Wireless sensor networks are an emerging research field with great potential application prospects in many fields such as military, environment, health, family, and business. Wireless sensor network nodes are the basic units of the network. The rapid development of wireless sensor networks has brought many challenges to the design and management of wireless sensor network nodes.
Wireless sensor network nodes
Wireless sensor network is a distributed self-organizing network that integrates data acquisition, processing and communication functions. A wireless sensor network consists of multiple network nodes with wireless communication, sensing and data processing functions within a certain area. Sensor nodes are responsible for collecting, processing, compressing data, transferring data packets from other nodes and sending data packets. In different applications, the structure of sensor network nodes is different. Generally, it consists of a data acquisition unit (sensor, A/D converter), a data processing and control unit (microprocessor, memory), a wireless communication unit (wireless transceiver) and a power supply unit (battery).
Compared with traditional wireless network nodes, wireless sensor network nodes have obvious technical characteristics: (1) The network node density is high and the number is large; (2) The computing and storage capabilities of the nodes are limited; (3) The nodes are small in size and usually carry batteries with very limited energy, so the node energy is limited; (4) The communication capability is limited. The communication bandwidth of the sensor network is narrow, and the single-hop distance between nodes is usually only tens to hundreds of meters. Therefore, how to design the network communication mechanism to meet the communication needs of the sensor network under limited communication capability is an issue that must be considered; (5) The locations of each sensor node are randomly distributed and have self-organizing characteristics.
Due to the above characteristics of wireless sensor network nodes, the design of nodes requires low hardware cost, low energy consumption, and support for multi-hop routing protocols. The IEEE802.15.4/ZigBee protocol fully considers the needs of wireless sensor network applications and has the characteristics of power saving, reliable communication, network self-organization, strong self-healing ability, low cost, large network capacity, and network security. Based on these basic requirements, the hardware design of wireless sensor network nodes supporting the 802.15.4/ZigBee protocol was carried out.
Network structure
Nodes can form three topological structures: star structure, mesh structure and cluster structure. Nodes form a network in a self-organizing form. Each node can collect data autonomously. The data is sent to the sink node through a single hop or multi-hop relay. The sink node sends the collected data to a remote control center, or sends the data to a PC through an RS232 interface for data processing and storage.
Node design
The node hardware adopts a modular structure design as shown in Figure 1, which consists of a computing and communication sub-board, a sensor sub-board, and a charging and status display sub-board. The computing and communication sub-board consists of a microprocessor, a data storage circuit, a wireless communication module, a power management module, etc. Its main function is to store and process data, complete wireless communication between nodes, and provide energy for the system. The sensor sub-board consists of several sensors and is responsible for collecting information in the monitoring area. The charging and status display sub-board consists of a charging module and an LCD liquid crystal display module, which is used to display the node battery charging status, the node's working status, and the battery power.
Microprocessor circuit
The microprocessor circuit uses Atmel's ATmega128L microcontroller, which is produced using low-power CMOS technology and based on RISC structure. It has 128KB of on-chip program memory (Flash), 4KB of data memory (SRAM) and 4KB of EEPROM. It has 8 10-bit ADC channels, 2 8-bit and 2 16-bit hardware timers/counters, 8 PWM channels, programmable watchdog timer and on-chip oscillator, on-chip analog comparator, JTAG, UART, SPI, I2C bus and other interfaces. ATmega128L can work in a variety of different modes. In addition to the normal operating mode, it also has six different levels of low-energy operating modes. Therefore, this microcontroller is suitable for low-energy applications. Its interface diagram is shown in Figure 2. [page]
The working clock source of ATmega128L can be selected from external crystal oscillator, external RC oscillator, internal RC oscillator, external clock source, etc. The selection of working clock source is designed through the internal fuse bit of ATmega128L, and the fuse bit can be set through JTAG programming, ISP programming, etc. In this design, ATmega128L uses two external crystal oscillators: 7.3728MHz crystal oscillator as the working clock of ATmega128L; 32.768kHz crystal oscillator as the real-time clock source.
Data storage circuit
Due to the limited transmission capacity of the communication module of the wireless sensor node and the very small duty cycle of the node, a lot of data cannot be forwarded in real time, so a manageable memory is needed to store this data and temporarily store the data collected by itself or collected by other nodes that need to be forwarded. This design uses 512KB serial FLASHAT45DB041 to store data. Compared with ordinary data storage, this chip has the characteristics of low power consumption, small size, serial interface, simple external circuit, etc., which is suitable for sensor nodes. The schematic diagram of the data storage circuit is shown in Figure 3.
