Some application designs have higher requirements on the speed of the system's switching power supply to provide voltage output. Figure 1 is a bootstrap circuit, also known as a startup circuit, for such a power supply system. In the power factor correction (PFC) pre-regulator of the switching power supply, the circuit's pulse width modulator (PWM) IC1 draws the power required for normal operation from the auxiliary coil L1 wound around the magnetic core of the boost inductor L2 and the diode D1.
Figure 1: In a traditional switching power supply bootstrap circuit, trickle charge resistor RT and capacitor CH provide startup power to the pulse width modulator and controller IC1
The resistor RT and the capacitor CH together form a trickle-charge circuit, which is responsible for providing power to the bootstrap boost component IC1 for its normal operation. The RT resistor value in the traditional design is usually large, so that after providing the required standby current, the circuit can continue to charge the potential holding capacitor CH with a small current, thereby ensuring that the capacitor can supply enough power to the PWM circuit before the power converter starts operating. Although the startup response speed of this type of circuit is slow, it is not a problem under normal operating conditions.
If the system's startup response speed needs to be accelerated, designers can rearrange the shunt regulator of the startup circuit to speed up the bootstrap boost time (Figure 2). The bootstrap boost circuit is composed of capacitor CT, shunt regulator component D1 (TL431), diode D3, transistor Q1, and resistors from RA to RD. When the power is just turned on, capacitor CT has no charge, and the voltage VAUX at the PWM power input is determined by the series regulator composed of Q1 and D1.
Figure 2: In this improved bootstrap boost circuit, transistor Q1 provides a reliable initial current pulse to capacitor CH, enabling the circuit to start up and provide power output faster.
At power-up, the VAUX voltage rises to a peak voltage VAUX_PEAK, which is determined by the ratio of resistors RA to RB. Capacitor CT and resistor RC set the cutoff time and voltage of the bootstrap boost circuit to conserve power. Resistor RD provides bias current to shunt regulator D1 (TL431), while resistor RE limits the collector current of transistor Q1, ensuring it stays in the safe operating area.
When designing the circuit, first select the resistors RA and RB according to the following formula so that the peak charging voltage meets the requirements:
VREF is the internal reference voltage of TL431. Then select the resistor RC so that the parallel voltage value is lower than the rated VAUX voltage (VAUX_NOMINAL) provided by the auxiliary coil:
Finally, select the capacitor CT and set the bootstrap boost time TBOOT to:
This circuit is shown in Figure 1, where diode D2 and auxiliary coil L2 provide normal operating power to IC1.
Previous article:Design of high-precision digital controlled DC regulated power supply based on NiosII
Next article:Low voltage dropout DC regulated power supply composed of operational amplifier
Recommended ReadingLatest update time:2024-11-16 17:38
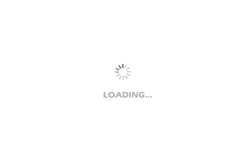
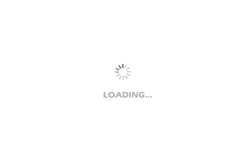
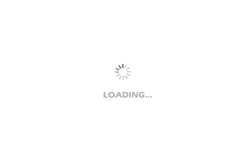
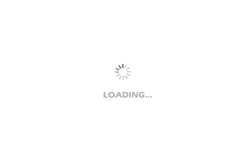
- Popular Resources
- Popular amplifiers
-
西门子S7-12001500 PLC SCL语言编程从入门到精通 (北岛李工)
-
Small AC Servo Motor Control Circuit Design (by Masaru Ishijima; translated by Xue Liang and Zhu Jianjun, by Masaru Ishijima, Xue Liang, and Zhu Jianjun)
-
Intelligent Control Technology of Permanent Magnet Synchronous Motor (Written by Wang Jun)
-
100 Examples of Microcontroller C Language Applications (with CD-ROM, 3rd Edition) (Wang Huiliang, Wang Dongfeng, Dong Guanqiang)
- MathWorks and NXP Collaborate to Launch Model-Based Design Toolbox for Battery Management Systems
- STMicroelectronics' advanced galvanically isolated gate driver STGAP3S provides flexible protection for IGBTs and SiC MOSFETs
- New diaphragm-free solid-state lithium battery technology is launched: the distance between the positive and negative electrodes is less than 0.000001 meters
- [“Source” Observe the Autumn Series] Application and testing of the next generation of semiconductor gallium oxide device photodetectors
- 采用自主设计封装,绝缘电阻显著提高!ROHM开发出更高电压xEV系统的SiC肖特基势垒二极管
- Will GaN replace SiC? PI's disruptive 1700V InnoMux2 is here to demonstrate
- From Isolation to the Third and a Half Generation: Understanding Naxinwei's Gate Driver IC in One Article
- The appeal of 48 V technology: importance, benefits and key factors in system-level applications
- Important breakthrough in recycling of used lithium-ion batteries
- Innolux's intelligent steer-by-wire solution makes cars smarter and safer
- 8051 MCU - Parity Check
- How to efficiently balance the sensitivity of tactile sensing interfaces
- What should I do if the servo motor shakes? What causes the servo motor to shake quickly?
- 【Brushless Motor】Analysis of three-phase BLDC motor and sharing of two popular development boards
- Midea Industrial Technology's subsidiaries Clou Electronics and Hekang New Energy jointly appeared at the Munich Battery Energy Storage Exhibition and Solar Energy Exhibition
- Guoxin Sichen | Application of ferroelectric memory PB85RS2MC in power battery management, with a capacity of 2M
- Analysis of common faults of frequency converter
- In a head-on competition with Qualcomm, what kind of cockpit products has Intel come up with?
- Dalian Rongke's all-vanadium liquid flow battery energy storage equipment industrialization project has entered the sprint stage before production
- Allegro MicroSystems Introduces Advanced Magnetic and Inductive Position Sensing Solutions at Electronica 2024
- Car key in the left hand, liveness detection radar in the right hand, UWB is imperative for cars!
- After a decade of rapid development, domestic CIS has entered the market
- Aegis Dagger Battery + Thor EM-i Super Hybrid, Geely New Energy has thrown out two "king bombs"
- A brief discussion on functional safety - fault, error, and failure
- In the smart car 2.0 cycle, these core industry chains are facing major opportunities!
- The United States and Japan are developing new batteries. CATL faces challenges? How should China's new energy battery industry respond?
- Murata launches high-precision 6-axis inertial sensor for automobiles
- Ford patents pre-charge alarm to help save costs and respond to emergencies
- New real-time microcontroller system from Texas Instruments enables smarter processing in automotive and industrial applications
- Special registers in ARM
- How to perform loopback test on Ethernet UDP through DDR3?
- ADI's smoke detector integrated solution based on ADPD188BI live data collection
- What is the use of a 28V operating voltage microcontroller?
- The microcontroller drives the P-MOS to conduct abnormally through the NPN transistor?
- How to support domestic suppliers who use tricks?
- Thank you for being there + seeking change
- RVB2601 First Experience
- If the Lingte LT3789 is to output 12V10A, can it be directly connected in parallel with MOS?
- MSP430 and ATK-NEO-6M GPS module