1 Introduction
The performance of the fuel injection system directly affects the working process and performance indicators of the diesel engine. It is a key part of the diesel engine to improve emissions, reduce fuel consumption and improve performance. The traditional diesel locomotive diesel injection pump calibration station is mainly used for the running-in and performance test of the injection pump. Its driving part adopts a thyristor electromagnetic slip clutch stepless speed regulation system to control and display the main shaft speed of the injection pump. Due to the use of separate components, the test sensitivity is low, the setting adjustment is inconvenient and the failure rate is high. At present, foreign injection pump calibration stations use microcomputer control and digital display systems. For this reason, a new type of pump calibration station speed regulation system is designed according to international standards using the 89C51 single-chip microcomputer, which can control the main shaft speed test and adjustment in real time, and transmit the relevant measurement data to the upper PC for display, thereby improving the test sensitivity.
2 System Structure Design
The system design adopts a speed single closed-loop speed control system, as shown in Figure 1. The drive circuit is composed of thyristors and motors, while the control circuit is composed of speed setting, speed feedback, proportional-integral-differential (PID) regulator and thyristor pulse trigger circuit.
The solid line frame in Figure 1 is the hardware design part, which mainly completes the speed regulation function. The dotted line frame is the software design part, which mainly completes the speed setting, speed feedback, deviation signal formation and PID operation.
3 System Hardware Circuit Design
The system hardware design is based on the 89C51 single-chip microcomputer and equipped with necessary peripheral equipment, such as data acquisition, electrical interface, actuator, communication interface and other circuits, as shown in Figure 2. 3CT20/500 thyristors are selected. Since thyristors work in AC circuits, they are not suitable for direct connection with microcomputers. Photocouplers 4N25 are used to isolate the single-chip microcomputer from the output part (thyristor-motor circuit). The ground wire of the output part is grounded, while the power ground wire of the single-chip microcomputer system is suspended and cannot be connected to the ground wire of the AC power supply to avoid the impact of the output part power supply change on the single-chip microcomputer power supply.
The inverting driver 7406 is used as the driver of the input end of 4N25. The excitation coil in the electromagnetic slip clutch is powered by a thyristor half-wave rectifier circuit with a freewheeling diode. The excitation coil is an inductive load, and a freewheeling diode VD6 is connected in parallel at both ends of the coil to smooth the current. The adjustment trigger device uses a single junction tube VBG7. In order to achieve closed-loop speed control of the operating mechanism, it is necessary to detect the spindle speed. The speed sensor uses a magnetoelectric speed sensor. The speed wheel has 120 teeth, and a pulse signal is induced on the speed sensor every time one tooth is turned. In this way, 120 pulses are generated for each rotation of the spindle, and the expression is:
In the formula: P is the number of pulses output by the speed sensor per revolution; T is the specified time; m1 is the number of speed pulses.
The timer/counter of 8155 is operated in timing mode, and the timing time is 10 ms. Its input terminal is connected to the 1 MHz clock signal as the counting frequency, and the output terminal is connected to the interrupt INT0 application terminal of 89C51. The timer/counter T1 of 89C51 works in counting mode. The pulse input of the speed sensor after shaping is input to T1. When the input signal has a negative jump, the counter increases by 1. Every time 10 ms is reached, an interrupt is applied through INT0, and the T1 count value is obtained in the interrupt processing program. The count value is multiplied by 50 to measure the current speed of the motor.
The main component of the fuel injection calibration pump power system is the electromagnetic speed regulating motor, which consists of a single-speed or multi-speed squirrel cage asynchronous motor and an electromagnetic slip clutch. The controller can achieve stepless speed regulation in a large range. The speed expression is:
In the formula: n1 is the synchronous speed, r/min; f1 is the power supply frequency, Hz; p is the number of pole pairs and s is the slip rate.
By adjusting the excitation current in the excitation coil within a certain load range, the slip rate s can be adjusted to achieve the purpose of adjusting the speed. The larger the excitation current, the higher the speed; conversely, the lower the speed.
4 System Software Design
[page]
The system software adopts modular structure design, mainly composed of three modules: PC, 89C51 single-chip microcomputer and communication. Among them, the PC module mainly completes the spindle speed preset and display; the communication module realizes the data transmission between the PC and the single-chip microcomputer; the 89C51 single-chip microcomputer module completes the timing sampling and automatic control of the spindle speed. The main program of its system software is shown in Figure 3. The main program mainly completes system initialization, handshake with the host computer, receives preset parameters, calls the spindle speed program, calls the injection counting program, and calls the data acquisition and transmission program.
Since the control object is a first-order inertia link with pure lag, it is designed as a fast follow-up system as required. In order to improve the rapidity of tracking, when the speed regulation range is too large, the controller output is first made close to the given requirement in the first beat, and then the PI control algorithm is started. The first beat control model is:
Where: U(T) is the current controller output value; U(T-1) is the previous controller output value; N(T) is the current controller given value; N(T-1) is the previous controller given value.
