Power supply is an important component of every electronic device. According to the requirements of the International Electrotechnical Commission standard IEC 61000-3-2, the harmonic current components in the input current of electronic equipment have certain limits. Small power supplies can use simple passive power factor correction to obtain effective suppression, while large power supplies generally use active power factor correction controllers. As a widely used APFC based on L4891B design in larger power supplies, there have been many introductions, but in the actual use of power supply equipment, due to different working environments and usage requirements, there are often problems of one kind or another, which limit and affect its widespread use. In view of this, an in-depth analysis and discussion of many problems that arise in this process is carried out, and some practical and effective solutions are proposed.
1 How to improve efficiency
The development of modern technology requires electrical equipment to be both small and efficient, and also requires the input voltage to have a wider range of versatility. A complete Boost APFC includes full-wave rectification and boost DC-DC conversion. This configuration of APFC has many advantages: continuous input current and easy to improve power factor. The boost topology can also achieve high efficiency by limiting the input voltage, but when the input voltage range becomes wider, it becomes somewhat difficult to maintain the same high efficiency.
For this reason, in actual application products, three methods with simple circuits and high reliability are used: one is to reduce the reverse recovery loss of semiconductor diodes; the second is to replace MOSFET with IGBT to reduce turn-on loss; and the third is to reduce AC loss.
First, a SiC Schottky diode is selected, which has high temperature characteristics (the maximum allowable operating temperature reaches 300°C), high reverse withstand voltage, low on-resistance and high switching frequency. The above characteristics make the switching device smaller, and the increase in switching frequency also makes the volume of Boost APFC further reduced. At the same time, it also has a positive temperature coefficient, which is convenient for using multiple diodes in parallel when the current is large, and will not cause the current between the diodes to be unbalanced. In addition, the reverse recovery time and reverse current of this diode are very small, and it has very good temperature characteristics, and its reverse recovery time will not change with the increase of temperature. Using it will reduce the switching loss when the switch tube is turned on, thereby improving efficiency.
Secondly, one of the main reasons for replacing MOSFET with IGBT is that when the input voltage is low, the conduction loss of MOSFET switch increases rapidly due to the conduction resistance between the drain and source of the conduction device, that is, it is proportional to the square of the current as the current increases. However, the voltage saturation voltage drop between the collector and emitter of IGBT is almost the same, so its conduction loss increases relatively slowly and is only linearly related to the input current. This reduces the loss under a wide range of input voltages and improves the system efficiency.
Finally, reduce AC loss. The generation of AC loss is mainly caused by the ripple current of the inductor. Most of the loss comes from the magnetic core itself and is heavily dependent on the magnetic core material itself. For this reason, an inductor made of amorphous iron core material is used because it has excellent constant inductance characteristics and DC bias resistance, and has low loss. However, the cost is relatively high, but it has a significant effect on improving the efficiency of Boost APFC.
The relationship between the input power and efficiency of the Boost APFC with a rectifier bridge after adjustment is shown in Figure 1 below.
2 How to improve stability
Average current control technology is developed on the basis of peak current control technology. In this control mode, a current regulator is added between the multiplier and the comparator. The current regulator controls the average value of the input current to make it the same as the programming signal waveform. Since the current loop has a high gain bandwidth and a small tracking error, the transient characteristics are better. It is currently the most widely used control technology.
The voltage loop bandwidth of this technology is controlled below 20 Hz, and the current loop is required to be fast enough to meet the requirements of no distortion and low harmonics. The fact is that in the design process of actual products, the circuit designed by theoretical analysis works normally when tested with resistive loads or AC variable frequency compressors. However, when working with inductive loads such as DC variable frequency compressors, new unstable phenomena appear as shown in Figure 2, that is, the double cycle bifurcation phenomenon is encountered.
Since there are many ideal assumptions in the whole design process, for example: assuming that the output ripple of the converter is very small; assuming that it can be ignored when passing through a large output capacitor, and the large capacitor is not so large in actual use due to its high cost and large size; assuming that the effective value of the input voltage is used instead of the time-varying value, ignoring its time-varying influence, etc. In addition, due to the inherent properties of PFC, the PFC dynamic loop is always compensated with a low bandwidth, the purpose is not to respond to the ripple of the frequency 2xfL, where fL refers to the frequency of the AC power line. Therefore, when the load changes suddenly, the adjustment circuit cannot respond quickly, causing the output voltage to fluctuate too much. The stable system can adjust the disturbance by itself to re-enter the stable operation state; the unstable system cannot control the disturbance and enters the unstable operation state. As a result, the above-mentioned double cycle phenomenon occurs.
