随着近年来汽车电气化、智能化及网联化的迅猛进展,汽车内部电子电气元器件的数量与复杂度显著增加。传统的E/E架构已无法满足汽车智能化时代的需求,车载网络正逐步向域控制和集中控制转型。行业巨头如博世、采埃孚等纷纷布局下一代车载网络架构,特斯拉在Model 3和Model Y中已采用了域控制结构。
At present, the number of ECUs in a single car has gradually increased from 20-30 to more than 100, and the wiring harness length of some models has even reached 2.5 miles. The data connections inside the car are increasing. Data connection is the "nervous system" of the car, responsible for connecting various sensors and actuators in various locations of the car to the car computing platform (brain). Under the trend of software-defined cars, the in-vehicle network architecture is facing unprecedented pressure.
In order to meet the demand for high-speed transmission of massive data under the development trend of the three trends of automobiles, high-bandwidth, low-latency high-speed interfaces have become key factors.
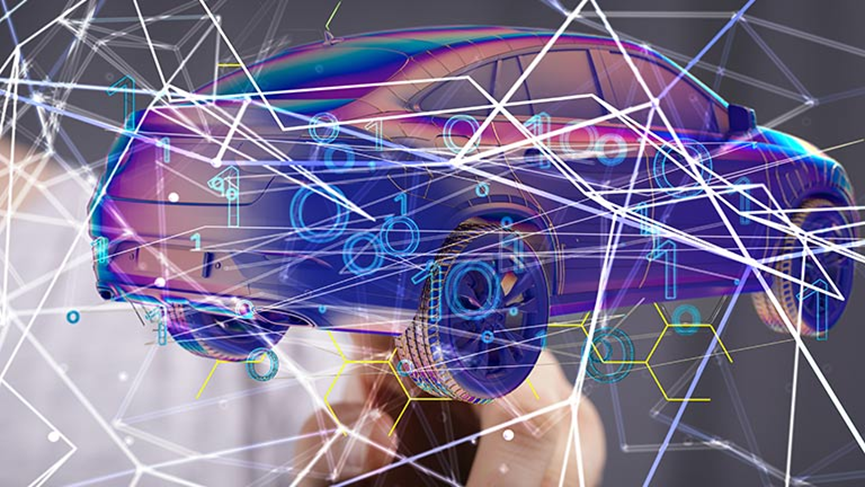
Ethernet interface replaces CAN bus | the general trend
After years of development, the in-vehicle network has now formed a solution with "CAN bus as the mainstream and multiple bus technologies coexisting". Due to its advantages such as low cost and simple architecture, CAN and LIN buses are still the most widely used communication protocols in the car. As a leading global electronic component distributor, Avnet has a wide range of CAN interface and LIN transceiver products, which can provide customers with various communication solutions from low speed to high speed.
The current industry development direction is actively transitioning to automotive Ethernet. The difference in speed between CAN bus and Ethernet is similar to the difference between "urban roads" and "highways". When CAN was first launched, the maximum data rate was only 150kb/s, which was gradually increased to 10Mb/s. The recently approved CAN XL standard extends the bandwidth to 20Mb/s, but this transmission speed is far from meeting the connection requirements of more in-vehicle computing resources in the vehicle network.
In-vehicle Ethernet with higher transmission speeds is now a new option.
In 2016, IEEE released the first automotive Ethernet standard IEEE 802.3bw, or 100Base-T1, with a data transmission bandwidth of 100Mbit/s. In the past, it often took 10 hours to transmit 1 gigabyte of data using CAN, while it only took about 2 minutes to transmit 1 gigabyte of data using Ethernet. This is enough to meet the data transmission needs of many basic automotive applications, so today the automotive Ethernet interface bus has been widely used.
The in-vehicle Ethernet interface can not only meet the requirements of in-vehicle electromagnetic compatibility, but also reduce the in-vehicle connection cost by up to 80% and the in-vehicle wiring weight by up to 30%. At the same time, its technical advantages can well meet the requirements of high reliability, low electromagnetic radiation, low power consumption, bandwidth allocation, low latency, and lightweight of automobiles, and will become the key technology of the next generation of automobile networks.