The mathematical model of the PI control algorithm is:
Where: Kp is the proportional coefficient; T is the sampling period; Ti is the integration time constant.
The second beat control model is:
In the formula: K0, K1, K2, K3, P1, P2, P3 are coefficients.
Due to the addition of the integral link, the dynamic performance of the system is affected, the residual error can be eliminated and the control accuracy can be improved.
5 Conclusion
The design system has been successfully applied to the test platform of a diesel engine injection pump for a certain internal combustion locomotive. Research shows that the speed control system of the injection pump calibration platform can automatically control the injection count and spindle speed, realize the digital display and screen display of the spindle speed when measuring oil, and is easy to use and maintain, thereby improving the detection accuracy and automation level.
Previous article:The continuous evolution of rechargeable batteries and charging technology creates new markets beyond EV
Next article:Magna's vision for electric vehicle technology development
Recommended ReadingLatest update time:2024-11-16 17:47
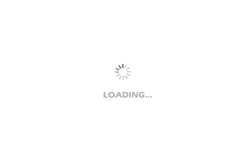
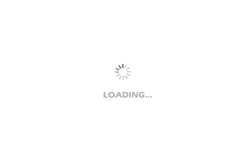
- Popular Resources
- Popular amplifiers
-
西门子S7-12001500 PLC SCL语言编程从入门到精通 (北岛李工)
-
Siemens Motion Control Technology and Engineering Applications (Tongxue, edited by Wu Xiaojun)
-
How to read electrical control circuit diagrams (Classic best-selling books on electronics and electrical engineering) (Zheng Fengyi)
-
MCU C language programming and Proteus simulation technology (Xu Aijun)
- Car key in the left hand, liveness detection radar in the right hand, UWB is imperative for cars!
- After a decade of rapid development, domestic CIS has entered the market
- Aegis Dagger Battery + Thor EM-i Super Hybrid, Geely New Energy has thrown out two "king bombs"
- A brief discussion on functional safety - fault, error, and failure
- In the smart car 2.0 cycle, these core industry chains are facing major opportunities!
- The United States and Japan are developing new batteries. CATL faces challenges? How should China's new energy battery industry respond?
- Murata launches high-precision 6-axis inertial sensor for automobiles
- Ford patents pre-charge alarm to help save costs and respond to emergencies
- New real-time microcontroller system from Texas Instruments enables smarter processing in automotive and industrial applications
- Innolux's intelligent steer-by-wire solution makes cars smarter and safer
- 8051 MCU - Parity Check
- How to efficiently balance the sensitivity of tactile sensing interfaces
- What should I do if the servo motor shakes? What causes the servo motor to shake quickly?
- 【Brushless Motor】Analysis of three-phase BLDC motor and sharing of two popular development boards
- Midea Industrial Technology's subsidiaries Clou Electronics and Hekang New Energy jointly appeared at the Munich Battery Energy Storage Exhibition and Solar Energy Exhibition
- Guoxin Sichen | Application of ferroelectric memory PB85RS2MC in power battery management, with a capacity of 2M
- Analysis of common faults of frequency converter
- In a head-on competition with Qualcomm, what kind of cockpit products has Intel come up with?
- Dalian Rongke's all-vanadium liquid flow battery energy storage equipment industrialization project has entered the sprint stage before production
- Allegro MicroSystems Introduces Advanced Magnetic and Inductive Position Sensing Solutions at Electronica 2024
- Car key in the left hand, liveness detection radar in the right hand, UWB is imperative for cars!
- After a decade of rapid development, domestic CIS has entered the market
- Aegis Dagger Battery + Thor EM-i Super Hybrid, Geely New Energy has thrown out two "king bombs"
- A brief discussion on functional safety - fault, error, and failure
- In the smart car 2.0 cycle, these core industry chains are facing major opportunities!
- The United States and Japan are developing new batteries. CATL faces challenges? How should China's new energy battery industry respond?
- Murata launches high-precision 6-axis inertial sensor for automobiles
- Ford patents pre-charge alarm to help save costs and respond to emergencies
- New real-time microcontroller system from Texas Instruments enables smarter processing in automotive and industrial applications
- [GD32E231 DIY Contest] 05. Automatic Fish Feeding Robot - PWM
- Shenzhen becomes the "world's first 5G city": challenges and business opportunities for the PCB industry
- 【Ended】 R&S Live 【PCI Express Gen 3 Conformance Test】
- Live broadcast at 10 am today [Renesas Electronics Secure IoT Suite provides you with secure cloud connection solutions
- Xun developed Qt for Android for i.MX6ULL Terminator QT application
- Applications of RF Transformers
- RF FilterRF knowledge classics to understand
- 【NXP Rapid IoT Review】+Hello world!
- 5G miniaturized terminal and base station antenna technology
- DIY retro game console based on Raspberry Pi Zero