introduction
Since the advent of the single-chip switching power supply in 1994, conditions have been created for the promotion and popularization of switching power supplies. The application of switching power supplies involves various fields of electronic and electrical equipment, such as program-controlled switches, communications, electronic testing equipment power supplies, control equipment power supplies, etc., which have been widely used in switching power supply technology, and have promoted the rapid development of switching power supply technology. Various new technologies, new processes and new devices have sprung up like mushrooms after rain, making the application of switching power supplies increasingly popular. The high frequency of switching power supplies is the direction of its development, from the initial 20kHz to the current hundreds of kHz or even several megahertz. High frequency brings about the miniaturization of switching power supplies. At present, switching power supplies are developing in the direction of high efficiency, energy saving, safety, environmental protection, miniaturization and lightness.
Introduction to LT3573
LT3573 is a monolithic switching regulator designed for isolated flyback topology. In the isolated flyback topology, the transformer primary circuit needs to constantly sense the change of the secondary output voltage in order to maintain the output voltage stability. In previous circuit topologies, optocouplers are often used or transformer windings are added to obtain output voltage feedback information. The problems with optocouplers are: ① Output power consumption; ② Increased cost and complex circuit structure; ③ Limited dynamic response, device nonlinearity, aging, etc., all bring troubles.
In addition, if a transformer or transformer winding is added, the physical size of the transformer will be increased, the cost will increase, and its dynamic response will not be very good. However, the LT3573 does not require an external optocoupler or a third winding. Its unique built-in flyback error amplifier starts sampling the output voltage information when the secondary winding current is zero, and directly detects the change information of the output voltage from the flyback voltage waveform of the primary side of the transformer, and automatically maintains the stability of the output voltage. This is also the highlight of this IC design. Due to the action of RFB and Q2, the flyback voltage is converted into current. Almost all of this current flows through the resistor RREF to form a feedback voltage, enters the flyback error amplifier, and is compared with its 1.22V reference voltage, so that the subsequent circuit can adjust the duty cycle of the switch tube to achieve the purpose of stabilizing the output voltage, as shown in Figure 1.
Figure 1 LT3573 internal topology block diagram
A 1.25A, 60V NPN power switch tube and all control logic units are integrated into the LT3573 in a 16-pin MSOP package. This greatly simplifies the peripheral circuit design of the integrated block application, works within the input voltage range of 3V~40V, and has a maximum output power value of up to 7W. It can be applied to many fields that require isolated power supplies, such as industry, medical, data communications, automotive applications, low-power PoE and VoIP phone interfaces, etc.
The LT3573 operates in boundary mode, which allows the use of a smaller transformer compared to an equivalent continuous conduction mode design.
Design of clamping circuit
The transformer leakage inductance Lsl (both primary and secondary), as shown in Figure 2, causes a voltage spike on the primary side. When the output switch is turned off, this spike becomes sharper with higher load current, which requires the selection of an energy absorption network to consume the energy stored in the leakage inductance. In most cases, a snubber circuit is required to prevent overvoltage from breaking down the output switch node. Therefore, the transformer leakage inductance should be minimized.
Select the absorption network to clamp the flyback switching voltage spike. Due to the voltage spike generated by the leakage inductance of the switching transformer, the flyback voltage can be calculated as follows:
(1
Where: VF—forward voltage drop of the rectifier diode D2 on the secondary side of the transformer;
ISEC—transformer secondary current;
ESR—total impedance of the secondary circuit;
NPS—Effective primary-to-secondary turns ratio of transformer;
VOUT—Output voltage.
The sum of this voltage and the input voltage (VIN + VFLBK) is directly added to the collector of the power switch Q1, which can easily cause secondary breakdown and damage to the power switch Q1. In order to clamp the voltage spike within the rated value of the switch, the most commonly used RCD absorption circuit is to transfer the energy stored in the leakage inductance to the absorption network capacitor C1 during the switch off period, and finally consume it on the resistor R1, as shown in Figure 2.
Figure 2 RCD absorption circuit diagram
The switching speed of the clamping diode D1 here must be fast enough, otherwise, when the switch tube is turned off, the leakage inductance spike cannot be transmitted to the capacitor C1 in time and will generate instantaneous high voltage at the collector of the switch tube Q1, as shown in Figure 3. Therefore, Schottky diodes are usually the best choice.
