1 Introduction to Customized User Peripherals Based on Avalon Bus
The Avalon bus of NiosⅡ is different from the fixed peripherals of other microprocessors. The peripherals of NiosⅡ can be customized arbitrarily, which allows users to customize according to specific application requirements. All NiosⅡ system peripherals are connected to the NiosⅡ soft core through the Avalon bus to exchange data. Therefore, user-defined peripherals must comply with the bus protocol to establish a connection with NiosⅡ.
The Avalon signal interface defines a set of signal types such as chip select, read enable, write enable, address, data, etc., which are used to describe the address-based read and write interface on the master and slave peripherals. The peripherals use accurate signals to interface with their core logic and remove signals that add unnecessary overhead.
In the Nios Ⅱ system, a custom device consists of the following parts:
(1) Hardware file: A hardware description file written in HDL language that describes the logic of custom device components.
(2) Software files: device register files and device driver files written in C language.
(3) Device Description File (Ptf): This file describes the structure of the device and contains the information required for SoPC Builder to configure and integrate it into the system. This file is automatically generated by SoPC Builder based on the hardware files and software files.
2 PWM Design Based on NiosⅡ System
PWM is a very effective technology for controlling analog circuits using digital outputs. It is widely used in many fields from measurement and communication to power control and conversion. In fact, PWM is a method of digitally encoding the level of analog signals. Through the use of high-resolution counters, the duty cycle of a square wave is modulated to encode the level of a specific analog signal. The PWM signal is still digital because at any given moment, the full-amplitude DC power supply is either completely present or completely absent. The voltage or current source is applied to the analog load in a repetitive sequence of pulses that are on or off. On means that the DC power supply is applied to the load, and off means that the power supply is disconnected. As long as the bandwidth is sufficient, any analog value can be encoded using PWM.
2.1 Hardware Design
Hardware files refer to HDL files, which consist of the following modules:
Logic module: describes the logical function of the device;
Register mapping module: provides a communication interface between the internal logic module and the Avalon bus;
Avalon bus interface module: enables the Avalon bus to access registers to complete corresponding logical functions.
2.1.1 Logical Structure
The custom PWM is also composed of the above modules. PWM is designed according to the following requirements:
(1) The task logic operates synchronously with a simple clock.
(2) The task logic uses a 32-bit counter to provide a certain range of period and duty cycle for PWM. The maximum period can be set to 232 clks.
(3) A microcontroller can be used to set the period and duty cycle values of PWM, so an interface and control logic that can read and write registers is required.
(4) Registers are defined to store the values of PWM period and duty cycle.
(5) The microcontroller can turn off the PWM output by controlling the disable bit of the register.
The structure diagram of PWM task logic is shown in Figure 1.
The PWM task logic consists of an input clock (clock), an output signal port (pwm_out), an enable bit, a 32-bit counter, and a 32-bit comparison circuit. clk is the clock signal of the 32-bit counter. The 32-way comparison circuit compares the current value of the 32-bit counter with the value in the duty cycle setting register (Duty Cycle Value Register) to determine whether the output of pwm_out is high or low. When the value in the current counter is less than or equal to the value in the duty cycle register, pwm_out outputs a low level, otherwise it outputs a high level. The PWM cycle setting register (Modulo_n ValueRegister) is used to set the signal cycle of pwm_out. When the current counter value is equal to the setting in the cycle setting register, a reset signal is generated to clear the value in the counter. The enable control register (EnableControl Register) can make the clock signal valid or invalid, that is, control whether the counter counts, thereby keeping the pwm_out output unchanged at the current level.
The PWM internal includes the Enable Control Register, the Modulo_n Value Register, and the Duty Cycle Value Register, as shown in Figure 1. In the design, each register is mapped to a separate offset address in the Avalon slave port address space. Each register can be read/written, and the software can read back the current value in the register. Table 1 is a list of PWM registers and offset addresses.
