1 Introduction
ADuC812 is a high-performance single-chip microcomputer produced by ADI (Analog Device Inc) in the United States. It is a fully integrated 12-bit data acquisition system. It integrates a high-performance self-calibrated multi-channel ADC (8-channel 12-bit high-precision), 2 12-bit DACs and a programmable 8-bit MCU (compatible with 8051) in the chip. There are 8kB flash/electrically erasable program memory and online download/debugging/programming functions, 640B flash/electrically erasable data memory, 256B on-chip data memory and a core compatible with 8051. In addition, the MCU supports functions including watchdog timer, power monitor and ADC DMA function. At the same time, it provides 32 programmable I/O lines, I2C-compatible serial ports, SPI serial interfaces and standard UART serial interfaces for multi-processor interfaces and I/O expansion. The MCU core and analog converter have normal, idle and power-down working modes. The device can operate at 3V and 5V voltages within the industrial temperature range, providing a flexible power management solution suitable for low-power applications.
2 System structure and main features
The structural block diagram of the ADuC812 microcontroller is shown in Figure 1. The main features are as follows:
(1) It has a high-speed (200 kSPS) 8-channel 12-bit high-precision ADC, an on-chip 40×10-6/℃ voltage reference, and an on-chip integrated temperature sensor. The ADC of the ADuC812 microcontroller has three operating modes: single-step or continuous conversion mode can be executed by software or by adding the conversion signal to the external pin convst; single-step or continuous conversion mode can be executed by using timer T2 to generate the trigger signal for A/D conversion; and the ADC is configured to work in DMA mode. In DMA mode, the ADC continuously samples and automatically writes the sampling results to the predetermined external RAM space without any intervention from the MCU core. This mode can achieve 200 kSPS high-speed A/D conversion. The DMA mode is particularly suitable for storage test systems that require high-speed sampling data streams.
(2) The DPP data page pointer can access a large external data memory with a maximum capacity of 16MB. ADuC812 has an extended 64kB program memory and 16MB data memory. Figure 2 shows the interface circuit for the extended 16MB data memory. P0 is a time-division multiplexed address/data bus. It first sends out the low byte of the data pointer (DPL) as the low address, which is latched into the low address latch by ALE, and then gives out the data (during write operation) or becomes high impedance (during read operation), and the SRAM loads the data into the data bus. At the same time as the P0 port sends out the low byte of the data pointer, the P2 port sends out the data pointer page byte (DPP), which is latched into the high address latch by ALE, and then gives out the high byte of the data pointer (DPH) as the middle address. When the P2 port has no external latch, DPP is ignored, and the ADuC812 accesses the external 64kB data memory like the 8051.
(3) ADuC812 can operate in a low-voltage, low-power power-saving mode. It can operate at 3V or 5V and has normal, idle, and power-down modes. The chip can be controlled by software to switch from normal mode to idle mode, or to power-down (shutdown) mode. In idle mode, the oscillator continues to work but is not connected to the chip core. The on-chip peripherals can receive clock signals and are active. In power-down mode, the oscillator stops working and all on-chip peripherals are turned off. When the chip receives a hardware reset signal or is powered on again, it will recover from power-down mode to normal operating mode. In power-down mode, the total current consumed by ADuC812 is approximately 5uA.
3 Application in Storage Test System
Since the ADuC812 microcontroller has the performance of high-speed and high-precision ADC conversion, flexible power management scheme and access to large-capacity external data storage, the ADuC812 microcontroller is the first choice in the design of storage test system. Figure 3 is a functional diagram of the downhole oil and gas pressure storage test system. The system consists of a host module, a power module, a power monitoring module, a data acquisition module, a data transmission module and a data processing and analysis module. The host module is the core part of the system, which consists of an ADuC812 microcontroller, a reset circuit, a clock oscillation circuit, an address latch and an external RAM chipset. The power module is composed of a boost circuit, a voltage regulator circuit and a feedback circuit. The lithium battery pack inputs 7.2V voltage to the power module, and the power module outputs +12V voltage to the data acquisition module and provides a +5V stable working voltage to the entire system. The power monitoring module consists of a monitoring circuit and an indication circuit. It monitors the output of the power supply from time to time. When it is lower than the normal range, it promptly notifies the microcontroller to save the relevant data, close the relevant ports, and issue a low power indication, and the system enters the power-off working mode. The data acquisition module is composed of a pressure sensor with a range of 0~100MPa, a correction circuit and a signal operational amplifier to complete the data acquisition and amplification functions. The data transmission module is composed of a dedicated PC232 interface conversion circuit, which is the channel for data transmission between the single-chip microcomputer and the microcomputer. The data processing and analysis module has data filtering function, data comparison function, chart display function, chart editing function, chart printing function and automatic test report generation function.
