Key points of LED car headlight designLED
has been widely used in cars. Choose appropriate LED products according to different performance requirements. In addition to the appearance, LED also has different performance output and light output compared to traditional light sources. When used in headlights, it will face design concepts such as optical design and heat dissipation design that are different from traditional lamps. However, due to its characteristics that are different from traditional light sources, when it is successfully integrated with the car body and overcomes technical difficulties, it will create a brand-new design concept for the car model.
LEDs in cars
LEDs have been widely used in related lighting or indicator light sources inside the car. As shown in Figure 1, LED related applications can be seen in the dashboard lights, roof lights, makeup lights, welcome lights, etc. inside the car, as well as the taillights, front and rear turn signals, reversing lights, third brake lights, etc. outside the car.
Figure 1 Application of LED in cars
From the application history of LED, as early as 1992, there was a precedent of LED being used in the third brake light; in 2000, it was further applied to taillights, turn signals and brake lights; in 2002, Audi A8 took the lead in placing LED light sources in the front lamps as daytime running lights, opening up the imagination of designers and engineers in front lamps. Concept cars using LED as headlight sources can be seen at many international auto shows, as shown in Figure 2.
Figure 2 LED headlight concept car
LED has the inherent advantage of small size. When used in front lamps, it can reduce the size of the entire lamp set, further giving up valuable engine space and other related equipment. The total length of the lamp designed with existing halogen bulbs or discharge bulbs is about 300mm, while in the design of many concept cars, LED lamps are only 125mm long. And with the advantage of small size, it can be combined with a variety of different design styles to create different visual perceptions for the body shape, breaking away from the round design of traditional lamps.
LED packaging applications for different needs
With different application levels, car manufacturers also choose different LED light source packages to correspond to different environmental requirements. According to the required brightness, they can be simply divided into three different needs: indication, lighting and projection. Indication light sources can be seen in third brake lights, taillight groups (taillights, brake lights, turn signals, etc.), side lights, etc. The light source output lumen value is low, and the required power is low, about 70mW~200mW. The heat generated has little effect on the package body, so the impact of this heat will be ignored in the package, and the whole is directly wrapped with resin materials for packaging. Because the thermal conductivity coefficient of resin is low (W/mK), its related thermal resistance will increase to 50~200K/W due to the difficulty of heat dissipation; and the packaging power of the lighting light source will be relatively higher. In addition to being used in indication light source products, it can also be used for brightness. The daytime running lights, fog lights, front turn lights, etc. require higher brightness, but because of the increased power loss (power is about 1~5W), the heat dissipation part cannot ignore the heat dissipation problem like the indicator light source. In addition to the resin material packaging, metal blocks must be used to conduct heat to maintain the light output efficiency, and its thermal resistance is maintained below 15K/W; the projection light source has the highest demand for light source packaging brightness, and its application products are mainly front lighting systems (high lights, low lights, fog lights, etc.). Its single package must be above 4W, and the thermal resistance must be less than 5K/W to ensure that the heat dissipation capacity can be maintained under the high temperature of the engine room and keep the light source output efficiency within the usable range.
Different application levels have different total brightness requirements. For interior lighting, about 80 lumens are required. Generally, surface mount (SMT) packaging is used. The output of a single package is about 2 lumens, and the efficiency can reach 15~20lm/W. For the third brake light, about 30lm is required. Generally, a shell-shaped packaging structure (φ=5mm) is used. The brightness of a single package is about 4 lumens, and the efficiency can reach 20~40lm/W.
The brightness requirement of the taillight group is about 300~500lm. Generally, a 1W SMT packaging structure is used. The brightness of a single package is about 10~20lm, and the efficiency can reach 15~40lm/W. All of the above are light sources that have been applied to the car body. Currently, LED manufacturers and car manufacturers are actively cooperating to try to introduce LED into the front lighting system (headlights, fog lights). The brightness of the headlights required by car manufacturers is about 2000 lumens of white light. LED manufacturers currently use high-wattage SMT LED packaging structure. Each single package can output 100~200lm, and the efficiency is expected to increase to 50~100lm/W.
The light sources currently used in cars can be divided into incandescent bulbs, halogen bulbs, gas discharge bulbs and LED light sources. The comparison is shown in Figure 4.