Figure 3 Schematic diagram of the collector voltage waveform of the switch tube Q1
Once the clamping diode D1 is turned on, the leakage current will be absorbed by C1. The absorption time must not be longer than 150ns, as shown in Figure 3. 4.1 Minimum primary inductance of the tSP switching transformer design
Because LT3573 adjusts the isolated output voltage by detecting the flyback pulse wave on the primary side of the switching transformer. When the secondary winding conducts current, LT3573 obtains output voltage information from the SW pin. At this time, the sampling circuit needs a minimum time to sample the output voltage. In order to ensure sufficient sampling time, the primary side needs to maintain a minimum inductance value LPRI. The inductance value calculation formula is as follows:
Where: toff (MIN) = 350ns, the minimum off time of the switch tube;
IMIN = 250mA, the minimum current limit of the converter.
4.2 Transformer turns ratio
Generally speaking, the transformer turns ratio is selected to maximize the output power and to give the converter sufficient current handling capability, but the turns ratio cannot be too large. For low output voltages (3.3V or 5V), the primary turns are several times the secondary turns (N:1) to maximize the transformer's current gain (and output power). At this time, the voltage at the SW pin is equal to the sum of the maximum input supply voltage plus the output voltage multiplied by the turns ratio. This value must be kept below the VSW (MAX) value of the SW pin to prevent the internal power switch from collapsing. Taking these conditions into account, for a particular application, it is necessary to set an upper limit value N for the turns ratio and select a transformer with a sufficiently low turns ratio.
Where: VSW (MAX) is the maximum voltage stress of the switch tube. According to the circuit simulation, the switch voltage stress and output current capability under different transformer turns ratios are obtained as shown in Table 1.
Table 1 Switch voltage stress and output current capability vs. turns ratio
Practical application circuit and simulation analysis The simulation experiment circuit is shown in Figure 4. With a 12V input voltage, the primary and secondary winding turns ratio of the switching transformer is set to 3:1. The RREF pin is externally connected to a reference resistor to ground, and the resistance is generally set to 6.04k. This resistance value cannot deviate too much from 6.04k. Generally, a few percent change is acceptable, otherwise it will cause a large output voltage error. RFB is the input pin of the external feedback resistor, and the resistance here is set to 80.6k. This pin is connected to the primary side of the transformer (Vsw). The ratio of this resistor to the RREF resistor determines the output voltage (plus the influence of any non-integrated transformer turns ratio). During the flyback period, the average current through this resistor is approximately 200μA. The relationship between RFB and RREF can also be determined by the following formula:
Among them: - Ic/Ie ratio of switch tube Q1, typical value is 0.986; VTC - 0.55V;
VBG—Internal bandgap reference voltage.
Figure 4 Example of actual application circuit
The Tc pin is internally connected to a positive temperature coefficient current source to the RREF pin, and the pin is externally connected to an output voltage temperature compensation resistor. The generated current is proportional to the absolute temperature. The resistance value is set to 28.7k during simulation. RILIM is the maximum current limit adjustment pin. A 10k resistor can allow the LT3573 to reach its maximum operating current capability. /UVLO is the shutdown/undervoltage lockout pin. The resistor divider connected to Vin is fixed to this pin to provide the minimum input voltage for the LT3573 to operate. When the voltage is below about 0.7V, there is almost no static current in the internal circuit. When >0.7V and 1.25V, the internal circuit will turn on and a 10μA current will be input to the SS pin.
The waveforms of each key potential of the circuit simulation are shown in Figure 5. It can be verified from the waveform that the boundary mode returns the secondary current to zero in each cycle, so that the voltage drop of the parasitic resistance will not cause load stability errors. The circuit can stably output 5V DC voltage, 0.5A DC current, and the rated power reaches 2.5W. When the input voltage is 12V, the maximum voltage stress of the switch tube Q1 is about 28V, which meets the predetermined design goals.
Figure 5 Circuit simulation key point waveform
Conclusion
The highlight of this circuit design is that it does not use optocouplers, transformers, or transformer windings. Instead, it relies on detecting the collector voltage waveform of the switching tube to stabilize the output voltage, which simplifies the peripheral circuit, avoids additional power loss in the circuit, and increases the reliability of the circuit.
