SiC is being incorporated into higher power, higher voltage designs such as electric vehicle (EV) motor drives, EV fast chargers, on-board and off-board chargers, wind and solar inverters, and industrial power supplies.
Power system designers face several challenges when turning to SiC:
Can the test equipment accurately measure the fast switching dynamics of SiC systems?
How can I accurately optimize door drive performance and idling time?
Do common mode transient signals affect measurement accuracy?
Is the ringing I see real or is it just the probe response?
Solving these challenges is difficult for engineers. What’s more, engineers need to accurately view all these signals to make the right design decisions in a timely manner. Increasing design margins and overdesigning will only drive up costs and reduce performance. Using the right measurement equipment is the key to solving the problem.
The accuracy of time domain measurements and switching loss calculations is affected by the accuracy, bandwidth, and latency of the probes used to acquire the measurement data. Although this discussion focuses on the differences between oscilloscope probes, the specific implementation methods (such as layout, parasitic signals, and coupling) also play a key role in measurement accuracy. Three important parameters need to be measured: gate voltage, drain voltage, and current to properly verify power modules using SiC technology.
Gate voltage measurement
Measuring the gate voltage of a SiC power device is challenging because it is a low voltage signal (~20 Vpp) referenced to a node that may have high DC offset and high dv/dt relative to the oscilloscope ground. Additionally, the largest dv/dt occurs during the switching event, which is the time of greatest concern when measuring the gate signal. Even in topologies where the source of the device is tied to ground, parasitic impedance between the circuit ground and the oscilloscope ground can still cause erroneous readings due to fast transients. This requires the measurement equipment to be backcoupled from ground and have very large common-mode rejection ratios. This gate voltage measurement has traditionally been made with standard differential probes (Figure 1a), but the latest optically isolated probes, such as the IsoVu probing system (Figure 1b), can greatly improve the accuracy of this measurement.
Figure 1. (a) Differential voltage probe example: Tektronix differential probe THDP0200 probe and accessories;
(b) Tektronix lsoVu TIVP1 optically isolated probe (TIVPMX10X, ±50 V sensor tip).
Figure 2 compares high-side gate voltage measurements made with a standard differential probe and an opto-isolated probe. High-frequency ringing is seen on the gate of the device after it passes through the threshold region, both when turned off and on. Some ringing is expected due to coupling between the gate and the power loop. However, the amplitude of the ringing is significantly higher in the differential probe than in the opto-isolated probe. This is likely due to common-mode currents induced within the probe by the reference voltage change, as well as glitches in the standard differential probe. While the waveform measured by the differential probe in Figure 2 appears to pass through the device’s maximum gate voltage, the opto-isolated probe’s measurements are more accurate and clearly show the device is within specification.
Figure 2. A differential probe (blue trace) compared to an IsoVu optically isolated probe (yellow trace).
Application engineers using standard differential probes for gate voltage measurements should beware as they may not be able to distinguish between the probe and measurement system artifacts shown here and actual violations of device ratings. Such measurement artifacts may cause designers to increase gate resistance to slow down switching transients and reduce ringing. However, this will not necessarily increase losses in SiC devices. For this reason, it is important to use a measurement system that accurately reflects the actual dynamics of the device in order to properly design the system and optimize performance.
Drain voltage measurement
Differential probes and ground-referenced probes are two common methods for making voltage measurements in power electronics systems. Differential probes are a popular choice because they can be added to any node in the circuit without any problems. Ground-referenced probes are more difficult to implement because their shield pins are connected to the oscilloscope's ground. Incorrectly implemented ground-referenced measurements generally result in a small ground current on the probe reference, significantly reducing the accuracy of the measurement. This effect is more pronounced in SiC designs because high dv/dt can introduce parasitic currents into the oscilloscope probe ground reference, causing measurement errors. In more severe cases (when the ground-referenced shield is connected to the power signal), large currents can flow through the ground, damaging the probe or oscilloscope. In the worst case, a failed connection from the instrument to ground can cause the oscilloscope's outer metal shell to float to the bus voltage, posing a serious threat to the operator's personal safety.
When using a ground-referenced CVR, grounding becomes even more critical. When using a ground-referenced probe with a CVR, it is possible to bypass the CVR through the oscilloscope shield path, as shown in Figure 3. This can cause the entire device current to flow through the oscilloscope, potentially damaging the voltage probe or oscilloscope, and can also pose a significant personal safety hazard. In general, differential probes are recommended for device drain-to-source measurements.
