3D printed solid-state batteries will be mass-produced in Germany in 2021! Energy density will be doubled, and charging speed will be increased by 6 times! Priority will be given to supporting Germany's huge automobile manufacturing industry. Do manufacturers such as BMW/Mercedes-Benz/Volkswagen/Audi/Porsche have a chance to turn around in the era of electric vehicles ?
In January 2021, Antarctic Bear 3D Printing Network learned that the Swiss company Blackstone Resources has made a series of important breakthroughs in its proprietary 3D printed lithium-ion solid-state battery technology. It has been investing in next-generation battery technology through its German subsidiary Blackstone Technology GmbH. This includes patented 3D printing technology and research into battery mass production. Coincidentally, Germany is one of the countries with the most advanced 3D printing technology in the world.
3D printed solid-state batteries have the potential to double the energy density and cut manufacturing costs in half compared to current lithium-ion battery technology.
Comparative advantages of 3D printed solid-state batteries
Some weaknesses faced by current state-of-the-art battery production:
Not flexible enough to support component design that must match product design
It is still too expensive (target: <80 US$/kWh)
Not suitable for future designs, such as all-solid-state batteries
The energy density provided is still too low (target: 600 miles and > 300Wh/kg)
Raw materials are still unsafe
Carbon emissions are still too high
△3D printed "porous" electrodes can improve energy density. The material in the electrode can be printed as a three-dimensional lattice result. The lattice means that the electrode has a larger exposed surface area, which increases the chemical reaction area and makes the battery more efficient. In addition, 3D printed battery modules do not require extra substances to achieve integration. Imagine that Tesla's 85kWh battery pack consists of 7104 batteries, and the weight of the glue and wires that bond 7104 batteries together is quite large. But if these become part of the additive manufacturing process instead of extra materials, the energy density will be greatly improved
Blackstone Technology’s 3D printing process offers distinct advantages over traditional battery designs that use liquid electrolytes: significantly lower costs and greater production flexibility in battery size, all without reliance on electrode chemistry.
△3D printing solid-state battery production workflow
Blackstone’s 3D printed solid-state battery technology addresses these weaknesses:
3D printed lithium-ion battery production is mature and patented, providing maximum flexibility in the production process;
It can save 30% CAPEX and 10% OPEX, while with solid-state technology, it can save 70% CAPEX and 30% OPEX;
The world’s first 3D printing production process that can mass produce solid-state batteries;
It can increase energy density by 20%, and 100% when using solid-state technology;
Leverage its own resources to shorten the supply chain and ensure long-term access to battery materials;
By reducing the drying process by 50%, energy consumption can be reduced by 25%, which is the most important manufacturing cost of battery pack cells - accounting for 45% to 57% of total energy costs.
△The world's first functional battery using printed electrodes has passed the test
Holger Gritzka, CEO of Blackstone Technologies, said: “Our developments to date in 3D printed battery technology pave the way for the mass production of solid-state batteries. In addition to major markets such as the automotive industry, marine applications and new 5G wireless networks will also benefit from the advantages of 3D printed solid-state batteries.”
△ Tesla's stock price has risen to Mars, with a market value of 800 billion US dollars, which is higher than the total market value of a group of traditional car manufacturers such as BMW + Mercedes-Benz + Volkswagen.
Elon Musk has acknowledged the importance of access to next-generation battery technology and the raw materials needed to produce those batteries. Even with new technologies that reduce the amount of battery materials, demand for electric vehicles could soon outstrip the amount of battery materials needed for those vehicles.
Musk expects the next generation of batteries to use less battery metals, such as cobalt, and more nickel and lithium. In fact, demand for all of these metals is likely to increase significantly as Tesla enters the fray with major automakers, which are also starting to roll out electric vehicles and plan to electrify their entire fleets.
3D printed solid-state batteries are being mass-produced
Blackstone Resources has developed and tested 3D printed batteries, funded by the European Horizon 2020 program, and has achieved significant results in battery density, charging cycles and cost. The Swiss company has also developed a workflow that can mass-produce these batteries in various shapes or forms in 2021 using proprietary battery printing technology, with charging speeds up to about six times faster.
In November 2020, Blackstone opened its first 3D printed battery production plant in the Am Fuchsloch Industrial Park in Saxony, Germany, in the town of Debenn, Germany, to support Germany's automotive manufacturing industry and mass-produce next-generation batteries for industrial applications and electric vehicles. The production capacity of the first phase of the plant will reach 0.5 GWh per year.
