Wireless technology to control charging has become a new development trend. With the widespread application of CANFD in industries such as automotive electronics and rail transportation, how can wireless technology to control charging achieve high-power and fast charging? This article will introduce a simple and feasible solution.
1. Disadvantages of traditional charging methods
As shown in Figure 1, traditional new energy vehicles are charged by charging guns, and each operation requires manual control. During repeated use and plugging, the gap between the charging gun and the vehicle charging port will gradually increase, which is easy to cause discharge and burn the charging gun. In this case, unnecessary maintenance costs are increased, and more seriously, electric shock safety accidents or fires may occur.
In addition, the maximum charging current of the traditional method does not exceed 250A, the charging power is low, and the charging time is relatively long. With the development of automobile intelligence, electrification, and networking, the use of high-power fast charging methods for new energy vehicles in the future will also become a new trend, thereby increasing the charging speed of the car and greatly shortening the charging time. If the charging gun mode is still used, it will only cause greater trouble. So, how should engineers solve this problem and achieve high-power fast charging? The following is a brief introduction.
Figure 1 Traditional charging method
2. Wireless technology controls the charging process
In order to solve the safety risks and cumbersome operation of the traditional charging mode, the charging bow solution came into being. As shown in Figure 2, it is a schematic diagram of wireless technology controlling charging. The first wireless communication module of the charging bow can be paired with the second wireless communication module in the car for wireless communication, completing the charging configuration, so that the charging bow can be lowered and contact charging can be performed without manual intervention, achieving high-power fast charging.
Figure 2 Schematic diagram of wireless technology controlling charging
As shown in Figure 3, it is the whole vehicle architecture of the new generation of intelligent networked vehicles. As can be seen from the figure, in the whole vehicle architecture of the new generation of vehicles, the vehicle Ethernet and CAN FD coexist, and most ECUs communicate through CAN FD. This means that in the process of controlling charging through wireless technology, the new generation of intelligent networked vehicles needs to convert CAN FD to Wifi, thereby realizing CAN FD control communication and wireless technology to control the fast charging of the car.
Figure 3: New generation of intelligent connected vehicle architecture
As shown in Figure 4, the car and the charging bow need to be connected and communicated. It is necessary to build CAN FD to WiFi devices in the car and the charging bow respectively. When the car is close to the charging bow, the wireless connection is completed, the charging bow is controlled to rise and fall, and charging data transmission is realized. CAN FD provides a higher transmission rate and data volume, which can realize the handshake communication between the car and the charging bow faster and more reliably, thereby strengthening the engineer's control over charging. Engineers can view parameters such as battery capacity, voltage, current, etc. in real time through the screen in the cockpit, and can monitor charging faults in real time to ensure charging safety.
Figure 4 New energy vehicle charging bow
3. High-performance WiFi to CAN FD device - CANFDWIFI-100U
With the increasing demand for wireless technology to control charging and the application of CANFD, Guangzhou Zhiyuan Electronics Co., Ltd. has launched a WiFi and CAN (FD)-bus data conversion device - the CANFDWIFI series, which can be used in many occasions such as cloud track wireless charging and new energy vehicle charging. It can help engineers quickly test the performance of charging equipment and complete charging control tasks.
As shown in Figure 5, the CANFDWIFI-100U product integrates a high-speed 528MHz main frequency M7 core processor, and integrates 1 CAN (FD) interface with a maximum baud rate of 5Mbps, 1 10M/100M adaptive Ethernet interface and 1 2.4G/5G WiFi interface. It supports multiple working modes such as TCP Server, TCP Client, UDP, etc. Users can flexibly select TCP Sever/TCP Client/UDP working mode and topology according to their needs, and the required parameter settings can be completed with the configuration software.
Figure 5 CANFDWIFI-100U schematic diagram
The CANFDWiFi-100U product is easy to use. You only need to use the "Network Device Configuration Tool" in the ZCANPRO software to complete a series of parameter configurations. In addition, the CANFDWiFi communication protocol is open and provides a secondary development interface function library (supporting Windows and Linux platforms). At the same time, the product has the following features:
1. Support AP/Station mode to meet various application scenarios
As shown in Figure 6, the unmanned delivery vehicle (or large-scale transport AGV) and the charging bow are equipped with CANFDWiFi-100U converters to complete the handshake matching and realize bow-down charging. Users can view parameters such as battery capacity, voltage, and current in real time, and can monitor charging faults in real time to ensure charging safety.
Figure 6 CANFDWIFI-100U working mode
2. Support high-speed CANFD and compatible with CAN2.0A/B
As shown in Figure 7, the CANFDWiFi series products support the ISO/Bosch CAN FD standard and are compatible with CAN2.0A/B mode transceiver. The data domain baud rate can be configured to 5Mbps at most, and the data length can be configured to 64 bytes at most. It can provide a data load 40 times higher than CAN2.0A/B, providing faster control and data channels for automotive electronics, rail transit, and medical electronics.
Figure 7 CANFDWIFI is compatible with CAN2.0A/B
3. Perfect combination of high-speed CAN FD and high-speed 5.8GHz WiFi
CANFDWiFi-100U integrates 2.4G and 5G WLAN interfaces, complies with IEEE 802.11a/b/g/n/ac standards, and can flexibly select AP/Station mode to complete the interconnection between CAN FD network and WiFi network.