Wireless communication module
The wireless communication module uses the wireless radio frequency CC2420 module. It is a wireless transceiver module compatible with the 2.4GHz IEEE802.15.4 standard launched by Chipcon at the end of 2003. It is based on Chipcon's SmartRF03 technology and is produced using CMOS technology. It has the characteristics of low operating voltage, low energy consumption, small size, and programmable output intensity and transceiver frequency. The chip only needs a few external components such as a crystal oscillator and load capacitors, input/output matching components, and power supply decoupling capacitors to work properly, ensuring the effectiveness and reliability of short-distance communication. Its maximum transceiver rate is 250kbps.
CC2420 has 33 16-bit configuration registers, 15 command strobe registers, 1 128-byte transmit FIFO buffer, 1 128-byte receive FIFO buffer, and 1 112-byte security information memory. The connection between CC2420 and the processor is relatively simple. It uses four pins, SFD, FIFO, FIFOP, and CCA, to indicate the state of data transmission and reception. The processor exchanges data and sends commands with CC2420 through the SPI interface (CSn, SO, SI, SCLK), resets the chip using the RESETn pin, and enables the voltage regulator of CC2420 using the VREG_EN pin to generate the 1.8V voltage required by CC2420, thereby enabling CC2420 to enter a normal working state. CC2420 communicates through a monopole antenna or a PCB antenna. Its module schematic is shown in Figure 4.
CC2420 requires a 16MHz reference clock for data transmission and reception. The reference clock can come from an external clock source or be generated by an internal crystal oscillator. If an external clock is used, it is directly input from the XOSC16_Q1 pin, and the XOSC16_Q2 pin is left floating; if an internal crystal oscillator is used, the crystal oscillator is connected between the XOSC16_Q1 and XOSC16_Q2 pins. To start the crystal oscillator, the CC2420 strobe command register SXOSCON must be enabled. [page]
Power Management Module
Electric energy is a very valuable resource in sensor networks. In order to ensure the low power consumption design of hardware circuits, the node chips are all low power and low voltage chips. The system uses ordinary batteries or rechargeable lithium-ion batteries, and the power management chip uses AD's ADP3338-3.3, SOT-223 package.
Charging and status display module
When the node can be charged, it uses lithium-ion batteries to work. The charging module can be used to supplement the node with electricity, thereby ensuring the continuity of the node's work and avoiding the interruption of the node's work due to battery replacement. The charging module is designed using Dallas' DS2770 and battery protection chip DS2720, and has functions such as charging control, power control, power counting, and battery protection. The processor and DS2770 use a one-line interface to transmit information, and an external pull-up resistor of about 4.7k! is required. The schematic diagram of the charging module is shown in Figure 5. The LCD display module uses an LCM6432ZK liquid crystal display, which is connected to the main MCU through a serial interface and is used to display system working status information, charging process, battery power, and other status. The node hardware has an LCD interface, which can be easily connected to the LCD display module when display is required.
Sensor Module
The node sensor module is separated from the computing and communication sub-boards, and the modular design improves the flexibility of the node in different applications. The sensor module can determine the appropriate sensor according to actual needs, such as temperature, humidity, vibration, light intensity, gas alarm, magnetic resistance, infrared, etc., to meet different needs. Since most nodes are battery-powered, the sensor is required to be small in size, low in power consumption, and simple in peripheral circuits. It is best to use a digital sensor that does not require complex signal conditioning circuits.
Some of the sensors used in this design are:
The temperature sensor DS18B20 is a new type of digital temperature sensor with a very simple external circuit and a one-wire bus interface. Its measurement range is -55℃~125℃, and the measurement accuracy is ±0.5℃ between -10℃~85℃. The maximum resolution can be designed to be 12 bits, and the measurement data is accurate and reliable.
The infrared sensor PD632 is a digital pyroelectric sensor with an operating wavelength of 7.5ηm to 14ηm. The detection distance can reach 6m to 15m under a working environment of -20℃ to 60℃.
The ADXL202 acceleration sensor is a two-dimensional digital acceleration sensor from AD. It has an operating temperature of -40℃~85℃ and uses advanced MEMS technology to measure vibration acceleration and static acceleration.
External Interface
The external interfaces of the node include JTAGE interface, ISP programming interface, RS232 interface, charging interface, sensor interface, SMA antenna seat interface, etc. The node uses JTAGE and ISP to download programs; uses RS232 interface to directly connect to the PC serial port; can be connected to different sensor modules through the sensor interface according to different needs; in the case of charging conditions, the node can be quickly replenished with energy through the charging interface. Figure 6 is a schematic diagram of the RS232 interface, and Figure 7 is a schematic diagram of the JTAG/ISP interface.
Key points and matters needing attention in node design
The RF part is the focus and difficulty of this design, and is also the key to the success of the system design. The main problems encountered in the module design process and their solutions are:
The carrier frequency of CC2420 is 2.4GHz, and one channel is added every 5MHz. The accuracy of the crystal oscillator will affect the frequency of the carrier, thereby affecting the establishment and stability of communication. CC2420 requires the accuracy of the clock source to be within ±40ppm. If an external crystal oscillator is used, a four-pin SMD crystal oscillator with high accuracy and stable performance should be used as much as possible.