The Avalon interface of PWM requires a simple slave port, which uses Avalon bus signals to complete register read/write transfers. The signals required for PWM and Avalon bus interface are shown in Table 2.
2.1.2 Hardware Design Files and Simulation
The PWM hardware design file contains three HDL files written in Verilog as shown in Table 3.
pwm_tasK_logic.v completes the logic function of PWM. Figure 2 is the simulation waveform of this file in QuartusⅡ environment.
In Figure 2: the clock_divide signal sets the number of clocks in the PWM output cycle, and the dutv_cycle signal sets the number of clocks in which the PWM outputs a low level within a cycle. The two signal setting values determine the duty cycle and period of the PWM signal.
2.2 Software Design
If you want the Nios soft core to be able to access custom devices, you must write device drivers based on the previous hardware design and the file structure of the hardware abstraction layer. Take PWM as an example to illustrate the file structure of HAL, as shown in Table 4.
2.3 Encapsulating PWM Design as SoPC Builder Component
When the hardware files and software files have been established, you can use the device editor in SoPC Builder to encapsulate the custom device into the development environment, and call it directly when building the NiosⅡ system. Click Create New Component in SoPC Builder, create a new component wizard to add HDL files, set signals and interfaces to add software, and finally generate a folder containing description files, folders for users to store hardware description files, and HAL folders for containing HAL software files.
2.4 Building the Nios System
The built kernel file is compiled in QuartusⅡ to generate a pof configuration file and download it to the E2PROM chip. Then you can use the Nios IDE development environment to edit the user program and debug the application on the target board through JTAGBlaster or USB Blaster.
3 Application of Customized Peripheral PWM in Embedded Intelligent Car Monitoring System
The design of the intelligent car monitoring system uses the SmartSoPC core board of Zhou Ligong Company, the FPGA is Altera's EPlC12, and the NiosⅡ processor is used as the embedded CPU. The robot car has two motors, the left wheel motor and the right wheel motor. This part includes the motor drive circuit and the motor control circuit, that is, the drive and control of the left motor and the drive and control of the right motor. The drive circuit uses the high-power DC motor drive chip L289 of CTMicroelectronics. The speed control uses PWM to control the forward speed of the car. The control word is written by the FPGA to obtain PWM drive signals with different duty cycles. This PWM signal is sent to the control end of the motor drive chip to adjust the speed. Call the motor driver program, change the PWM duty cycle, output PWM waves, and realize the speed control of the motor. When the PWM signal is used to control the speed of the DC motor, the motor will not run stably when the frequency is low, and the driving efficiency of the PWM signal is reduced when the frequency is high. After multiple tests of the actual circuit, the debugging results show that the effect is better when the frequency is between 500 and 1,000 Hz. Some C language control codes are as follows:
4 Conclusion
The NiosⅡ embedded processor is a user-configurable general-purpose RISC embedded processor, which is a very flexible and powerful processor. Embedded system design based on this technology can easily integrate general equipment and custom equipment modules into the system, enriching the interface resources, so that users can quickly develop a customized system-on-chip, improve efficiency, and shorten the development cycle. This article uses the method of customizing PWM peripherals and proves the feasibility and correctness of the solution through hardware testing, hoping to provide some methods and suggestions for developers using NiosⅡ processors.
