Airborne radio stations are responsible for air-to-air and ground-to-air communications. To ensure the performance of the radio stations, they need to be regularly inspected. The detectors based on single-chip microcomputers have the problems of slow measurement speed and poor scalability; while the detectors based on PXI instruments or VXI instruments have the disadvantages of high power consumption, large size, and high price. In order to solve the above problems, the use of ARM processors to implement radio detection controllers has become an important development direction. ARM is a high-performance, low-power RISC structure processor. Due to its excellent performance, it is widely used in industrial control, wireless communications, imaging and security, network applications, etc. The use of ARM-based radio detection controllers has the advantages of strong portability, good scalability, and strong anti-interference ability.
1 Hardware Design
Good hardware design is the key to solving the problems of radio detectors based on single-chip microcomputers, PXI, VXI and other systems. In order to realize the modular design of the hardware structure, the hardware is mainly divided into two parts: the main controller circuit and the conditioning circuit. In order to design a detector with high performance, low power consumption, good scalability and low cost, the selection of the main controller is crucial. In order to meet the scalability design of the detector, the main controller must have network functions, USB storage, serial communication, SPI communication, I2C communication, analog-to-digital conversion and other functional modules. In order to meet the requirements of human-computer interaction design, it must also have necessary frequency preset circuits, display circuits, etc. Only ARM processors can complete controllers with so many functions and controllers that meet the performance of high performance and low power consumption. According to the electrical characteristics of a radio station, the communication between the main controller and the radio station must also perform necessary level conversion. In addition, the response signal output by the radio station cannot be directly sent to the main controller. It is also necessary to design necessary circuits such as voltage divider networks and impedance matching, which requires conditioning circuits. The main controller circuit and the conditioning circuit cooperate to complete the detection of the radio station. The overall structure of the hardware designed according to the radio test requirements is shown in Figure 1.
1.1 Main Controller
The main control is the core of the radio detection controller, responsible for important tasks such as information collection, storage, network functions and communication with the radio. The quality of the main control directly determines the system performance. After comparison, Philips' LPC2388 was selected as the main controller of the radio. This device is a processor based on the ARM7TDMI-S core and has rich peripherals such as Ethernet controller, USB controller, I2C, serial interface, etc., which can meet the needs of the detector.
1.2 Storage Circuit
In order to meet the requirements of scalability and storability of test results, the detection controller must save the results of each measurement of a certain type of radio. This requires communication between the main controller and the radio integrated tester. A certain radio integrated tester has a serial communication method for external communication. During measurement, the communication control interface can be connected to the serial port line of the radio integration, so that the test results can be read into the control system. If you want to store this information, the memory must be erasable. In order to save the valuable general I/O port of the controller, a 12C communication port is selected.
Information storage function CAT24WC64 is used as E2PROM. This device is responsible for saving the radio performance test results. It can save up to 50 radio test results. If it exceeds 50 times, the system will automatically erase the original stored test results and then store them again. When you need to view the system radio test results, there are three ways to do it: 1) Insert the USB storage device into the USB storage interface circuit, the system will automatically identify the device, and then select the store test result button to save the test results to the USB storage device: 2) Connect to the computer through the network interface, and then read the test results by remote control: 3) Use serial communication to read the information to the computer.
1.3 USB storage interface circuit
The USB interface circuit is the window for completing the communication with the USB storage device. The LPC2388 has a controller compatible with the USB2.0 protocol, which provides convenience for the USB interface design. To meet the system reliability, a 33 Ω resistor is connected in series on the D+ and D- lines respectively, and a 1.5 kΩ pull-up resistor is added to the D+. To indicate that the USB storage device is connected, an indicator light is added to the Ul_UPLED pin. When the USB storage device is connected, the indicator light is on.
1.4 Network interface circuit
To meet the needs of remote control, the detection controller should have a network control interface. LPC2388 has a 10/100 Mb/s Ethernet communication rate. To ensure reliable transmission, it is implemented by integrating a 16 KB-byte Ethernet controller dedicated SDRAM, using a high-speed AHB bus to communicate between the Ethernet controller and the ARM7 core, and using a dedicated DMA for data transmission. The Ethernet controller used inside the processor uses the RMII interface, and the Ethernet communication function can be realized by communicating with the peripheral circuit PHY chip DM9161A.
