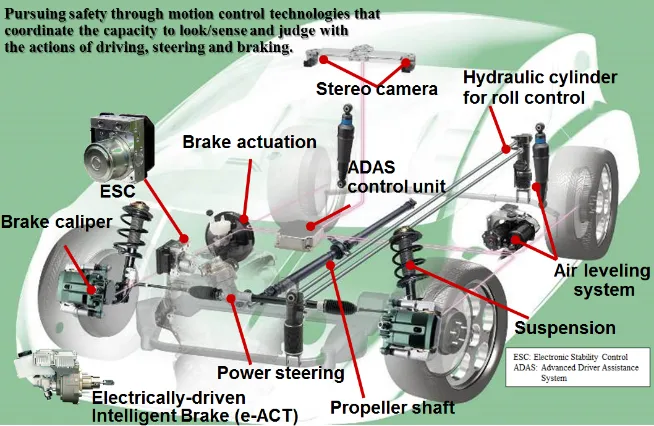
The Vehicle Motion Control (VMC) system is a system that integrates multiple sensors, controllers and actuators to improve the vehicle's handling, safety and comfort by comprehensively controlling the vehicle's acceleration, braking, steering and suspension functions. With the development of autonomous driving technology, the advancement of vehicle intelligence and the rapid expansion of the electric vehicle market, the importance of the VMC system has become increasingly prominent.
#01
The vehicle chassis is an important part of the car, responsible for supporting, carrying, transmitting power and controlling the vehicle's movement. The chassis system includes a variety of actuators, which play a key role in vehicle motion control (VMC).
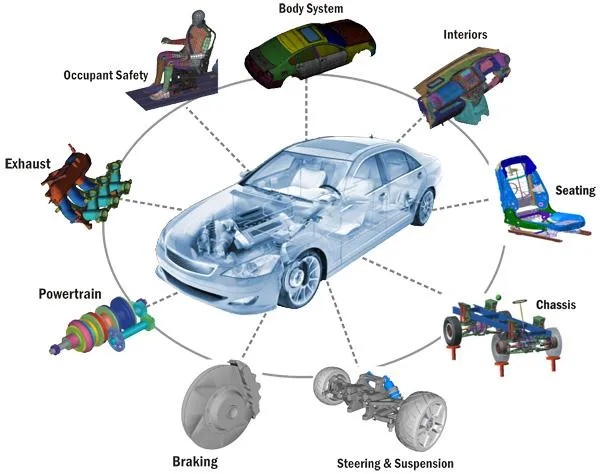
The following are common actuators and their functions in the vehicle chassis, classified by the lateral, longitudinal and vertical directions of the vehicle:
1. Lateral control actuator
(1) Steering system actuator
-
Electric Power Steering (EPS) Actuator
-
Function: The electric power steering system provides steering assistance through an electric motor, reducing the driver's steering effort.
-
Application: Improve vehicle handling and driving comfort, and integrate active steering control functions.
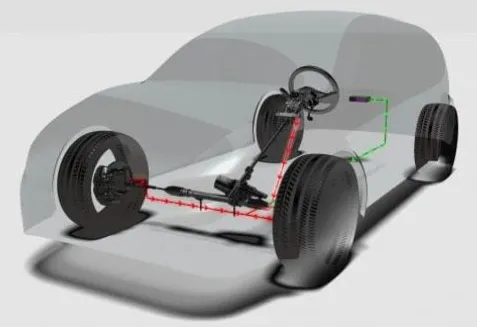
-
Four Wheel Steering (4WS) Actuator
-
Function: The four-wheel steering system improves the vehicle's maneuverability at low speeds and stability at high speeds by independently controlling the steering angles of the front and rear wheels.
-
Application: Improve vehicle handling, especially in narrow spaces and at high speeds.
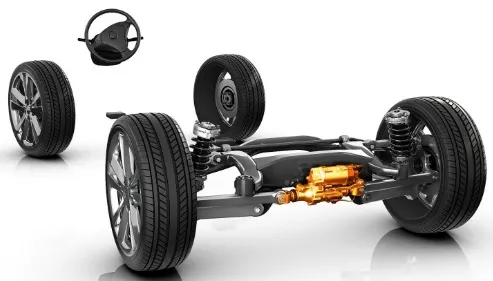
(2) Active Roll Control Actuator
-
Function: Active roll control system reduces vehicle roll when cornering by adjusting the stiffness of the anti-roll bar.
-
Application: Improve vehicle stability and ride comfort in curves.
