadingLatest update time:2024-11-16 11:27
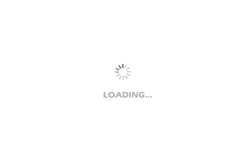
- Huawei's Strategic Department Director Gai Gang: The cumulative installed base of open source Euler operating system exceeds 10 million sets
- Analysis of the application of several common contact parts in high-voltage connectors of new energy vehicles
- Wiring harness durability test and contact voltage drop test method
- Sn-doped CuO nanostructure-based ethanol gas sensor for real-time drunk driving detection in vehicles
- Design considerations for automotive battery wiring harness
- Do you know all the various motors commonly used in automotive electronics?
- What are the functions of the Internet of Vehicles? What are the uses and benefits of the Internet of Vehicles?
- Power Inverter - A critical safety system for electric vehicles
- Analysis of the information security mechanism of AUTOSAR, the automotive embedded software framework
Professor at Beihang University, dedicated to promoting microcontrollers and embedded systems for over 20 years.
- Innolux's intelligent steer-by-wire solution makes cars smarter and safer
- 8051 MCU - Parity Check
- How to efficiently balance the sensitivity of tactile sensing interfaces
- What should I do if the servo motor shakes? What causes the servo motor to shake quickly?
- 【Brushless Motor】Analysis of three-phase BLDC motor and sharing of two popular development boards
- Midea Industrial Technology's subsidiaries Clou Electronics and Hekang New Energy jointly appeared at the Munich Battery Energy Storage Exhibition and Solar Energy Exhibition
- Guoxin Sichen | Application of ferroelectric memory PB85RS2MC in power battery management, with a capacity of 2M
- Analysis of common faults of frequency converter
- In a head-on competition with Qualcomm, what kind of cockpit products has Intel come up with?
- Dalian Rongke's all-vanadium liquid flow battery energy storage equipment industrialization project has entered the sprint stage before production
- Allegro MicroSystems Introduces Advanced Magnetic and Inductive Position Sensing Solutions at Electronica 2024
- Car key in the left hand, liveness detection radar in the right hand, UWB is imperative for cars!
- After a decade of rapid development, domestic CIS has entered the market
- Aegis Dagger Battery + Thor EM-i Super Hybrid, Geely New Energy has thrown out two "king bombs"
- A brief discussion on functional safety - fault, error, and failure
- In the smart car 2.0 cycle, these core industry chains are facing major opportunities!
- The United States and Japan are developing new batteries. CATL faces challenges? How should China's new energy battery industry respond?
- Murata launches high-precision 6-axis inertial sensor for automobiles
- Ford patents pre-charge alarm to help save costs and respond to emergencies
- New real-time microcontroller system from Texas Instruments enables smarter processing in automotive and industrial applications
- Introduction to Intelligent Agents
- Traditional silicon components, silicon carbide (SiC) and gallium nitride (GaN)
- Collection of popular embedded system downloads
- What are the modulation methods of variable frequency power supply?
- This week's highlights
- 3.3V powered half-duplex RS-485 transceiver
- Passive Device Wireless Charging Solution Coil Testing
- DSP System Design-Technical Issues
- 【BLE 5.3 wireless MCU CH582】3. Non-blocking lighting
- CC3200 Kit OURS-SDK-WFB_Exploration2