Previous article:Realization of high-precision synchronous clock signal in distributed oscilloscope based on MAXII570
Next article:Embedded Network Communication System Based on NiosII
Recommended ReadingLatest update time:2024-11-16 21:25
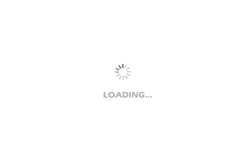
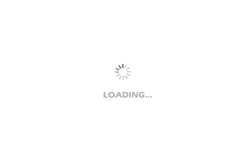
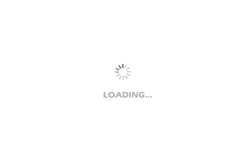
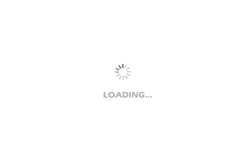
- Popular Resources
- Popular amplifiers
-
西门子S7-12001500 PLC SCL语言编程从入门到精通 (北岛李工)
-
Small AC Servo Motor Control Circuit Design (by Masaru Ishijima; translated by Xue Liang and Zhu Jianjun, by Masaru Ishijima, Xue Liang, and Zhu Jianjun)
-
Intelligent Control Technology of Permanent Magnet Synchronous Motor (Written by Wang Jun)
-
100 Examples of Microcontroller C Language Applications (with CD-ROM, 3rd Edition) (Wang Huiliang, Wang Dongfeng, Dong Guanqiang)
- Huawei's Strategic Department Director Gai Gang: The cumulative installed base of open source Euler operating system exceeds 10 million sets
- Analysis of the application of several common contact parts in high-voltage connectors of new energy vehicles
- Wiring harness durability test and contact voltage drop test method
- Sn-doped CuO nanostructure-based ethanol gas sensor for real-time drunk driving detection in vehicles
- Design considerations for automotive battery wiring harness
- Do you know all the various motors commonly used in automotive electronics?
- What are the functions of the Internet of Vehicles? What are the uses and benefits of the Internet of Vehicles?
- Power Inverter - A critical safety system for electric vehicles
- Analysis of the information security mechanism of AUTOSAR, the automotive embedded software framework
Professor at Beihang University, dedicated to promoting microcontrollers and embedded systems for over 20 years.
- Innolux's intelligent steer-by-wire solution makes cars smarter and safer
- 8051 MCU - Parity Check
- How to efficiently balance the sensitivity of tactile sensing interfaces
- What should I do if the servo motor shakes? What causes the servo motor to shake quickly?
- 【Brushless Motor】Analysis of three-phase BLDC motor and sharing of two popular development boards
- Midea Industrial Technology's subsidiaries Clou Electronics and Hekang New Energy jointly appeared at the Munich Battery Energy Storage Exhibition and Solar Energy Exhibition
- Guoxin Sichen | Application of ferroelectric memory PB85RS2MC in power battery management, with a capacity of 2M
- Analysis of common faults of frequency converter
- In a head-on competition with Qualcomm, what kind of cockpit products has Intel come up with?
- Dalian Rongke's all-vanadium liquid flow battery energy storage equipment industrialization project has entered the sprint stage before production
- Allegro MicroSystems Introduces Advanced Magnetic and Inductive Position Sensing Solutions at Electronica 2024
- Car key in the left hand, liveness detection radar in the right hand, UWB is imperative for cars!
- After a decade of rapid development, domestic CIS has entered the market
- Aegis Dagger Battery + Thor EM-i Super Hybrid, Geely New Energy has thrown out two "king bombs"
- A brief discussion on functional safety - fault, error, and failure
- In the smart car 2.0 cycle, these core industry chains are facing major opportunities!
- The United States and Japan are developing new batteries. CATL faces challenges? How should China's new energy battery industry respond?
- Murata launches high-precision 6-axis inertial sensor for automobiles
- Ford patents pre-charge alarm to help save costs and respond to emergencies
- New real-time microcontroller system from Texas Instruments enables smarter processing in automotive and industrial applications
- Commonly used algorithms for drones - Kalman filter (Part 9)
- Reset time problem
- Can anyone compare the characteristics of op amps made of various materials?
- STM32 Example - LCD1602 Circuit
- Advantages and disadvantages of 7nm processors
- 【FAQ】Trust&GO for any cloud service |Microchip Security Solutions Seminar Series 3
- ARM and Intel, which one can replace DSP?
- 【Project source code】Calculator based on FPGA
- Will 65V GaN technology change the radar market?
- Why does DLL not found error appear when running VB with Ginkgo?