Today, the operation of our world is increasingly dependent on "data". Data not only provides a reference for our actions, but sometimes directly participates in decision-making and issues instructions to machines. Moreover, such scenarios are infiltrating some more "critical" fields, such as industrial manufacturing.
As the saying goes, "If you want to get rich, build roads first." Improved transportation in the real world will increase the efficiency of the circulation of production factors such as people and logistics, thereby boosting the development of the entire economic system. The same principle applies to the virtual digital world - only by providing an efficient network for the circulation of data can we release its huge energy. Unfortunately, such a network was not so smooth in the industrial field in the past.
Building roads for industrial networks
The idea of "building roads" for data exchange in the industrial field has actually been around for a long time. In the 1970s, with the development of programmable logic controllers (PLCs) and automation technology, distributed control of production equipment gradually became a rigid demand, which gave rise to the industrial field bus, which connected previously isolated devices. Just as every technology will go through a "Warring States" era of standards in the early stages of development, the industrial field bus is no exception. Moreover, due to the unique "vertical" ecological structure of the industrial field, these standards have not been unified until today, which has also limited the flow of data to a limited range, which is very unfavorable for the expansion of industrial networks and data sharing between each other.
The "pain points" caused by the proliferation of standards and their fragmentation have become more and more "painful" as the scale of industrial networks expands. Therefore, in the early 21st century, people introduced "Industrial Ethernet". As the name suggests, Industrial Ethernet is to introduce the Ethernet architecture that "unified" the IT field into the industrial field, uniformly adopt standard Ethernet media, and use this as an opportunity to achieve the unification of standards at the physical layer and data link layer.
This ideal looks beautiful, but it should be noted that the word "industrial" is still in front of industrial Ethernet, because it is different from traditional Ethernet technology. Standard Ethernet uses the carrier sense multiple access/collision detection (CSMA/CD) mechanism. When two data senders collide, they must delay a certain period of time before resending the message. If the network is congested, some messages may not be sent for a long time. So in essence, Ethernet is a time-insensitive and uncertain network. In industrial automation control, the priority is real-time to ensure the timely delivery of data messages. In order to meet such requirements in industrial applications, it is necessary to "transform" the standard Ethernet, modify or add some specific protocols on its basis to ensure real-time and determinism, making it a deterministic network, which forms the so-called industrial Ethernet.
However, different manufacturers have different ideas and methods for transforming the same Ethernet, which results in the fact that the networks called "Industrial Ethernet" cannot actually achieve interconnection, intercommunication, and interoperability. In order to allow data to flow between these "sub" networks, people have to add additional gateways. This is like everyone has built the same "road", but the traffic rules on different road networks are different. It is not easy to run smoothly and barrier-free between such road networks.
At the same time, a bigger challenge is that the introduction of smart manufacturing concepts such as Industry 4.0 requires a matching network that can support the flow of different types of data at the same time. Whether it is real-time data required for manufacturing site control or non-real-time data required for production management and optimization, they all need to be centralized and processed in a unified network. For some global optimization tasks, they can be directly connected to the edge and the cloud without going through traditional hierarchical controllers... In other words, an ideal Ethernet architecture in industrial applications should be a converged network that can meet the real-time control requirements of OT (operational technology) networks and support the high-throughput data transmission needs of the IT (information technology) field. Only in this way can data from the entire industrial production process be gathered together without leaving any information blind spots.
To realize this ideal, we must deeply transform the Ethernet we are familiar with and create a unified network and protocol specification that meets the requirements of the manufacturing industry. This is also the only way to get rid of the obstacles in interoperability between different bus standards. TSN (Time Sensitive Network) was born.
The road to TSN
Although we are discussing the application of TSN in the industrial field the most today, it actually originated from a standard in the audio and video field. In order to effectively solve the problem of real-time synchronous transmission of data in audio and video networks, the IEEE 802.1 working group established the AVB Audio Video Bridging Task Group in 2006 and made fruitful progress. People soon realized that there are many similarities between AVB's series of research results and solving the problem of time determinism of data transmission in Ethernet. So in 2012, the AVB Task Group expanded the application requirements and scope of application of time deterministic Ethernet and changed the name of the task group to "TSN Task Group".
There are three main challenges that TSN needs to address: time synchronization, scheduling and traffic shaping, as well as communication path selection, reservation and fault tolerance.
Time synchronization: This is to achieve a common time reference for all devices in the network, provide clocks that are synchronized with each other, and also provide a negotiated benchmark for end-to-end transmission delay.
Scheduling and traffic shaping: Allows traffic classes of different priorities to coexist on the same network, each with different requirements for available bandwidth and end-to-end latency, thereby enabling the transmission of different data traffic types on the same network.
Communication path selection, reservation, and fault tolerance: Defines that all devices participating in real-time communication need to follow the same rules in selecting communication paths, reserving bandwidth, and time slots, so that they can use multiple paths to achieve fault elimination and ensure network security and reliability.
