Precision Battery Formation and Testing: A Game Changer for Electric Vehicles
Next time you're on Main St., take a look around and see for yourself how the automotive industry is changing: The popularity of electric vehicles (EVs) is reaching a fever pitch. In fact, it is expected that by 2025, up to 10% of vehicles sold will be battery-powered, although currently this proportion is still less than 2%1.
As the electric vehicle market explodes, so does the need for high-performance batteries to power vehicles. Plus, older EV batteries will eventually reach their end and be replaced. As a result, many technology companies are under pressure to bring battery manufacturing equipment to market quickly. However, due to the stringent requirements of electric vehicle batteries, these companies cannot cut corners by using lower-performing devices.
ADI understands that the performance of an electric vehicle is directly proportional to the performance of the battery that powers it. It is this recognition that has led ADI to become a leader in critical battery formation and test stage technologies.
Overview
Company/Industry: Electric vehicle manufacturers and battery formation and testing companies;
Applications: Battery formation and testing;
Challenge: The growth of the electric vehicle market has placed higher demands on battery manufacturers and supply chains, requiring the use of high-quality and reliable battery technology to meet demand;
The goal: Improve battery formation, quality and reliability to increase electric vehicle manufacturers’ manufacturing capabilities and increase supply chain efficiency.
Invest in car batteries and build a quality brand
The high cost of EV batteries keeps EV sticker prices high. In fact, up to 40% of the total cost of an electric vehicle is battery cost. In addition, the final stages of battery production (formation and testing) are particularly challenging, accounting for as much as 20% of the battery cost. But battery manufacturers understand the impact the end product has on their overall brand. Historical data shows that in other markets (cell phones, power tools, gaming, etc.), battery performance can be an important factor in determining the success of a brand.
Battery manufacturers and instrument suppliers realize that expanding production scale and improving production efficiency are key to gaining a share of this emerging electric vehicle industry. But battery manufacturers for smart electric vehicles also know that the key to the problem is not to start production in order to enter the market first, but to put the performance quality of the battery first.
After all, battery formation and testing is a time-consuming process that involves multiple charges and discharges to activate the battery's chemistry. This process is quite arduous and may take two full days to complete. But it is necessary. It helps the battery to be successfully put into practical applications and is crucial to ensuring the reliability and quality of the battery.
Battery formation and precision testing advocate
The level of precision with which a battery is formed and tested can completely determine its performance. Important battery formation and testing capabilities ensure battery quality and safety, and ADI has made a significant contribution to raising standards in this area. ADI continues to develop many new products, reference designs and integrated solutions that provide high accuracy while enabling manufacturers to produce batteries more efficiently and improve factory test capabilities – all of which help expand battery formation and testing scale, allowing customers to scale up electric vehicle production. "Optimizing battery formation can increase battery yield and reduce losses."
"Optimizing battery formation can increase battery yield and reduce losses," said Vikas Choudhary, strategic marketing manager of the Battery Formation and Test Products Division.
A holistic approach using system-level expertise
To reduce battery costs, manufacturers need to consider the entire ecosystem and leverage suppliers' system-level expertise to reduce overall battery test circuit area while increasing the number of channels. It should be noted that both must simultaneously maintain the accuracy, precision, reliability and speed of battery formation and test measurements to ensure that safety, performance and reliability requirements are met.
This is not easy to do. On the front end, the power supply driving the battery charging circuit needs to be tightly controlled. At a deeper level, battery formation and testing requires close monitoring of the current and voltage profiles used during power cycling to prevent overcharging and undercharging of the battery. This ensures safety during testing and maximizes battery life, significantly reducing the total cost of ownership for the end user.
The benefits of working closely with Analog Devices, which has system-level expertise and broad product offerings, extend beyond access to more sophisticated components and modules. It also gives battery manufacturers access to easier-to-use system architecture reference designs, enabling time to market three to four times faster than if battery manufacturers were developing battery formation and test systems from scratch.
More importantly, high system-level accuracy during cell formation and testing (battery charging/discharging) enables power delivery architectures that enable energy recovery across multiple cells. As a result, manufacturers can achieve previously unobtainable high efficiencies, scale up production, and ultimately reduce waste/cost savings, making battery production more cost-effective.
As Analog Devices leads the way in taking on battery formation and test challenges and moving them into safer, more efficient areas, manufacturers now have a partner with system-level experience and a steadfast commitment to high accuracy – one that can help them meet the needs of emerging electric vehicles The market demands for high-quality, high-performance batteries.
