The working principle and characteristics of the half-bridge LLC resonant circuit are described, and the LLC resonance is simulated with MATLAB, and its working area is analyzed. On this basis, a high-power intelligent charger is designed by using NCP1653 to provide PFC circuit, NCP1396 (voltage-controlled oscillator) to provide protection function for the circuit, and the single-chip microcomputer chip S3F84K4 to provide intelligent control for the circuit through programming. Through testing, this charger can well realize the charging function.
0 Introduction
The charger is closely related to people's daily life. The charging performance of the charger is closely related to the service life and charging efficiency of the charged battery. Due to the change of external temperature and the fluctuation of grid voltage, the stability of the charging performance of the charger is greatly reduced. This requires a self-regulating system that can respond in real time to external interference, ensure the stability of charging, and not damage the charged battery. Intelligent control can provide a good solution here. The power supply industry has begun to use intelligent control in its products, and judges overvoltage and overcurrent through single-chip microcomputer programming to provide protection for the battery. LLC resonant converters are increasingly used in chargers. The LLC resonant converter topology itself has some superior performance, which can realize zero voltage soft switching (ZVS (Zero Voltage Switch)) of the primary switch tube under full load, and the voltage stress of the secondary rectifier diode is low, so higher efficiency can be achieved under high output voltage. This makes the LLC resonant converter particularly suitable for applications with high output voltage. The future development direction of power supply is to use single-chip microcomputers to complete all functions, including: pulse width control, feedback, overvoltage and overcurrent protection, etc.
The following is a smart charger based on single-chip microcomputer designed at the request of BYD. The charger intelligently controls the charging process, and the management circuit in the system also has a protection function to prevent the battery from being damaged by overcharging and over-discharging.
1 LLC resonant converter
In the design of this charger, rectification and filtering, energy conversion, circuit protection, software design, etc. should be considered. The LLC resonant converter is the most important part of energy conversion, which is related to the performance of the charger. The following focuses on its basic structure, mathematical model and timing analysis.
1.1 Basic structure of LLC resonant converter
Figure 1 shows the schematic diagram of LLC resonant converter. Series resonant inductor Lr, series resonant capacitor Cr and parallel resonant inductor Lm form LLC resonant network, and Cr also plays a role of DC isolation [3]. At the secondary of the transformer, the rectifier diode is directly connected to the output capacitor Co.
Figure 1 Schematic diagram of LLC resonant converter
When resonance occurs, the intrinsic resonant frequency of LC is:
When Lr, Cr and Lm resonate, the intrinsic resonant frequency of LLC is:
From equations (1) and (2), it can be seen that f1 > f2. When the load RL changes, the switching frequency (Q1, Q2) can be adjusted between f1 and f2 to maximize the quality factor. Using this characteristic, the pulse frequency model (PFM) can be easily realized. The quality factor is expressed as follows: The
LLC resonant network requires two magnetic components Lr and Lm.
However, considering the actual structure of the high-frequency transformer, the magnetic components Lr and Lm can be integrated into one transformer, using the leakage inductance of the transformer as Lr and the magnetizing inductance of the transformer as Lm. In this way, the number of magnetic components can be greatly reduced. When designing, it is only necessary to focus on the leakage inductance and magnetizing inductance of the transformer. Therefore, in order to increase the leakage inductance, it is necessary to add an appropriate air gap to the transformer, and controlling the winding method of the primary and secondary sides of the transformer can improve the quality factor.
1. 2 LLC mathematical model analysis
Through the above analysis, the LLC equivalent model is obtained from the schematic diagram of the LLC resonant converter in Figure 1 as shown in Figure 2.
Figure 2 Equivalent model diagram of LLC schematic diagram The
voltage transfer function is:
Where:
Q is the quality factor.
Using MA TIAB to simulate the model, its working characteristics can be preliminarily analyzed as shown in Figure 3. Where fs is the start frequency (Start Frequency) fr is the resonant frequency (ResonantFrequency).
Figure 3 LLC resonant working characteristics.