LED in headlight design
Before starting to design headlights, you should first consider the relevant regulations, including light type brightness, environmental testing, brightness attenuation and other requirements, and further consider the relevant optical design, mechanism design, heat resistance design and electronic control design. For LEDs, in addition to the reflector design, the optical design also needs to consider the light type of the LED itself. Different packaging types will produce different light outputs, which will further affect the requirements of the reflector or imaging transmission, similar to the need to consider different bulbs (H1, H4, H7, H11, etc.) in traditional headlight design. In traditional headlight design, the photon release of the bulb itself comes from the heated tungsten filament, and the brightness output will not be affected by the heat emitted by the bulb itself or the high temperature from the engine compartment. The focus of heat dissipation is on the uniform temperature design of the entire headlight cavity rather than the heat dissipation of the bulb. However, when choosing headlight materials, it is necessary to consider whether they can withstand the high temperature from the bulb (the headlight cavity can withstand a temperature of about 100°C, and the temperature in the fog lamp cavity can be as high as 300°C), so the materials selected here are generally heat-resistant materials. However, for LEDs, their photon release comes from the energy level jump of the PN interface, which is negatively correlated with temperature. The higher the temperature, the weaker the light source output. Therefore, heat dissipation becomes an important issue in the design of LEDs as light sources.
Figure 5 Low beam headlight pattern in EU regulations
When designing optics, we first consider the regulatory requirements and discuss the relationship between viewing angle and intensity. For example, the low beam must be designed for its special 15-degree elevation angle, as shown in Figure 5. In traditional lamp design, the angle and intensity are controlled by using a reflector with lens engravings in the early stage, and then the intensity angle is directly controlled by using a reflector. The fisheye lens design method using imaging has also been developed. Regardless of the design method, the characteristics of the selected light source must be considered first, especially the angle and intensity of the beam output (Beam pattern). For traditional light sources, most of them are columnar light sources, which can produce a butterfly-shaped beam output, and then develop lenses, reflectors, baffles, lenses and other optical components to match them. When designing lamps using LEDs as light sources, it is necessary to reconsider their optical characteristics from traditional columnar light sources to planar light sources (different packaging designs have different light output patterns), and then match external optical components to produce different combinations for different products. According to the design classification of German car lamp manufacturer HELLA, light sources can be divided into eight categories, as shown in Figure 6. The current unit area luminescence of LED is not as good as that of halogen bulbs and discharge bulbs. To obtain the same lumen output, LED requires a larger packaging area. As the output area of the light source increases, the difficulty of optical design also increases. Therefore, in existing concept cars, modular optical design replaces the existing single lamp room design, using multiple sets of light sources to achieve the lighting level of traditional lamps. In addition to reducing the difficulty of optical design, it also increases the design sense of the body shape.
Figure 6 Headlight design related technologies
Figure 7 LED light source design
Heat dissipation design is one of the issues that distinguish LED light sources from traditional light sources. Traditional lamps generate much more heat than LEDs, but traditional lamps will not reduce their light output capacity due to high temperature, but the light output of LEDs will decrease as the temperature of their own junction (PN interface) increases, as shown in Figure 8. How the heat generated is dissipated to the external environment is closely related to its packaging structure material, involving the heat dissipation material used and the related appearance, as shown in Figure 9. The concept of thermal resistance represents how many K temperatures need to be increased to dissipate heat when the input power is W. With the existing packaging technology, the maximum allowable LED operation temperature is 185℃ (Lumiled K2), but generally due to the packaging glue, the allowable operating temperature is about 125℃. In addition to considering the light source output efficiency, the deterioration of the packaging glue is also considered (resin materials will age at high temperatures).
Figure 8 Effect of interface temperature on light output
The temperature of the engine room can reach up to 85℃ near the lamp. When used with Lumiled K2, there is a 100℃ heat dissipation space, but when used with ordinary LEDs, there is only a 40℃ heat dissipation space. Observing the relevant thermal resistance, R_Junction-Slug and R_Slug-Board are both determined by the package. For designers, they can only work on R_Board-Ambient, including how to fix the package on the heat dissipation substrate (attachment quality), heat dissipation structure appearance design, active and passive heat dissipation considerations and external environment conditions. Therefore, relevant simulation design should be carried out with the mechanism here, and the required heat dissipation mode should be considered after obtaining the flow field and temperature conditions of the lamp in the engine room. If passive heat dissipation is selected, a larger heat dissipation space is required, which is a considerable burden on the engine. If active heat dissipation is selected, although the required heat dissipation environment is smaller, because of the addition of moving parts such as fans, it is necessary to consider whether this moving part can pass the relevant regulations on car lights, including harsh environments such as vibration, dust, corrosion and moisture.
Figure 9 Relationship between package and heat dissipation thermal resistance
Difficulties encountered in the application of LED in headlights
LED is applied to headlights. At many auto shows, various car manufacturers have displayed related concept cars, but no finished products have been seen in the headlight part. There are still many problems to be solved. The main problems should be brightness output, heat dissipation and error design.
The brightness of the headlight requires 900 lumens for the low beam and 1100 lumens for the high beam, with an overall requirement of 2000 lumens, which is about the total light source output of 40 1W packaged Luxeon emitters produced by Lumiled at 25℃. However, when the external temperature rises to 50℃, its efficiency will drop below 80%, and its light source output area is about 90_2 (about 13_2 for gas discharge bulbs), and the design difficulty will also increase accordingly.