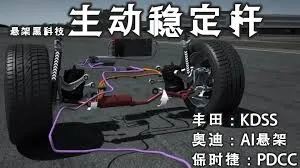
2. Longitudinal control actuator
(1) Braking system actuator
-
Electronic Stability Control (ESC) Actuator
-
Function: Electronic stability control system prevents vehicle loss of control and skidding by independently controlling the braking force of each wheel.
-
Application: Improve vehicle stability and safety in emergency situations.
-
Anti-lock Braking System (ABS) Actuator
-
Function: The anti-lock braking system prevents the wheels from locking during emergency braking and maintains directional control.
-
Application: Improve braking safety and shorten braking distance.
-
Automatic Emergency Braking (AEB) Actuator
-
Function: Automatic Emergency Braking automatically applies braking force to avoid or mitigate a collision when a risk of collision is detected.
-
Application: Improve vehicle safety and reduce traffic accidents.
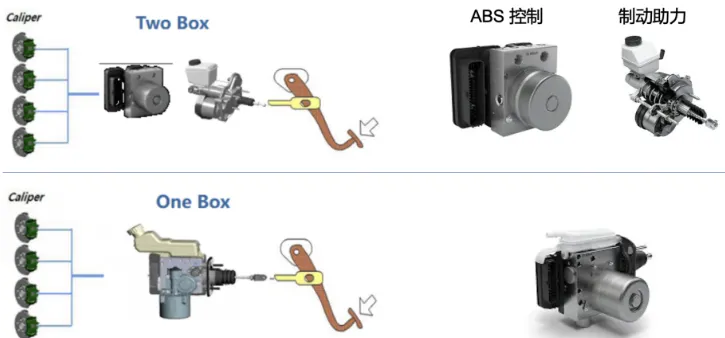
(2) Powertrain actuators
-
Electronic Lock Differential (eLSD) Actuator
-
Function: The electronic differential lock optimizes the vehicle's traction and stability by controlling the torque distribution between the left and right wheels.
-
Application: Improve the vehicle's passability and handling under various road conditions.
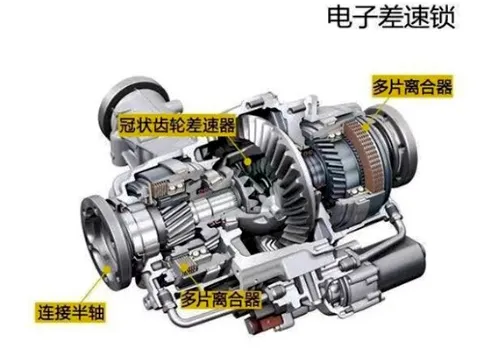
-
Torque Vectoring Actuator
-
Function: The torque vector control system improves the vehicle's steering performance and stability by adjusting the torque output of each wheel.
-
Application: Enhance the vehicle's cornering performance and dynamic response.
(3) Energy recovery system (Regenerative Braking) actuator
-
Function: The energy recovery system converts kinetic energy into electrical energy during braking and stores it in the battery for auxiliary driving.
-
Application: Improve vehicle energy efficiency and extend the driving range of electric vehicles.
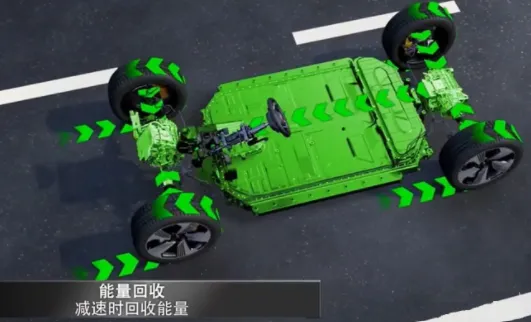
3. Vertical control actuator
(1) Suspension system actuator
-
Active Suspension Actuator
-
Function: Active suspension systems adjust suspension stiffness and damping through electric motors or hydraulic devices, responding to road conditions and driving needs in real time.
-
Application: Improve the ride comfort and handling stability of the vehicle.
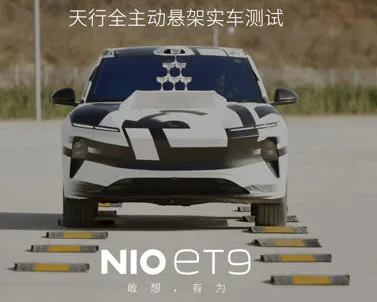
-
Adaptive Suspension Actuator
-
Function: The adaptive suspension system adapts to different road conditions and driving modes by adjusting the suspension damping coefficient.
-
Application: Provide better riding experience and vehicle dynamic response.
