summary
This article describes the system composition and main technical parameters of the carton packaging machine and the control scheme, the design scheme of the carton board supply process, and analyzes and studies the production process of the carton packaging machine in the automatic bottle packaging line, and applies the Siemens servo motion control system to this equipment, communicating with all drive servos through the CAN field bus. The advantages of this control system are also explained.
introduction
With the development of packaging technology, the number of electronic equipment in packaging is increasing, which brings about the problem that a large number of signals in the integrated control system of packaging need to be exchanged in real time. Traditional wiring harnesses are far from meeting this requirement. Therefore, more and more packaging uses controller area network (CAN). However, the CAN bus only defines the physical layer and data link layer in the open system interconnection reference model (OSI). Generally, users must directly operate the link layer with the driver, which cannot directly meet the configuration and product interconnection requirements of complex control networks. CANopen, as a truly open CAN high-level protocol, enables different CAN devices to communicate in a standardized way, making CAN devices interoperable. With the increasing perfection of the CANopen protocol, it has been widely used in many industries.
The packaging form of heat shrink film has the characteristics of safety, reliability, and convenience for transportation and sales, and has been widely used in the domestic beverage industry. However, the glass bottles used in the production process of beer are easily damaged after collision. Due to the limitations of the packaging form of heat shrink film, it cannot completely solve the production needs of the beer industry and other related glass bottle packaging industries. Therefore, the use of carton packaging is a high-end and high-specification packaging for beverages and beer. It is also easy to solve the problems caused by long-distance transportation and effectively make up for the defects of heat shrink film packaging. The two complement each other and are two indispensable packaging forms in the modern beverage and beer packaging industry.
In the past, the packaging capacity of carton packaging machines in my country has always been at the level of 35 boxes/min, which can only meet the needs of 20,000 bottles/h beverage and beer packaging production lines. This paper improves and upgrades the existing carton packaging machine technology, absorbs the characteristics of domestic and foreign carton packaging machines, and successfully develops a fully automatic carton packaging machine with a production capacity of 60 boxes/min using a servo motion control system, effectively solving the production needs of the beverage and beer industry.
1. Technical structure and working principle of paper packaging machine
1.1 Composition of the control system
Koshimin's R60 carton packaging machine uses the B&R control system. The main control PLC uses CP476 to communicate with all drive servos through a CAN-type field bus. The upper computer panel uses PP451, which is also connected via the CAN bus and uses EX470 to expand remote IO.
Figure 1 B&R control system diagram of carton packaging machine
Set the IP address of the upper PP451 to 01; the CAN bus address of the 3IF771.9 communication card to 09; the CAN bus address of the servo driver for pushing the bottle to 01; the CAN bus address of the servo driver for the bottle distributor 1 to 02; the CAN field bus address of the servo driver for the bottle distributor 2 to 03; the CAN bus address of the servo driver at the exit to 04; the CAN bus address of the servo driver for the cardboard suction card to 05; the CAN bus address of the EX470 bus controller to C6; the CAN bus address set on each device must be absolutely correct with the address set on the device, otherwise the control system will not operate normally. Under normal circumstances, after the control system is powered on, the CAN communication indicator of the IF771 will flash quickly, and the two communication indicators of the AC110 communication card on each servo driver will remain on, otherwise it means that the communication is abnormal.
1.2 Composition and working principle of automatic carton packaging machine
The automatic carton packaging machine mainly includes: bottle conveying, cardboard supplying, carton board taking, carton board conveying, bottle separation, bottle pushing, carton folding and forming, carton sealing and gluing, glue spraying and other parts.
The carton board supply mainly consists of carton board storage, carton board horizontal conveyor, carton board waiting station, carton board supply auxiliary fork, carton board supply main fork and detection switch. Its main function is to complete the supply of carton boards to the packaging machine. The carton board supply to the high-speed packaging machine should be continuous to make the supply of carton boards smoother.