4. Small size, excellent performance
The high-performance WiFi to CAN FD device is compact and exquisite, which makes it easy for users to integrate the device and expand the CAN network. As shown in Figure 8, the longest length of the device is about 3.3 times that of a one-yuan coin.
Figure 8 Equipment size comparison
5. Multiple encryptions improve communication security
CANFDWiFi-100U supports 64-bit and 128-bit encryption/decryption, as well as 256-bit WEP, TKIP or AES keys, which can effectively improve the security of communication between devices, as shown in Figure 9.
Figure 9 CANFDWIFI-100U encryption function
5. Blacklist and whitelist mode improves data security and effectively reduces load
As shown in Figure 10, the configuration tool supports high-efficiency channel filtering. Users can flexibly set black and white lists according to the required messages to achieve efficient use of data.
Figure 10 Blacklist and whitelist mode
6. TCP keep-alive mechanism makes the connection more reliable
As shown in Figure 11, the TCP Server/Client mode connection has a built-in TCP keep-alive mechanism to ensure the reliability of the TCP connection. After the network is disconnected, it will automatically reconnect and establish a stable TCP connection.
Figure 11 TCP keep-alive mechanism
Previous article:Electric vehicle V2G model | The road ahead is long
Next article:Tata Elxsi launches new smart parking technology that teaches vehicles to park themselves
Recommended ReadingLatest update time:2024-11-16 14:56
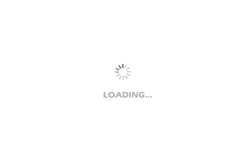
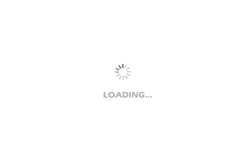
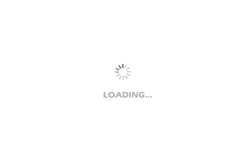
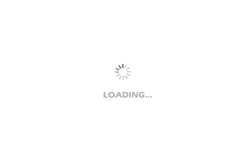
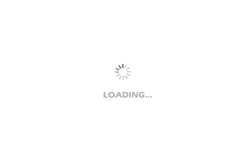
- Popular Resources
- Popular amplifiers
-
New Energy Vehicle Control System Inspection and Maintenance (Edited by Bao Pili)
-
Detailed explanation of big data technology system: principles, architecture and practice (Dong Xicheng)
-
Automotive CAN embedded intrusion detection system based on deep learning
-
Lightweight FPGA-based IDS-ECU architecture for automotive CAN networks
- Car key in the left hand, liveness detection radar in the right hand, UWB is imperative for cars!
- After a decade of rapid development, domestic CIS has entered the market
- Aegis Dagger Battery + Thor EM-i Super Hybrid, Geely New Energy has thrown out two "king bombs"
- A brief discussion on functional safety - fault, error, and failure
- In the smart car 2.0 cycle, these core industry chains are facing major opportunities!
- The United States and Japan are developing new batteries. CATL faces challenges? How should China's new energy battery industry respond?
- Murata launches high-precision 6-axis inertial sensor for automobiles
- Ford patents pre-charge alarm to help save costs and respond to emergencies
- New real-time microcontroller system from Texas Instruments enables smarter processing in automotive and industrial applications
- Innolux's intelligent steer-by-wire solution makes cars smarter and safer
- 8051 MCU - Parity Check
- How to efficiently balance the sensitivity of tactile sensing interfaces
- What should I do if the servo motor shakes? What causes the servo motor to shake quickly?
- 【Brushless Motor】Analysis of three-phase BLDC motor and sharing of two popular development boards
- Midea Industrial Technology's subsidiaries Clou Electronics and Hekang New Energy jointly appeared at the Munich Battery Energy Storage Exhibition and Solar Energy Exhibition
- Guoxin Sichen | Application of ferroelectric memory PB85RS2MC in power battery management, with a capacity of 2M
- Analysis of common faults of frequency converter
- In a head-on competition with Qualcomm, what kind of cockpit products has Intel come up with?
- Dalian Rongke's all-vanadium liquid flow battery energy storage equipment industrialization project has entered the sprint stage before production
- Allegro MicroSystems Introduces Advanced Magnetic and Inductive Position Sensing Solutions at Electronica 2024
- Car key in the left hand, liveness detection radar in the right hand, UWB is imperative for cars!
- After a decade of rapid development, domestic CIS has entered the market
- Aegis Dagger Battery + Thor EM-i Super Hybrid, Geely New Energy has thrown out two "king bombs"
- A brief discussion on functional safety - fault, error, and failure
- In the smart car 2.0 cycle, these core industry chains are facing major opportunities!
- The United States and Japan are developing new batteries. CATL faces challenges? How should China's new energy battery industry respond?
- Murata launches high-precision 6-axis inertial sensor for automobiles
- Ford patents pre-charge alarm to help save costs and respond to emergencies
- New real-time microcontroller system from Texas Instruments enables smarter processing in automotive and industrial applications
- Write EEPROM, write FLASH experience record
- Commonly used algorithms for drones - Kalman filter (Part 9)
- Reset time problem
- Why does DLL not found error appear when running VB with Ginkgo?
- The problem of STM8L151k4t6 with programmed code being damaged by soldering?
- DSP28335 external interrupt configuration process
- Circuit PCB Design
- What is Wi-Fi 6?
- MSP430F5529 Getting Started with Small Examples
- What will the elevators of the future look like?