Central air conditioning energy efficiency management system based on P87LPC764 single chip microcomputer
The central air conditioning system is mainly composed of a refrigerator, a cooling water circulation system, a chilled water circulation system, a fan coil system and a cooling water tower. The refrigerator compresses the refrigerant into liquid through the compressor and sends it to the evaporator for heat exchange with the chilled water to cool the chilled water. The chilled water pump sends the chilled water to the cooling coils of each fan outlet, and the fan blows cold air to achieve the purpose of cooling. In the system, the cooling pump, cooling pump, and water tower fan inverter adopt open-loop control, which is adjusted by maintenance personnel according to different seasons and load changes. Heat exchangers and circulating fans are installed in each room. The heat exchange amount is changed by controlling the speed of the fan to achieve the purpose of adjusting the room temperature.
The common control method is to control the room temperature in "high, medium, low, off" mode. The disadvantage is that the room temperature needs to be adjusted manually, and changes in various environmental factors often make people feel uncomfortable. The fan speed control solution uses inverter speed control to effectively solve the above problems, achieve the purpose of automatic indoor temperature adjustment, and greatly save energy.
2. Principle of overall control parameters of central air conditioning energy efficiency management system
The indoor temperature required to be controlled is set to Tsv, the wind box outlet temperature is Tw, the current indoor ambient temperature is measured to be Tpv, the outdoor temperature is T0, the indoor heat dissipation (absorption) coefficient is Kv, the specific heat capacity is C, the air flow rate generated by the fan rotation is q, its specific heat capacity is Cp, the flow rate q is proportional to the fan speed n, and its proportional coefficient is Kc. According to the principle of dynamic energy balance, it can be obtained:
From formula (1), we can see that the main factors affecting the indoor temperature are the wind box outlet temperature Tw, the indoor ambient temperature Tpv, the indoor heat dissipation (absorption) coefficient Kv, and the speed of the circulating fan n. Kv is determined by the indoor ambient temperature, the outdoor temperature and the sealing and insulation conditions of the room. Therefore, choosing the speed of the circulating fan as the control parameter is the best parameter to adjust the room temperature and achieve energy saving.
3 Performance characteristics of central air conditioning energy efficiency management system
The central air conditioning energy efficiency management system has the following main features:
(1) The power supply is 220 VAC and the power consumption is less than 5 W;
(2) Indoor temperature LCD display, temperature measurement range -5 ~ 30 ℃; accuracy ± 1 ℃, LCD 8-10 digits display real-time temperature value;
(3) Control voltage output function, voltage output resolution is 10 bits, output voltage range is 0~5 V, PID control cycle is 5 min;
(4) Running time accumulation function, LCD 1-4 digits display hours, 5,6 digits display minutes, automatically store once every hour, each time the running time is automatically stored in E2PROM, each time the running time is automatically read from E2PROM, and sent to LCD display;
(5) On-site programming function, which can randomly set the indoor target temperature, control cycle and adjustment range on-site;
(6) Human-machine interface function, 10-digit LCD digital display, 5 operation keys are MOD, UP, DOWN, ENTER, SLT/END. Sound prompt function, the buzzer sounds once when the key is valid, the buzzer sounds twice when the input setting data is valid, the buzzer sounds three times when the input setting data is wrong, and the equipment failure alarm buzzer sounds five times.
4 System Hardware Principle and Design
The hardware structure of the central air conditioning energy efficiency management system is shown in Figure 1. The temperature sensor with linear voltage output of TCl047A is selected, and its output signal (temperature measurement signal) is sent to the analog/digital converter TLC0834 for A/D sampling through the integrated operational amplifier LM358. The digital signal after the analog signal is changed by A/D is sent to the single-chip microcomputer through the bus for processing. After processing, the output control signal is sent to the digital/analog converter TLC5615 to realize the control of the inverter power, which greatly saves energy. The display data is sent to LCD621 through the bus, the keyboard uses the keyboard interrupt method for interrupt processing, the relay controls the start and stop of the fan by closing and disconnecting, and the E2PROM 24C02 is used to store the temperature setting value and PID parameters. It can be seen that compared with similar products, the hardware of this product is simple, realizes human-machine exchange, requires fewer devices, and can be realized at a very low cost.
