0 Preface
In recent years, with the application of fieldbus technology and embedded technology in the field of industrial control, it has brought great changes to the entire manufacturing industry and greatly improved the level of productivity development. This paper designs an embedded CNC system based on the ARM9 series microprocessor S3C2440 and the professional motion chip MCX314As, and transplants the tailored open source Linux operating system into the microprocessor to enable it to have multi-task processing capabilities. The CNC system has the advantages of simple structure, low cost, high interpolation accuracy, etc. It is an economical CNC system that meets the new generation of open standards. By expanding the CAN bus interface circuit on ARM, the embedded CNC system is networked using CAN bus technology to form a LAN CNC processing network based on CAN bus. CAN bus has outstanding reliability, real-time and flexibility in data communication, and is particularly suitable for the interconnection of industrial field automation equipment. According to the actual situation, considering the special requirements of internal CNC networking processing in the enterprise, the use of CAN bus to connect the industrial field embedded CNC system is of great significance to the construction of a new type of LAN embedded CNC system.
1 Hardware structure of the network system
The overall block diagram of the networked embedded CNC system based on CAN bus designed in this paper is shown in Figure 1: In the industrial field, an industrial computer or an industrial laptop can monitor the embedded CNC system connected to the CAN bus. By installing the monitoring software on the main monitoring computer, the CNC machining program is processed to obtain the data files required for machining. The monitoring computer can be connected to the CAN-bus network through the USB bus through the USBCAN intelligent CAN interface card to transfer the machining data files to the embedded CNC system. S3C2440 receives the machining data files from the CAN bus through the extended CAN bus interface circuit, and then starts the data transmission processing program, and transmits the data to the motion control chip MCX314As through the bus interface to realize the control of MCX314As. MCX314As performs corresponding interpolation calculations on the received data processing files and then outputs pulse levels to control the motor operation.
Figure 1 Overall block diagram of system architecture
Overall structure of embedded CNC system The embedded CNC system mainly consists of ARM9-based S3C2440 main control board and professional motion control chip MCX314As. Its hardware structure diagram is shown in Figure 2.
Figure 2 Hardware structure diagram of embedded CNC system
The main frequency of the microprocessor S3C2440 can reach up to 533MHz, which fully meets the multi-task processing requirements of the CNC system. The chip is based on the ARM920T core, adopts a 5-stage pipeline and Harvard structure, and has the advantages of small size, low power consumption, low cost, and high performance. MCX314As is a powerful motion control chip. It is a single chip that can control 4-axis pulse sequence output to drive servo motors and stepper motors. Linear and circular interpolation can be performed on any two axes.
2 CAN controller hardware structure
The S3C2440 main control board does not have an integrated CAN controller circuit. The CAN bus interface can be expanded through the SPI bus interface to achieve data communication between the microprocessor and the CAN bus controller, so that the embedded CNC system can be connected to the CAN bus network. The CAN controller expansion circuit is shown in Figure 3. The microprocessor communicates with the MCP2510 through the SPI interface.
Figure 3 CAN controller circuit schematic
The CAN protocol controller uses the MCP2510 controller, which supports technical protocol specifications such as CAN2.0A and CAN2.0B. MCP2510 can be powered in the range of 3V to 5.5V, so it can be directly connected to a 3.3VI/O embedded processor. The system structure is simple, and the SPI serial interface between the processor reduces the physical connection of the bus and improves the reliability of the system. It can send and receive standard and extended messages, and the communication rate can reach 1Mb/s. MCP2510 also includes three transmit buffers and two receive buffers, which can reduce the management burden of the microprocessor. The data transmission rate of its SPI bus interface can reach 5Mb/s.
The CAN bus transceiver uses TJA1050. The design of TJA1050 uses the latest EMC technology. It uses advanced insulating silicon technology for processing and has good anti-electromagnetic interference performance.
Write the driver of CAN bus controller MCP2510 in Linux operating system. The design of CAN bus communication program can be divided into three modules: sending data, receiving data and interrupt processing. Tests prove that the written CAN driver is correct.
