Since the 21st century, the automobile industry has played a leading role. At the same time, the proportion of electronic equipment in the cost of vehicle manufacturing has increased from 16% to more than 30%. In 2010, the proportion of automobiles equipped with automotive electronics will reach 40%. In the future, components and peripheral products around safety, energy saving, environmental protection, comfort and entertainment will develop faster. In this context, this paper designs and develops an intelligent vehicle safety system based on image processing technology.
2 System Introduction
2.1 Development Platform
This system is based on the EC5-1719CLDNA development board. EC5-1719CLDNA supports Intel CoreDuo/Celeron M low-power processors, and is integrated with the graphics processing core by the Intel945GM chipset. It supports VGA, LVDS, DVI, TV-OUT and dual-screen displays, and has 1 PCI-104, 1 PCIE×4 expansion bus, 4 USB2.0 interfaces, and 2 SATA interfaces.
The development board has expanded a wealth of peripheral hardware devices, using the powerful algorithm technology in the image processing open source code opencv, combined with signal processing technology, to give full play to the high-speed CPU performance of this development board.
2.2 System Framework
The functions of this system are divided into three aspects: safety, communication, and multimedia. Safety includes license plate distance measurement, laser distance measurement, fatigue driving detection, panoramic view system (AVM), alcohol concentration detection and temperature detection. Communication includes GPRS Internet access, GSM calls, GPS navigation, multimedia, media player, including car entertainment system, video acquisition.
The system block diagram is shown in Figure 1.
2.3 Basic functions
The system functions include laser ranging, fatigue detection, alcohol concentration detection, GPS positioning, and panoramic view.
Laser distance measurement measures the distance between a car and possible cars on its left and right sides to determine whether it is safe. If it is not safe, an alarm will be issued. Fatigue detection monitors the time the human eye is closed. If it exceeds a certain time, the driver is considered to be fatigued and an alarm will be issued. Alcohol concentration detection tests the alcohol concentration in the air. If the alcohol concentration exceeds the standard, an alarm will be issued. GPS positioning embeds the GPS system into this system to achieve GPS positioning.
The panoramic surround view system installs four cameras around the vehicle, captures the real-time view through the four cameras, and combines the images collected by the four cameras and displays them on the display screen in the cab. The driver can understand the entire situation around the vehicle at a glance, thereby improving the overall safety factor of the car.
3 Function Implementation
3.1 Functional implementation of laser ranging
The principle diagram is shown in Figure 2. Assuming that the laser beam is completely parallel to the optical axis of the camera, the center of the laser beam is the brightest point in the camera's field of view. When the laser beam shines on the tracking target in the camera's field of view, the camera can capture this point.
It is easy to deduce the distance D:
Where: Num is the number of pixels from the center of the image to the landing point, Rop is the radian value of each pixel, and Offet is the radian error.
The algorithm flow is as follows: first, start the camera, collect video images through the camera, and capture images; use the bright spot detection program to find the bright spot shown by the laser, and if it exists, measure the number of pixels Num from the center of the image; finally, calculate the distance through the formula, and determine whether it is safe by comparing it with the set safety distance. If it is not safe, an alarm will be issued.
3.2 Implementation of Fatigue Driving Detection Function
Studies have shown that when people feel sleepy, their blinking speed slows down and the duration of blinking increases. This system determines whether fatigue occurs by extracting the duration of the driver's eyes closing.
By detecting the face range, determine whether the face exists. If not, the timer is reset and the system returns. If a face is detected, the timer starts and begins counting. At the same time, the eyes are located through facial feature recognition. If the eyes can be located within a certain time slot, it proves that the driver is not in a fatigued driving state. At this time, the timer is reset and the system returns. If the eyes cannot be located within 5S, it is considered that the driver is in a fatigued driving state, and an alarm is issued.
The algorithm flow chart is shown in Figure 3.
3.3 Implementation of alcohol concentration detection function
This system uses the alcohol sensor NAP-66E to measure alcohol concentration. NAP-66E has good linearity, a wide operating temperature range, and can work normally in various harsh environments. Its maximum output voltage is 10mV. Therefore, in order to obtain the alcohol content, the output analog quantity of the alcohol sensor must be amplified by a two-stage amplifier to a voltage value that matches the A/D converter TLC2543. After A/D conversion, the obtained value is properly processed in the MCU, and finally communicates with the PC through the serial port line, and transmits the measured data to the PC in real time, and uses the PC to realize display, alarm and other functions. The alcohol detection chip is applied, and the alcohol detection module is formed through the hardware connection with the single-chip microcomputer, A/D chip, and operational amplifier. The designed circuit is shown in Figure 4.
3.4 Implementation of GPS positioning function
This system uses GARMIN's GPS receiver OEM board - GPS 15H, with RS-232 output, and the interface protocol uses NMEA0183 version 2.00 or 3.00 (optional) ASCII code statements. The data update rate is once per second, and the serial transmission parameters are: baud rate = 9600, data bits = 8 bits, stop bits = 1 bit, no parity check.
When reading GPS data, the system uses the serial port to receive data. The software implementation principle is as follows:
Initialize first and set the serial port to use. The corresponding baud rate is 9600, the data bit is 8 bits, and the stop bit is 1 bit. After the user clicks the receive button, use the query method to read in 1024 bytes to find some strings after GPRMC (Global Position Recommended Minimum Specific). GPRMC includes the valid bits of the data that the program is most concerned about, latitude and longitude. The data format is as follows:
$GPRMC,<1>,<2>,<3>,<4>,<5>,<6>,<7>,<8>,<9>,<10>,<11>,<12> ,<13>
<1> Greenwich Mean Time of the current location, in the format of hhmmss
<2> status, A is a valid position, V is an invalid reception warning, that is, the number of satellites above the current antenna field of view is less than 3.