Bottle conveying is mainly divided into two parts. One part is to control the running speed of the motor through the frequency converter, to convey the bottles on the conveyor line regularly as required, and to ensure the continuous supply of bottles through bottle shortage detection; the other part is to drive the mechanical part through the main driver to convey the bottles according to the running speed of the main motor.
The cardboard removal is driven by a servo motor, which runs synchronously with the main shaft motor in the form of a driven shaft, and is equipped with two sets of suction cups, which are used to take the cardboard alternately, thereby achieving the function of high-speed cardboard removal. Bottle separation is controlled by the servo motors of No. 1 and No. 2 bottle separation and the main drive motor, and the bottles are sequentially divided into groups of 3×4.
The cardboard conveying part transfers the sucked cardboard to the upper bottle position through several stations, and is powered by the main drive. The detection of double-layer cardboard and missing cardboard is mainly used to ensure the supply of cardboard.
The main function of the bottle pushing part is to sort the bottles after they are separated. The bottles are pushed down with the bottle pushing rod. When the bottles pass through the unpowered transition plate, the bottles are arranged closely, thereby improving the quality of packaging.
The carton is folded, glued and sealed to complete the packaging of beverages or beer. According to the structure of the carton, the exact position of glue spraying is determined and the sealing is adjusted appropriately to ensure the sealing quality. Figure 2 shows the working flow of the paper packaging machine.
Figure 2 R60 automatic carton packaging machine production flow chart
2. Control system design
2.1 Main Controller
The main controller mainly controls analog quantity control, sensor control, light source control, transmission control, positioning control, pneumatic control, process parameters, process, operation failure, product quality and safety protection, etc. PLC programmable logic controller and related auxiliary systems are used to complete the real-time and accuracy control of the system.
2.2 Multi-motor synchronization technology and servo technology
The packaging items are transmitted through the main transmission system, and the auxiliary materials of various packaging are transmitted through the feeding system. The mutual actions between them need to be coordinated and the control should also be consistent. The multi-motor servo control system adopts PLC control, and the detection between each station of the machine equipment is completed through the proximity switch of each station on the periphery, so as to realize the input of contactless signal and the coordinated action of electricity, light, machine and gas of the control system. By properly adjusting the position of the bottle distributor and the sealing, glue spraying and shaping cylinders, cartons of different specifications can be packaged.
2.3 Operating System Design
Through the application of frequency conversion technology and human-machine interface, the packaging equipment can be controlled to run at different speeds in different working modes such as manual, automatic and debugging modes. The frequency converter communicates through the RS-485 interface and can display and set relevant parameters on the human-machine interface.
3. Control system solution
The control system of the automatic carton packaging machine mainly includes: PP451 human-machine interface, motion controller EX470, detection elements, servo drive, actuators and servo motors, etc. The motion controller EX470 controls the servo drive through the CAN bus to complete the real-time control of the servo motor.
The operation detection and packaging cycle of the machine position are set by servo control. An encoder is installed on one side of the servo motor, which forms a closed-loop control with the servo motor according to the pulse feedback signal received from the rotary encoder. The encoder is an incremental encoder. The data is transmitted to EX470 through the encoder interface, and the received data is processed to indicate the actual operation position of the machine. In the process of carton packaging, the bottle pusher completes a packaging every time a group of bottles is pushed out. A detection switch is installed on one side of the place where the bottle pusher passes, and the encoder data recorded by EX470 is cleared. In each packaging cycle, the position data of the actions of taking cardboard, putting cardboard and separating bottles are compared one by one with the encoder data in EX470, and each action of the machine is controlled according to the compared data.
