Some time ago, a friend asked me about this composite current collector technology. After searching for a while, I found two places where this application is available. I think it is necessary to sort out the two pieces of information:
(1) Power battery: The content of the application submitted by Company C at the Hainan New Energy Conference mainly includes a sandwich structure composite current collector of "metal conductive layer-polymer support layer-metal conductive layer". There are many descriptions here, but no pictures. The application material uses a battery cell made for VW that can be punctured by needles as an illustration.
Figure 1 Previous experimental products in 2017
(2) Consumer batteries: This is OPPO's battery in July. I think power batteries and energy storage can also pay attention to the development of current mobile phone batteries. Silicon-doped lithium and composite current collector technologies have all emerged. In OPPO's design, a layer of new composite polymer material is used as the matrix, and two layers of aluminum are plated using a special process, thus forming a sandwich structure current collector. Compared with traditional aluminum foil current collectors, it has higher reliability and can better avoid short circuits between positive and negative electrodes. Combined with the two safety coatings applied on the top and bottom, the final five-layer safety structure is formed.
Let’s sort out these materials first:
1. OPPO's composite current collector technology
OPPO released this battery technology at the "Flash Charge Open Day" held in July. This technology is aimed at the safety of the battery cell itself and the safety of the charging technology. It is named "sandwich safety battery". It is based on a layer of new polymer composite material, plated with two layers of aluminum, and then coated with a safety coating to form a five-layer safety structure "sandwich" sandwich current collector.
Figure 2 Schematic diagram of sandwich battery
When the battery is squeezed or collided by external force, this five-layer current collector can not only greatly reduce the probability of internal short circuit in the battery, but the polymer material in the sandwich layer can also isolate the positive and negative electrodes. OPPO uses two demonstration methods, external impact and needle puncture, to demonstrate the difference between conventional current collectors and composite current collectors.
Figure 3 Protection of composite current collector technology during impact testing
Figure 4 Blocking effect of composite current collector technology during needle puncture
2. C's composite current collector
I will simplify the contents of the application materials:
1) Safety Aluminum foil is simulated by thermal-mechanical load short circuit in the battery, and vacuum vapor deposition technology is introduced to construct a sandwich structure composite current collector of "metal conductive layer-polymer support layer-metal conductive layer". Through the multiple coupling relationship between the mechanical-electrical-thermal properties of the metal layer and the polymer layer, when the short circuit occurs in "point contact", the conductive layer is stressed to crack and peel off at the short circuit point or melt instantly under the high current of the short circuit, and the short circuit current loop is cut off within milliseconds; when the short circuit occurs in "surface contact", the support layer is heated and melted and contracted on the short circuit surface to form a partial collapse of the current collector structure, and the short circuit current loop is cut off before thermal runaway.
Based on this design, the problem of internal short circuit in high-nickel batteries is solved, and the industry problem of thermal runaway caused by internal short circuit in batteries is completely solved.
2) Life and reliability: Integrating nano riveting and three-dimensional conductive repair technology increases the bonding strength between the metal layer and the polymer layer by 10 times, while repairing the conductive attenuation caused by cracks on the metal layer surface, achieving a service life of 15 years. Compared with metals, polymer materials have a lower elastic modulus and form a layered annular sponge structure around the active material layer in the battery. During the battery charging and discharging process, it absorbs the expansion-contraction stress generated by the insertion and removal of lithium ions in the active material layer of the pole piece, maintains the long-term integrity of the pole piece interface, and increases the battery cycle life by 5%.
3) Process Manufacturing: We have developed in-situ passivation and continuous roller welding processes and equipment, which solves the shortcoming of the current collector being difficult to mass-produce due to material and structural changes, and the production cycle has reached 20ppm.
4) Improve energy density The composite current collector uses lightweight polymer materials in the middle layer, which is 50%-80% lighter than pure metal current collectors. At the same time, the thickness of the composite current collector is reduced by 25%-40% compared with pure metal current collectors in the industry, thereby giving more space in the battery to active materials. Traditional pure metal current collectors account for 15% or even more of the battery. As the weight of the composite current collector decreases and the proportion of active materials in the battery increases, the battery energy density is increased by 5%-10%.
As shown below, this picture shows the product displayed by C company when it was at the center of the storm. I think this technology is very important for whether high-nickel batteries will have long-term cost advantages in the future. This battery was actually tested with three different needle penetration depths of 1mm, 5mm and 10mm. The results showed that under the condition of fine needles, it can pass the needle penetration test.