<3> Latitude, the format is ddmm.mmmm
<4> Indicates the northern and southern hemispheres, N for the northern hemisphere and S for the southern hemisphere
<5> Diameter, the format is dddmm.mmmm
<6> Indicates the eastern and western hemispheres, E for the eastern hemisphere and W for the western hemisphere
<7> Speed on the ground, ranging from 0.0 to 999.9
The data after <8> are not used.
In order to facilitate data reception, the corresponding software is used to shield unnecessary statements, leaving only the GPRMC statement. Since the GPS module obtains valid data in about 90 seconds in the open air after power-on, the 13th bit after the G in GPRMC is found to be the valid data bit.
When 'A' is determined, the following 9 bits are read from the 17th bit in the data segment as latitude display, and the following 10 bits are read from the 29th bit as longitude display. Then the received GPS longitude and latitude are automatically called to the map in the library through appropriate conversion, and the current location is indicated by a red dot on the map.
3.5 Implementation of Panoramic View Function
The panoramic view system has four cameras installed on the front grille, left and right side exterior mirrors and tailgate of the vehicle. The camera has a wide-angle lens and can take real-time wide-angle photos. The software is developed using the DirectShow development kit. Using DirectShow to develop applications can easily capture data from acquisition cards that support the WDM driver model, and perform corresponding post-processing or even store it in a file.
Previous article:Connecting cars, people and society: NEC Networks' vision for in-vehicle intelligent communication system
Next article:Application of TMS320VC5402 in Automobile Anti-collision Warning Radar
Recommended ReadingLatest update time:2024-11-16 16:20
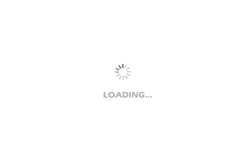
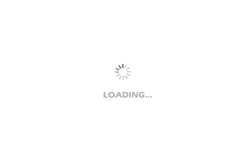
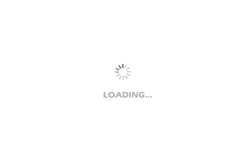
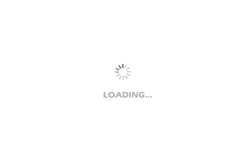
- Popular Resources
- Popular amplifiers
- Car key in the left hand, liveness detection radar in the right hand, UWB is imperative for cars!
- After a decade of rapid development, domestic CIS has entered the market
- Aegis Dagger Battery + Thor EM-i Super Hybrid, Geely New Energy has thrown out two "king bombs"
- A brief discussion on functional safety - fault, error, and failure
- In the smart car 2.0 cycle, these core industry chains are facing major opportunities!
- The United States and Japan are developing new batteries. CATL faces challenges? How should China's new energy battery industry respond?
- Murata launches high-precision 6-axis inertial sensor for automobiles
- Ford patents pre-charge alarm to help save costs and respond to emergencies
- New real-time microcontroller system from Texas Instruments enables smarter processing in automotive and industrial applications
- Innolux's intelligent steer-by-wire solution makes cars smarter and safer
- 8051 MCU - Parity Check
- How to efficiently balance the sensitivity of tactile sensing interfaces
- What should I do if the servo motor shakes? What causes the servo motor to shake quickly?
- 【Brushless Motor】Analysis of three-phase BLDC motor and sharing of two popular development boards
- Midea Industrial Technology's subsidiaries Clou Electronics and Hekang New Energy jointly appeared at the Munich Battery Energy Storage Exhibition and Solar Energy Exhibition
- Guoxin Sichen | Application of ferroelectric memory PB85RS2MC in power battery management, with a capacity of 2M
- Analysis of common faults of frequency converter
- In a head-on competition with Qualcomm, what kind of cockpit products has Intel come up with?
- Dalian Rongke's all-vanadium liquid flow battery energy storage equipment industrialization project has entered the sprint stage before production
- Allegro MicroSystems Introduces Advanced Magnetic and Inductive Position Sensing Solutions at Electronica 2024
- Car key in the left hand, liveness detection radar in the right hand, UWB is imperative for cars!
- After a decade of rapid development, domestic CIS has entered the market
- Aegis Dagger Battery + Thor EM-i Super Hybrid, Geely New Energy has thrown out two "king bombs"
- A brief discussion on functional safety - fault, error, and failure
- In the smart car 2.0 cycle, these core industry chains are facing major opportunities!
- The United States and Japan are developing new batteries. CATL faces challenges? How should China's new energy battery industry respond?
- Murata launches high-precision 6-axis inertial sensor for automobiles
- Ford patents pre-charge alarm to help save costs and respond to emergencies
- New real-time microcontroller system from Texas Instruments enables smarter processing in automotive and industrial applications
- Anxinke NB-IoT module evaluation-Shangdian
- After more than two months of hard work, it is finally finished. Haha
- Live Review: Renesas Electronics R-Car Advanced Driver Assistance System Solution
- TI CC2531 USB Evaluation Module Kit
- Lantern with capacitive touch support
- TI's active equalization solution
- After the ZIGBEE3.0 online seminar this morning, have you DIYed a home automation control system?
- Overcome last-minute requirement changes with small, leaded SOT-23 thin multiplexers
- Where can I find older ICs?
- Make ADAS technology more popular in vehicles