Figure 3. When two ground-referenced probes are connected to reference planes at different voltages, device currents bypass the CVR and flow through the ground leads and the oscilloscope. This can cause measurement errors and potentially damage the equipment.
Current measurement
Current view resistors (CVRs) and Rogowski coils (Figure 4 a and b) are two common methods of measuring current in power electronics systems. Rogowski coils are a popular choice because they can be easily added to the circuit and are non-intrusive, but these probes typically have significant bandwidth limitations and are not suitable for SiC. CVRs, on the other hand, have extremely high bandwidths and can make accurate current measurements. Unfortunately, the need to add additional devices when connecting transistors in series requires careful planning of the PCB layout, as adding a CVR generally increases the parasitic inductance in the circuit.
Figure 4 compares a typical SiC hard switching event measured with a Rogowski coil and a CVR. The bandwidth of the Rogowski coil is significantly lower, causing artificial suppression of the ringing present in the test waveform. More importantly, it artificially suppresses the initial overshoot, giving an early warning of the measured di/dt.
Figure 4. CVR and Rogowski current probe, CAB016M12FM3 (TJ = 25°C, RG = 6.8, Vos = 600 V, Is = 100A).
Figure 5. CVR and Rogowski current probe, CAB011M12FM3 (TJ = 150°C, RG = 1W), VDS = 600 V, IS = 100A).
Figure 5 compares the different probes under more aggressive switching conditions, highlighting two points of interest. First, the Rogowski coil does not adequately capture the shape of the current waveform when turning off, missing the slight knee that would reduce the apparent switching losses. Additionally, the predicted drop in di/dt when turning on also causes the predicted switching losses to slow down. The cumulative effect of the reduced bandwidth of the Rogowski coil is a reduction in the estimated switching losses.
Figure 6 directly compares the switching losses estimated by the Wolfspeed WolfPACK™ CAB011Ml2FM3 in the drain current. As mentioned above, the Rogowski coil consistently underestimates the switching losses of the circuit when predicting, giving the impression that the circuit losses are too optimistic. Since the inconsistency is related to the probe bandwidth limitation, it depends on the edge rate of the transistor and will increase further with more aggressive gate resistors. For slow switching technologies (such as IGBTs), the difference in metrology is negligible.
Figure 6. Estimation of switching losses (Eoff + Eon) using different probes (CAB011M12FM3, TJ = 150°C , RG = 1W).
In addition to having sufficient bandwidth and noise suppression, the probes used for head delay must also be time-delay corrected to ensure delay matching between voltage and current signals. Even a 1-2ns mismatch between voltage and current probe delays can result in 30% or more Eon and Eoff measurement errors. Proper time delay correction is critical for the fast switching transients inherent in SiC systems.
Before deskewing, the probes are automatically zeroed and calibrated, if necessary, to eliminate any offset or calibration errors. The voltage probes VDS and VGS can be deskewed by connecting both probes to a function generator using symmetrical connections. Using a square wave generated by the function generator, check that the ringing and falling edges of the signals are aligned. The circuit board shown in Figure 7 can be used to easily connect a function generator to any voltage probe. The function generator signal is connected to the center of the board, and various options are provided around the edge of the board for oscilloscope probe connections to accommodate a variety of probe interfaces.
Figure 7. The power measurement deskew and calibration fixture (067-1686-00)7 can compensate for timing differences between voltage and current probes.
There are several methods to correct the VDS and ID probe delays to ensure that the switching loss is measured correctly. The principle behind all methods is the same, that is, to have a test circuit, such as the fixture shown in Figure 7, that is as close to a pure resistor circuit as possible so that the voltage waveform and current waveform are aligned. This test circuit can then be used to correct the current probe delay to match the voltage probe response.