3 Software Structure of Network System
The networked software structure of the embedded CNC system based on the CAN bus mainly refers to the preprocessing part of the CNC machining code on the industrial computer. This part of the functions includes reading in the NC machining program, editing the NC machining program, lexical checking, syntax checking, decoding, tool compensation processing and data saving. The processed data is stored in a fixed format data file in turn. If there are fixed loops, jump instructions and special point intersections, the corresponding subroutine is required for processing, and then the data is modified in the data. The preprocessing flow chart of the CNC machining code by the industrial computer is shown in Figure 4. After starting the system software, the system first loads the data information saved after the last system operation and the system status information, and prompts whether to perform zeroing of the origin, etc. Then the system calls in the CNC machining program and performs syntax, lexical and other checks. After the check is correct, the corresponding algorithm is used to calculate according to the preparation function word, auxiliary function word, T function, H function, etc. of the CNC machining program segment, so as to obtain data with tool compensation, and these data and the corresponding preparation function word, auxiliary function word, tool number, tool compensation number and other function words are saved in a fixed format data file. After the industrial computer has processed the data, it will transfer the data to S3C2440 through the CAN bus. Then S3C2440 will process the data accordingly and send it to the motion control board through the bus interface. The motion control board will output control pulses to the servo system through complex interpolation calculations to control the motor.
Figure 4 Flowchart of preprocessing of CNC machining code by industrial computer
4 Conclusion
With the widespread application of fieldbus and embedded technology in the control field, CAN bus has become the mainstream of industrial network with its significant advantages such as high reliability, strong real-time performance and easy implementation. The designed embedded CNC system based on ARM and motion control chip has good openness, high performance and low cost. The networked architecture of embedded CNC system based on CAN bus can realize online automatic monitoring of the processing process of multiple CNC machine tools. The system has high integration, high intelligence, good structural and functional scalability, and is safe and reliable. The transformation of this research result has a certain positive role in promoting the networked embedded CNC system and has positive reference significance for the future development of flexible manufacturing system (FMS).
Previous article:PWM output program of LPC210X
Next article:Stepper Motor Control System Based on Cortex-M3 Processor
Recommended ReadingLatest update time:2024-11-16 13:55
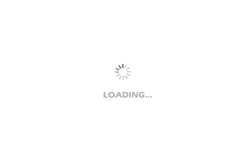
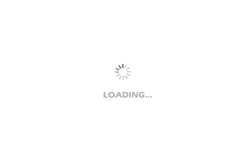
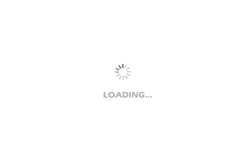
- Popular Resources
- Popular amplifiers
Professor at Beihang University, dedicated to promoting microcontrollers and embedded systems for over 20 years.
- Innolux's intelligent steer-by-wire solution makes cars smarter and safer
- 8051 MCU - Parity Check
- How to efficiently balance the sensitivity of tactile sensing interfaces
- What should I do if the servo motor shakes? What causes the servo motor to shake quickly?
- 【Brushless Motor】Analysis of three-phase BLDC motor and sharing of two popular development boards
- Midea Industrial Technology's subsidiaries Clou Electronics and Hekang New Energy jointly appeared at the Munich Battery Energy Storage Exhibition and Solar Energy Exhibition
- Guoxin Sichen | Application of ferroelectric memory PB85RS2MC in power battery management, with a capacity of 2M
- Analysis of common faults of frequency converter
- In a head-on competition with Qualcomm, what kind of cockpit products has Intel come up with?
- Dalian Rongke's all-vanadium liquid flow battery energy storage equipment industrialization project has entered the sprint stage before production
- Allegro MicroSystems Introduces Advanced Magnetic and Inductive Position Sensing Solutions at Electronica 2024
- Car key in the left hand, liveness detection radar in the right hand, UWB is imperative for cars!
- After a decade of rapid development, domestic CIS has entered the market
- Aegis Dagger Battery + Thor EM-i Super Hybrid, Geely New Energy has thrown out two "king bombs"
- A brief discussion on functional safety - fault, error, and failure
- In the smart car 2.0 cycle, these core industry chains are facing major opportunities!
- The United States and Japan are developing new batteries. CATL faces challenges? How should China's new energy battery industry respond?
- Murata launches high-precision 6-axis inertial sensor for automobiles
- Ford patents pre-charge alarm to help save costs and respond to emergencies
- New real-time microcontroller system from Texas Instruments enables smarter processing in automotive and industrial applications
- FPGA technology introduction and FPGA application fields
- What is a recording digital pressure gauge? In what fields is it used?
- Basic learning of programming
- [Synopsys IP Resources] Automotive cybersecurity starts with chips and IP
- From design to market launch - how many batons are needed in this 5G terminal relay race?
- Ferroelectric Random Access Memory (F-RAM) and Device System Design
- 【FAQ】Secure Boot of Microprocessors | Microchip Security Solutions Seminar Series 7
- Application of “C2000+TMS570” dual-chip solution in automotive electric drive functional safety
- The role of capacitors and inductors in circuits
- I recently played with RTT's MicroPython on STM32407, and the IDE is really easy to use.