Overall system design
This system uses PIC690 microcontroller as the main control chip and thyristor as the main switch device. The design goal is to keep the output DC voltage stable, the output voltage ripple small, the AC output current THD low, and the performance reliable.
The main circuits of the system include: three-phase bridge half-controlled rectifier circuit, synchronous signal sampling circuit, single-chip control circuit, and thyristor trigger circuit. First, the synchronous signal is obtained by the synchronous signal sampling circuit and sent to the integrated trigger chip TC787. After zero detection, the corresponding delay is performed to achieve phase shift. The ADC in the single-chip microcomputer is responsible for collecting the DC bus voltage, and the given output is adjusted through PI operation according to the deviation between the set value and the actual value of the voltage. The PIC single-chip microcomputer outputs the reference value of the voltage to TC787, and TC787 realizes the phase shift triggering of the thyristor to achieve rectification and voltage regulation. The overall block diagram of the hardware circuit is shown in Figure 1.
Figure 1 Overall block diagram of system hardware
Main circuit design
The main circuit adopts a three-phase bridge semi-controlled rectifier circuit, and the DC measurement adopts an LC filter current structure. The main current schematic diagram is shown in Figure 2. The semi-controlled bridge selects SEMIKRON's SKDH146/120-L100 module, which has a rated current of 140A and a rated voltage of 1200V. The DC side adopts an LC filter circuit structure, which is better than a single capacitor filter. In addition, the current THD on the AC input side can also be improved. The main harmonic content on the DC side is 6 times the power frequency and an integer multiple of 6. When designing LC low-pass filtering, it is necessary to avoid resonance caused by high-content harmonics. In this design, an inductor of 5mH and a filter capacitor of 480μF are selected.
Figure 2 Main circuit structure
The three-phase voltage obtained from the power grid is shaped by the synchronization circuit and sent to the integrated trigger chip TC787 pin 18AT, pin 2 BT and pin 1CT. TC787 integrates 3 zero-crossing and polarity detection units, 3 sawtooth wave forming units, 3 comparators, 1 pulse generator, 1 anti-interference locking circuit and 1 pulse distribution and drive circuit digital given phase shift control voltage, which can automatically identify the phase sequence.
Control circuit design
PIC16F690 is used as the control chip. The PIC16F690 microcontroller has a built-in 10-bit AD; wide operating voltage (2.0~5.5V); low power consumption; PWM output function; built-in crystal oscillator. The chip's built-in 10-bit AD is used to convert the collected DC side voltage. In order to reduce hardware costs, a voltage divider resistor is directly used instead of a voltage sensor to collect the DC side voltage. The voltage on the voltage divider resistor passes through two reverse proportional circuits to the microcontroller. The analog ground and signal ground of the microcontroller are directly connected (can also be connected through magnetic beads to reduce interference). The PIC16F690 microcontroller enables or disables the output of the chip TC787 through an IO port, as shown in Figure 3. When the I/O port RC3 of the PIC microcontroller outputs a high level (+5V), the Lock port is a low level; when the I/O port RC3 of the microcontroller outputs a low level, Lock is a high level (+15V). Select an IO port as the given signal of the reference voltage of TC787, use PWM pulse mode, adjust the duty cycle to adjust the output voltage, the PWM wave passes through an RC low-pass filter to become an approximate DC signal, use this signal as the reference voltage given Uref, its range is 0 ~ 5V. Since the given input range required by the chip TC787 is 0-15V, the PWM wave needs to pass through an optocoupler for level conversion, as shown in Figure 3. [page]
Figure 3 Control circuit hardware structure
The grid voltage is input to TC787 through a synchronous transformer. The 6th pin of TC787 outputs a double pulse when high or a single wide pulse when low. Pins 12, 11, and 10 are the trigger output terminals of A, B, and C respectively, and are output to the thyristor through a pulse transformer.
Trigger drive circuit design
The trigger chip is a high-performance thyristor three-phase phase-shift trigger integrated circuit TC787. TC787 can work with a single power supply or dual power supplies. It is mainly suitable for three-phase thyristor phase-shift trigger and three-phase power transistor pulse width modulation circuits to form a variety of AC speed regulation and current conversion devices. The internal structure of TC787 is shown in Figure 4.
Figure 4 TC787 chip internal structure
In this design, TC787 is powered by 15V, Pin 4 (Vr): Phase shift control voltage input terminal. The input voltage of this terminal directly determines the phase shift range of the output pulse of TC787/TC788, and is connected to the output of a given link in the application. Pin 5 (Pi): Output pulse prohibition terminal. This terminal is used to block the output of TC787/TC788 under fault conditions. High level is valid. In the application, it is connected to the output of the protection circuit. Synchronous voltage input terminal: Pin 1 (Vc), Pin 2 (Vb) and Pin 18 (Va) are three-phase synchronous input voltage connection terminals. In the application, the input filtered synchronous voltage is connected respectively, and the peak value of the synchronous voltage should not exceed the working power supply voltage VDD of TC787/TC788.
The trigger drive circuit is mainly composed of the grid voltage synchronization circuit, the TC787 integrated trigger circuit and the pulse amplification isolation drive circuit. Figure 5 shows the synchronization circuit and the peripheral circuit of TC787. The first half is the voltage synchronization circuit. This design method requires more auxiliary components. By adjusting the three potentiometers RP1 to RP3 differently, a phase shift of 0 to 60° can be achieved to meet the needs of different main transformer connections. In Figure 5, the midpoint of the synchronous transformer is directly connected to the (1/2) power supply voltage, which simplifies the components used. Pin 4 of TC787 outputs the given voltage (0 to +15V) of the microcontroller, and pin 6 is the trigger pulse blocking pin. Pins 10 to 12 are trigger pulse output pins, which are connected to the isolation circuits of phases C, B, and A respectively.
