The five major problems on Earth at present, including energy imbalance, dictatorship of oil-producing countries, uncontrolled climate change, energy shortage, and disappearance of biodiversity, are all caused by the extensive use and reliance on traditional energy by humans. Moreover, the five major problems are closely linked and imminent. If no active action is taken, all mankind will fall into an unimaginable catastrophe. Therefore, the development of alternative energy is not only a solution to high oil prices, but also the most critical factor for human beings to survive sustainably on Earth. Coal and oil are the main energy sources used in China. Their huge consumption is not only the main source of air pollution, but also their non-renewable nature makes them gradually replaced by renewable energy. Most parts of China have rich wind and solar energy resources, but they have not been effectively utilized due to the development of science and technology. In recent years, with the continuous progress of electronic technology and silicon material research, the development and utilization of wind and solar energy have been promoted, and the market prospects are quite broad. Under this premise, a new generation of wind and light complementary integrated power supply system with intelligent, modular and integrated features has been developed.
1 Wind-solar complementary power generation system
The wind-solar complementary power system mainly consists of wind turbines, solar panels, battery packs and power integrated control cabinets. Its design concept is to use the solar panels and wind turbine dual power generation system to charge the battery pack (48V), and then invert the DC power into AC 220V/50Hz AC power, which becomes our commonly used AC power supply. The charging method of the battery pack determines the length of its service life, but the suddenness of wind energy and the timeliness of solar energy are destined to prevent the power generation system from outputting reliable and stable DC power. If the battery pack is directly charged without processing, it will not only greatly shorten the life of the battery pack, but also fail to effectively utilize wind energy and solar energy. Therefore, a control system based on ATMEGA8 single-chip microcomputer digital power following technology is introduced during the charging process, which not only greatly improves the stability of the power generation system, but also improves the reliability of the power supply system.
2 Charging system composition
Taking the wind turbine as an example, the main circuit of the charging system adopts the DC conversion module PH600S28048 of a Nissan company, with a DC input voltage of 200-400V and an output voltage of 43-6lV, which can be adjusted by remote control. The fan has a three-phase line voltage of 220V output, and the battery pack has a charging voltage range of 46~57V. The constant current and power following of the charging are completed by ATMEGA8. The system composition schematic diagram is shown in Figure 1.

System schematic diagram 1
3 System Working Principle
ATMEGA8 is an AVR high-end single-chip microcomputer, which integrates an RC oscillator with selectable and calibrated frequency, 8K FIASH program memory, 1K SRAM data memory, and 512 bytes of E2PROM. 8-channel 10-bit A/D conversion, 3 PWM output channels can be used as D/A output, internal programmable watchdog timer, etc. The charging current is converted into a standard signal of 0-5V through the Hall current sensor, converted into a digital signal through A/D and sent to the CPU for processing, and the output voltage of the charger is controlled through the PB1 pin. The PWM output controls the pass of the optocoupler PC817 to control the output voltage of the charger, thereby achieving the purpose of constant current through simple digital PI regulation. However, an important prerequisite for the constant current operation of the charger is that the input energy must have sufficient power. However, the randomness and suddenness of wind energy and solar energy in nature make constant current charging difficult to achieve. Especially for wind energy, if the wind speed is particularly high and the charger still outputs a constant current (the load remains unchanged), it will damage the fan. If the wind speed is low and the power is insufficient, the charger will not work properly, sometimes shutting down and sometimes opening. This phenomenon is caused by the normal working input voltage range of the charging module PH600S is DC 200~400V. In order to overcome this situation, digital power following technology is added, and the load size (output current) is adjusted by digital PI adjustment based on the fan input voltage 300V converted by A/D, so as to achieve normal operation of the charger.
4 Software Design Ideas
The program is written in the assembly language dedicated to the AVR microcontroller and modular design. The program flow diagram of the monitoring program and the input control module is shown in Figure 2.

Figure 1: Flow chart of monitoring main program
The entire program code consists of digital acquisition of analog quantity, median filtering, digital comparison, PWM output, etc. The key is that digital comparison constitutes a simple PI regulation and the current loop is nested in the voltage loop.