The CC2420 RF circuit operates in the high-frequency operating frequency band of 2.400GHz to 2.4835GHz. The anti-interference design is directly related to the RF performance and the operation of the entire sensor node. When wiring the RF part, reasonable layout and wiring and the use of multi-layer boards are both necessary for wiring and effective means to reduce electromagnetic interference and improve anti-interference capabilities. Pay special attention to the following points when wiring: First, the area of the RF circuit that is not used for wiring must be filled with copper and connected to the ground to provide RF shielding to achieve effective anti-interference purposes; second, the bottom of the CC2420 chip should be grounded; in order to reduce delays, reduce crosstalk, and ensure the transmission of high-frequency signals, use multiple ground vias to connect the bottom of the CC2420 chip to the ground layer; third, to reduce crosstalk as much as possible and reduce the impact of distributed parameters, the devices should be closely distributed around the CC2420 and use smaller packages.
For wireless communication networks, antennas play a pivotal role. The selection and setting of antennas will directly affect the operation quality of the entire wireless communication network. The RF chip CC2420 of this node can use two design schemes: metal inverted F-type PCB lead antenna and monopole antenna. PCB lead antenna is a wire printed on a circuit board, which is used to sense air waves and receive information. The shape and size of the PCB antenna should be designed strictly according to the data sheet. In recent years, with the decline in computer costs and the reduction in the size of microprocessors, wireless sensor networks have received more and more attention. This design is a low-power, low-cost, and practical wireless sensor network node designed by the author based on the summary of domestic and foreign wireless sensor network research results. The node uses an independent optional charging module, LCD status display module and rich external interfaces. It has strong practicality, can work in a variety of environments, and can be configured according to a variety of needs to complete system functions. It has obvious advantages in cost, power consumption, flexibility, etc.
Previous article:Railway Crossing Monitoring System in Mining Areas Based on Single Chip Microcomputer and GPRS
Next article:Design of Communication between PC104 Bus and CAN Bus Based on Linux
Recommended ReadingLatest update time:2024-11-16 16:56
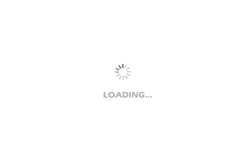
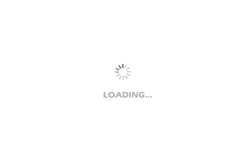
- Popular Resources
- Popular amplifiers
Professor at Beihang University, dedicated to promoting microcontrollers and embedded systems for over 20 years.
- Innolux's intelligent steer-by-wire solution makes cars smarter and safer
- 8051 MCU - Parity Check
- How to efficiently balance the sensitivity of tactile sensing interfaces
- What should I do if the servo motor shakes? What causes the servo motor to shake quickly?
- 【Brushless Motor】Analysis of three-phase BLDC motor and sharing of two popular development boards
- Midea Industrial Technology's subsidiaries Clou Electronics and Hekang New Energy jointly appeared at the Munich Battery Energy Storage Exhibition and Solar Energy Exhibition
- Guoxin Sichen | Application of ferroelectric memory PB85RS2MC in power battery management, with a capacity of 2M
- Analysis of common faults of frequency converter
- In a head-on competition with Qualcomm, what kind of cockpit products has Intel come up with?
- Dalian Rongke's all-vanadium liquid flow battery energy storage equipment industrialization project has entered the sprint stage before production
- Allegro MicroSystems Introduces Advanced Magnetic and Inductive Position Sensing Solutions at Electronica 2024
- Car key in the left hand, liveness detection radar in the right hand, UWB is imperative for cars!
- After a decade of rapid development, domestic CIS has entered the market
- Aegis Dagger Battery + Thor EM-i Super Hybrid, Geely New Energy has thrown out two "king bombs"
- A brief discussion on functional safety - fault, error, and failure
- In the smart car 2.0 cycle, these core industry chains are facing major opportunities!
- The United States and Japan are developing new batteries. CATL faces challenges? How should China's new energy battery industry respond?
- Murata launches high-precision 6-axis inertial sensor for automobiles
- Ford patents pre-charge alarm to help save costs and respond to emergencies
- New real-time microcontroller system from Texas Instruments enables smarter processing in automotive and industrial applications
- Understanding C language pointers
- Intelligent POS system block diagram analysis and its seven key functional module solutions
- Animation demonstrates the working principle of capacitors and the principle of capacitive sensors
- AT commands in C language
- Circuit Playground Bluefruit NeoPixel Animated Remote Control
- 5224. FAQs on debugging C2000 CLA on CCS V1.0
- GD32F105RBT6 About FMC internal flash operation issues
- This week's review information is here~
- A pitfall of threadx queue, and also pay attention to a mistake in the tough guy tutorial
- About 48V input buck type DCDC chip