introduction
In addition to being used as an AC signal amplifier, the triode can also be used as a switch. Strictly speaking, the triode is not exactly the same as a general mechanical contact switch in terms of action, but it has some characteristics that mechanical switches do not have. Figure 1 shows the basic circuit diagram of a triode electronic switch. As can be seen from the figure, the load resistor is directly connected between the collector of the triode and the power supply, and is located in the loop of the main current of the triode.
The input voltage Vin controls the opening and closing of the transistor switch. When the transistor is in the open state, the load current is blocked. Conversely, when the transistor is in the closed state, the current can flow. In detail, when Vin is a low voltage, since there is no current in the base, there is no current in the collector, resulting in no current in the load connected to the collector end, which is equivalent to the opening of the switch. At this time, the transistor is in the cut-off region.
Similarly, when Vin is a high voltage, due to the flow of base current, a larger amplified current flows through the collector, so the load circuit is turned on, which is equivalent to the closing of the switch. At this time, the transistor operates in the saturation region.
1 Analysis and design of transistor switch circuit
Since the forward bias voltage of the base-emitter junction of a silicon transistor is about 0.6 volts, in order to cut off the transistor, Vin must be lower than 0.6 volts to make the base current of the transistor zero. Usually, in order to be more sure that the transistor is in the cut-off state, the Vin value is often set lower than 0.3 volts. (838 Electronic Resources) Of course, the closer the input voltage is to zero volts, the more it can guarantee that the transistor switch is in the cut-off state. In order to transmit current to the load, the collector and emitter of the transistor must be short-circuited, just like the closing action of a mechanical switch. To do this, Vin must reach a high enough level to drive the transistor into the saturation working area. When the transistor is in saturation, the collector current is quite large, almost making the entire power supply voltage Vcc across the load resistance, so that VcE is close to 0, and the collector and emitter of the transistor are almost short-circuited. Under ideal conditions, according to Ohm's law, when the transistor is saturated, its collector current should be:
Therefore, the minimum base current should be:
The above formula shows the basic relationship between IC and IB. The β value in the formula represents the DC current gain of the transistor. For some transistors, there is a big difference between the AC β value and the DC β value. To close the switch, the Vin value must be high enough to send out a minimum base current value greater than or equal to the minimum base current value required by (Formula 1). Since the base loop is just a series circuit of a resistor and the base-emitter junction, Vin can be solved by the following formula:
Once the base voltage exceeds or is equal to the value obtained by (Equation 2), the transistor is turned on, so that the entire supply voltage is applied across the load resistor, completing the closing action of the switch.
In summary, after the transistor is connected to form the circuit of Figure 1, its function is the same as a mechanical switch connected in series with the load, and the way to open and close the switch can be conveniently controlled by directly utilizing the input voltage, without the need to use the control methods commonly used by mechanical switches such as mechanical actuators, solenoid plungers, or relay armatures.
To avoid confusion, the transistor switches introduced in this article all use NPN transistors. Of course, NPN transistors can also be used as switches, but it is less common.
Explain what the input voltage is that is required to close the switch (transistor saturation) in the switch circuit of Figure 2? And explain the load current and base current values at this time. Solution: From equation 2, we can see that in the saturation state, all the supply voltages are completely dropped across the load resistance. Therefore, from equation (1), we can see that:
Therefore, the input voltage can be calculated as follows:
Figure 2 Using a transistor as a light bulb switch
To use a transistor switch to control the on and off action of a load current as large as 1.5A, only a very small control voltage and current are needed. In addition, although a large current flows through the transistor, it does not need to be equipped with a heat sink, because when the load current flows through it, the transistor is in a saturated state and its VCE approaches zero, so the power multiplied by the current and voltage is very small, and a heat sink is not needed at all.
2 Comparison between transistor switch and mechanical switch
So far, we have assumed that when the transistor switch is turned on, the base and emitter are completely short-circuited. This is not the case. No transistor can be completely short-circuited to make VCE=0. Most small-signal silicon transistors have a VCE (saturation) value of about 0.2 volts when saturated. Even for switching transistors designed for switching applications, their VCE (saturation) value can only be as low as 0.1 volt at most. Moreover, when the load current is high, the VCE (saturation) value will rise slightly. Although for most analysis and calculations, the VCE (saturation) value can be ignored, but when testing switching circuits, it must be understood that the VCE (saturation) value is not really 0.
