Single-chip microcomputers are widely used in the fields of instrumentation, intelligent household appliances, and industrial control, with their advantages of small size, low power consumption, flexible application, and high cost performance. Single-chip microcomputers are also widely used in new electronic equipment of our army. When these equipments fail, the fault can be located on the printed circuit board using the built-in self-test program. Therefore, the performance test and fault diagnosis of the circuit board have become the focus of equipment maintenance work. When we developed a general automatic test system for electronic equipment, we studied the test of PCB, especially the fault diagnosis of PCB with single-chip microcomputer (referred to as CPU board) as one of the difficult problems. The test and diagnosis of CPU board have similarities with ordinary digital circuit boards, and also have their own characteristics, because CPU board is a PCB board with bus structure, and the bus devices (such as RAM, ROM, etc.) in its bus structure complete different functions as the program instructions proceed, and the pin data information changes continuously as the program is executed, so it is generally tested by simulation method. Simulation test is to apply the simulator developed by single-chip microcomputer system to circuit board test. General simulation test methods include: processor simulation test, memory simulation test, bus cycle simulation test, DMA simulation test, etc. To test non-bus devices (such as logic devices, timing devices, etc.), isolation technology can be used to inject test excitation, collect the response of the corresponding nodes for online testing, functional testing, etc. By weighing the performance, type and test speed requirements of the CPU board of the equipment under test, we chose a method that combines processor simulation testing with automatic probe testing in the test system.
2 Test content and implementation method
The CPU board generally has a single-chip microcomputer, ROM, RAM, digital I/O and other IC devices. The CPU board under test is provided with a specific excitation signal by the test system, executes a dedicated test program, completes the test task, and generates an output signal at the output port of the circuit board. The test system collects the output signal and compares it with the expected signal to determine whether the function of the circuit board is normal. When the functional test fails, the test system uses a programmable probe to collect signals from the key nodes inside the circuit board, compares them with the predetermined data, isolates and displays the fault through the fault tree analysis program, and determines the fault to one or several devices. For non-bus logic and timing digital integrated devices that cannot be judged by the test program, the real-time simulation test method can be combined with the auxiliary IC fixture test method to perform fault diagnosis and locate the fault to a certain integrated device.
The following technical supports are needed to complete the performance test and fault diagnosis of the above-mentioned CPU board.
2.1 Processor simulation test technology
The working program carried by the circuit board itself cannot provide the test vectors required by the test system and complete the test tasks. Test developers need to compile the corresponding MCU program according to the working principle, circuit design and device types of the circuit board under test to implement complex test algorithms, and edit the MCU test program into a library. When the test operator performs a functional test on a specific circuit board, he first replaces the MCU on the board under test with the simulation head corresponding to the MCU on the board under test. The test system calls the developed MCU program and writes it into the emulator, then executes the emulator offline running state, and uses the simulation system to read/write the bus devices on the board under test to determine whether its function is normal. Because the current MCU simulation development and debugging technology has become increasingly mature, only a small improvement in the MCU emulator hardware and software supplied on the market can be applied to the general automatic test system. The advantages of processor simulation testing are: dynamic functional testing at the same working rate as the board under test; complex test algorithms can be implemented, and complex test patterns can be easily generated; the fault coverage rate of bus device testing is high; due to the use of mature market simulation technology, the development workload is less.
2.2 Programmable probe automatic detection technology
The programmable automatic probe can programmatically locate the detection point and pierce the protective layer to obtain the detection signal. It uses stepper motor open-loop control, and the motor drives the probe to complete the vector displacement. The pressure of the probe contacting the circuit solder joint is adjustable. This device has two working states: remote control and local. The programmable signal is implemented using the IEEE488 interface, and the detection signal is led out by a dedicated cable. When developing the PCB to be tested, first calibrate the physical position of the PCB to be tested on the program-controlled probe device, and generally select two calibration points for record; then determine the coordinate parameters of the selected node through manual assisted positioning, and its local function is used at this time: use the displacement key on the control panel to accurately locate the probe to the node to be tested; then execute its remote control function, and the computer accurately reads and records the coordinate parameters; call the test point coordinate parameters into the test program, calculate the distance between the test point and the current probe position, call the needle lifting and displacement commands of the equipment, locate the probe at the node to be tested, and then call the needle drop and relative displacement to scratch the coating program, control the matrix switch and measuring instrument to measure, and record the test data. Compared with the traditional manual detection method, this automatic detection method has a high degree of automation and fewer human faults. Compared with the needle bed, it has good versatility and relatively fast test speed, which adapts to the current development trend of high chip integration and intensive installation. However, when testing special-shaped PCBs, it is difficult to install and fix the circuit board and cannot be detected.