As can be seen from Figure 3, within the entire frequency range, there are both step-down working areas (M < 1) and step-up working areas (M > 1), and this LLC resonance has a large application range. When the load is light, the operating frequency gradually increases and works in the step-down area; when the load is heavy, the operating frequency gradually decreases and works in the step-up area. As can be seen from Figure 3, the working area of the series resonance should be fs / fr > 1 in order to work in the ZVS state. Under different loads, in order to obtain the ZVS working conditions, it is sufficient to make it work on the right side of fs / fr > 1. However, LLC resonance is not limited to the area of fs / fr > 1, and can work in the area of fs / fr < 1 under certain loads. The working condition of zero voltage conversion can also be obtained. And compared with series resonance, the frequency variation range under different loads is smaller.
1.3 Timing Analysis of LLC Resonant Converter
The LLC resonant converter consists of two main switch tubes Q1 and Q2, and its driving signal is a complementary driving signal with a fixed duty cycle of 0.5. In order to ensure that the ZVS of the primary power MOS tube and the ZCS (Zero Current Switch) of the secondary diode can be achieved, when the operating frequency is f2 < f≤f1, its operating waveform is shown in Figure 4. It can be seen from the figure that the LLC converter can be divided into three working modes within half a cycle.
Mode 1 (t0-t1): Both switch tubes (Q1, Q2) are turned off, the reverse diode of Q1 is turned on for continuous current, the current on Lr gradually decreases, and the transformer generates an induced current to supply power to the load. The conduction of the reverse diode clamps the voltage across Q1 to zero.
Mode 2 (t1 - t2): The current on Lr decreases to zero at t1, Q1 is turned on at this moment, and the current on Lr increases in the reverse direction, reaches a peak value and then decreases. The current on Lm decreases first, and then increases in the reverse direction.
It can be seen that at t1, due to the clamping effect of Q1's reverse diode, the conduction voltage of Q1 is zero. In this stage, only Lr and Cr resonate.
Figure 4 Working timing waveform
Mode 3 (t2 - t3): The current on Lm is equal to the current on Lr at t2. At this time, the current flowing through the transformer is zero, and the load is isolated from the transformer. Q1 is turned off at this moment, and the reverse diode of Q2 is turned on for continuous current. In this stage, Lm is also added to the resonant part, and is connected in series with Lr and Cr to form a resonant circuit.
In the second half cycle, the operation of the circuit is just similar to the first half cycle, but in the opposite direction. The circuit working waveform of the entire cycle: in the first half cycle, the switch tube Q1 is turned on at zero voltage, and the turn-off current im of Q1 at time t3 is very small; in the second half cycle, the switch tube Q2 is turned on at zero voltage, and the turn-off current im of Q2 at time t6 is very small, so the switching loss of Q1 and Q2 when working is very small.
2 Charger hardware design
After the above analysis, the design adopts the method of current and voltage negative feedback to achieve the purpose of constant current and constant voltage charging. The charger hardware principle block diagram is shown in Figure 5.
Figure 5 Charger hardware principle block diagram
After filtering and rectification, the AC power flows to NCP1653, which provides PFC (Power Factor Correction) operation. NCP1653 is a continuous conduction (CCM) power factor correction (PFC) boost control circuit. It has a small number of peripheral components, which effectively reduces the volume of the boost inductor and the current stress of the power MOS tube, thereby reducing the cost and greatly simplifying the operation of the CCM type PFC. It also integrates a highly reliable protection function. The NCP1396 circuit provides protection for the entire hardware circuit (including feedback loop failure detection, fast and slow event input, and power supply voltage undervoltage detection to avoid working at low input voltage, etc.). The unique architecture of the NCP1396 includes a 500 kHz voltage-controlled oscillator. Since it is very important to avoid resonance spikes in the resonant circuit structure, in order to arrange the converter in the correct working area, the NCP1396 has a built-in adjustable and accurate minimum switching frequency, supported by proprietary high-voltage technology. The S3F84K4 microcontroller is used to realize intelligent charger control.
3 Software Design
In order to meet the charging requirements, the charger software design not only completes the charge and discharge control, but also has functional modules such as overcurrent protection, overvoltage protection, overtemperature protection, and short-circuit alarm. The main program flow chart is shown in Figure 6.
Figure 6 Main program flow chart.
