流驱动、制备工艺简单等在平板显示中显著的优点,从而日益成为国际研究的热点。在不到20年的时间内,OLED已经由研究进入产业化阶段。
目前已经制作出了使用寿命突破10000h,存储寿命超过50000h的OLED器件,但与液晶显示(LCD)和等离子体显示(PDP)比较起来,寿命相对较短仍是制约OLED商业化的重要因素之一。
根据资料报道[2],影响OLED寿命的因素很多,主要有物理影响和化学影响。物理影响:如功能层组合以及它们相互间界面的影响、阴极材料的影响、空穴传输层(HTL)的玻璃化温度、驱动方式等;化学影响:如阴极的氧化、空穴传输层的晶化等。这些因素都会影响有机电致发光器件的寿命。
研究表明,空气中的水汽和氧气等成分对OLED的寿命影响很大,其原因主要从以下方面进行考虑:OLED器件工作时要从阴极注入电子,这就要求阴极功函数越低越好,但做阴极的这些金属如铝、镁、钙等,一般比较活波,易与渗透进来的水汽发生反应。另外,水汽还会与空穴传输层以及电子传输层(ETL)发生化学反应,这些反应都会引起器件失效。因此对OLED进行有效封装,使器件的各功能层与大气中的水汽、氧气等成分隔开,就可以大大延长器件寿命。
2 OLED的工作原理及器件封装对水汽渗透率的要求
OLED器件一般是在玻璃或聚合物基板上,由夹在透明阳极、金属阴极和夹在它们之间的两层或更多层有机层构成。当器件上加正向电压时,在外电场的作用下,空穴和电子分别由正极和负极注入有机小分子、高分子层内,带有相反电荷的载流子在小分子、高分子层内迁移,在发光层复合,形成激子,激子把能量传给发光分子,激发电子到激发态,激发态能量通过辐射失活,产生光子,形成发光。有机电致发光器件的基本结构是夹层式结构,即各有机功能层被两侧电极像三明治一样夹在中间,且至少有一侧的电极是透明的,以便获得面发光。具体说来,OLED的基本器件结构有单层、双层、三层和多层等。
为了使有机电致发光器件达到实用要求,即要求OLED的器件使用寿命大于10000h,存储寿命超过50000h, 那么, 器件封装的水汽渗透率
(WVTR)要小于5×10-6g·m-2/d[3],氧气的渗透率要小于10-5cm2·m-2/d[4]。数值是以器件的阴极被腐蚀所需要水的量为基础估算而来,例如,假设镁阴极的厚度为50nm,镁的密度为174g/cm3,摩尔质量为24g。这样的OLED阴极镁金属的含量为3.6×10-7mol/cm2,单位面积(cm2)的镁阴极完全被腐蚀所需要的水约为6.4×10-6g,要使器件的工作时间超过10000h,则可以计算出器件的水汽渗透率约为1.5×10-4g·m-2/d,在实际工作时,阴极被腐蚀10%就会严重影响器件的工作。另外在以上的推导中没有考虑其他受到水分的催化作用而阴极受到腐蚀的因素。如果考虑到以上的两个因素,便可以估计出对器件渗透率的要求应该小于10-5g·m-2/d。
3 传统的有机电致发光器件的封装
传统的OLED器件是在刚性基板(玻璃、金属)上制作电极和各有机功能层,对这类器件进行的封装一般是给器件加一个盖板,并将基板和盖板用环氧树脂粘接。这样就在基板和盖板之间形成了一个罩子,把器件和空气隔开,空气中的水、氧等成分只能通过基板和盖板之间的环氧树脂向器件内部进行渗透,因而,比较有效地防止了OLED各功能层以及阴极与空气中的水、氧等成分发生反应[5]。对OLED进行的封装所用的盖板,通常用玻璃和金属两种材料。整个封装过程在充惰性气体,如氮气、氩气等的手套箱内完成。手套箱内水汽含量应小于3×10-6。金属盖板即可以阻挡水、氧等成分对器件封装的渗透,又可以使器件坚固,但是其不透光性限制了这种封装方法在有机电致发光器件上的应用,另外,用金属盖板进行封装时要特别注意金属盖板不能接触到器件的电极,以免引起短路。盖板封装时需要密封胶,由于密封胶的多孔性,容易使空气中的水分渗透进入器件内部,因此在这种封装方式中,一般在器件内部加入氧化钙或氧化钡作为干燥剂来吸收在涂环氧树脂时和封装时残留的水分。
这种封装形式如图1所示。
|
4. Flexible OLED packaging
Compared with other forms of display, organic electroluminescent display has an important advantage in that it can realize flexible display. In 1992, Gustafsson et al. invented OLED based on flexible polymer materials on PET (polyethylene-terephthalate) substrate; in 1997, Forrest et al. invented OLED based on flexible small molecule materials. This type of display device is soft, deformable and not easy to damage. It can be installed on curved surfaces and even wearable. Therefore, it has become a research hotspot in the international display industry [6]. For flexible OLED, traditional packaging methods are ineffective because the cover plate cannot be rolled.