The program flow is as follows: Take the current loop as an example for introduction: The output current of the hardware charger composed of PH600S series modules is linearly regulated by a 0-5V signal. The current given signal (0-5V) is output by the ATMEGA8 microcontroller PBl port as a 10-bit PWM pulse width modulation waveform, which is then generated by RC filtering. Set the T/C1 control register TCCR1A of the M8 microcontroller to 83H, and the TCCR1B control register to 05H, which defines the PBl port to output a 10-bit fast PWM waveform. The value of the T/C1 count register TCNTI (TCNT1H: TCNT1H) changes from 0000 to 01FFH. The pulse output duty cycle (output voltage) is generated by comparing the set value of the comparison control register OClA with the count value of the TCNTl register; the content of OClA is variable from 0000 to 0lFFH, which determines that the output voltage is linearly adjustable from 0 to 5V. The OClA value is given by the voltage loop after analog PI adjustment operation, so that the mutual nesting of the voltage loop and the current loop constitutes a constant follow of power, thereby improving the efficiency of wind and light complementary power generation.
5 Conclusion
The power following principle of the solar charging circuit and the wind turbine is the same, except that the input voltage of the solar panel is low and changes slowly. The PH30048-48 module has been used as the main circuit. The wind-solar complementary power generation system made of a Nissan company's DC conversion module as the main circuit using the ATMEGA8 microcontroller as control has been in operation for more than two years in a garrison on Shanghai's Huaniao Island. It is very stable and has been well received by military leaders.
Previous article:Implementation of Coding and Decoding of Load Cylinder Multi-channel Remote Control Switch Based on AVR Single Chip Microcomputer
Next article:Single-chip Microcomputer Pulse Generator Based on LabVIEW
Recommended ReadingLatest update time:2024-11-17 03:05
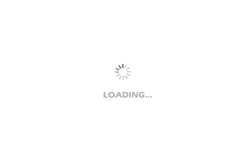
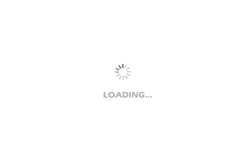
- Popular Resources
- Popular amplifiers
Professor at Beihang University, dedicated to promoting microcontrollers and embedded systems for over 20 years.
- Innolux's intelligent steer-by-wire solution makes cars smarter and safer
- 8051 MCU - Parity Check
- How to efficiently balance the sensitivity of tactile sensing interfaces
- What should I do if the servo motor shakes? What causes the servo motor to shake quickly?
- 【Brushless Motor】Analysis of three-phase BLDC motor and sharing of two popular development boards
- Midea Industrial Technology's subsidiaries Clou Electronics and Hekang New Energy jointly appeared at the Munich Battery Energy Storage Exhibition and Solar Energy Exhibition
- Guoxin Sichen | Application of ferroelectric memory PB85RS2MC in power battery management, with a capacity of 2M
- Analysis of common faults of frequency converter
- In a head-on competition with Qualcomm, what kind of cockpit products has Intel come up with?
- Dalian Rongke's all-vanadium liquid flow battery energy storage equipment industrialization project has entered the sprint stage before production
- Allegro MicroSystems Introduces Advanced Magnetic and Inductive Position Sensing Solutions at Electronica 2024
- Car key in the left hand, liveness detection radar in the right hand, UWB is imperative for cars!
- After a decade of rapid development, domestic CIS has entered the market
- Aegis Dagger Battery + Thor EM-i Super Hybrid, Geely New Energy has thrown out two "king bombs"
- A brief discussion on functional safety - fault, error, and failure
- In the smart car 2.0 cycle, these core industry chains are facing major opportunities!
- Rambus Launches Industry's First HBM 4 Controller IP: What Are the Technical Details Behind It?
- The United States and Japan are developing new batteries. CATL faces challenges? How should China's new energy battery industry respond?
- Murata launches high-precision 6-axis inertial sensor for automobiles
- Ford patents pre-charge alarm to help save costs and respond to emergencies
- Inductor selection and layout of switching power supplies
- Interaction between data collection and MATLAB
- Tips for taming ADC
- MSP430 MCU Timer A Structure and Application Examples
- How should the chassis ground of a high-speed interface connector be designed?
- SX1278LORA Module FAQ
- What effect does it have if a transistor is connected in parallel behind the differential line and a 10 ohm resistor is connected in series?
- Analysis of the characteristics of nrf24l01 wireless module
- A classic analog circuit worth collecting
- LM3644 Application Guide for Industrial Scanning