Although switching power supplies operate at frequencies far above the human hearing range, they can generate audible noise under certain load conditions. There are many possible sources for audible noise. The noise can be caused by design flaws, such as an oscillating output voltage, or by noisy components such as capacitors or transformers. In some cases, the high-pitched hum or hiss you hear may sound like a fan oscillating at an unusual frequency, or may be caused by the power supply being close to external EMI sources (fluorescent lighting or power strips).
This article will examine the most common sources of noise in flyback power supplies and describe possible solutions. All of the procedures described below can be accomplished using a programmable AC source or autotransformer and an electronic load. Keep in mind that in some cases the noise level produced by your power supply may be very low and if the power supply will be used in a sealed enclosure, then audible noise will not be a problem.
Possible Noise Sources
The most common sources of noise in flyback power supplies are noisy components. This noise is usually generated by ceramic capacitors or ferrite transformer cores. Noise in ceramic capacitors is usually caused by the reverse piezoelectric effect. When a voltage is applied to a dielectric structure, it induces mechanical stress or strain, causing the material to deform. When this material deforms, it displaces the surrounding air, generating noise.
Because the reverse piezoelectric effect occurs when large voltage swings occur, designers can focus on finding ceramic capacitors that experience high dV/dt swings. In a typical power supply, these capacitors include snubber capacitors, clamp capacitors, and ceramic output capacitors. To quickly determine if a ceramic capacitor is generating noise, replace it with a metal film capacitor of the same capacitance value and the appropriate voltage rating. If the noise level drops, you have found the source of the noise in your circuit.
If the noise source is the clamp capacitor, you can replace it completely with a metal film capacitor, or try a ceramic capacitor with a different dielectric material. Another method is to change the clamp capacitor you are using, for example, replace it with a Zener clamp circuit. If the noise problem comes from the snubber capacitor, you can replace it with a metal film capacitor, or increase the value of the series resistor to reduce the dV/dt noise on the capacitor. You can also use a ceramic capacitor with a different dielectric to see if the noise can be reduced.
Figure 1: Methods for repairing noisy clamping capacitors
Source: Power Integrations
If the noise problem is with the ceramic output capacitors, there are many different strategies that can be tried. One approach is to try switching to electrolytic capacitors or capacitors with other dielectric materials. Alternatively, the problem capacitor can be replaced with multiple ceramic capacitors in parallel. The reduction in the size of each capacitor will reduce its surface area accordingly, thus changing the mechanical resonance of the capacitor.
Managing Transformer Core Noise
On the other hand, noise generated by transformer cores is often caused by magnetostriction, which is similar to the reverse piezoelectric effect. Many ferromagnetic materials change shape when subjected to a magnetic field. As the magnetic field in the transformer core changes, these materials cause the core to physically vibrate. When the vibration frequency reaches the mechanical resonant frequency of the transformer, the vibration is amplified and causes louder audible noise. In AC electrical devices (such as transformers using a 60 Hz applied magnetic field), the maximum length change occurs twice per cycle, resulting in the familiar 120 Hz noise.
If your design exhibits this problem, make sure it is not caused by a poor design before you begin troubleshooting. First, verify that the input voltage and output load provided are within the design specifications. If the power supply is operating below the specified minimum input voltage, or above the specified output load, regulation will be lost for part of the AC cycle, which will cause increased flux in the core and generate noise.
If the input voltage and load are within specifications, next verify that the input bulk capacitors have the correct value. If the input capacitors are too small for the application, the DC bus voltage will drop significantly between AC refresh cycles, causing regulation to be lost for part of the input AC cycle.
Transformers contain many moving parts, such as coils, isolation tapes, and bobbins, which make them a common source of noise. Current in the coils generates electromagnetic fields, which generate forces that cause many transformer components to mechanically vibrate. The most effective way to reduce the physical movement of transformer components is to use bonding materials or varnishes. For example, impregnating the core with varnish is a widely used method to prevent the core from vibrating with the bobbin. Although there are many varnishing techniques available from suppliers, we recommend varnish impregnation rather than vacuum impregnation because vacuum impregnation significantly increases winding capacitance, which reduces efficiency and increases EMI.