After the program starts executing, it first initializes and detects whether the battery voltage, current, temperature and other information are normal. If normal, it goes to the next step. Otherwise, it alarms and closes the circuit. If the battery voltage is between the charge termination voltage and the discharge termination voltage, it means that the battery can be charged or discharged. At this time, the circuit will determine whether the charger or the load is connected to perform the corresponding charging and discharging. If neither is connected, the detection process will be cyclic. If the battery voltage has reached the charge termination voltage, it will wait for the load to be connected for discharge; similarly, if the battery voltage has reached the discharge termination voltage, it will wait for the charger to be connected for charging. During the whole process, the circuit will always detect the battery information in real time. If an abnormal situation occurs, it will immediately use the interrupt signal to terminate the ongoing charging or discharging process, shut down the charging and discharging circuit, and alarm and prompt the alarm reason.
4 Test results
The various indicators of this charger are as follows:
(1) Input current: 50/60 Hz.
(2) AC/DC output voltage 48: V, AC/DC output current: 5.0 A.
(3) Constant current charging current: 4.5 A.
(4) Constant voltage charging voltage: 45 V (AC).
(5) Ambient temperature: -5~45 ℃.
After analysis, according to the above design and analysis results, the parameters of LLC are finally selected as Cr = 0.043 055μF, Lr = 72.636 09μH, Lm = 435.816 5μH.
After testing, the intelligent charger has reliable charging protection measures, accurate charging status, and charging time of about 6 h. If the charging time needs to be further shortened, it is only necessary to set a larger charging current during initialization. Because the PWM controller is used, the charging efficiency can reach more than 92%, and the lowest is about 85%. According to actual needs, in order to achieve the ideal charging efficiency, further precise requirements are made on the charging device.
5 Conclusion
In the design process of the intelligent charger control system, the main focus is to ensure the precise control of the charger on the charging battery voltage. The selection of components in the design is also completed around this focus. After the actual test of the experimental circuit, the AC/DC conversion circuit is composed of the power transformer, rectifier circuit, filter circuit and voltage regulator circuit. High system accuracy can be achieved under the coordinated control of NCP1653, NCP1396 and S3F84 K4.
Reference address:Design of high-power intelligent charger based on LLC
0 Introduction
The charger is closely related to people's daily life. The charging performance of the charger is closely related to the service life and charging efficiency of the charged battery. Due to the change of external temperature and the fluctuation of grid voltage, the stability of the charging performance of the charger is greatly reduced. This requires a self-regulating system that can respond in real time to external interference, ensure the stability of charging, and not damage the charged battery. Intelligent control can provide a good solution here. The power supply industry has begun to use intelligent control in its products, and judges overvoltage and overcurrent through single-chip microcomputer programming to provide protection for the battery. LLC resonant converters are increasingly used in chargers. The LLC resonant converter topology itself has some superior performance, which can realize zero voltage soft switching (ZVS (Zero Voltage Switch)) of the primary switch tube under full load, and the voltage stress of the secondary rectifier diode is low, so higher efficiency can be achieved under high output voltage. This makes the LLC resonant converter particularly suitable for applications with high output voltage. The future development direction of power supply is to use single-chip microcomputers to complete all functions, including: pulse width control, feedback, overvoltage and overcurrent protection, etc.
The following is a smart charger based on single-chip microcomputer designed at the request of BYD. The charger intelligently controls the charging process, and the management circuit in the system also has a protection function to prevent the battery from being damaged by overcharging and over-discharging.
1 LLC resonant converter
In the design of this charger, rectification and filtering, energy conversion, circuit protection, software design, etc. should be considered. The LLC resonant converter is the most important part of energy conversion, which is related to the performance of the charger. The following focuses on its basic structure, mathematical model and timing analysis.
1.1 Basic structure of LLC resonant converter
Figure 1 shows the schematic diagram of LLC resonant converter. Series resonant inductor Lr, series resonant capacitor Cr and parallel resonant inductor Lm form LLC resonant network, and Cr also plays a role of DC isolation [3]. At the secondary of the transformer, the rectifier diode is directly connected to the output capacitor Co.