In the LED industry, the so-called classified sales process has been developed to deal with the unevenness of chips caused by epitaxy. In particular, high-wattage chips are fully inspected and shipped in the LED industry, and are classified according to wavelength brightness. Therefore, there are slight differences between the encapsulated individuals. This difference may exist in brightness, color temperature or reliability. However, when LEDs are used in headlights, it is inevitable to use multiple chips to output sufficient brightness for optical design. At this time, special attention must be paid to the LED quality inspection and quality control to ensure the same quality of light source output.
Conclusion
Since 2003, more than 13 automakers have exhibited concept cars featuring LED headlights at relevant auto shows. For example, Lexus announced that it will launch a mass-produced car with LED headlights in mid-2007. I believe that the engineering problems related to LEDs will be solved one by one under the eager expectations of consumers, so let us wait and see.
Previous article:Driving high-brightness LEDs for lighting
Next article:LED knowledge encyclopedia (principle, classification and LED characteristics table)
Recommended ReadingLatest update time:2024-11-16 21:40
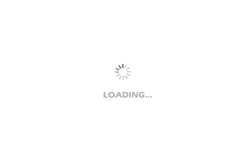
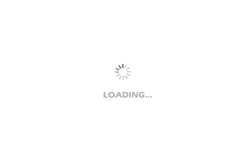
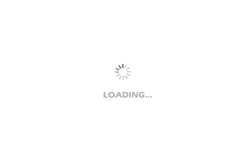
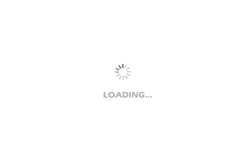
- Popular Resources
- Popular amplifiers
- MathWorks and NXP Collaborate to Launch Model-Based Design Toolbox for Battery Management Systems
- STMicroelectronics' advanced galvanically isolated gate driver STGAP3S provides flexible protection for IGBTs and SiC MOSFETs
- New diaphragm-free solid-state lithium battery technology is launched: the distance between the positive and negative electrodes is less than 0.000001 meters
- [“Source” Observe the Autumn Series] Application and testing of the next generation of semiconductor gallium oxide device photodetectors
- 采用自主设计封装,绝缘电阻显著提高!ROHM开发出更高电压xEV系统的SiC肖特基势垒二极管
- Will GaN replace SiC? PI's disruptive 1700V InnoMux2 is here to demonstrate
- From Isolation to the Third and a Half Generation: Understanding Naxinwei's Gate Driver IC in One Article
- The appeal of 48 V technology: importance, benefits and key factors in system-level applications
- Important breakthrough in recycling of used lithium-ion batteries
- Innolux's intelligent steer-by-wire solution makes cars smarter and safer
- 8051 MCU - Parity Check
- How to efficiently balance the sensitivity of tactile sensing interfaces
- What should I do if the servo motor shakes? What causes the servo motor to shake quickly?
- 【Brushless Motor】Analysis of three-phase BLDC motor and sharing of two popular development boards
- Midea Industrial Technology's subsidiaries Clou Electronics and Hekang New Energy jointly appeared at the Munich Battery Energy Storage Exhibition and Solar Energy Exhibition
- Guoxin Sichen | Application of ferroelectric memory PB85RS2MC in power battery management, with a capacity of 2M
- Analysis of common faults of frequency converter
- In a head-on competition with Qualcomm, what kind of cockpit products has Intel come up with?
- Dalian Rongke's all-vanadium liquid flow battery energy storage equipment industrialization project has entered the sprint stage before production
- Allegro MicroSystems Introduces Advanced Magnetic and Inductive Position Sensing Solutions at Electronica 2024
- Car key in the left hand, liveness detection radar in the right hand, UWB is imperative for cars!
- After a decade of rapid development, domestic CIS has entered the market
- Aegis Dagger Battery + Thor EM-i Super Hybrid, Geely New Energy has thrown out two "king bombs"
- A brief discussion on functional safety - fault, error, and failure
- In the smart car 2.0 cycle, these core industry chains are facing major opportunities!
- The United States and Japan are developing new batteries. CATL faces challenges? How should China's new energy battery industry respond?
- Murata launches high-precision 6-axis inertial sensor for automobiles
- Ford patents pre-charge alarm to help save costs and respond to emergencies
- New real-time microcontroller system from Texas Instruments enables smarter processing in automotive and industrial applications
- The GD32450I-EVAL you want~ Unboxing and pictures~~~
- Hybrid beamforming: the new main force of future 5G construction
- Circuit board anti-tampering silk screen, do you use it in circuit design?
- EEWORLD University ---- Electrical Engineering
- F28002x write OTP Error
- Activity award question
- 【Silicon Labs BG22-EK4108A Bluetooth Development Review】Three-point light program development steps
- 【ESP32-C3-DevKitM-1】Hardware SPI+0.96-inch OLED
- Definition of various data types in TI DSP
- TI eSports training video recommendation