Previous article:Circuit that makes digital power controllers compatible with analog controllers
Next article:Lithium-ion battery charging and discharging safety and battery detection design
Recommended ReadingLatest update time:2024-11-16 17:27
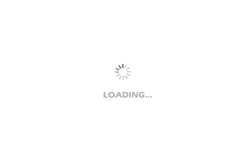
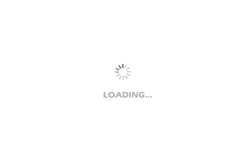
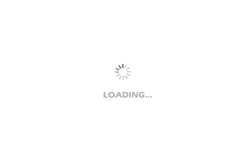
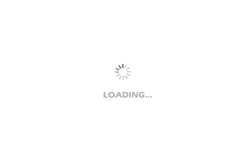
- Popular Resources
- Popular amplifiers
-
New Energy Vehicle Detection and Diagnosis Experiment (Edited by Mao Caiyun, Zhou Xien, and Long Jiwen)
-
Design of an adaptive constant on-time buck DC-DC converter with high efficiency and low power consumption
-
Research on design technology of high-efficiency step-up DC-DC converter with wide load range
-
Switching power supply design based on charge pump DC-DC converter
- MathWorks and NXP Collaborate to Launch Model-Based Design Toolbox for Battery Management Systems
- STMicroelectronics' advanced galvanically isolated gate driver STGAP3S provides flexible protection for IGBTs and SiC MOSFETs
- New diaphragm-free solid-state lithium battery technology is launched: the distance between the positive and negative electrodes is less than 0.000001 meters
- [“Source” Observe the Autumn Series] Application and testing of the next generation of semiconductor gallium oxide device photodetectors
- 采用自主设计封装,绝缘电阻显著提高!ROHM开发出更高电压xEV系统的SiC肖特基势垒二极管
- Will GaN replace SiC? PI's disruptive 1700V InnoMux2 is here to demonstrate
- From Isolation to the Third and a Half Generation: Understanding Naxinwei's Gate Driver IC in One Article
- The appeal of 48 V technology: importance, benefits and key factors in system-level applications
- Important breakthrough in recycling of used lithium-ion batteries
- Innolux's intelligent steer-by-wire solution makes cars smarter and safer
- 8051 MCU - Parity Check
- How to efficiently balance the sensitivity of tactile sensing interfaces
- What should I do if the servo motor shakes? What causes the servo motor to shake quickly?
- 【Brushless Motor】Analysis of three-phase BLDC motor and sharing of two popular development boards
- Midea Industrial Technology's subsidiaries Clou Electronics and Hekang New Energy jointly appeared at the Munich Battery Energy Storage Exhibition and Solar Energy Exhibition
- Guoxin Sichen | Application of ferroelectric memory PB85RS2MC in power battery management, with a capacity of 2M
- Analysis of common faults of frequency converter
- In a head-on competition with Qualcomm, what kind of cockpit products has Intel come up with?
- Dalian Rongke's all-vanadium liquid flow battery energy storage equipment industrialization project has entered the sprint stage before production
- Allegro MicroSystems Introduces Advanced Magnetic and Inductive Position Sensing Solutions at Electronica 2024
- Car key in the left hand, liveness detection radar in the right hand, UWB is imperative for cars!
- After a decade of rapid development, domestic CIS has entered the market
- Aegis Dagger Battery + Thor EM-i Super Hybrid, Geely New Energy has thrown out two "king bombs"
- A brief discussion on functional safety - fault, error, and failure
- In the smart car 2.0 cycle, these core industry chains are facing major opportunities!
- The United States and Japan are developing new batteries. CATL faces challenges? How should China's new energy battery industry respond?
- Murata launches high-precision 6-axis inertial sensor for automobiles
- Ford patents pre-charge alarm to help save costs and respond to emergencies
- New real-time microcontroller system from Texas Instruments enables smarter processing in automotive and industrial applications
- AD automatically adds test points
- iTOP-3399 development board Linux system modify boot LOGO
- [GD32E231 DIY Contest] 4. Simulate IIC to operate OLED
- CPU chip testing technical information
- Analysis of possible causes of I2C failure
- Pingtouge RVB2601 board-IIC bus test
- 【GD32E503 Review】 + littlegl ported to GD32E503V-EVAL
- EEWORLD University ---- Deep Learning Course (NYU, Spring 2020) Yann Lecun
- Discover the world's most in-demand medical power supplies
- Great God Tesla ~AC~