Figure 1 Schematic diagram of LLC resonant converter
When resonance occurs, the intrinsic resonant frequency of LC is:
When Lr, Cr and Lm resonate, the intrinsic resonant frequency of LLC is:
From equations (1) and (2), it can be seen that f1 > f2. When the load RL changes, the switching frequency (Q1, Q2) can be adjusted between f1 and f2 to maximize the quality factor. Using this characteristic, the pulse frequency model (PFM) can be easily realized. The quality factor is expressed as follows: The
LLC resonant network requires two magnetic components Lr and Lm.
However, considering the actual structure of the high-frequency transformer, the magnetic components Lr and Lm can be integrated into one transformer, using the leakage inductance of the transformer as Lr and the magnetizing inductance of the transformer as Lm. In this way, the number of magnetic components can be greatly reduced. When designing, it is only necessary to focus on the leakage inductance and magnetizing inductance of the transformer. Therefore, in order to increase the leakage inductance, it is necessary to add an appropriate air gap to the transformer, and controlling the winding method of the primary and secondary sides of the transformer can improve the quality factor.
1. 2 LLC mathematical model analysis
Through the above analysis, the LLC equivalent model is obtained from the schematic diagram of the LLC resonant converter in Figure 1 as shown in Figure 2.
Figure 2 Equivalent model diagram of LLC schematic diagram The
voltage transfer function is:
Where:
Q is the quality factor.
Using MA TIAB to simulate the model, its working characteristics can be preliminarily analyzed as shown in Figure 3. Where fs is the start frequency (Start Frequency) fr is the resonant frequency (ResonantFrequency).
Figure 3 LLC resonant working characteristics.
As can be seen from Figure 3, within the entire frequency range, there are both step-down working areas (M < 1) and step-up working areas (M > 1), and this LLC resonance has a large application range. When the load is light, the operating frequency gradually increases and works in the step-down area; when the load is heavy, the operating frequency gradually decreases and works in the step-up area. As can be seen from Figure 3, the working area of the series resonance should be fs / fr > 1 in order to work in the ZVS state. Under different loads, in order to obtain the ZVS working conditions, it is sufficient to make it work on the right side of fs / fr > 1. However, LLC resonance is not limited to the area of fs / fr > 1, and can work in the area of fs / fr < 1 under certain loads. The working condition of zero voltage conversion can also be obtained. And compared with series resonance, the frequency variation range under different loads is smaller.
1.3 Timing Analysis of LLC Resonant Converter
The LLC resonant converter consists of two main switch tubes Q1 and Q2, and its driving signal is a complementary driving signal with a fixed duty cycle of 0.5. In order to ensure that the ZVS of the primary power MOS tube and the ZCS (Zero Current Switch) of the secondary diode can be achieved, when the operating frequency is f2 < f≤f1, its operating waveform is shown in Figure 4. It can be seen from the figure that the LLC converter can be divided into three working modes within half a cycle.
Mode 1 (t0-t1): Both switch tubes (Q1, Q2) are turned off, the reverse diode of Q1 is turned on for continuous current, the current on Lr gradually decreases, and the transformer generates an induced current to supply power to the load. The conduction of the reverse diode clamps the voltage across Q1 to zero.
Mode 2 (t1 - t2): The current on Lr decreases to zero at t1, Q1 is turned on at this moment, and the current on Lr increases in the reverse direction, reaches a peak value and then decreases. The current on Lm decreases first, and then increases in the reverse direction.
It can be seen that at t1, due to the clamping effect of Q1's reverse diode, the conduction voltage of Q1 is zero. In this stage, only Lr and Cr resonate.
Figure 4 Working timing waveform
Mode 3 (t2 - t3): The current on Lm is equal to the current on Lr at t2. At this time, the current flowing through the transformer is zero, and the load is isolated from the transformer. Q1 is turned off at this moment, and the reverse diode of Q2 is turned on for continuous current. In this stage, Lm is also added to the resonant part, and is connected in series with Lr and Cr to form a resonant circuit.
In the second half cycle, the operation of the circuit is just similar to the first half cycle, but in the opposite direction. The circuit working waveform of the entire cycle: in the first half cycle, the switch tube Q1 is turned on at zero voltage, and the turn-off current im of Q1 at time t3 is very small; in the second half cycle, the switch tube Q2 is turned on at zero voltage, and the turn-off current im of Q2 at time t6 is very small, so the switching loss of Q1 and Q2 when working is very small.