The voltage on the output capacitor of the converter is formed by the difference between the input power and the output power. The input power is controlled by the output current of the multiplier, and the output current of the multiplier is jointly determined by the feedforward current loop and the feedback voltage loop. Voltage feedforward can be used to compensate for the gain change caused by the input voltage, improve the stability of the loop and the instantaneous response to AC voltage transients. At the same time, the crossover frequency should be as high as possible to achieve fast tracking performance. There should be enough stability margin to make the system robust.
In order to solve this problem, the enhanced dynamic response function is adopted in the peripheral design of the chip. Using high ripple and low equivalent series resistance (ESR) capacitors, redesigning and adjusting the voltage loop and current loop network parameters, repeated experiments, and finally came to a conclusion. That is: carefully adjust the output of the output voltage error amplifier to make the transient tracking characteristics of the designed current loop stronger, and the converter has better ability to stabilize the output voltage under large current and inductive or resistive load conditions, eliminating the occurrence of double cycle phenomenon. The power factor and other performance indicators are normal, no adverse results are produced, and the expected purpose is achieved.
3 How to improve electromagnetic compatibility
Electromagnetic compatibility means that in the same electromagnetic environment, the equipment can work normally without being affected by other equipment, and at the same time, it does not interfere with other equipment that affects its work. Based on this, there are two reasons for interference, internal and external. Internal interference is mainly the impact of the main circuit switching process on the control circuit and external circuit, and external interference is the interference caused by the ripple of the power grid and the surrounding electrical equipment on the Boost PFC. In view of the three elements of interference generation, namely the interference source, coupling path and sensitive receiving equipment, the following measures are adopted:
(1) Reasonable layout and wiring. The interference intensity decreases with the square of the distance between the wire and the interference source. Therefore, in the layout and wiring of circuit components, the AC input and DC output should be separated and kept away as much as possible. The wiring should be strictly separated to simplify the current path and reduce mutual cross interference.
(2) Anti-interference measures for the main circuit and the control circuit itself. In the main circuit, the input and output ends of the single-phase rectifier bridge should be connected to high-frequency capacitors to block the high-frequency interference of the power grid. The reference voltage of the control circuit chip should be stable, and a high-frequency decoupling capacitor should also be connected to the ground.
In addition, the lead from the oscillator timing capacitor to the ground should be as short as possible. The connection from the drive input of the switch tube to the output of the control chip should be as short as possible to reduce external stray interference. The impedance of the connection between the IGBT and the FRD diode should be reduced as much as possible, that is, the length should be reduced and the width should be increased. In addition, the wiring distance between the IGBT and the smoothing capacitor should be as short as possible. The strong power part of the entire system should follow the principle of orderly entry and exit, and the wiring should not be routed back and forth. The output capacitor of the Boost PFC controller should also be connected in parallel with a small high-voltage capacitor to filter out high-frequency noise. It is also necessary to reduce the interference of the chip power supply. For example, a high-frequency decoupling capacitor can be connected to the ground at the output end of the power supply, so that the quality of the power supply can be improved. Reduce external interference and internal mutual influence, and improve the electromagnetic compatibility design level of the system.
The power factor correction circuit made using the average current boost mode of L4981B has continuous input current. And the
input current is small at the moment of Boost PFC switching, which is easy to filter electromagnetic interference. Principle 1: Reduce the interference generated by the PFC circuit itself to control the switching speed (dv/dt) of the switch tube; reduce the parasitic inductance of the high di/dt path to avoid unnecessary resonance in the circuit; reduce the switching frequency.
Principle 2: Try to prevent interference from being transmitted to the outside world. Reduce the capacitive coupling between high dv/dt nodes (for example, the collector of IGBT) and the outside world; reduce the loop area formed by high di/dt paths to avoid antenna effects; increase the filtering at the power input end.
Connection method of heat sink: The heat sink should be disconnected from the ground as much as possible. The heat sink of APFC should have a low-impedance AC path between the cold point of the APFC circuit. This path can be directly connected or connected in series with a Y capacitor of several nF. The value of the Y capacitor should take into account the parasitic capacitance between the dv/dt device and the heat sink in the circuit. If the Y capacitor is n times larger than the parasitic capacitance, the common-mode interference coupled to the outside world through the heat sink will also be reduced by n times.
The impact of APFC inductance on electromagnetic compatibility: The wire at the end of the inductor connected to the switch tube should be as close to the PFC circuit as possible, and a magnetic ring should be connected in series; try to use ring-shaped inductor materials to reduce leakage magnetic flux.
The unique frequency jitter modulation mode of the control chip L4981B makes the original single switching signal frequency jitter in a certain range, forming a continuous spectrum, and finally reducing the spectrum peak and electromagnetic interference.
The switching frequency jitter control method adjusts the jitter switching frequency to disperse the energy concentrated on the switching frequency and its harmonics to the frequency conversion band around them (see Figure 3), thereby reducing the electromagnetic interference amplitude at each frequency point to reach a value lower than the limit specified by the electromagnetic interference standard.