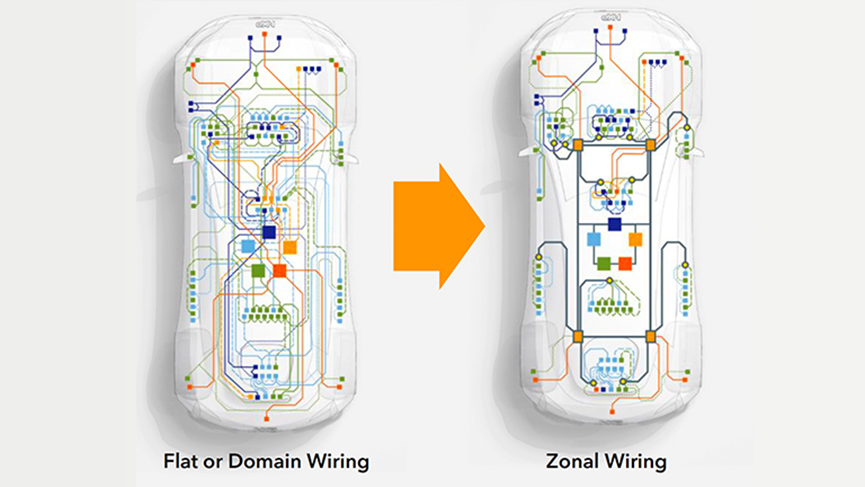
Avnet is continuing to pay attention to industry development trends, constantly enriching its product line, providing customers with more advanced and reliable in-vehicle network solutions, and promoting the innovative development of the automotive industry.
As a key bridge for in-vehicle information exchange, the market demand for in-vehicle high-speed SerDes (Serializer/Deserializer) interfaces is growing continuously, driven by the upgrade of intelligent driving and infotainment systems. However, this field is currently dominated by foreign manufacturers, and the solutions are mainly dedicated, with no unified standards.
In order to break this situation, in 2020, the MIPI Alliance released the MIPI A-PHY standard, which is designed specifically to meet the needs of the automotive industry and can support a variety of applications such as advanced driver assistance (ADAS), in-vehicle infotainment (IVI) displays and other sensors (such as cameras, lidar, radar).
The A-PHY standard provides an asymmetric data link in a point-to-point or daisy-chain topology with high-speed unidirectional data, embedded bidirectional control data and optional power transmission, all over a single cable. This standard reduces wiring, cost and weight, and allows designers to optimize the system for the performance, cost and complexity required for their use cases, providing scalability and flexibility to meet a wide range of speed and design requirements.
The biggest difference between it and traditional SerDes is that MIPI A-PHY is an open, global standard without patent restrictions. Since its release, the MIPI A-PHY standard has received widespread attention in the industry. A-PHY enriches and optimizes existing network integration and is a very good supplement to existing Ethernet, CAN, FlexRay and other interface applications.
In addition to automotive Ethernet and SerDes interfaces, PCIe (Peripheral Component Interconnect Express), as a mature bus interface technology, is mainly used to connect peripheral devices to computer motherboards and is gradually being considered for certain automotive application scenarios.
The maximum transmission distance of PCIe is very short, with the standard being around 1 meter or 2 meters, but for the densely arranged ECUs in the car, PCIe is undoubtedly a solution worth exploring.
One of the main advantages of PCIe is its high data transfer rate. For data-intensive applications, data generated by sensors such as ADAS systems, cameras, and lidar can be transmitted at high speeds via PCIe. Moreover, its design does not require complex transceivers, which can reduce system costs.
Avnet not only provides a variety of PCIe hardware products, including PCIe switches, PCIe bridges, etc., but also provides customers with comprehensive technical support to help customers quickly build high-performance, low-cost in-vehicle networks and accelerate product launch.
PCI and PCIe devices
Cars are often described as “data centers on wheels” because of the huge amounts of data they generate.