Figure 5 The report given during the debate
summary:
I think this composite current collector technology has already begun to be implemented in the process and production ends. We need to continue to observe it in the future. It will play a decisive role in the overall direction of the technology route.
Previous article:Driving the next generation of electric vehicle systems through distributed architecture
Next article:Tesla showcases new structural battery pack using 4680 cells
Recommended ReadingLatest update time:2024-11-16 22:47
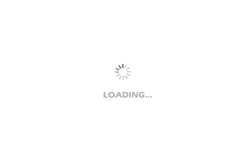
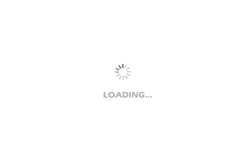
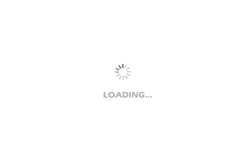
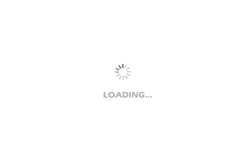
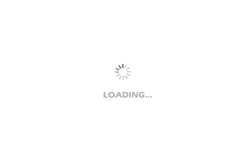
- Car key in the left hand, liveness detection radar in the right hand, UWB is imperative for cars!
- After a decade of rapid development, domestic CIS has entered the market
- Aegis Dagger Battery + Thor EM-i Super Hybrid, Geely New Energy has thrown out two "king bombs"
- A brief discussion on functional safety - fault, error, and failure
- In the smart car 2.0 cycle, these core industry chains are facing major opportunities!
- The United States and Japan are developing new batteries. CATL faces challenges? How should China's new energy battery industry respond?
- Murata launches high-precision 6-axis inertial sensor for automobiles
- Ford patents pre-charge alarm to help save costs and respond to emergencies
- New real-time microcontroller system from Texas Instruments enables smarter processing in automotive and industrial applications
- Innolux's intelligent steer-by-wire solution makes cars smarter and safer
- 8051 MCU - Parity Check
- How to efficiently balance the sensitivity of tactile sensing interfaces
- What should I do if the servo motor shakes? What causes the servo motor to shake quickly?
- 【Brushless Motor】Analysis of three-phase BLDC motor and sharing of two popular development boards
- Midea Industrial Technology's subsidiaries Clou Electronics and Hekang New Energy jointly appeared at the Munich Battery Energy Storage Exhibition and Solar Energy Exhibition
- Guoxin Sichen | Application of ferroelectric memory PB85RS2MC in power battery management, with a capacity of 2M
- Analysis of common faults of frequency converter
- In a head-on competition with Qualcomm, what kind of cockpit products has Intel come up with?
- Dalian Rongke's all-vanadium liquid flow battery energy storage equipment industrialization project has entered the sprint stage before production
- Allegro MicroSystems Introduces Advanced Magnetic and Inductive Position Sensing Solutions at Electronica 2024
- Car key in the left hand, liveness detection radar in the right hand, UWB is imperative for cars!
- After a decade of rapid development, domestic CIS has entered the market
- Aegis Dagger Battery + Thor EM-i Super Hybrid, Geely New Energy has thrown out two "king bombs"
- A brief discussion on functional safety - fault, error, and failure
- In the smart car 2.0 cycle, these core industry chains are facing major opportunities!
- The United States and Japan are developing new batteries. CATL faces challenges? How should China's new energy battery industry respond?
- Murata launches high-precision 6-axis inertial sensor for automobiles
- Ford patents pre-charge alarm to help save costs and respond to emergencies
- New real-time microcontroller system from Texas Instruments enables smarter processing in automotive and industrial applications
- RVB2601 Evaluation Board Trial 5: Remote Audio Acquisition System
- God, please help me find where I am wrong.
- Comparison of three basic triode amplifier circuits
- SinlinxA33 lvds screen configuration
- PCB size measurement, VX9000 optical scanning imaging measuring machine VS imager measurement
- DC Gain of Nanopower Op Amps
- What model can replace the EPM570T144C5 model? Need PIN2PIN compatible
- How does the SPI bus work?
- Xiaomi Mi Band 3 Disassembly
- 17 "Ten Thousand Miles" Raspberry Pi Car——VSCode Learning (Compiling and Debugging)