There are two main packaging methods for flexible OLED: (1) Similar to traditional OLED devices, consider adding a flexible polymer cover plate to the device, and then make a barrier layer on the substrate and cover plate to prevent the penetration of water vapor and oxygen. (2) Making a single layer or multiple layers of thin film on the substrate and each functional layer to block the penetration of water, oxygen and other components. The above two packaging methods are shown in Figures 2 and 3.
|
Compared with the one shown in Figure 2, the device is thinner with the direct film encapsulation shown in Figure 3, and there is no need to worry about the wear of the polymer cover during the flexible display. However, this encapsulation requires that the film barrier layer must be closely bonded to the OLED substrate during the formation process. This process is generally completed at a lower temperature, and damage to the organic layer should be avoided as much as possible.
In addition, if the substrate of the device is a material with good water vapor and oxygen barrier properties, such as extremely thin glass or metal, the barrier layer on the substrate can be omitted during encapsulation.
5 Thin film encapsulation technology for flexible OLEDs
Thin film encapsulation technology has been widely used in food and drug packaging before the development of OLEDs. In the 1960s, inorganic coatings were used to coat polymers to reduce the penetration of water into polymers. Organic-inorganic hybrid polymer coatings were also used at this time. The technology of evaporating aluminum film on PET was also commercialized in the 1970s. For flexible OLED, it is difficult to carry out thin film packaging. The barrier layer made on the flexible OLED substrate and cover should meet the following requirements: it must be able to be tightly combined with the OLED substrate or cover; the water and oxygen permeability must meet the life requirements of the OLED; it must have a certain mechanical strength; the barrier layer itself is stable; the formation of other working layers has no effect on the barrier layer; the barrier layer is flexible.
Thin film packaging of flexible OLED devices usually adopts two packaging methods: single-layer thin film packaging and multi-layer thin film packaging.
5.1 Single-layer thin film packaging
This packaging method generally uses plasma chemical vapor deposition (PECVD) or vacuum evaporation technology to prepare a barrier layer on the substrate and the device to block the penetration of water vapor and oxygen. The barrier layer material is mostly silicon oxide compounds or silicon nitrogen compounds. In order to study the barrier effect of single-layer films (inorganic films and organic films) on water vapor, we conducted the following experiments: (1) OLED devices were made on PET substrates. The device structure was ITO/TPD/Alq3/LiF/Al. Al was used as the cathode. After the cathode of the device was evaporated, a layer of SiO2 with a thickness of 150 nm was evaporated on the cathode of the device as a barrier layer (temperature 1200℃, evaporation rate 0.1 nm/s). When the device was taken out of the glove box, the cathode was corroded within 10 minutes. Increasing the thickness of the protective film can delay the time of cathode corrosion. The reason for this problem may be that the evaporated inorganic film is not completely dense. The small holes or other fine channels that appear during the evaporation will cause the device to fail quickly. (2) Still using the above device structure, after evaporating the cathode, a layer of epoxy resin adhesive was dip-coated in the glove box. After curing in the glove box for 24 hours, it was taken out and the cathode was quickly corroded. It can be seen that this polymer film cannot effectively block the penetration of water and oxygen, which may be related to the fact that the cured polymer material is a porous structure. Therefore, if a single-layer film is used to encapsulate FOLED (flexible organic electroluminescent device), an inorganic film with almost no pores and grain boundary defects should be used to achieve better sealing. EliaTECH of South Korea developed this thin film encapsulation technology in 2002. It forms a thin film coating on the back of the substrate to block the moisture or air that causes fatal defects such as insufficient brightness and black spots of OLED. And because glass or metal plates and desiccants are not used, the thickness of the OLED module can be reduced from 2.1mm in the past to less than 1.1mm, and more than 50% of the cost can be saved.
5.2 Multi-layer thin film encapsulation
Another more effective method is to use multi-layer thin film encapsulation and sealing on polymer substrates and organic light-emitting devices, which is what we often call Barix encapsulation technology. The method is to seal and package the flexible organic light-emitting device with a coating material. The mixed protective layer is composed of vacuum-deposited polymer film and high-density dielectric layer alternately, which effectively eliminates the mutual influence between the protective layer materials. The polymer film layer used in the Barix packaging technology can make the substrate surface smooth. The polymer is deposited and cross-linked in a vacuum to form a non-conformal polyacrylate film, and then the number and composition of the dielectric film layer are controlled. The last layer of the Barix structure is an ITO layer, which can be used as the anode of the organic light-emitting diode. The transmittance of the manufactured substrate is greater than 80% in the visible spectrum, and the resistance of the film layer is less than 40Ω/□.
