Based on the design requirements and functions, this paper designs a battery management system for hybrid electric vehicles. The hardware
system includes: power module, single cell voltage acquisition circuit and I2C communication circuit based on OZ890, RS232
serial communication and CAN communication based on DSP, etc. The software system includes: using periodic interrupts and underflow interrupts to realize data
acquisition and processing, SOC estimation and various communication programs.
Keywords: battery management system; OZ890; I2C bidirectional isolation; underflow interrupt
Document code: TM912.2 Document identifier: A Article number:
Design of battery management system based on DSP and OZ890
WANG Tao, QI Bo-jin, WU Hong-jie, LI Wei(School of Mechanical Engineering & Automation, Beihang University, Beijing 100191, China)
Abstract: A battery management system for Hybrid Electrical Vehicle is designed according to its design requirements and functions. The design of BMS contains two parts: hardware system and software system. The hardware system comprises power module, data acquisition and communication circuit, I2C bus circuit, CAN bus circuit, RS232 circuit and so on. The software
comprises data acquisition and processing program based on periodic interrupt and underflow interrupt, evaluation of SOC and communication programs.
Key words: battery management system; OZ890; Dual I2C Isolator; underflow interrupt
Battery Management System (BMS) is one of the key components of electric vehicles. A high-
performance and high-reliability battery management system can enable the battery to achieve optimal performance under various working conditions. The battery management system
can monitor the battery status in real time, such as battery voltage, charge and discharge current, operating temperature, etc.; predict the battery state of charge (SOC
) to prevent the battery from being overcharged or over-discharged, thereby improving the battery performance and life, and improving
the reliability and safety of hybrid vehicles.
This design mainly realizes functions such as data acquisition, battery status calculation, balancing control, thermal management, various communications, and fault diagnosis
.
1 Hardware composition of battery management system The
battery management system circuit consists of a power module, a DSP chip
TMS320LF2407
A[1] (abbreviated as "LF2407"),
a data acquisition module based on multiple OZ890[2], an I2C[3] communication module, an SCI communication module, and a CAN communication module.
The system hardware block diagram is shown in Figure 1.
1.1 Power module
The power supply provided by the vehicle is +12V. The voltages required by the management system include: +3.3V (DSP, isolation circuit), +5V (bus
driver and other chips), ±15V (current sensor), which can be obtained through DC-DC conversion. This can not only meet
the power supply requirements of each chip but also play an isolation and anti-interference role.
1.2 Data acquisition module
The DSP completes the acquisition of total voltage, current and temperature. The OZ890 chip completes the acquisition and balancing of the battery cell voltage
and sends it to the DSP via the I2C bus. The circuit of this module mainly includes the front-end acquisition processing and balancing circuit.
1.3 I2C communication module
The OZ890 sampling module sends the collected and processed data to the LF2407 via the I2C bus. Since the LF2407 itself does not
have an I2C interface, this design uses PCA9564[4] to expand its I2C interface. In order to prevent electromagnetic interference from affecting
the transmission of data on the I2C bus, the bus signal must be isolated. Considering that the I2C bus is bidirectional, the ADuM1250 bidirectional isolation chip is used for isolation. The PCA9564 and the bidirectional isolation circuit are shown in Figure 2.
Figure 2 PCA9564 and bidirectional isolation circuit
PCA9564 is an I2C bus expander, connected to the GPIO port of LF2407, it supports data transmission and reception in master-slave mode,
LF2407 is set as the master device in BMS, and OZ890 is set as the slave device. LF2407
communicates with OZ890 by reading and writing the contents of four registers inside PCA9564.
ADuM1250 is a hot-swappable digital isolator, which contains a non-latching, bidirectional communication channel compatible with the I2C interface. In this way,
there is no need to divide the I2C signal into a transmission signal and a reception signal for use by a separate optocoupler.
1.4 Serial communication module
The battery management system sends the collected and processed data to the PC interface through the serial port to realize human-computer interaction. Through
the serial port interface, the total voltage, single cell voltage, current, SOC, fault status, charge and discharge power and other parameters of the battery can be observed
, and the online calibration of the management system can also be realized through the serial port. Its hardware circuit is mainly based on MAX232 chip,
as shown in Figure 3a).