Previous article:Innovative SABICLNP™ ELCRES™ EXL resin provides excellent flame retardancy for ultra-thin wall parts
Next article:Bourns Launches Newest Precision Current Sense Resistors
Recommended ReadingLatest update time:2024-11-16 23:56
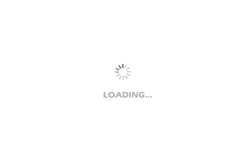
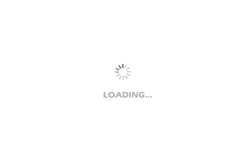
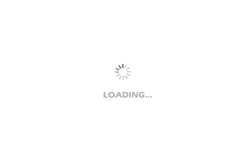
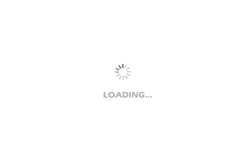
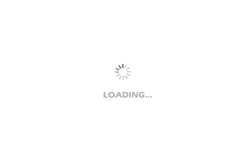
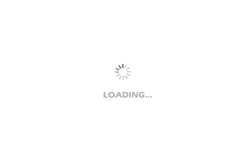
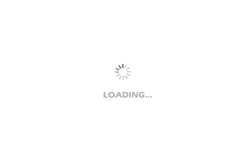
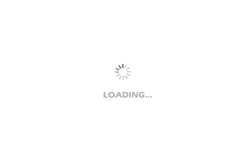
- Popular Resources
- Popular amplifiers
-
Progress in high-power silicon carbide power electronic devices
-
Study on the Behavioral Model of Silicon Carbide MOSFET Power Module and EMI Prediction of Low-Voltage Auxiliary Power Supply
-
Test solutions in the 800V electric drive development and design process (Tektronix China)
-
Overview and Prospect of Silicon Carbide Power Device Technology
- MathWorks and NXP Collaborate to Launch Model-Based Design Toolbox for Battery Management Systems
- STMicroelectronics' advanced galvanically isolated gate driver STGAP3S provides flexible protection for IGBTs and SiC MOSFETs
- New diaphragm-free solid-state lithium battery technology is launched: the distance between the positive and negative electrodes is less than 0.000001 meters
- [“Source” Observe the Autumn Series] Application and testing of the next generation of semiconductor gallium oxide device photodetectors
- 采用自主设计封装,绝缘电阻显著提高!ROHM开发出更高电压xEV系统的SiC肖特基势垒二极管
- Will GaN replace SiC? PI's disruptive 1700V InnoMux2 is here to demonstrate
- From Isolation to the Third and a Half Generation: Understanding Naxinwei's Gate Driver IC in One Article
- The appeal of 48 V technology: importance, benefits and key factors in system-level applications
- Important breakthrough in recycling of used lithium-ion batteries
- Innolux's intelligent steer-by-wire solution makes cars smarter and safer
- 8051 MCU - Parity Check
- How to efficiently balance the sensitivity of tactile sensing interfaces
- What should I do if the servo motor shakes? What causes the servo motor to shake quickly?
- 【Brushless Motor】Analysis of three-phase BLDC motor and sharing of two popular development boards
- Midea Industrial Technology's subsidiaries Clou Electronics and Hekang New Energy jointly appeared at the Munich Battery Energy Storage Exhibition and Solar Energy Exhibition
- Guoxin Sichen | Application of ferroelectric memory PB85RS2MC in power battery management, with a capacity of 2M
- Analysis of common faults of frequency converter
- In a head-on competition with Qualcomm, what kind of cockpit products has Intel come up with?
- Dalian Rongke's all-vanadium liquid flow battery energy storage equipment industrialization project has entered the sprint stage before production
- Allegro MicroSystems Introduces Advanced Magnetic and Inductive Position Sensing Solutions at Electronica 2024
- Car key in the left hand, liveness detection radar in the right hand, UWB is imperative for cars!
- After a decade of rapid development, domestic CIS has entered the market
- Aegis Dagger Battery + Thor EM-i Super Hybrid, Geely New Energy has thrown out two "king bombs"
- A brief discussion on functional safety - fault, error, and failure
- In the smart car 2.0 cycle, these core industry chains are facing major opportunities!
- The United States and Japan are developing new batteries. CATL faces challenges? How should China's new energy battery industry respond?
- Murata launches high-precision 6-axis inertial sensor for automobiles
- Ford patents pre-charge alarm to help save costs and respond to emergencies
- New real-time microcontroller system from Texas Instruments enables smarter processing in automotive and industrial applications
- "Operational Amplifier Parameter Analysis and LTspice Application Simulation" 4. Chapter 2 Slew Rate
- Have you ever been shocked by a capacitor?
- MicroPython 1.19 released
- [Sipeed LicheeRV 86 Panel Review] 3- Transplanting LVGL
- EEWORLD University ---- FreeRTOS on stm32 ST
- Read the white paper on Renesas Electronics' power module series and win double gifts: energy boost gift & 100% recommendation gift!
- Understanding common mode and differential mode
- 【McQueen Trial】Unboxing and microbit
- LLC or Flyback Topology? It all depends on the end-user requirements
- The basics of power management you must know