A common concept in industrial control systems: hard-wired exchange of signals and communication between different devices.
In some large-scale smart factories, one or more large PLCs are usually used to form the processing core. All important equipment needs to be controlled by this unified core. The advantage of doing so is that information can be highly integrated.
So should we use one PLC or multiple PLCs? That depends on the size of the factory. Even a large PLC cannot be used indefinitely. It also has a capacity. If there are too many programs, the response time will naturally be slower, so multiple PLCs are needed to complete the task together.
Or due to some technical reasons or the reasons of the equipment supplier, it is necessary to purchase multiple unrelated devices, which generally have separate processing units, and then transform them to integrate the signals together according to production needs.
If multiple PLCs are used, the question is how to exchange signals between them? There are two general ways:
1. Communications
For example, PROFIBUS, PROFINET, Modbus, free port communication, etc. This is a hardware + software method. Generally speaking, PLCs of the same brand are easier to communicate, but using them requires a certain understanding of PLCs, and the difficulty of getting started is relatively high.
2. Hard-wired signal exchange
The hard wire here does not refer to the hardness or softness of the cable, but it means that it is a little harder than the communication method. The hard wire method has nothing to do with the brand of PLC. The signals of both sides can be transferred through relays. This method does not require software programming, only cables, so the operation coefficient is higher, so it is easier to be accepted by people.
Due to the transformation and upgrading of factory equipment, I debugged and put into production several mobile automation equipment in 2018. The new equipment is a set of auxiliary equipment, which needs to exchange signals with the main equipment. At the beginning of the design, a series of issues such as its maintenance convenience were considered, and the auxiliary equipment needed to be moved, so the exchange signal was made into a hard line + aviation plug, which ran well, but I was always worried about the hard line, fearing that the aviation plug would be damaged due to worker operation errors, resulting in a cable short circuit, and then other problems. Fortunately, the cable and aviation plug were selected with good quality during the design, and there have been no problems in operation for more than half a year.
But after using it for a period of time, due to the overall process upgrade, the equipment needed to be integrated together, which meant that more information needed to be transmitted, including some analog signals, etc., so they considered making the hard wire into Ethernet communication, but unexpectedly, this idea was opposed by many people.
The main equipment uses Siemens S1200, and the auxiliary equipment uses Siemens S7-200smart. Both have Ethernet ports. The transformation only requires removing the hard wires and adding switches. The reason for adding switches is that there are multiple touch screens. Modifying the program and adding S7 communication can change the connection method from hard wires to S7 communication.
However, maintenance engineers and electricians generally do not want this method, the reasons are:
1. Maintenance personnel are generally not very skilled and do not know the principles of communication. They think this method is unsafe and that network cables (even Category 6 cables) do not seem to be as strong as dedicated cables + aviation plugs.
2. Maintenance electricians are accustomed to using multimeters to find faults, and hard-wired cables are visible and tangible, making them more intuitive for maintenance electricians to check.
3. For Internet devices such as switches, some grassroots maintenance personnel feel that these belong to the IT department, so they do not want or are not prepared to take over.
But I think Ethernet connections have the following advantages over hardwired connections:
1. Only one network cable is needed for communication, which is very convenient for maintenance and installation. Hard-wired communication requires connectors, and generally the better quality ones are metal aviation plugs. The cable is welded to the plug, and it is troublesome to repair and replace it after damage. The network cable only needs to replace a finished wire.
2. Since both parties in communication have touch screens, the signals of both parties can be put on the touch screen, and both sides can be clearly displayed, and troubleshooting will not be more troublesome than hard wiring.
3. The communication method is safer than the hard-wired one, because the communication has a protocol. Once the network cable is damaged, etc., the PLC can identify it. The hard-wired one is a separate signal line. Once the signal is short-circuited, the system cannot recognize it.
4. The communication method is easier to integrate the system, which is a necessary condition for integrating existing equipment together, and can also make the overall equipment run more smoothly. Anyone who has done a project knows that there are many ways to integrate two separate devices together. You can simply perform logical processing, but the more perfect solution is deep information exchange, so that information can be exchanged, making the entire production process similar to a system.
5. Compared with hard wiring, communication is a more advanced technology. As time goes by, those who are engaged in technology should strengthen their learning. Therefore, even grassroots maintenance electricians need to learn and enrich themselves.