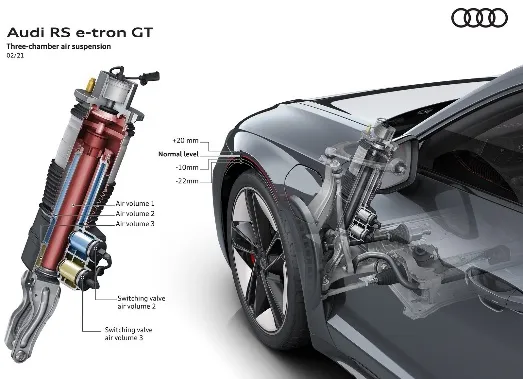
(2) Air Suspension Actuator
-
Function: The pneumatic suspension system adjusts the vehicle height and suspension stiffness through air springs.
-
Application: Improve riding comfort and adapt to different load and road conditions.
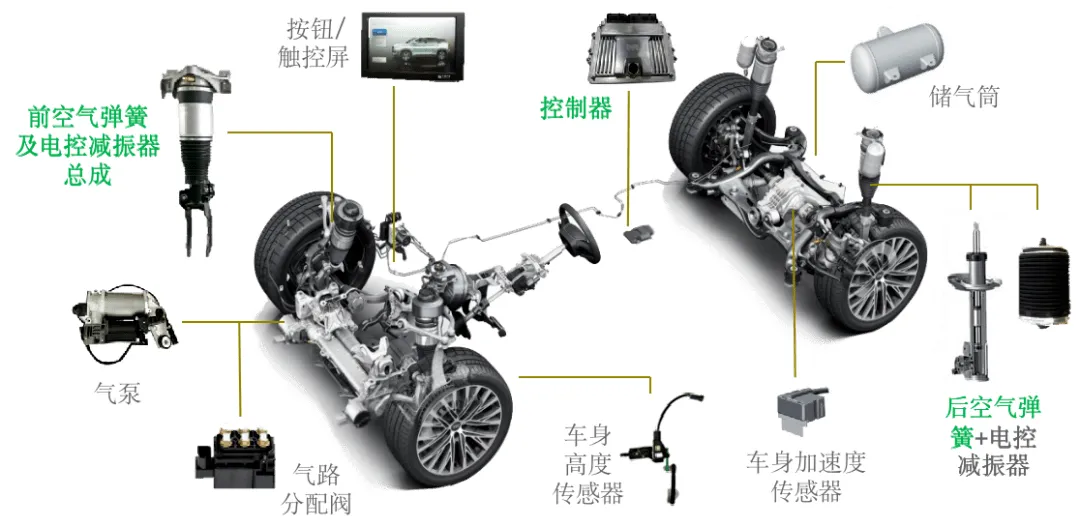
4. Other actuators
Brake-by-Wire Actuator
-
Function: The electronically controlled mechanical brake system realizes braking operation through electronic control, eliminating the traditional hydraulic transmission.
-
Application: Improve the response speed and control accuracy of the braking system.
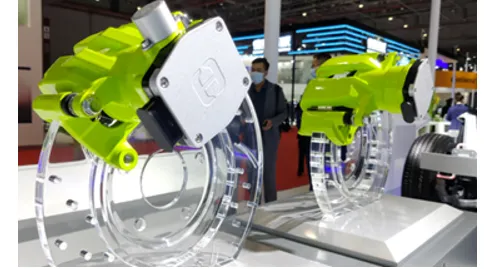
There are many types of actuators in the vehicle chassis, each with different functions, working together to achieve efficient, safe and comfortable motion control of the vehicle. These actuators are coordinated and controlled by the electronic control unit (ECU) and sensor network to ensure the best performance of the vehicle under various driving conditions. With the continuous advancement of technology, the intelligence and integration of chassis actuators will continue to improve, providing a solid foundation for future autonomous driving and intelligent transportation.
#02
There is a close relationship between vehicle motion control (VMC) and vehicle dynamics (VDC) modeling. Vehicle dynamics modeling is the basis of the VMC system. By establishing a mathematical model of the vehicle and simulating the dynamic behavior of the vehicle under various working conditions, precise control of vehicle motion can be achieved. The following is a detailed analysis of the relationship between the two:
1. Overview of Vehicle Dynamics Modeling
Vehicle dynamics modeling refers to describing the motion characteristics and dynamic behavior of a vehicle through mathematical and physical methods. These models usually include the longitudinal, lateral and vertical dynamics of the vehicle, as well as the dynamic characteristics of steering, suspension and tires. Common vehicle dynamics models include the following:
(1) Longitudinal dynamics model
The longitudinal dynamics model mainly describes the behavior of the vehicle during forward movement and braking, including the vehicle's acceleration, deceleration, driving force and braking force. The basic equation is as follows:
????⋅????˙=????drive−????brake−????resistance
Among them, ???? is the vehicle mass, ????˙ is the vehicle acceleration, ????drive is the driving force, ????brake is the braking force, and ????resistance is the sum of air resistance and rolling resistance.