1.5 Frequency forming circuit
If the radio detector wants to fully detect the radio performance, it should detect the radio performance at multiple frequency points. This requires the detector to be able to output a variable frequency control code. The formation of the frequency control code requires a frequency forming circuit. The frequency forming circuit is to send the pulse to the main controller through pulse shaping and counting, and finally buffering. The pulse forming circuit is realized by a self-reset switch, the shaping circuit uses MAX708 counting and the buffer circuit uses 54HCl90 and 54LVC245 respectively. In order to save the precious I/O port resources of the processor, the analog bus is used to realize it, and the formation of the frequency code is controlled by latching and decoding circuits.
1.6 Display and keyboard circuit
The display circuit is a window for human-computer interaction, which directly displays the current status of the detector and the radio station detection results. When the detected radio station cannot meet the performance requirements, the error result is directly displayed; the keyboard circuit completes the input of some functions of the detector. In order to ensure the reliability of the display results of the detector, the display circuit of the detector uses a LED digital tube display with strong anti-interference performance. The driver of the LED digital tube is ZLG7290. ZLG7290 uses three-line serial code to interact with the ARM processor for information. Its dynamic display function reduces system power consumption. In addition to driving the display digital tube, ZLG7290 also realizes some inputs of radio station detection through its keyboard interface. Its circuit diagram is shown in Figure 2. [page]
1.7 Other circuits
For a system to work reliably, it must have a series of circuits such as crystal oscillators, watchdogs, and power supplies to provide the clock and monitoring circuits necessary for the system to work. The crystal oscillator circuit provides the necessary clock signal. When an abnormality occurs during program operation, the watchdog circuit provides a reset signal to the microcontroller, increasing the robustness of the system: the power supply circuit is the power supply for the entire system, and a DC/DC switching power supply with high conversion efficiency is used to power the system design according to function, that is, the control circuit power supply and the conditioning circuit are independently powered: increasing the system's anti-interference ability.
1.8 Conditioning Circuit
The working status and working sequence of the detection controller are completed by the main controller. However, this is only one aspect of the normal operation of the detection controller. Another important aspect is the conditioning circuit, which is mainly composed of relay array, voltage divider network, analog switch, level conversion, etc. The signal output by the controller cannot be directly added to the radio. There are two main reasons for this: 1) The serial port data output by the detection controller is a single-ended output, while the signal required by the radio is a differential signal; 2) The signal level and format of the controller output are completely correct. To ensure the system
In order to improve the anti-interference performance, a buffer is usually added at the output of the controller and the input of the radio to increase the isolation between the system modules. All control information of the detection controller panel is processed by the processor and sent to the radio through the serial port. The radio needs a differential signal, and the DSl6F95 is used to realize the conversion of the signal level mode. In addition to testing the performance of the transceiver, the detection controller can also test the performance of the control box. In addition, the control can also be used to control the transceiver, thereby simulating the control box on the machine to control the transceiver. The control box control and the detection controller itself cannot be sent to the radio at the same time, which requires a relay array to complete the conversion between the detector and the control box. In addition, in order to monitor the working voltage of the radio, the detector must display the working voltage in time, and the working radio 27V and the internal transceiver control voltage must also be displayed. These voltages need to be sent to the CNC analog switch after voltage division by the voltage divider network, and the controller monitors each voltage in turn.
2 Software Architecture Design
The radio detection controller is a typical embedded control system, and the quality of its performance design is directly related to whether the system can work reliably. Embedded software design is quite different from ordinary PC software. Due to the complex control relationship of the detector, coupled with factors such as network interface, USB storage driver, interrupt time control, timer design, serial communication, etc., the requirements for software architecture are high, and the coordination of software and hardware detection must be considered. In addition, the software must also meet the design of testability, portability, robustness, etc., and multiple factors must be considered comprehensively. The software flow of the radio detection controller is shown in Figure 3. After the system is powered on, it is initialized and configured, and then the measurement control mode is selected. If it is remote control, the network connection is started, and the computer is used to control the detection controller to work, and the transceiver performance test is entered. The test results are stored in the remote computer through the network; if it is a manual test, it is determined whether the measurement mode is measurement and control, external control or measurement and control. If it is internal control, the transceiver is controlled by the detection controller, and the main performance of the transceiver is measured with the cooperation of the radio comprehensive tester. The results can be saved by reading the test results of the radio comprehensive tester. When saving the results, if the USB storage device exists, the results are stored in it, otherwise, they are stored in the internal erasable E2PROM; if it is measurement and control, the detection controller measures the control box status and saves the results; if it is external control, the transceiver performance is measured under the control of the control box, and the detection controller also saves the test results by reading the radio comprehensive tester results.