2.3 Real-time simulation test technology for digital integrated circuits
For non-bus devices that cannot be involved in processor simulation tests, auxiliary test fixtures can realize the detection of digital integrated circuits. In the test system, we abandon the traditional back drive technology and adopt the test method of real-time simulation of the working environment of circuit devices. We use the logical relationship and conditional function provided by the graphical programming tool to establish a simulation device library, synchronously inject the input information of the actual device under test into the input end of the simulation device, collect the output data of the actual circuit, and compare it with the simulation output after the input data is calculated by the logical relationship and conditional function, so as to detect the working performance of this integrated circuit. The simulation implementation of combinational logic devices is relatively simple. The simulation device can be constructed using mathematical logic formulas according to the function table. The output of the sequential circuit device is not only related to the input at the time, but also to the previous level of the circuit timing state. It needs to be memorized and represented by the storage circuit composed of the storage trigger. Therefore, its construction process needs to solve the problems of the initial state, storage and memory of the sequential circuit. We use HPVEE software for simulation and use its special function functions such as Math, Sample & Hold and ShiftRegister to realize the construction of the simulation device library.
This technology avoids the device damage that the back-drive technology may cause to the CMOS circuit, and expands the scope of application. The improved sawtooth artificial fixture enhances its ability to pierce the coating and reduces the test failure caused by poor contact. However, in the simulation test development work, the huge simulation device library takes up a lot of space, which may affect the running speed.
3 Example Analysis
The general automatic test system for electronic equipment is a new, high-performance integrated test system that integrates VXI bus technology and various test and diagnosis technologies. It is used to complete the performance test and fault diagnosis of new electronic equipment. The system hardware consists of a main control computer, a VXI chassis and card-type instruments, a programmable AC and DC power supply, a universal adapter, and a programmable probe locator; the software design platform selects HPVEE, the basic environment is Windows98, the programming language is HPVEE and VC++, and the Chinese platform is Chinese Star. The software structure mainly consists of five parts: the diagnostic information library of the tested device, the system editing and development software library, the system test diagnosis database, the system test diagnosis program set, and the tested device test diagnosis report. PCB detection and diagnosis is one of the main functions of the test system. The system structure for CPU board testing is shown in Figure 1.
The software testing process is shown in Figure 2. During the software design process, the performance test and fault diagnosis of the PCB board under test can be performed separately or continuously, and the fault diagnosis history record can be saved. The fault display uses the test point image display method to call the circuit diagram of the board under test and dynamically display the test nodes and the location of the fault isolation device.


In this test system, the core (single-chip microcomputer) of the CPU board is tested from the inside out, which not only improves the accuracy of fault diagnosis, but also improves the fault coverage of the test system. In addition, it is worth mentioning that the RAM test in this system adopts the k/n code extraction graphic method, and its test performance and test time basically meet the requirements of the tested weapons and equipment. The ROM test uses the original code comparison method, using the additional functions of the emulator to read the actual working program code on the tested board and compare it with the standard original program code saved by the system to obtain the diagnosis result. This method does not require the addition of hardware and software and is simple and easy.