2 Charger hardware design
After the above analysis, the design adopts the method of current and voltage negative feedback to achieve the purpose of constant current and constant voltage charging. The charger hardware principle block diagram is shown in Figure 5.
Figure 5 Charger hardware principle block diagram
After filtering and rectification, the AC power flows to NCP1653, which provides PFC (Power Factor Correction) operation. NCP1653 is a continuous conduction (CCM) power factor correction (PFC) boost control circuit. It has a small number of peripheral components, which effectively reduces the volume of the boost inductor and the current stress of the power MOS tube, thereby reducing the cost and greatly simplifying the operation of the CCM type PFC. It also integrates a highly reliable protection function. The NCP1396 circuit provides protection for the entire hardware circuit (including feedback loop failure detection, fast and slow event input, and power supply voltage undervoltage detection to avoid working at low input voltage, etc.). The unique architecture of the NCP1396 includes a 500 kHz voltage-controlled oscillator. Since it is very important to avoid resonance spikes in the resonant circuit structure, in order to arrange the converter in the correct working area, the NCP1396 has a built-in adjustable and accurate minimum switching frequency, supported by proprietary high-voltage technology. The S3F84K4 microcontroller is used to realize intelligent charger control.
3 Software Design
In order to meet the charging requirements, the charger software design not only completes the charge and discharge control, but also has functional modules such as overcurrent protection, overvoltage protection, overtemperature protection, and short-circuit alarm. The main program flow chart is shown in Figure 6.
Figure 6 Main program flow chart.
After the program starts executing, it first initializes and detects whether the battery voltage, current, temperature and other information are normal. If normal, it goes to the next step. Otherwise, it alarms and closes the circuit. If the battery voltage is between the charge termination voltage and the discharge termination voltage, it means that the battery can be charged or discharged. At this time, the circuit will determine whether the charger or the load is connected to perform the corresponding charging and discharging. If neither is connected, the detection process will be cyclic. If the battery voltage has reached the charge termination voltage, it will wait for the load to be connected for discharge; similarly, if the battery voltage has reached the discharge termination voltage, it will wait for the charger to be connected for charging. During the whole process, the circuit will always detect the battery information in real time. If an abnormal situation occurs, it will immediately use the interrupt signal to terminate the ongoing charging or discharging process, shut down the charging and discharging circuit, and alarm and prompt the alarm reason.
4 Test results
The various indicators of this charger are as follows:
(1) Input current: 50/60 Hz.
(2) AC/DC output voltage 48: V, AC/DC output current: 5.0 A.
(3) Constant current charging current: 4.5 A.
(4) Constant voltage charging voltage: 45 V (AC).
(5) Ambient temperature: -5~45 ℃.
After analysis, according to the above design and analysis results, the parameters of LLC are finally selected as Cr = 0.043 055μF, Lr = 72.636 09μH, Lm = 435.816 5μH.
After testing, the intelligent charger has reliable charging protection measures, accurate charging status, and charging time of about 6 h. If the charging time needs to be further shortened, it is only necessary to set a larger charging current during initialization. Because the PWM controller is used, the charging efficiency can reach more than 92%, and the lowest is about 85%. According to actual needs, in order to achieve the ideal charging efficiency, further precise requirements are made on the charging device.
5 Conclusion
In the design process of the intelligent charger control system, the main focus is to ensure the precise control of the charger on the charging battery voltage. The selection of components in the design is also completed around this focus. After the actual test of the experimental circuit, the AC/DC conversion circuit is composed of the power transformer, rectifier circuit, filter circuit and voltage regulator circuit. High system accuracy can be achieved under the coordinated control of NCP1653, NCP1396 and S3F84 K4.