Like any data center, cars also need to rely on reliable and powerful networks to operate safely and reliably. In-vehicle Ethernet and MIPI A-PHY high-speed interfaces are like the "communication soldiers" in cars. Their continuous innovation will provide strong network support for car intelligence, enabling cars to process and transmit massive amounts of data more efficiently and achieve more advanced autonomous driving and smart cockpit functions.
From interface connectivity to security, Avnet, with its rich experience and strong technical capabilities in the field of automotive electronics, will help automotive companies build intelligent, efficient and safe automotive products, thereby achieving interaction between cars, people and infrastructure.
Previous article:Huawei's Tuling chassis Zhijie R7 debuts intelligent downhill cruise control: significantly reducing manual braking
Next article:Automotive Electronic Braking (EMB), the Last Piece of the Puzzle for Intelligent Driving
- Popular Resources
- Popular amplifiers
- Car key in the left hand, liveness detection radar in the right hand, UWB is imperative for cars!
- After a decade of rapid development, domestic CIS has entered the market
- Aegis Dagger Battery + Thor EM-i Super Hybrid, Geely New Energy has thrown out two "king bombs"
- A brief discussion on functional safety - fault, error, and failure
- In the smart car 2.0 cycle, these core industry chains are facing major opportunities!
- The United States and Japan are developing new batteries. CATL faces challenges? How should China's new energy battery industry respond?
- Murata launches high-precision 6-axis inertial sensor for automobiles
- Ford patents pre-charge alarm to help save costs and respond to emergencies
- New real-time microcontroller system from Texas Instruments enables smarter processing in automotive and industrial applications
- Innolux's intelligent steer-by-wire solution makes cars smarter and safer
- 8051 MCU - Parity Check
- How to efficiently balance the sensitivity of tactile sensing interfaces
- What should I do if the servo motor shakes? What causes the servo motor to shake quickly?
- 【Brushless Motor】Analysis of three-phase BLDC motor and sharing of two popular development boards
- Midea Industrial Technology's subsidiaries Clou Electronics and Hekang New Energy jointly appeared at the Munich Battery Energy Storage Exhibition and Solar Energy Exhibition
- Guoxin Sichen | Application of ferroelectric memory PB85RS2MC in power battery management, with a capacity of 2M
- Analysis of common faults of frequency converter
- In a head-on competition with Qualcomm, what kind of cockpit products has Intel come up with?
- Dalian Rongke's all-vanadium liquid flow battery energy storage equipment industrialization project has entered the sprint stage before production
- Allegro MicroSystems Introduces Advanced Magnetic and Inductive Position Sensing Solutions at Electronica 2024
- Car key in the left hand, liveness detection radar in the right hand, UWB is imperative for cars!
- After a decade of rapid development, domestic CIS has entered the market
- Aegis Dagger Battery + Thor EM-i Super Hybrid, Geely New Energy has thrown out two "king bombs"
- A brief discussion on functional safety - fault, error, and failure
- In the smart car 2.0 cycle, these core industry chains are facing major opportunities!
- The United States and Japan are developing new batteries. CATL faces challenges? How should China's new energy battery industry respond?
- Murata launches high-precision 6-axis inertial sensor for automobiles
- Ford patents pre-charge alarm to help save costs and respond to emergencies
- New real-time microcontroller system from Texas Instruments enables smarter processing in automotive and industrial applications
- Arteli AT32F415_Getting Started Guide_V1.00
- Questions about rotary transformer and AD2S83
- BYD employee died suddenly in a rental house: worked night shifts for a month before death, each shift lasted 12 hours
- MicroPython Hands-on (15) - AB Buttons on the Control Panel
- Security Tools Bombercat
- The solid state drive doesn't seem to be as good as I thought
- [NXP Rapid IoT Review] Local compilation of online generated projects
- EEWORLD University ---- Practical Guide to Motor Application Development - Based on STM32
- Simulation Help Post
- Based in Chengdu, job position: Reliability Engineer