ADI battery formation and testing advantages
Technical performance, leveraging the precision required to form cells under repeatable conditions, ensuring consistent, high-performance cells.
System-level expertise enables ADI to design solutions that increase the density and efficiency of the formation and classification processes.
System-level accuracy in cell formation enables manufacturers to utilize excess energy for additional cell formation.
Integrated solutions reduce system size and allow battery manufacturers to install more test equipment in the same space, increasing formation and testing capabilities without requiring more workspace.
refer to
1 David Keohane and Peter Campbell. “Valeo forecasts electric car sales to double.” Financial Times, February 2018.
2 electrive.com, “Global plug-in hybrid number climbs to 5.6 million” (2019)
Previous article:From chips to cars, indispensable
Next article:Hongjing Intelligent Driving and Ambarella start strategic cooperation based on CV3-AD to jointly expand the global market
Recommended ReadingLatest update time:2024-11-16 16:33
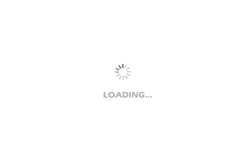
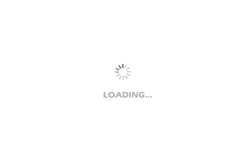
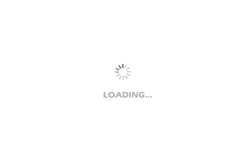
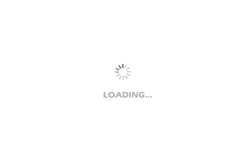
- Popular Resources
- Popular amplifiers
-
FOUNDRY PROCESS QUALIFICATION GUIDELINES – TECHNOLOGY QUALIFICATION VEHICLE TESTING JEP001-3B
-
A review of learning-based camera and lidar simulation methods for autonomous driving systems
-
Evaluating Roadside Perception for Autonomous Vehicles: Insights from Field Testing
-
Battery Management Systems for Electric and Hybrid Vehicles
- Car key in the left hand, liveness detection radar in the right hand, UWB is imperative for cars!
- After a decade of rapid development, domestic CIS has entered the market
- Aegis Dagger Battery + Thor EM-i Super Hybrid, Geely New Energy has thrown out two "king bombs"
- A brief discussion on functional safety - fault, error, and failure
- In the smart car 2.0 cycle, these core industry chains are facing major opportunities!
- The United States and Japan are developing new batteries. CATL faces challenges? How should China's new energy battery industry respond?
- Murata launches high-precision 6-axis inertial sensor for automobiles
- Ford patents pre-charge alarm to help save costs and respond to emergencies
- New real-time microcontroller system from Texas Instruments enables smarter processing in automotive and industrial applications
- Innolux's intelligent steer-by-wire solution makes cars smarter and safer
- 8051 MCU - Parity Check
- How to efficiently balance the sensitivity of tactile sensing interfaces
- What should I do if the servo motor shakes? What causes the servo motor to shake quickly?
- 【Brushless Motor】Analysis of three-phase BLDC motor and sharing of two popular development boards
- Midea Industrial Technology's subsidiaries Clou Electronics and Hekang New Energy jointly appeared at the Munich Battery Energy Storage Exhibition and Solar Energy Exhibition
- Guoxin Sichen | Application of ferroelectric memory PB85RS2MC in power battery management, with a capacity of 2M
- Analysis of common faults of frequency converter
- In a head-on competition with Qualcomm, what kind of cockpit products has Intel come up with?
- Dalian Rongke's all-vanadium liquid flow battery energy storage equipment industrialization project has entered the sprint stage before production
- Allegro MicroSystems Introduces Advanced Magnetic and Inductive Position Sensing Solutions at Electronica 2024
- Car key in the left hand, liveness detection radar in the right hand, UWB is imperative for cars!
- After a decade of rapid development, domestic CIS has entered the market
- Aegis Dagger Battery + Thor EM-i Super Hybrid, Geely New Energy has thrown out two "king bombs"
- A brief discussion on functional safety - fault, error, and failure
- In the smart car 2.0 cycle, these core industry chains are facing major opportunities!
- The United States and Japan are developing new batteries. CATL faces challenges? How should China's new energy battery industry respond?
- Murata launches high-precision 6-axis inertial sensor for automobiles
- Ford patents pre-charge alarm to help save costs and respond to emergencies
- New real-time microcontroller system from Texas Instruments enables smarter processing in automotive and industrial applications