Previous article:Design of solar street light controller based on lithium polymer battery
Next article:Design principle and production process of lithium-ion battery repair instrument
Recommended ReadingLatest update time:2024-11-16 18:03
Research on the design of charger for new energy vehicles based on three-level LLC resonant converter
Abstract: The on-board charger is the core part of the power unit of new energy vehicles and is also a device connected to the grid voltage. High efficiency, high power factor and small size are its necessary functions. In order to achieve high efficiency and wide output voltage range adjustment, the DC/DC conversion
[Automotive Electronics]
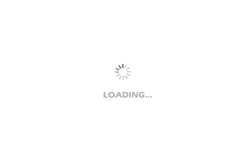
- Popular Resources
- Popular amplifiers
-
A high efficiency half-bridge LLC AC-DC converter design
-
Spread spectrum modulation suppresses conducted interference of LLC switching power supply_Geng Yanqing
-
Design of switching power supply based on dual-transformer LLC resonant converter
-
A review of switching power supply optimization methods based on LLC resonant converter
Recommended Content
Latest Power Management Articles
- MathWorks and NXP Collaborate to Launch Model-Based Design Toolbox for Battery Management Systems
- STMicroelectronics' advanced galvanically isolated gate driver STGAP3S provides flexible protection for IGBTs and SiC MOSFETs
- New diaphragm-free solid-state lithium battery technology is launched: the distance between the positive and negative electrodes is less than 0.000001 meters
- [“Source” Observe the Autumn Series] Application and testing of the next generation of semiconductor gallium oxide device photodetectors
- 采用自主设计封装,绝缘电阻显著提高!ROHM开发出更高电压xEV系统的SiC肖特基势垒二极管
- Will GaN replace SiC? PI's disruptive 1700V InnoMux2 is here to demonstrate
- From Isolation to the Third and a Half Generation: Understanding Naxinwei's Gate Driver IC in One Article
- The appeal of 48 V technology: importance, benefits and key factors in system-level applications
- Important breakthrough in recycling of used lithium-ion batteries
MoreSelected Circuit Diagrams
MorePopular Articles
- Innolux's intelligent steer-by-wire solution makes cars smarter and safer
- 8051 MCU - Parity Check
- How to efficiently balance the sensitivity of tactile sensing interfaces
- What should I do if the servo motor shakes? What causes the servo motor to shake quickly?
- 【Brushless Motor】Analysis of three-phase BLDC motor and sharing of two popular development boards
- Midea Industrial Technology's subsidiaries Clou Electronics and Hekang New Energy jointly appeared at the Munich Battery Energy Storage Exhibition and Solar Energy Exhibition
- Guoxin Sichen | Application of ferroelectric memory PB85RS2MC in power battery management, with a capacity of 2M
- Analysis of common faults of frequency converter
- In a head-on competition with Qualcomm, what kind of cockpit products has Intel come up with?
- Dalian Rongke's all-vanadium liquid flow battery energy storage equipment industrialization project has entered the sprint stage before production
MoreDaily News
- Allegro MicroSystems Introduces Advanced Magnetic and Inductive Position Sensing Solutions at Electronica 2024
- Car key in the left hand, liveness detection radar in the right hand, UWB is imperative for cars!
- After a decade of rapid development, domestic CIS has entered the market
- Aegis Dagger Battery + Thor EM-i Super Hybrid, Geely New Energy has thrown out two "king bombs"
- A brief discussion on functional safety - fault, error, and failure
- In the smart car 2.0 cycle, these core industry chains are facing major opportunities!
- The United States and Japan are developing new batteries. CATL faces challenges? How should China's new energy battery industry respond?
- Murata launches high-precision 6-axis inertial sensor for automobiles
- Ford patents pre-charge alarm to help save costs and respond to emergencies
- New real-time microcontroller system from Texas Instruments enables smarter processing in automotive and industrial applications
Guess you like
- Several interesting GIF animations
- Several issues on the second-order low-pass filter circuit of voltage-controlled voltage source
- EEWORLD University Hall----Live Replay: Application of TI Precision ADC in Transmitter
- 【TI recommended course】#What is I2C design tool? #
- BQ40Z50-R2 security mode introduction and password modification method
- [NUCLEO-L552ZE Review] Expansion board ws2812 power supply correction
- Don't stop me, I want to do mpy development!
- TPS23861 48V power supply has a small probability of burning out.
- Free resource download | Five trends driving change in power management
- My Journey of MCU Development (Part 2)