Finally, under my strong suggestion, I tried to change the first device to Ethernet S7 connection. It ran smoothly for nearly 1 month without any problems. Sometimes, small signal interference will occur in the hard line, so in order to deal with this interference, a software filter was specially added to the program. This invisibly increased the production time and reduced the production efficiency. After changing to Ethernet, not only the stability is guaranteed, but also there is no need to add filtering, which shortens the production cycle and improves production efficiency.
Previous article:Definition and hardware introduction of stepper motor
Next article:PLC/DCS control system interference types and phenomena
Recommended ReadingLatest update time:2024-11-16 12:45
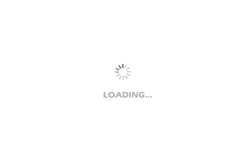
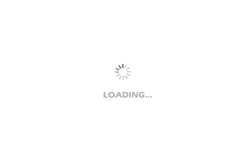
- Popular Resources
- Popular amplifiers
- Huawei's Strategic Department Director Gai Gang: The cumulative installed base of open source Euler operating system exceeds 10 million sets
- Analysis of the application of several common contact parts in high-voltage connectors of new energy vehicles
- Wiring harness durability test and contact voltage drop test method
- Sn-doped CuO nanostructure-based ethanol gas sensor for real-time drunk driving detection in vehicles
- Design considerations for automotive battery wiring harness
- Do you know all the various motors commonly used in automotive electronics?
- What are the functions of the Internet of Vehicles? What are the uses and benefits of the Internet of Vehicles?
- Power Inverter - A critical safety system for electric vehicles
- Analysis of the information security mechanism of AUTOSAR, the automotive embedded software framework
Professor at Beihang University, dedicated to promoting microcontrollers and embedded systems for over 20 years.
- Innolux's intelligent steer-by-wire solution makes cars smarter and safer
- 8051 MCU - Parity Check
- How to efficiently balance the sensitivity of tactile sensing interfaces
- What should I do if the servo motor shakes? What causes the servo motor to shake quickly?
- 【Brushless Motor】Analysis of three-phase BLDC motor and sharing of two popular development boards
- Midea Industrial Technology's subsidiaries Clou Electronics and Hekang New Energy jointly appeared at the Munich Battery Energy Storage Exhibition and Solar Energy Exhibition
- Guoxin Sichen | Application of ferroelectric memory PB85RS2MC in power battery management, with a capacity of 2M
- Analysis of common faults of frequency converter
- In a head-on competition with Qualcomm, what kind of cockpit products has Intel come up with?
- Dalian Rongke's all-vanadium liquid flow battery energy storage equipment industrialization project has entered the sprint stage before production
- Allegro MicroSystems Introduces Advanced Magnetic and Inductive Position Sensing Solutions at Electronica 2024
- Car key in the left hand, liveness detection radar in the right hand, UWB is imperative for cars!
- After a decade of rapid development, domestic CIS has entered the market
- Aegis Dagger Battery + Thor EM-i Super Hybrid, Geely New Energy has thrown out two "king bombs"
- A brief discussion on functional safety - fault, error, and failure
- In the smart car 2.0 cycle, these core industry chains are facing major opportunities!
- The United States and Japan are developing new batteries. CATL faces challenges? How should China's new energy battery industry respond?
- Murata launches high-precision 6-axis inertial sensor for automobiles
- Ford patents pre-charge alarm to help save costs and respond to emergencies
- New real-time microcontroller system from Texas Instruments enables smarter processing in automotive and industrial applications
- STM32F767 ADC self-calibration problem
- EEWORLD University ---- Digi-Key: Accelerated Application of Graph Algorithms in Deep Learning
- Echo Cancellation - How to solve the serious problem of sound swallowing during dual talk in WebRTC AEC algorithm
- A constant and adjustable output power electronic cigarette power supply solution based on TPS61022
- Sales of new energy vehicles have skyrocketed, how should we deal with used batteries?
- E-ON China Online Cloud Sharing Laboratory——"Microcomputer Principles and Applications"
- Improving Power Supply Network Efficiency Using Fixed Ratio Converters
- Large amplitude sine wave signal frequency acquisition circuit
- 【Share】Output adjustable
- [N32L43x Review] 6. Software and Hardware I2C Driver for 0.96-inch OLED