Steer-By-Wire can obtain the relationship between the command target input of the driverless turning and the change of the steering wheel of the car without restraint, and can control the relationship between the steering mechanism and the driving needs, so that the vehicle can be adjusted. It directly controls the precise control of the path and direction of the autonomous driving.
Since the first modern steering system with a steering wheel was installed in a passenger car in 1894, its steering system has gone through five stages:
Early purely mechanical steering systems;
Ford first proposed the hydraulic power steering system;
Toyota's first electronic hydraulic power steering system;
A new generation of electric power steering;
Such as wire-controlled steering systems that are free from mechanical connections and front-wheel active steering systems with active steering functions.
1.1. Electronic Hydraulic Power Steering (EHPS)
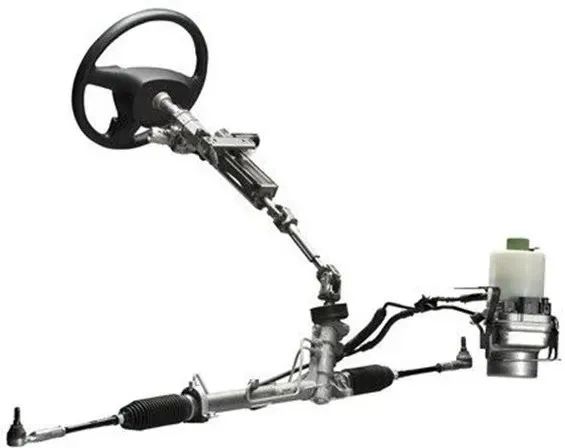
Electronic hydraulic power steering mechanism
1.3. Steer-by-wire (SBW)
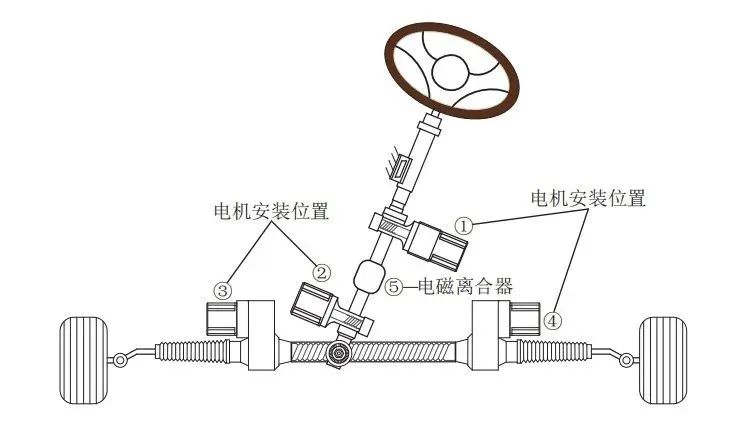
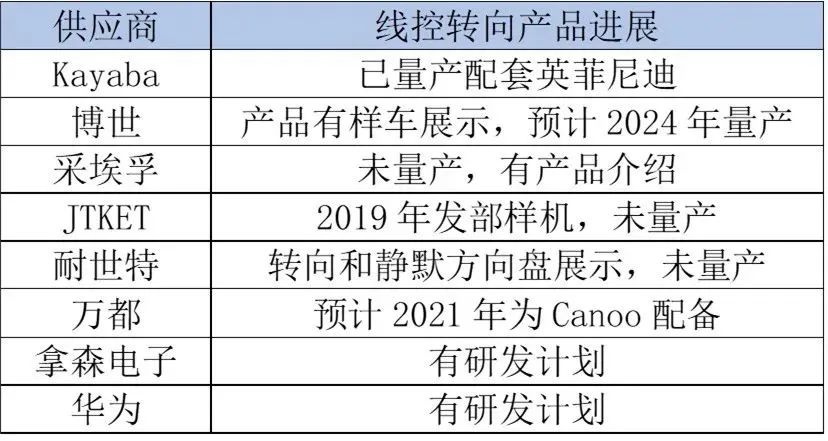
Previous article:Xiaomi invested in another smart chassis company
Next article:Technical Tips | Designing a Position Sensing System with AMR Angle Sensors
- Popular Resources
- Popular amplifiers
- Car key in the left hand, liveness detection radar in the right hand, UWB is imperative for cars!
- After a decade of rapid development, domestic CIS has entered the market
- Aegis Dagger Battery + Thor EM-i Super Hybrid, Geely New Energy has thrown out two "king bombs"
- A brief discussion on functional safety - fault, error, and failure
- In the smart car 2.0 cycle, these core industry chains are facing major opportunities!
- The United States and Japan are developing new batteries. CATL faces challenges? How should China's new energy battery industry respond?
- Murata launches high-precision 6-axis inertial sensor for automobiles
- Ford patents pre-charge alarm to help save costs and respond to emergencies
- New real-time microcontroller system from Texas Instruments enables smarter processing in automotive and industrial applications
- Innolux's intelligent steer-by-wire solution makes cars smarter and safer
- 8051 MCU - Parity Check
- How to efficiently balance the sensitivity of tactile sensing interfaces
- What should I do if the servo motor shakes? What causes the servo motor to shake quickly?
- 【Brushless Motor】Analysis of three-phase BLDC motor and sharing of two popular development boards
- Midea Industrial Technology's subsidiaries Clou Electronics and Hekang New Energy jointly appeared at the Munich Battery Energy Storage Exhibition and Solar Energy Exhibition
- Guoxin Sichen | Application of ferroelectric memory PB85RS2MC in power battery management, with a capacity of 2M
- Analysis of common faults of frequency converter
- In a head-on competition with Qualcomm, what kind of cockpit products has Intel come up with?
- Dalian Rongke's all-vanadium liquid flow battery energy storage equipment industrialization project has entered the sprint stage before production
- Allegro MicroSystems Introduces Advanced Magnetic and Inductive Position Sensing Solutions at Electronica 2024
- Car key in the left hand, liveness detection radar in the right hand, UWB is imperative for cars!
- After a decade of rapid development, domestic CIS has entered the market
- Aegis Dagger Battery + Thor EM-i Super Hybrid, Geely New Energy has thrown out two "king bombs"
- A brief discussion on functional safety - fault, error, and failure
- In the smart car 2.0 cycle, these core industry chains are facing major opportunities!
- The United States and Japan are developing new batteries. CATL faces challenges? How should China's new energy battery industry respond?
- Murata launches high-precision 6-axis inertial sensor for automobiles
- Ford patents pre-charge alarm to help save costs and respond to emergencies
- New real-time microcontroller system from Texas Instruments enables smarter processing in automotive and industrial applications
- An Algorithm for Simultaneous Operation of RF Multi-channels
- Find the period of the following TCL555 output square wave
- PIC18F26K80 INT0 interrupt does not work, see where the problem is
- Application design of MCU in blood analyzer
- GD32E231 DIY Competition (8) - Complete the driver of timer 2
- 4-20mA in industry?
- [NXP Rapid IoT Review] + First Rapid IOT Studio Project
- At 10 am today, Datang NXP will broadcast a live broadcast of [New energy lithium battery management solution with impedance detection function]
- Can anyone help me figure out what chip model this is?
- 【DJI】Automotive Software Engineer Position