4.1 Temperature detection link
4.1.1 Overview of TCl047A
TCl047A is a temperature sensor with linear voltage output, and its output voltage is proportional to the measured temperature. It can accurately measure the temperature in the range of -40 to +125°C. At the same time, the operating voltage range of TCl047A is 2.5 to 5.5 V. The typical output voltage values of this type of temperature sensor are: 100 mV at -40°C, 500 mV at 0°C, 750 mV at +25°C and 1.75 V at +125°C. The output voltage slope of 10 mV/°C can accurately measure the temperature in a wide temperature range. TCl047A is available in a 3-pin SOT-23B package, suitable for temperature measurement applications with strict space requirements.
4.1.2 TLC0834 Overview
TLC0834 is an 8-bit successive approximation analog/digital converter produced by TI. It has a multi-channel multiplexer with configurable input and a serial input/output mode. Its multiplexer can be configured by software as a single-ended or differential input, or as a pseudo-differential input. In addition, its input reference voltage can be adjusted. At full 8-bit resolution, it allows arbitrarily small analog voltage encoding intervals. Since TLC0834 uses a serial input structure, the package size is small, which can save 51 series microcontroller I/O resources and the price is also moderate. Its main features are as follows: 8-bit resolution; easy to interface with a microprocessor or use independently; can operate at full scale; 4 input channels can be selected using an address logic multiplexer; single 5 V power supply, input range is 0~5 V; when the input and output are compatible with TTL, CMOS levels and the clock frequency is 250 kHz, its conversion time is 32μs; can be replaced with National Semiconductor's ADC0834 and ADC0838, but it does not have an internal Zener regulator network; the total adjustment error is ±1 LSB.
4.2 Signal Processing Unit P87LPC764 8-bit 0TP MCU
The P87LPC764 series of microcontrollers are chips developed by Philips to meet low-cost, high-integration applications. The chip uses an accelerated 51 core. At the same clock frequency, its speed is twice that of the standard 51. It contains A/D, UART serial port, built-in oscillator, I2C bus interface, etc., which can meet many performance requirements.
P87LPC764 includes a central processing unit, 128 B internal data memory RAM, 4 kB OTP program memory, 15 I/O ports and 1 input port, 2 16-bit independent timer/counters with overflow trigger function, 8 keyboard interrupt inputs and two external interrupt inputs. In addition, P87LPC764 also has power-on reset, idle power-down mode, and low-level interrupt wake-up functions. In power-down mode, the current is only 1μA. If the on-chip oscillator is selected, no external components are required, just connect the positive power supply and ground wire. Independent watchdog oscillator circuit, so it can detect the working status of the clock source. The 32 B user code area can be used to store sequence codes and set parameters, 4 interrupt priorities.
5 System Software Design
The main program flow chart is shown in Figure 2. It adopts a humanized design, and the user does not need to do any operation, and it runs intelligently. After powering on, the system enters the initialization program and initializes the single-chip microcomputer P87LPC764, LCD, and E2PROM respectively. The indoor temperature is collected and displayed in real time, and then the single-chip microcomputer enters the sleep state, waiting for the external interrupt generated by the square wave generator or the occurrence of the keyboard interrupt.
When the square wave generator generates an interrupt to wake up the microcontroller every 0.5 s, the main program calls the cumulative time processing subroutine to accumulate the system running time and automatically store the time data into the E2PROM once an hour.
After the keyboard interrupt, the program enters the key interrupt service program, executes the key operation function, and completes the setting of the working mode, control cycle and adjustment range. After the interrupt program is executed, the system measures the real-time temperature and displays the temperature. The system has a total of 5 temperature control states. After the square wave generator generates an external interrupt every 0.5 s, the system queries the system temperature control state once and makes corresponding adjustments according to the corresponding state.
State 0 is the unstarted state, which means that the host has just started running, and the difference between the indoor temperature and the target temperature may be large. At this time, the system runs at full power for 5 minutes to make the indoor temperature reach the target temperature in the shortest time.