If your design requires a long core transformer, another strategy is to use a standard core length. Long core products, such as EEL and EERL transformers, have very low mechanical resonant frequencies. This low resonant frequency tends to increase audible noise. Using a standard core length with a higher resonant frequency can alleviate this problem. However, it is important to note that if you switch to a shorter standard core, you must use a larger core size to provide adequate winding window area.
Dealing with Pulse Bunching
Pulse bundling is another potential source of noise. Pulse bundling occurs when the conduction current pulses in a design are bunched together and then skipped in greater numbers. Pulse bundling creates frequency components in the switching mode that are usually within the audible range. Pulse bundling is most common in power supplies that use on/off control.
To determine if this phenomenon exists in your design, disconnect the MOSFET drain trace and insert a current loop to monitor the switching pattern of the drain current. See www.powerint.com/sites/default/files/PIU-104_MeasuringDrainVoltageCurrent.pdf for details on how to do this.
A current probe and an oscilloscope were used to capture a set of drain switching pulses over a wide time scale while the power supply was operating under normal load. The following figure compares the waveform showing pulse bunching with the waveform with normal switching pattern. If you see pulses similar to the one on the left – a large number of pulses in a row followed by two or more skipped pulses, you may have this problem in your design.
Figure 2: Comparison of circuit waveforms with pulsed beam current (left) andnormal switching mode (right) Source: Power Integrations
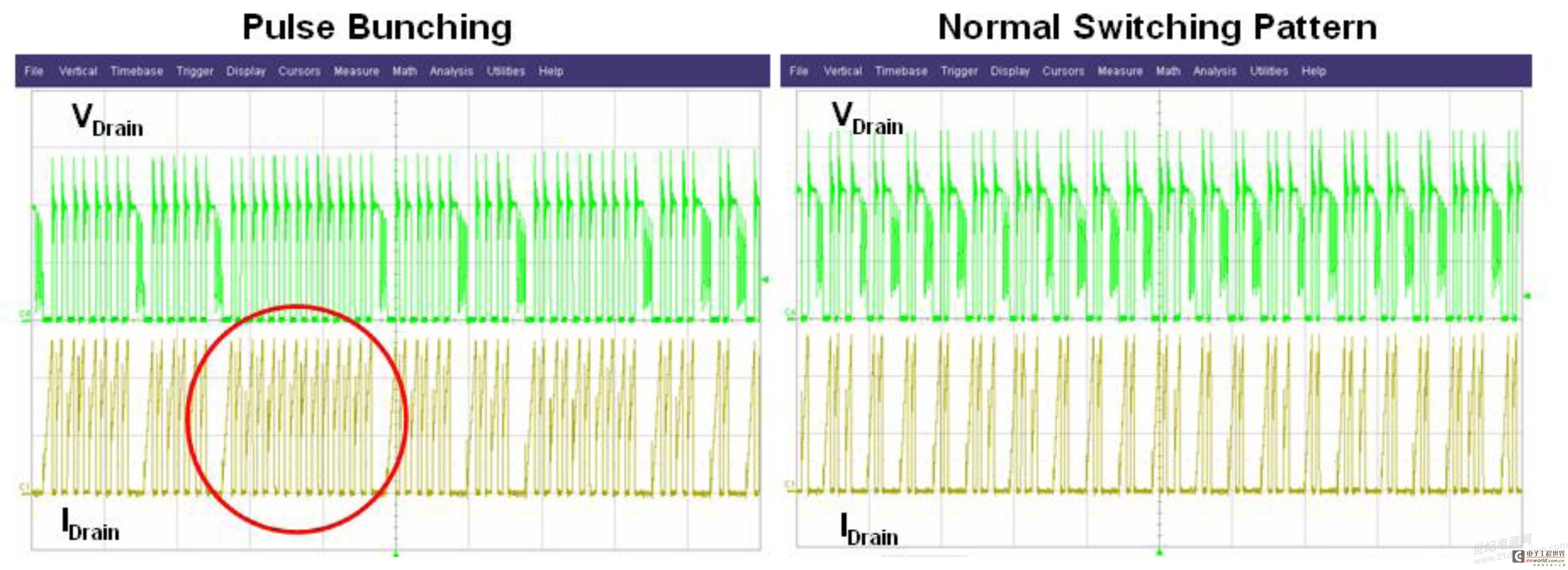
Typically, bunching indicates that the feedback circuit is too slow, causing the controller to respond slowly. To diagnose this problem, you can first confirm that all component values in the feedback circuit match the values specified in the design. One solution you can try is to use a D-type optocoupler in your design. D-type optocouplers have higher gain than standard optocouplers. Another strategy is to add a feedback loop speed-up circuit to shorten the response time. This circuit will ensure that the optocoupler transistor always operates in the active region, which prevents it from saturating and increases the response speed.