Although this method cannot reduce the total interference energy, it disperses the interference energy to a wider frequency band, making it easier for Boost PFC to reach the limit value below the electromagnetic interference standard.
In practical terms, the interference energy is dispersed within a certain frequency bandwidth. Compared with the energy-concentrated point-frequency pulse interference, the harm of electromagnetic interference to the environment is reduced. Frequency jitter control will not affect the duty cycle while changing the frequency, and will not affect the output voltage.
Experiments have shown that frequency jitter control can significantly reduce the maximum interference amplitude and other harmonic point amplitudes by dispersing the interference energy concentrated on the switching frequency and its multiple frequency points to the nearby frequency bands; at the same time, this control method keeps the output voltage unchanged and also suppresses the electromagnetic interference of the output voltage.
4 How to implement circuit protection
Some protections are inherent in the chip, such as input undervoltage protection, input overcurrent protection, output overvoltage protection, etc. This only requires a reasonable circuit design and parameter configuration according to the chip's functions, which will not be described in detail here. Some protections are not inherent in the chip, but are required by the system. In this case, it is necessary to conduct a specific analysis based on the specific situation and design a protection circuit suitable for the system, that is, a fault protection circuit, that is, when the output voltage is low, ensure that the subsequent frequency conversion system can respond quickly to avoid unnecessary losses. This design adopts the design method shown in Figure 4.
In Figure 4, fault is the voltage to be measured after the resistor divider. This design cleverly utilizes the reference voltage characteristics of the low-cost adjustable shunt reference source TL431 and a single-power supply comparator with a temperature-compensated threshold composed of peripheral components. The specific principle is: after adding a variable voltage to the reference end, a high +15 V or low +2.5 V level voltage will be output between the cathode and the anode, and then the voltage reduction effect of the light-emitting diode and the diode will be applied to the optocoupler and other devices, and the high and low levels will be output at FAULT and fed back to the main controller, thereby playing the role of fault detection. The advantage of this circuit is that the circuit cost is low, simple and reliable. In the test, the performance is good.
In addition, in order to prevent the instantaneous large current during the power-on process from damaging the diode in the PFC, a surge protection circuit must be provided at the power input end, such as a PTC resistor plus a relay. This ensures that the maximum instantaneous value of the input current is within a controllable range and does not cause damage to the circuit.
5 How to improve cost performance, reliability and electrical safety requirements
The reduction in the number of components and the simplification of circuit design have improved the performance-price ratio of the entire system. In addition, the boost inductor L in the circuit can prevent rapid voltage and current transients, thereby improving the reliability of the entire circuit.
In recent years, the rapid development of economy and science and technology has made the requirements for the power factor of various electrical equipment higher and higher. Improving the performance of power factor correction circuits has become a topic with both theoretical value and practical significance. There is no end to improvement. With the development of power electronics technology and related disciplines, there will be more and more methods to improve the performance of APFC.
As a Class I device, it should meet the requirements of basic insulation and grounding. This requires:
First, the grounding is good and meets the potential difference requirements of the grounding point. Anti-drop gaskets should be used. The grounding wire should be thick enough to meet the grounding continuity requirements. At the same time, there should be a grounding symbol at the grounding end. When powering on, it should be connected before the power lines L and N. When powering off, it should be disconnected after the power lines L and N.
Secondly, the electrical clearance and creepage distance between the primary strong current part and the secondary weak current part of the power supply must meet the requirements of the power supply voltage or/and the voltage of the primary and secondary devices such as the transformer. This includes: the internal structure of the switching power supply transformer, the internal and external electrical clearance and creepage distance of the optocoupler connected across the strong current part and the secondary weak current part of the power supply meet the requirements, the cross-over capacitor uses a Y1 capacitor, the working voltage must meet the requirements and pass the corresponding safety certification, and the primary and secondary power supply must also meet the corresponding high voltage withstand requirements.
Thirdly, the layout of the connection between the primary strong current and the secondary weak current part of the power supply inside the device must meet the requirements of safety regulations. The connection lines between the primary and secondary cannot touch or cross each other, but should use different circuits. At the same time, it is necessary to ensure that they meet the double insulation or reinforced insulation required by the safety regulations. This is conducive to meeting the relevant requirements of the safety regulations and has a positive impact on the suppression of electromagnetic interference. It is also beneficial and harmless.
Finally, in the coordination with other circuits, the same requirements must be followed. Consider the overall rather than local requirements, so that you can get twice the result with half the effort.
6 Conclusion
Through the improvement and perfection of the average current mode active power factor correction controller designed using L4981B, the performance of the circuit has become more stable, the scope of use has been further expanded, and the expected goal of the transition from a research prototype to an actual production prototype has been achieved. Practice has proved that the above method is not only effective but also feasible, and truly realizes the overall performance optimization of the active power factor correction circuit. This also has a certain reference role in improving the performance of active power factor correction circuits using other similar chip designs.