(2) Lateral dynamics model
The lateral dynamics model describes the behavior of the vehicle when turning, including the lateral force, steering angle, and yaw motion of the vehicle. Commonly used models are the Single Track Model and the Double Track Model. The basic equation of the Single Track Model is as follows:
????⋅(????˙????+????⋅???????)=????????????+?????? ??????
???????⋅????˙=????⋅????????????−????⋅????????????
Where ???????? is the lateral velocity, ???? is the yaw rate, ???????????? and ???????????? are the lateral forces on the front and rear axles respectively, ???????? is the moment of inertia of the vehicle about the vertical axis, and ???? and ???? are the distances from the front and rear axles to the center of mass respectively.
(3) Vertical dynamics model
The vertical dynamics model mainly describes the behavior of the vehicle suspension system, including the stiffness and damping characteristics of the suspension, the vertical displacement and acceleration of the vehicle body. The basic equation is as follows:
Previous article:How powerful is the automatic emergency assist braking function of Huawei's Q7? Can it really be far ahead?
Next article:Chery makes another breakthrough in technology, with super hybrid gearbox, fuel consumption less than 1L per 100km
- Popular Resources
- Popular amplifiers
- Car key in the left hand, liveness detection radar in the right hand, UWB is imperative for cars!
- After a decade of rapid development, domestic CIS has entered the market
- Aegis Dagger Battery + Thor EM-i Super Hybrid, Geely New Energy has thrown out two "king bombs"
- A brief discussion on functional safety - fault, error, and failure
- In the smart car 2.0 cycle, these core industry chains are facing major opportunities!
- The United States and Japan are developing new batteries. CATL faces challenges? How should China's new energy battery industry respond?
- Murata launches high-precision 6-axis inertial sensor for automobiles
- Ford patents pre-charge alarm to help save costs and respond to emergencies
- New real-time microcontroller system from Texas Instruments enables smarter processing in automotive and industrial applications
- Innolux's intelligent steer-by-wire solution makes cars smarter and safer
- 8051 MCU - Parity Check
- How to efficiently balance the sensitivity of tactile sensing interfaces
- What should I do if the servo motor shakes? What causes the servo motor to shake quickly?
- 【Brushless Motor】Analysis of three-phase BLDC motor and sharing of two popular development boards
- Midea Industrial Technology's subsidiaries Clou Electronics and Hekang New Energy jointly appeared at the Munich Battery Energy Storage Exhibition and Solar Energy Exhibition
- Guoxin Sichen | Application of ferroelectric memory PB85RS2MC in power battery management, with a capacity of 2M
- Analysis of common faults of frequency converter
- In a head-on competition with Qualcomm, what kind of cockpit products has Intel come up with?
- Dalian Rongke's all-vanadium liquid flow battery energy storage equipment industrialization project has entered the sprint stage before production
- Allegro MicroSystems Introduces Advanced Magnetic and Inductive Position Sensing Solutions at Electronica 2024
- Car key in the left hand, liveness detection radar in the right hand, UWB is imperative for cars!
- After a decade of rapid development, domestic CIS has entered the market
- Aegis Dagger Battery + Thor EM-i Super Hybrid, Geely New Energy has thrown out two "king bombs"
- A brief discussion on functional safety - fault, error, and failure
- In the smart car 2.0 cycle, these core industry chains are facing major opportunities!
- The United States and Japan are developing new batteries. CATL faces challenges? How should China's new energy battery industry respond?
- Murata launches high-precision 6-axis inertial sensor for automobiles
- Ford patents pre-charge alarm to help save costs and respond to emergencies
- New real-time microcontroller system from Texas Instruments enables smarter processing in automotive and industrial applications
- Looking to buy Freescale's 9S12HY64 development board
- Can the MY-R16 board automatically obtain an IP?
- I disassembled a device but couldn't find any information. Can you help me analyze the three electrodes?
- Finally got it done, the full character set of the digital tube defined by myself, everyone is welcome to use it
- This white paper explains how to leverage the power of 5G to empower your product design!
- Which of the two ways of making differential lines of equal length internally is better?
- X-NUCLEO-IKS01A3 Review——by dcexpert
- Can anyone explain this circuit?
- Wireless communication signal propagation
- The 5 yuan proofing board is back