State 1 is the startup state. At this time, the relationship between the sampled indoor temperature and the user-set temperature value must be determined. When the indoor sampled temperature is greater than the user-set temperature, the system enters state 2, the acceleration state, to increase the output voltage of the digital/analog converter, thereby increasing the motor power and accelerating the refrigeration. When the indoor sampled temperature is less than the user-set temperature, the system enters state 3, the deceleration state, to reduce the output voltage of the digital/analog converter, thereby achieving the purpose of reducing the motor power. When the indoor sampled temperature is equal to the user setting, the system enters the equilibrium state and keeps the motor power unchanged. Thus, the room temperature is maintained at the constant temperature expected by the user, making people feel comfortable and satisfied. More importantly, its energy saving effect is as high as more than 30%.
6 Conclusion
After debugging, the program has good results in actual application. In the actual test, there are two points worth noting:
(1) Industrial data collection requires both accuracy and sensitivity, but these two points are sometimes in conflict with each other. In practical applications, 64 acquisitions are generally sufficient to ensure accuracy and sensitivity.
(2) Since the compared parameters can be stored in E2PROM, it can be applied to other occasions and industrial and mining requirements with only a slight modification of the circuit. Therefore, this low-cost, high-precision temperature control and energy-saving device has stronger competitiveness and is beneficial to both buyers and sellers.
This system is controlled by P87LPC764 single-chip microcomputer, with few peripheral circuits, stable system, powerful functions, convenient operation, low cost, and worthy of promotion.
Previous article:Application of Single Chip Microcomputer in Frequency Conversion Speed Regulation System
Next article:Central air conditioning intelligent management system using P87LPC764 single chip microcomputer
Recommended ReadingLatest update time:2024-11-16 16:46
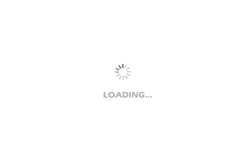
Professor at Beihang University, dedicated to promoting microcontrollers and embedded systems for over 20 years.
- Innolux's intelligent steer-by-wire solution makes cars smarter and safer
- 8051 MCU - Parity Check
- How to efficiently balance the sensitivity of tactile sensing interfaces
- What should I do if the servo motor shakes? What causes the servo motor to shake quickly?
- 【Brushless Motor】Analysis of three-phase BLDC motor and sharing of two popular development boards
- Midea Industrial Technology's subsidiaries Clou Electronics and Hekang New Energy jointly appeared at the Munich Battery Energy Storage Exhibition and Solar Energy Exhibition
- Guoxin Sichen | Application of ferroelectric memory PB85RS2MC in power battery management, with a capacity of 2M
- Analysis of common faults of frequency converter
- In a head-on competition with Qualcomm, what kind of cockpit products has Intel come up with?
- Dalian Rongke's all-vanadium liquid flow battery energy storage equipment industrialization project has entered the sprint stage before production
- Allegro MicroSystems Introduces Advanced Magnetic and Inductive Position Sensing Solutions at Electronica 2024
- Car key in the left hand, liveness detection radar in the right hand, UWB is imperative for cars!
- After a decade of rapid development, domestic CIS has entered the market
- Aegis Dagger Battery + Thor EM-i Super Hybrid, Geely New Energy has thrown out two "king bombs"
- A brief discussion on functional safety - fault, error, and failure
- In the smart car 2.0 cycle, these core industry chains are facing major opportunities!
- The United States and Japan are developing new batteries. CATL faces challenges? How should China's new energy battery industry respond?
- Murata launches high-precision 6-axis inertial sensor for automobiles
- Ford patents pre-charge alarm to help save costs and respond to emergencies
- New real-time microcontroller system from Texas Instruments enables smarter processing in automotive and industrial applications
- [Mil MYB-YT507 development board trial experience] Unboxing + HELLOWORLD
- How many versions of the C language main function are there? Which one is right?
- stm32f4 serial port 3 prompts NE error
- Design and implementation of asynchronous FIFO based on Verilog HDL.pdf
- The common-mode gain, differential-mode gain, and power supply rejection ratio of the op amp are shown in the figure.
- 01. Environment construction and driving 0.96OLED
- 【RT-Thread software package application work】Small alarm clock
- High-side current sampling problem
- Qorvo 100 MHz Envelope Tracking Solution for 5G
- 【Beetle ESP32-C3】3. Adjust LED brightness with knob (potentiometer) (Arduino)