At present, the development of test and diagnosis software for various equipment has been completed on this system. Through fault simulation experiments, typical faults of 13 single-chip microcomputer application circuit boards such as computer communication boards, information machine CPU boards, information machine communication boards, artillery terminal CPU boards, and communication boards can be correctly isolated by the test system.
for circuit boards with microprocessors. Computer Technology and Applications, 2000, 20 (6): 25-30 2 Deng Bin et al. Research on simulation test methods for circuit boards with microprocessors. Microprocessor, 1999, (4): 57-59
3 Lei Zhiyong et al. Principles and hardware and software structure of online testing technology. Journal of Xi'an Institute of Technology, 1997, 17 (1): 61-65
4 Du Shuming. A practical method for fault diagnosis of digital circuit boards. Modern Radar, 1996, (6): 12-20
5 Ma Sasa et al. Real-time simulation test of general digital integrated circuits. Proceedings of the 2000 National Testing Academic Conference. Beijing: Armored Forces Engineering Academy, pp139-143
6 Wang Gefang et al. Research on automatic detection technology for printed circuit board diagnosis. Systems Engineering and Electronics, 2001, 23 (2): 23-27
Previous article:Intelligent temperature control meter with communication port based on 51 single chip microcomputer
Next article:Hardware and software implementation of serial communication between PC and embedded computer system
Recommended ReadingLatest update time:2024-11-17 00:06
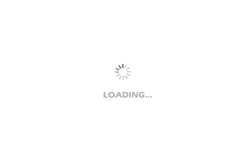
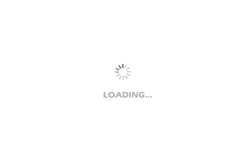
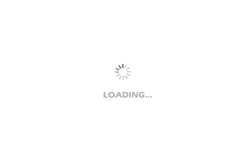
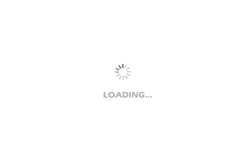
- Popular Resources
- Popular amplifiers
-
Wireless Sensor Network Technology and Applications (Edited by Mou Si, Yin Hong, and Su Xing)
-
Modern Electronic Technology Training Course (Edited by Yao Youfeng)
-
Modern arc welding power supply and its control
-
Small AC Servo Motor Control Circuit Design (by Masaru Ishijima; translated by Xue Liang and Zhu Jianjun, by Masaru Ishijima, Xue Liang, and Zhu Jianjun)
Professor at Beihang University, dedicated to promoting microcontrollers and embedded systems for over 20 years.
- Innolux's intelligent steer-by-wire solution makes cars smarter and safer
- 8051 MCU - Parity Check
- How to efficiently balance the sensitivity of tactile sensing interfaces
- What should I do if the servo motor shakes? What causes the servo motor to shake quickly?
- 【Brushless Motor】Analysis of three-phase BLDC motor and sharing of two popular development boards
- Midea Industrial Technology's subsidiaries Clou Electronics and Hekang New Energy jointly appeared at the Munich Battery Energy Storage Exhibition and Solar Energy Exhibition
- Guoxin Sichen | Application of ferroelectric memory PB85RS2MC in power battery management, with a capacity of 2M
- Analysis of common faults of frequency converter
- In a head-on competition with Qualcomm, what kind of cockpit products has Intel come up with?
- Dalian Rongke's all-vanadium liquid flow battery energy storage equipment industrialization project has entered the sprint stage before production
- Allegro MicroSystems Introduces Advanced Magnetic and Inductive Position Sensing Solutions at Electronica 2024
- Car key in the left hand, liveness detection radar in the right hand, UWB is imperative for cars!
- After a decade of rapid development, domestic CIS has entered the market
- Aegis Dagger Battery + Thor EM-i Super Hybrid, Geely New Energy has thrown out two "king bombs"
- A brief discussion on functional safety - fault, error, and failure
- In the smart car 2.0 cycle, these core industry chains are facing major opportunities!
- The United States and Japan are developing new batteries. CATL faces challenges? How should China's new energy battery industry respond?
- Murata launches high-precision 6-axis inertial sensor for automobiles
- Ford patents pre-charge alarm to help save costs and respond to emergencies
- New real-time microcontroller system from Texas Instruments enables smarter processing in automotive and industrial applications
- Computer Organization and Design: Hardware-Software Interface (RISC-V Edition)
- Please tell me how the following two circuit diagrams work
- TI Smart Building Systems: Using mmWave to count and track people
- RF front-end market in the 5G era
- What are the advantages of using stepper servo motors to replace stepper motors?
- FPGA_100 Days_Calculator Design
- What is a thick film non-inductive resistor? What is its main use?
- MCU's ADC sampling error
- LC Application Circuit Collection
- Some junk foods may change your brain and make you eat more