3 Conclusion
The radio station detection controller based on ARM has flexible hardware design and good software architecture design, which realizes the seamless combination of software and hardware platform, has high performance, low power consumption, good portability and scalability, and realizes the detection and control of radio stations. Through the network interface, remote control can be realized, and the measurement results can be read in real time: by adding a USB storage interface, the measurement data can be directly saved in the case of manual testing, which greatly improves the processing speed of test results and has broad economic and military benefits.
Previous article:Design of 3G wireless networking solution based on Linux-ARM platform
Next article:System architecture of wireless LAN MAC layer based on ARM7
Recommended ReadingLatest update time:2024-11-16 22:54
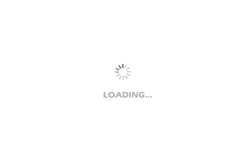
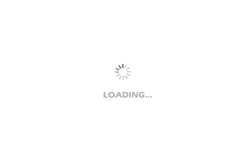
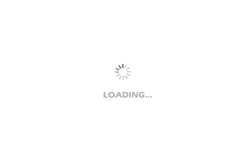
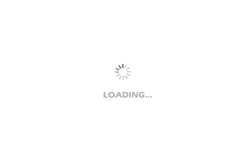
Professor at Beihang University, dedicated to promoting microcontrollers and embedded systems for over 20 years.
- Innolux's intelligent steer-by-wire solution makes cars smarter and safer
- 8051 MCU - Parity Check
- How to efficiently balance the sensitivity of tactile sensing interfaces
- What should I do if the servo motor shakes? What causes the servo motor to shake quickly?
- 【Brushless Motor】Analysis of three-phase BLDC motor and sharing of two popular development boards
- Midea Industrial Technology's subsidiaries Clou Electronics and Hekang New Energy jointly appeared at the Munich Battery Energy Storage Exhibition and Solar Energy Exhibition
- Guoxin Sichen | Application of ferroelectric memory PB85RS2MC in power battery management, with a capacity of 2M
- Analysis of common faults of frequency converter
- In a head-on competition with Qualcomm, what kind of cockpit products has Intel come up with?
- Dalian Rongke's all-vanadium liquid flow battery energy storage equipment industrialization project has entered the sprint stage before production
- Allegro MicroSystems Introduces Advanced Magnetic and Inductive Position Sensing Solutions at Electronica 2024
- Car key in the left hand, liveness detection radar in the right hand, UWB is imperative for cars!
- After a decade of rapid development, domestic CIS has entered the market
- Aegis Dagger Battery + Thor EM-i Super Hybrid, Geely New Energy has thrown out two "king bombs"
- A brief discussion on functional safety - fault, error, and failure
- In the smart car 2.0 cycle, these core industry chains are facing major opportunities!
- The United States and Japan are developing new batteries. CATL faces challenges? How should China's new energy battery industry respond?
- Murata launches high-precision 6-axis inertial sensor for automobiles
- Ford patents pre-charge alarm to help save costs and respond to emergencies
- New real-time microcontroller system from Texas Instruments enables smarter processing in automotive and industrial applications
- TI Embedded Live Month: In-depth exploration of new applications of embedded products in industry and automobiles. The fourth session will be live at 10:00 today.
- The price of chips has increased 20 times? Reportedly, there is panic stockpiling in China
- 【GD32L233C-START Review】2. Timer interrupt
- [Shanghai Hangxin ACM32F070 development board evaluation] 4. LCD_TK program analysis
- These pictures can explain the problems in the previous class. Popular science and practical application
- Automatic watering system based on esp32s2-work submission
- Principles and Design of Automatic Control (5th Edition)
- C2000Ware for C2000 MCUs
- MSP430F5529 ADC Reference
- EEWORLD University ---- Linux driver development: character device driver