Previous article:Introduction to the working principles of various protection circuits for LED switching power supplies
Next article:Voltage-type critical working mode APFC control chip FAN7530
Recommended ReadingLatest update time:2024-11-17 03:03
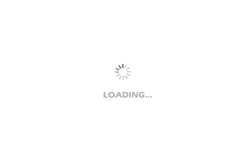
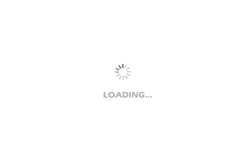
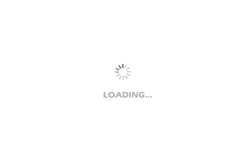
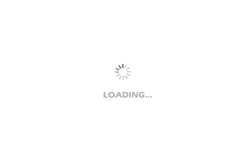
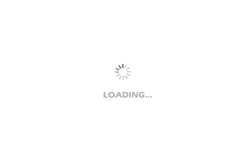
- Popular Resources
- Popular amplifiers
-
New Energy Vehicle Detection and Diagnosis Experiment (Edited by Mao Caiyun, Zhou Xien, and Long Jiwen)
-
Virtualization Technology Practice Guide - High-efficiency and low-cost solutions for small and medium-sized enterprises (Wang Chunhai)
-
Design of an adaptive constant on-time buck DC-DC converter with high efficiency and low power consumption
-
Research on design technology of high-efficiency step-up DC-DC converter with wide load range
- MathWorks and NXP Collaborate to Launch Model-Based Design Toolbox for Battery Management Systems
- STMicroelectronics' advanced galvanically isolated gate driver STGAP3S provides flexible protection for IGBTs and SiC MOSFETs
- New diaphragm-free solid-state lithium battery technology is launched: the distance between the positive and negative electrodes is less than 0.000001 meters
- [“Source” Observe the Autumn Series] Application and testing of the next generation of semiconductor gallium oxide device photodetectors
- 采用自主设计封装,绝缘电阻显著提高!ROHM开发出更高电压xEV系统的SiC肖特基势垒二极管
- Will GaN replace SiC? PI's disruptive 1700V InnoMux2 is here to demonstrate
- From Isolation to the Third and a Half Generation: Understanding Naxinwei's Gate Driver IC in One Article
- The appeal of 48 V technology: importance, benefits and key factors in system-level applications
- Important breakthrough in recycling of used lithium-ion batteries
- Innolux's intelligent steer-by-wire solution makes cars smarter and safer
- 8051 MCU - Parity Check
- How to efficiently balance the sensitivity of tactile sensing interfaces
- What should I do if the servo motor shakes? What causes the servo motor to shake quickly?
- 【Brushless Motor】Analysis of three-phase BLDC motor and sharing of two popular development boards
- Midea Industrial Technology's subsidiaries Clou Electronics and Hekang New Energy jointly appeared at the Munich Battery Energy Storage Exhibition and Solar Energy Exhibition
- Guoxin Sichen | Application of ferroelectric memory PB85RS2MC in power battery management, with a capacity of 2M
- Analysis of common faults of frequency converter
- In a head-on competition with Qualcomm, what kind of cockpit products has Intel come up with?
- Dalian Rongke's all-vanadium liquid flow battery energy storage equipment industrialization project has entered the sprint stage before production
- Allegro MicroSystems Introduces Advanced Magnetic and Inductive Position Sensing Solutions at Electronica 2024
- Car key in the left hand, liveness detection radar in the right hand, UWB is imperative for cars!
- After a decade of rapid development, domestic CIS has entered the market
- Aegis Dagger Battery + Thor EM-i Super Hybrid, Geely New Energy has thrown out two "king bombs"
- A brief discussion on functional safety - fault, error, and failure
- In the smart car 2.0 cycle, these core industry chains are facing major opportunities!
- Rambus Launches Industry's First HBM 4 Controller IP: What Are the Technical Details Behind It?
- The United States and Japan are developing new batteries. CATL faces challenges? How should China's new energy battery industry respond?
- Murata launches high-precision 6-axis inertial sensor for automobiles
- Ford patents pre-charge alarm to help save costs and respond to emergencies
- Vehicle GPS Antenna Installation Location
- MSP430F5529 generates PWM waves with CCS
- FPGA Multiplier
- Quartus2 simulation can not produce waveform
- After the microcontroller is connected to the computer via a USB cable, the problem of "unrecognized USB device" appears
- 2. GD32L233C-START environment construction
- Commonly used algorithms for drones - Kalman filter (Part 2)
- STEVAL-IDB007V1_by cruefox
- AI automatically generates Spring Festival couplets to warm up for FZ5
- STM32F407VG mount SD card