Figure 5 Synchronous circuit and pulse generation circuit structure diagram
Voltage detection circuit design
In order to reduce hardware costs, the voltage divider resistor method is used instead of the voltage sensor when designing the DC bus voltage detection circuit. The voltage divider resistor method is simple in structure and easy to debug. The circuit is shown in Figure 6. The voltage obtained by the voltage divider resistor is 1/31 of the DC bus voltage. The voltage is input to the AD1 input port of the PIC microcontroller through two reverse proportional amplifier circuits, and then processed into a digital quantity through the AD conversion of the PIC microcontroller.
Figure 6 Voltage detection circuit
References:
[1]. TC787 datasheet http://www.dzsc.com/datasheet/TC787_1137127.html.
[2]. PIC16F690 datasheet http://www.dzsc.com/datasheet/PIC16F690_.html.
[3]. 2.0 datasheet http://www.dzsc.com/datasheet/2.0_1758666.html.
Previous article:Design of sine wave inverter power supply based on PICFxx microcontroller control
Next article:Design and application of intelligent instrument monitoring platform based on single chip microcomputer
Recommended ReadingLatest update time:2024-11-16 20:32
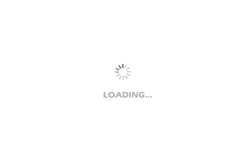
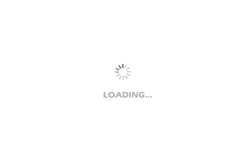
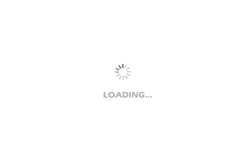
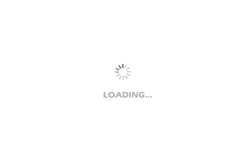
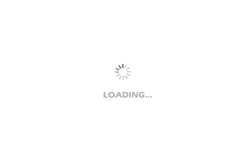
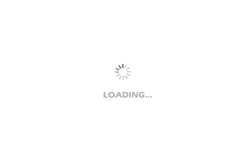
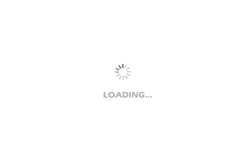
- Popular Resources
- Popular amplifiers
-
Wireless Sensor Network Technology and Applications (Edited by Mou Si, Yin Hong, and Su Xing)
-
Modern Electronic Technology Training Course (Edited by Yao Youfeng)
-
Modern arc welding power supply and its control
-
Small AC Servo Motor Control Circuit Design (by Masaru Ishijima; translated by Xue Liang and Zhu Jianjun, by Masaru Ishijima, Xue Liang, and Zhu Jianjun)
Professor at Beihang University, dedicated to promoting microcontrollers and embedded systems for over 20 years.
- Innolux's intelligent steer-by-wire solution makes cars smarter and safer
- 8051 MCU - Parity Check
- How to efficiently balance the sensitivity of tactile sensing interfaces
- What should I do if the servo motor shakes? What causes the servo motor to shake quickly?
- 【Brushless Motor】Analysis of three-phase BLDC motor and sharing of two popular development boards
- Midea Industrial Technology's subsidiaries Clou Electronics and Hekang New Energy jointly appeared at the Munich Battery Energy Storage Exhibition and Solar Energy Exhibition
- Guoxin Sichen | Application of ferroelectric memory PB85RS2MC in power battery management, with a capacity of 2M
- Analysis of common faults of frequency converter
- In a head-on competition with Qualcomm, what kind of cockpit products has Intel come up with?
- Dalian Rongke's all-vanadium liquid flow battery energy storage equipment industrialization project has entered the sprint stage before production
- Allegro MicroSystems Introduces Advanced Magnetic and Inductive Position Sensing Solutions at Electronica 2024
- Car key in the left hand, liveness detection radar in the right hand, UWB is imperative for cars!
- After a decade of rapid development, domestic CIS has entered the market
- Aegis Dagger Battery + Thor EM-i Super Hybrid, Geely New Energy has thrown out two "king bombs"
- A brief discussion on functional safety - fault, error, and failure
- In the smart car 2.0 cycle, these core industry chains are facing major opportunities!
- The United States and Japan are developing new batteries. CATL faces challenges? How should China's new energy battery industry respond?
- Murata launches high-precision 6-axis inertial sensor for automobiles
- Ford patents pre-charge alarm to help save costs and respond to emergencies
- New real-time microcontroller system from Texas Instruments enables smarter processing in automotive and industrial applications
- [Experience sharing] [Scene reproduction project based on AI camera] AI recognition solution based on Allwinner v831
- How to isolate power modules and non-isolated power supplies respectively
- High Voltage Impedance Tuning Quick Guide
- Will 5G really bring about big changes?
- Today I suddenly thought of this: If resistors of the same resistance are first connected in series and then in parallel, what is the resistance after N?
- Let’s talk about high technology today… Why is a chip so difficult to make?
- I thought foreign manufacturers were indifferent to the RISC-V core...
- 【Zero Knowledge ESP8266 Project】1 OLED Weather Clock
- Is it necessary to enroll in a training course to learn embedded software programming?
- Mobile 5G device antenna tuning revealed