Figure 3 Serial communication interface circuit
MAX232 is a +5V power transceiver, connected to the computer serial port, to achieve RS-232 interface signal and TTL signal
level conversion, so that BMS and PC can perform asynchronous serial communication.
In order to prevent electromagnetic interference from affecting the transmission of data on the serial port, the bus signal must be isolated. The serial port is a one-way transmission,
so it is more convenient to use 6N137 photoelectric coupling. Figure 3b) shows the 232TXD signal photocoupler isolation circuit.
1.5 CAN communication module
CAN communication is an information bridge between the battery management system (BMS) and the vehicle HCU. The BMS sends the battery status
parameters to the HCU through the CAN bus. The HCU makes decisions by judging the current battery status, allocates
power between the motor and the engine, and controls the charging and discharging of the battery. At the same time, the BMS can also receive relevant commands sent by the HCU and make
corresponding processing. The hardware mainly uses the PCA82C250 universal CAN transceiver to provide
differential transmission capability for bus data and differential reception capability for communication bus data. The anti-interference capability of the CAN bus is enhanced through an optical coupling isolation circuit similar to Figure 3b)
. The hardware circuit is shown in Figure 4.
Figure 4 CAN communication interface circuit
In the circuit, whether to connect a 120Ω terminal resistor can be determined according to the requirements of the vehicle. When the JP201 jumper is connected to pins 1 and 2,
the resistor is not connected. When it is connected to pins 2 and 3, the resistor is connected.
2 Software design of battery management system
The battery management system software [6] system includes 6 tasks and 5 interrupts. The 6 tasks include: AD conversion processing task
(including reading data from OZ890), CAN receiving task, CAN sending task, SOC calculation task, system monitoring
fault diagnosis task and serial port sending task. The 5 interrupts include: AD acquisition interrupt service subroutine, Timer1 underflow interrupt
service subroutine, periodic interrupt subroutine, CAN bus receiving interrupt service subroutine and serial port receiving interrupt service subroutine,
as shown in the interrupt vector table below:
.ref _c_int0
.ref _ADC, _INT2, _INT5
.sect ".vectors"
rset: B _c_int0;00h reset
int1: B ADC ;02h ADC
int2: B _INT2 ;04h cycle, underflow interrupt
int3: B int3 ;06h INT3
int4: B int4 ;08h INT4
int5: B _INT5 ;0Ah CAN, SCI
int6: B int6 ;0Ch INT6
According to the vehicle control strategy, the refresh period of each frame of battery status data on CAN is 10ms, so
the clock beat of the periodic interrupt is set to 10ms; accordingly, the execution period of the above tasks is set to 10ms.
Figure 5 Cycle clock beat diagram
As can be seen from Figure 5, after the system initialization is completed, Time1 starts timing. When it reaches 5ms,
a cycle interrupt occurs at point A, and then the cycle interrupt subroutine is entered to start AD conversion and read the data in OZ890 through the I2C bus
. After the AD conversion is completed, the software triggers the ADC interrupt to save the data and perform corresponding processing, and clears the cycle interrupt flag
. When it reaches 10ms, an underflow interrupt occurs, and the underflow interrupt service subroutine is entered to execute the CAN sending task, SOC
calculation task, system monitoring fault diagnosis task, and serial port sending task. In addition, CAN reception and serial port reception are executed using
the interrupt trigger method. Using cycle interrupts and underflow interrupts to divide the task execution time area can not only meet
the CAN transmission requirements of 10ms per frame of data for the entire vehicle, but also each task time can be calculated through the status of the counter and the flag bit to calculate
the execution time of the task, so as to better allocate the execution time period of the task.
3 Conclusions
The battery management system adopts the structure of DSP+OZ890, and with the corresponding anti-interference measures, it has
the characteristics of high performance and low cost. Due to the use of a special battery sampling chip OZ890, the sampling accuracy is improved and
the overcharge problem caused by the imbalance of battery cell voltage is solved. At the same time, the hardware development cycle is greatly shortened, the reliability and maintainability of the system are enhanced
, and good results have been achieved in practical applications.