Previous article:Basic concepts and main transmission parameters of permanent magnet servo motors
Next article:Detailed explanation of the principle of brushed DC motor
Recommended ReadingLatest update time:2024-11-16 13:05
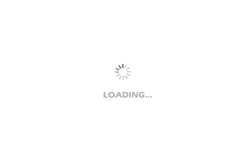
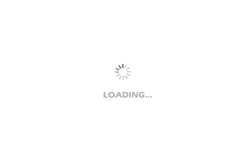
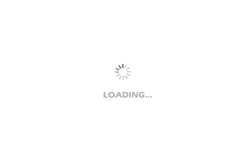
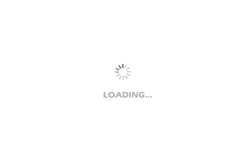
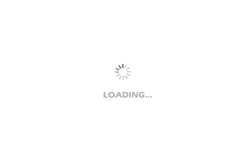
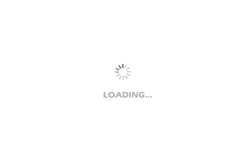
- Popular Resources
- Popular amplifiers
- Huawei's Strategic Department Director Gai Gang: The cumulative installed base of open source Euler operating system exceeds 10 million sets
- Analysis of the application of several common contact parts in high-voltage connectors of new energy vehicles
- Wiring harness durability test and contact voltage drop test method
- Sn-doped CuO nanostructure-based ethanol gas sensor for real-time drunk driving detection in vehicles
- Design considerations for automotive battery wiring harness
- Do you know all the various motors commonly used in automotive electronics?
- What are the functions of the Internet of Vehicles? What are the uses and benefits of the Internet of Vehicles?
- Power Inverter - A critical safety system for electric vehicles
- Analysis of the information security mechanism of AUTOSAR, the automotive embedded software framework
Professor at Beihang University, dedicated to promoting microcontrollers and embedded systems for over 20 years.
- Innolux's intelligent steer-by-wire solution makes cars smarter and safer
- 8051 MCU - Parity Check
- How to efficiently balance the sensitivity of tactile sensing interfaces
- What should I do if the servo motor shakes? What causes the servo motor to shake quickly?
- 【Brushless Motor】Analysis of three-phase BLDC motor and sharing of two popular development boards
- Midea Industrial Technology's subsidiaries Clou Electronics and Hekang New Energy jointly appeared at the Munich Battery Energy Storage Exhibition and Solar Energy Exhibition
- Guoxin Sichen | Application of ferroelectric memory PB85RS2MC in power battery management, with a capacity of 2M
- Analysis of common faults of frequency converter
- In a head-on competition with Qualcomm, what kind of cockpit products has Intel come up with?
- Dalian Rongke's all-vanadium liquid flow battery energy storage equipment industrialization project has entered the sprint stage before production
- Allegro MicroSystems Introduces Advanced Magnetic and Inductive Position Sensing Solutions at Electronica 2024
- Car key in the left hand, liveness detection radar in the right hand, UWB is imperative for cars!
- After a decade of rapid development, domestic CIS has entered the market
- Aegis Dagger Battery + Thor EM-i Super Hybrid, Geely New Energy has thrown out two "king bombs"
- A brief discussion on functional safety - fault, error, and failure
- In the smart car 2.0 cycle, these core industry chains are facing major opportunities!
- The United States and Japan are developing new batteries. CATL faces challenges? How should China's new energy battery industry respond?
- Murata launches high-precision 6-axis inertial sensor for automobiles
- Ford patents pre-charge alarm to help save costs and respond to emergencies
- New real-time microcontroller system from Texas Instruments enables smarter processing in automotive and industrial applications
- 【XMC4800 Relax EtherCAT Kit Review】+ Getting Started with DAVE, Timer Interrupt and UART Simple Application
- Share: In actual project, the average load was too high, and finally found that it was this that was causing the problem
- The problem of MCLK frequency of LIS25BA
- 【GD32307E-START】Development practice->UART sends HELLOWORD to the world
- Electromagnetic waves and antennas
- The voltage difference of bq4050 with load is very high, almost 1V. How to solve this problem? It is two strings of batteries.
- 2.4 GHz CDMA Radio Transceiver CYWUSB6934 Application Circuit
- It feels like USB3 isn't popular yet, and USB4 is here!
- On Unjust Death and Redress
- LED stepless color temperature adjustment solution GP9101