After years of development, TSN has defined a series of "sub-standards" under the IEEE802.1 standard framework, forming a complete set of protocols to provide a general processing mechanism for the MAC layer of the Ethernet protocol. While ensuring the time determinism (real-time) of Ethernet data communication, it also makes interoperability between networks with different protocols possible.
Of course, it will take a long time for the standards to be formulated, accepted by the industry and put into commercial use on a large scale. For a meticulous field like industrial manufacturing, people have to consider more factors. Therefore, people have been working hard to build the entire TSN ecosystem. Various technology suppliers and businesses have provided support and accumulated energy for the final implementation of TSN from different levels.
Figure 1. Avnet’s TSN HW Eval Kit
For example, Avnet provides developers with a TSN HW Eval Kit, which is a TSN platform built using existing Xilinx and Avnet hardware resources. Developers can use it to develop and verify TSN prototypes, laying a solid foundation for the final solution implementation.
Figure 2: TSN system block diagram based on Avnet TSN HW Eval Kit
In short, the rise of Industry 4.0 and the Industrial Internet of Things (IIoT) has led people to embark on a path of in-depth "magic modification" of Ethernet. As the result of this "magic modification", TSN is waving at us in front. Now is the time to speed up and sprint towards this goal.
Previous article:Challenges that control-level design will face in smart factory automation systems
Next article:Service robots will usher in a boom, why are humans obsessed with them?
Recommended ReadingLatest update time:2024-11-16 11:31
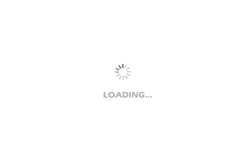
- Huawei's Strategic Department Director Gai Gang: The cumulative installed base of open source Euler operating system exceeds 10 million sets
- Analysis of the application of several common contact parts in high-voltage connectors of new energy vehicles
- Wiring harness durability test and contact voltage drop test method
- Sn-doped CuO nanostructure-based ethanol gas sensor for real-time drunk driving detection in vehicles
- Design considerations for automotive battery wiring harness
- Do you know all the various motors commonly used in automotive electronics?
- What are the functions of the Internet of Vehicles? What are the uses and benefits of the Internet of Vehicles?
- Power Inverter - A critical safety system for electric vehicles
- Analysis of the information security mechanism of AUTOSAR, the automotive embedded software framework
Professor at Beihang University, dedicated to promoting microcontrollers and embedded systems for over 20 years.
- Innolux's intelligent steer-by-wire solution makes cars smarter and safer
- 8051 MCU - Parity Check
- How to efficiently balance the sensitivity of tactile sensing interfaces
- What should I do if the servo motor shakes? What causes the servo motor to shake quickly?
- 【Brushless Motor】Analysis of three-phase BLDC motor and sharing of two popular development boards
- Midea Industrial Technology's subsidiaries Clou Electronics and Hekang New Energy jointly appeared at the Munich Battery Energy Storage Exhibition and Solar Energy Exhibition
- Guoxin Sichen | Application of ferroelectric memory PB85RS2MC in power battery management, with a capacity of 2M
- Analysis of common faults of frequency converter
- In a head-on competition with Qualcomm, what kind of cockpit products has Intel come up with?
- Dalian Rongke's all-vanadium liquid flow battery energy storage equipment industrialization project has entered the sprint stage before production
- Allegro MicroSystems Introduces Advanced Magnetic and Inductive Position Sensing Solutions at Electronica 2024
- Car key in the left hand, liveness detection radar in the right hand, UWB is imperative for cars!
- After a decade of rapid development, domestic CIS has entered the market
- Aegis Dagger Battery + Thor EM-i Super Hybrid, Geely New Energy has thrown out two "king bombs"
- A brief discussion on functional safety - fault, error, and failure
- In the smart car 2.0 cycle, these core industry chains are facing major opportunities!
- The United States and Japan are developing new batteries. CATL faces challenges? How should China's new energy battery industry respond?
- Murata launches high-precision 6-axis inertial sensor for automobiles
- Ford patents pre-charge alarm to help save costs and respond to emergencies
- New real-time microcontroller system from Texas Instruments enables smarter processing in automotive and industrial applications
- Two wireless communication modulation methods: similarities and differences between LoRa and FSK
- What are the advantages and disadvantages of 2.4G Wi-Fi and 5G Wi-Fi?
- CPLD dual integral AD analog-to-digital conversion help
- About UWB (Ultra-Wideband)
- USB Type-C Docking Design
- Miscellaneous talks on rectification (VIII)
- Things to note when selecting and using a POE switch
- How to use smart home to make taking off shoes more technological and convenient?
- [HC32F460 Development Board Review] 07 Clock Configuration of ADC Acquisition Process
- AD09 has problems loading libraries