Previous article:High-brightness LED packaging light flux principle
Next article:Key technologies for LED packaging for lighting
Recommended ReadingLatest update time:2024-11-17 00:29
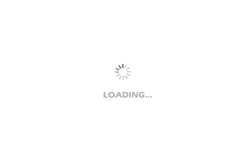
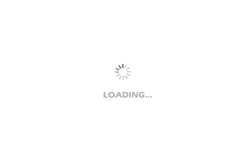
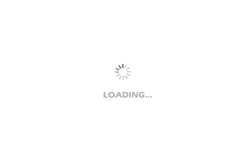
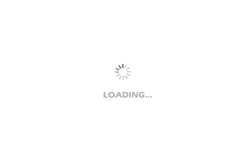
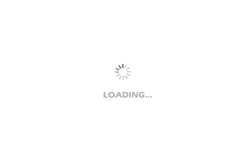
- Popular Resources
- Popular amplifiers
- MathWorks and NXP Collaborate to Launch Model-Based Design Toolbox for Battery Management Systems
- STMicroelectronics' advanced galvanically isolated gate driver STGAP3S provides flexible protection for IGBTs and SiC MOSFETs
- New diaphragm-free solid-state lithium battery technology is launched: the distance between the positive and negative electrodes is less than 0.000001 meters
- [“Source” Observe the Autumn Series] Application and testing of the next generation of semiconductor gallium oxide device photodetectors
- 采用自主设计封装,绝缘电阻显著提高!ROHM开发出更高电压xEV系统的SiC肖特基势垒二极管
- Will GaN replace SiC? PI's disruptive 1700V InnoMux2 is here to demonstrate
- From Isolation to the Third and a Half Generation: Understanding Naxinwei's Gate Driver IC in One Article
- The appeal of 48 V technology: importance, benefits and key factors in system-level applications
- Important breakthrough in recycling of used lithium-ion batteries
- Innolux's intelligent steer-by-wire solution makes cars smarter and safer
- 8051 MCU - Parity Check
- How to efficiently balance the sensitivity of tactile sensing interfaces
- What should I do if the servo motor shakes? What causes the servo motor to shake quickly?
- 【Brushless Motor】Analysis of three-phase BLDC motor and sharing of two popular development boards
- Midea Industrial Technology's subsidiaries Clou Electronics and Hekang New Energy jointly appeared at the Munich Battery Energy Storage Exhibition and Solar Energy Exhibition
- Guoxin Sichen | Application of ferroelectric memory PB85RS2MC in power battery management, with a capacity of 2M
- Analysis of common faults of frequency converter
- In a head-on competition with Qualcomm, what kind of cockpit products has Intel come up with?
- Dalian Rongke's all-vanadium liquid flow battery energy storage equipment industrialization project has entered the sprint stage before production
- Allegro MicroSystems Introduces Advanced Magnetic and Inductive Position Sensing Solutions at Electronica 2024
- Car key in the left hand, liveness detection radar in the right hand, UWB is imperative for cars!
- After a decade of rapid development, domestic CIS has entered the market
- Aegis Dagger Battery + Thor EM-i Super Hybrid, Geely New Energy has thrown out two "king bombs"
- A brief discussion on functional safety - fault, error, and failure
- In the smart car 2.0 cycle, these core industry chains are facing major opportunities!
- The United States and Japan are developing new batteries. CATL faces challenges? How should China's new energy battery industry respond?
- Murata launches high-precision 6-axis inertial sensor for automobiles
- Ford patents pre-charge alarm to help save costs and respond to emergencies
- New real-time microcontroller system from Texas Instruments enables smarter processing in automotive and industrial applications
- A power engineer's insights on EMI!
- MSP430 MCU Development Record (28)
- TWS Bluetooth Headset Disassembly
- [GD32L233C-START Review] Review 3: Accurate delay measurement using timer time5
- 【Chuanglong TL570x-EVM】Review 03 - Evaluation Board Test Manual
- [nRF52840 DK Review] Custom BLE Services
- 【AT32F421 Review】+ Unboxing and Quick Start
- 【Smart Desktop Interactive Robot】Completed
- [Project source code] [Modelsim FAQ] Definition of port reg and wire in TestBench
- Automatic indoor environment control system