Relevant insiders told Antarctic Bear 3D Printing Network that the first batch of solid-state battery prototypes have been tested, and many battery composite materials, shells and solid electrolytes required for mass production have been 3D printed. After developing and testing this technology, Blackstone is ready to plan the production of 3D printed solid-state batteries. This will change the development of solid-state batteries. The automated 3D printing production process reduces fixed investment by 70% compared to traditional battery production processes. Solid-state batteries are also safer and do not use flammable liquid electrolytes that are more harmful to the environment.
Blackstone is one of a number of companies vying to develop next-generation battery technology that could beat Tesla to the punch, including solid-state batteries and new advanced manufacturing techniques.
Using 3D printing technology, Keracel of the United States is able to reduce the thickness of the ceramic electrolyte to 100um, with a long-term goal of reaching 15um. These technological advances will enable Keracel ceramic batteries to provide an energy density of 1200Wh/L, which is about twice that of standard lithium-ion batteries, and can meet the high rate needs of industrial and automotive applications.
Of course, for Tesla, because of its high stock price and sufficient capital, it can quickly accelerate its pace through targeted acquisitions.
Previous article:A brief discussion on the battery design of Mercedes-Benz EQA and the latest progress of Tesla CTC
Next article:US research team invents new 3D zinc-manganese nanoalloy anode that charges faster and safer
Recommended ReadingLatest update time:2024-11-16 13:04
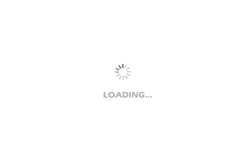
- Popular Resources
- Popular amplifiers
-
Battery Management Systems for Electric and Hybrid Vehicles
-
Optimized drivetrain and new semiconductor technologies enable the design of energy-efficient electr
-
Automotive Ethernet (written by the person in charge of BMW Ethernet)
-
Detailed Explanation of Automotive In-Vehicle Network Technology_2nd Edition
- Car key in the left hand, liveness detection radar in the right hand, UWB is imperative for cars!
- After a decade of rapid development, domestic CIS has entered the market
- Aegis Dagger Battery + Thor EM-i Super Hybrid, Geely New Energy has thrown out two "king bombs"
- A brief discussion on functional safety - fault, error, and failure
- In the smart car 2.0 cycle, these core industry chains are facing major opportunities!
- The United States and Japan are developing new batteries. CATL faces challenges? How should China's new energy battery industry respond?
- Murata launches high-precision 6-axis inertial sensor for automobiles
- Ford patents pre-charge alarm to help save costs and respond to emergencies
- New real-time microcontroller system from Texas Instruments enables smarter processing in automotive and industrial applications
- Innolux's intelligent steer-by-wire solution makes cars smarter and safer
- 8051 MCU - Parity Check
- How to efficiently balance the sensitivity of tactile sensing interfaces
- What should I do if the servo motor shakes? What causes the servo motor to shake quickly?
- 【Brushless Motor】Analysis of three-phase BLDC motor and sharing of two popular development boards
- Midea Industrial Technology's subsidiaries Clou Electronics and Hekang New Energy jointly appeared at the Munich Battery Energy Storage Exhibition and Solar Energy Exhibition
- Guoxin Sichen | Application of ferroelectric memory PB85RS2MC in power battery management, with a capacity of 2M
- Analysis of common faults of frequency converter
- In a head-on competition with Qualcomm, what kind of cockpit products has Intel come up with?
- Dalian Rongke's all-vanadium liquid flow battery energy storage equipment industrialization project has entered the sprint stage before production
- Allegro MicroSystems Introduces Advanced Magnetic and Inductive Position Sensing Solutions at Electronica 2024
- Car key in the left hand, liveness detection radar in the right hand, UWB is imperative for cars!
- After a decade of rapid development, domestic CIS has entered the market
- Aegis Dagger Battery + Thor EM-i Super Hybrid, Geely New Energy has thrown out two "king bombs"
- A brief discussion on functional safety - fault, error, and failure
- In the smart car 2.0 cycle, these core industry chains are facing major opportunities!
- The United States and Japan are developing new batteries. CATL faces challenges? How should China's new energy battery industry respond?
- Murata launches high-precision 6-axis inertial sensor for automobiles
- Ford patents pre-charge alarm to help save costs and respond to emergencies
- New real-time microcontroller system from Texas Instruments enables smarter processing in automotive and industrial applications
- RS-485 communication interface encoder
- FPGA Implementation of Fully Parallel FFT
- RT-Thread has been ported to W600
- MakeCode now supports STM103
- Please help me with the trip zone configuration of TI's 28034!!!
- Is the threshold for electromagnetic wave and antenna major getting lower and lower? Is the reliance on simulation software getting higher and higher?
- EV-HC32F460_1. Unboxing
- The input capture of stm8s cannot enter the interrupt. Please help? ? Thank you!!!
- 10 bit serial controlled analog to digital converter (MS1549)
- [NXP Rapid IoT Review] I2C Program Small Bug