The author's innovation point: using the OZ890 battery sampling chip to measure battery data, and using PCA9564 to expand
the I2C interface of LF2407, the communication between LF2407 and OZ890 is realized.
Previous article:Research on performance test of intelligent battery charger
Next article:Single-cell lithium-ion battery charger application circuit design based on MAX8844/MAX8844Z/MAX8844Y
Recommended ReadingLatest update time:2024-11-16 23:30
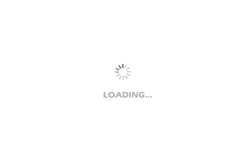
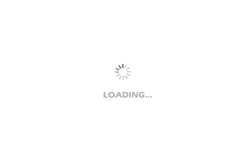
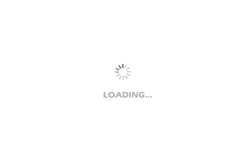
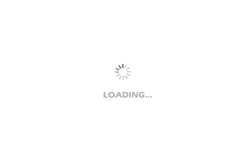
- Popular Resources
- Popular amplifiers
- MathWorks and NXP Collaborate to Launch Model-Based Design Toolbox for Battery Management Systems
- STMicroelectronics' advanced galvanically isolated gate driver STGAP3S provides flexible protection for IGBTs and SiC MOSFETs
- New diaphragm-free solid-state lithium battery technology is launched: the distance between the positive and negative electrodes is less than 0.000001 meters
- [“Source” Observe the Autumn Series] Application and testing of the next generation of semiconductor gallium oxide device photodetectors
- 采用自主设计封装,绝缘电阻显著提高!ROHM开发出更高电压xEV系统的SiC肖特基势垒二极管
- Will GaN replace SiC? PI's disruptive 1700V InnoMux2 is here to demonstrate
- From Isolation to the Third and a Half Generation: Understanding Naxinwei's Gate Driver IC in One Article
- The appeal of 48 V technology: importance, benefits and key factors in system-level applications
- Important breakthrough in recycling of used lithium-ion batteries
- Innolux's intelligent steer-by-wire solution makes cars smarter and safer
- 8051 MCU - Parity Check
- How to efficiently balance the sensitivity of tactile sensing interfaces
- What should I do if the servo motor shakes? What causes the servo motor to shake quickly?
- 【Brushless Motor】Analysis of three-phase BLDC motor and sharing of two popular development boards
- Midea Industrial Technology's subsidiaries Clou Electronics and Hekang New Energy jointly appeared at the Munich Battery Energy Storage Exhibition and Solar Energy Exhibition
- Guoxin Sichen | Application of ferroelectric memory PB85RS2MC in power battery management, with a capacity of 2M
- Analysis of common faults of frequency converter
- In a head-on competition with Qualcomm, what kind of cockpit products has Intel come up with?
- Dalian Rongke's all-vanadium liquid flow battery energy storage equipment industrialization project has entered the sprint stage before production
- Allegro MicroSystems Introduces Advanced Magnetic and Inductive Position Sensing Solutions at Electronica 2024
- Car key in the left hand, liveness detection radar in the right hand, UWB is imperative for cars!
- After a decade of rapid development, domestic CIS has entered the market
- Aegis Dagger Battery + Thor EM-i Super Hybrid, Geely New Energy has thrown out two "king bombs"
- A brief discussion on functional safety - fault, error, and failure
- In the smart car 2.0 cycle, these core industry chains are facing major opportunities!
- The United States and Japan are developing new batteries. CATL faces challenges? How should China's new energy battery industry respond?
- Murata launches high-precision 6-axis inertial sensor for automobiles
- Ford patents pre-charge alarm to help save costs and respond to emergencies
- New real-time microcontroller system from Texas Instruments enables smarter processing in automotive and industrial applications
- ZTE's 7nm chip mass production still needs time to catch up with high-end chip track
- Comparison of Three Synchronous Designs in FPGA
- Looking for package SOT128-1
- 【Qinheng RISC-V core CH582】Timer PWM drive servo
- Selection and use of bypass capacitors
- CircuitPython Holiday Wreath
- Application and advantages of mica capacitors
- First Battlefield
- Infrared remote control LED dot matrix
- [Chuanglong TL570x-EVM] Install Prossessor SDK and create a development environment