In this storage test system, the selection of the trigger point is the key point and also the technical difficulty of the system. The test of deep well oil and gas pressure requires that the test system must be able to accurately track the changes in oil and gas pressure at the moment of armor-piercing projectile detonation, and record the pressure changes during this period in real time. If the trigger point is started too early, due to the limitation of storage space, some practical data will inevitably be lost; if the trigger point is started late, the important oil and gas pressure peak at the moment of detonation will be lost, resulting in test failure. Therefore, the control of the trigger point in the storage test system is particularly important (due to space limitations, it will not be described in detail). The ADuC812 microcontroller works in DMA mode during sampling.
4 Conclusion
In the process of developing the downhole oil and gas pressure storage test system, a large amount of Chinese and English materials were consulted for the selection of single-chip microcomputers. Finally, ADuC812 was selected as the single-chip microcomputer of the system. It not only has a small package size, but also almost all the high-performance hardware and functions required by the test system are integrated on the chip. The system is stable and reliable after use.
Previous article:Improvement of microcontroller driven piezoelectric buzzer
Next article:Introduction to RAM testing methods based on several commonly used single-chip microcomputer systems
Recommended ReadingLatest update time:2024-11-16 17:58
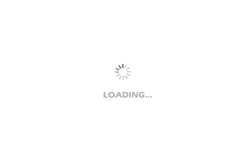
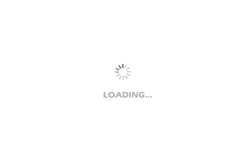
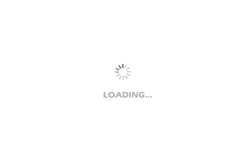
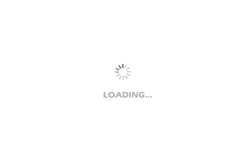
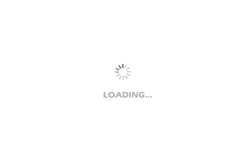
- Popular Resources
- Popular amplifiers
-
Wireless Sensor Network Technology and Applications (Edited by Mou Si, Yin Hong, and Su Xing)
-
Modern Electronic Technology Training Course (Edited by Yao Youfeng)
-
Modern arc welding power supply and its control
-
Small AC Servo Motor Control Circuit Design (by Masaru Ishijima; translated by Xue Liang and Zhu Jianjun, by Masaru Ishijima, Xue Liang, and Zhu Jianjun)
Professor at Beihang University, dedicated to promoting microcontrollers and embedded systems for over 20 years.
- Innolux's intelligent steer-by-wire solution makes cars smarter and safer
- 8051 MCU - Parity Check
- How to efficiently balance the sensitivity of tactile sensing interfaces
- What should I do if the servo motor shakes? What causes the servo motor to shake quickly?
- 【Brushless Motor】Analysis of three-phase BLDC motor and sharing of two popular development boards
- Midea Industrial Technology's subsidiaries Clou Electronics and Hekang New Energy jointly appeared at the Munich Battery Energy Storage Exhibition and Solar Energy Exhibition
- Guoxin Sichen | Application of ferroelectric memory PB85RS2MC in power battery management, with a capacity of 2M
- Analysis of common faults of frequency converter
- In a head-on competition with Qualcomm, what kind of cockpit products has Intel come up with?
- Dalian Rongke's all-vanadium liquid flow battery energy storage equipment industrialization project has entered the sprint stage before production
- Allegro MicroSystems Introduces Advanced Magnetic and Inductive Position Sensing Solutions at Electronica 2024
- Car key in the left hand, liveness detection radar in the right hand, UWB is imperative for cars!
- After a decade of rapid development, domestic CIS has entered the market
- Aegis Dagger Battery + Thor EM-i Super Hybrid, Geely New Energy has thrown out two "king bombs"
- A brief discussion on functional safety - fault, error, and failure
- In the smart car 2.0 cycle, these core industry chains are facing major opportunities!
- The United States and Japan are developing new batteries. CATL faces challenges? How should China's new energy battery industry respond?
- Murata launches high-precision 6-axis inertial sensor for automobiles
- Ford patents pre-charge alarm to help save costs and respond to emergencies
- New real-time microcontroller system from Texas Instruments enables smarter processing in automotive and industrial applications
- A newbie needs help. What are the sensors that can detect tiny distances?
- [NXP Rapid IoT Review] + First impressions
- 【Xianji HPM6750】Review and unboxing
- Who is proficient in medical regulations? To make medical devices or medical equipment, you need to understand or be proficient in the following regulations
- Live broadcast today at 10:00 AM | Omron relay/switch/connector solutions for photovoltaic inverters/energy storage systems
- How difficult is it to produce domestic automotive-grade MCU?
- Recently I made a [51 MCU building block graphical Chinese programming software/C language code generator/circuit simulation]
- Regarding the use of serial ports for ESP32 MicroPython - Thanks!
- Qorvo Design Tools - The Go-to Resource for RF Projects
- FPGA Learning