Figure 3: Feedback loop acceleration circuit Source: Power Integrations
in conclusion
Although there are many sources of audio noise in flyback power supplies, the most common culprits are often ceramic capacitors or ferrite transformer cores. If you test and find significant noise in your power supply, you can try the strategies described in this article. In most cases, you can quickly find the faulty component and solve the noise problem.
Previous article:Design bulbs suitable for all countries and regions around the world using LYTSwitch-0
Next article:LED lighting market is going to take off, reliable driver power is the key
- Popular Resources
- Popular amplifiers
- MathWorks and NXP Collaborate to Launch Model-Based Design Toolbox for Battery Management Systems
- STMicroelectronics' advanced galvanically isolated gate driver STGAP3S provides flexible protection for IGBTs and SiC MOSFETs
- New diaphragm-free solid-state lithium battery technology is launched: the distance between the positive and negative electrodes is less than 0.000001 meters
- [“Source” Observe the Autumn Series] Application and testing of the next generation of semiconductor gallium oxide device photodetectors
- 采用自主设计封装,绝缘电阻显著提高!ROHM开发出更高电压xEV系统的SiC肖特基势垒二极管
- Will GaN replace SiC? PI's disruptive 1700V InnoMux2 is here to demonstrate
- From Isolation to the Third and a Half Generation: Understanding Naxinwei's Gate Driver IC in One Article
- The appeal of 48 V technology: importance, benefits and key factors in system-level applications
- Important breakthrough in recycling of used lithium-ion batteries
- Innolux's intelligent steer-by-wire solution makes cars smarter and safer
- 8051 MCU - Parity Check
- How to efficiently balance the sensitivity of tactile sensing interfaces
- What should I do if the servo motor shakes? What causes the servo motor to shake quickly?
- 【Brushless Motor】Analysis of three-phase BLDC motor and sharing of two popular development boards
- Midea Industrial Technology's subsidiaries Clou Electronics and Hekang New Energy jointly appeared at the Munich Battery Energy Storage Exhibition and Solar Energy Exhibition
- Guoxin Sichen | Application of ferroelectric memory PB85RS2MC in power battery management, with a capacity of 2M
- Analysis of common faults of frequency converter
- In a head-on competition with Qualcomm, what kind of cockpit products has Intel come up with?
- Dalian Rongke's all-vanadium liquid flow battery energy storage equipment industrialization project has entered the sprint stage before production
- Allegro MicroSystems Introduces Advanced Magnetic and Inductive Position Sensing Solutions at Electronica 2024
- Car key in the left hand, liveness detection radar in the right hand, UWB is imperative for cars!
- After a decade of rapid development, domestic CIS has entered the market
- Aegis Dagger Battery + Thor EM-i Super Hybrid, Geely New Energy has thrown out two "king bombs"
- A brief discussion on functional safety - fault, error, and failure
- In the smart car 2.0 cycle, these core industry chains are facing major opportunities!
- The United States and Japan are developing new batteries. CATL faces challenges? How should China's new energy battery industry respond?
- Murata launches high-precision 6-axis inertial sensor for automobiles
- Ford patents pre-charge alarm to help save costs and respond to emergencies
- New real-time microcontroller system from Texas Instruments enables smarter processing in automotive and industrial applications
- I saw a beautiful PCB fish today.
- FAQ_How to calculate the response time from shutdown state to READY state
- [NXP Rapid IoT Review] Low Power Consumption Experiment & Summary
- There is something wrong with the program, please solve it
- What does the data check code mean? Can someone explain it to me?
- Supercapacitor constant power charging and voltage regulation
- EEWORLD University ---- Big Data Machine Learning (Yuan Chun)
- Boss, what's your home WIFI password? ——Qorvo~Wi-Fi 6
- When BLE meets MEMS——attitude calculation
- Lazy voice-controlled lamp based on Gizwits Cloud