Although the VCE (saturation) voltage is very small and insignificant in itself, if several transistor switches are connected in series, the total voltage drop effect will be considerable. Unfortunately, mechanical switches often work in series, as shown in Figure 3 (a). The transistor switch cannot simulate the equivalent circuit of the mechanical switch (as shown in Figure 3 (b)) to work, which is a major disadvantage of the transistor switch.
Figure 3 Transistor switch and mechanical switch circuit
Fortunately, although transistor switches are not suitable for series connection, they are perfectly suitable for parallel connection, as shown in Figure 4. Compared with traditional mechanical switches, transistor switches have the following four advantages:
(1) Transistor switches do not have moving contacts, so there is no concern about wear and tear, and they can be used an unlimited number of times. Conventional mechanical switches can only be used millions of times at most due to contact wear, and their contacts are easily contaminated and affect their operation, so they cannot operate in dirty environments. Transistor switches have no contacts and are sealed, so there is no such concern.
(2) The operating speed of a transistor switch is faster than that of a general switch. The opening and closing time of a general switch is measured in milliseconds (ms), while that of a transistor switch is measured in microseconds (μs).
(3) Transistor switches do not have a bounce phenomenon. A general mechanical switch will have a rapid and continuous opening and closing action at the moment of conduction, and then gradually reach a stable state.
(4) When using a transistor switch to drive an inductive load, no spark will be generated at the moment the switch is turned on. On the contrary, when a mechanical switch is turned on, the current on the inductive load is instantly cut off, so the instantaneous induced voltage of the inductor will cause an arc on the contact. This arc will not only erode the surface of the contact, but may also cause interference or harm.
Figure 4 Parallel connection of transistor switches
3. Test of transistor switch
Unlike mechanical switches, transistor switches cannot be judged by naked eyes to determine their current on/off status, so they must be tested with an ammeter. In the standard transistor switch circuit shown in Figure 5, when the switch is turned on, the reading of VEC should be 0, and vice versa, when the switch is turned off, VCE should be equal to VCC.
When the transistor switch is cut off, there is no current flowing through the load, so there is no voltage drop, so the entire supply voltage is dropped across the switch, so its VCE value should be equal to VCC, which is exactly the same as a mechanical switch. If the switch itself should be turned on but is not, then you have to test the size of Vin. To ensure that the transistor is turned on, the Vin voltage value of its base must be high enough. If the Vin value is too low, the problem comes from the signal source rather than the transistor itself. If the Vin level is high enough and there is no problem driving the transistor to turn on, but the load is still not turned on, then you have to test whether the power supply voltage is normal.
In the on state, the VBE value of a silicon transistor is about 0.6 volts. If the Vin value is high enough, but the VBE value is higher or lower than 0.6 volts, for example, VBE is 1.5 volts or 0.2 volts, this means that the base-emitter junction may be damaged and the transistor must be replaced. Of course, this criterion may not be 100% correct. Many power transistors with high current ratings often have VBE values exceeding 1 volt. Therefore, even if the VBE reading reaches 1.5 volts, it may not be certain that the junction of the transistor is damaged. At this time, it is best to check the transistor specification sheet before making an assertion.
Once VBE is normal and base current is flowing, VCE value must be tested. If VCE approaches VCC, it means the collector-base junction of the transistor is damaged and the transistor must be replaced. If VCE approaches zero volts and the load is still not turned on, it may be that the load itself has an open circuit phenomenon, so the load must be checked and replaced.
Figure 5 Transistor switch circuit, voltage diagram of each main test circuit
When Vin drops to a low voltage level, the transistor should be cut off and the load should be disconnected. If the load is still not disconnected, it may be that the collector-base and collector-emitter of the transistor are short-circuited and must be replaced.
3.1 Improved circuit of basic triode switch
Sometimes, the low voltage level we set may not be able to turn off the transistor switch, especially when the input level is close to 0.6 volts. To overcome this critical situation, correction steps must be taken to ensure that the transistor can be turned off. Figure 6 shows two common improved circuits designed for this situation.
Figure 6 Two correct improved circuits to ensure transistor switching action
In the circuit of Figure 6 (a), a diode is connected in series between the base and the emitter, so that the input voltage value that can cause the base current to conduct is increased by 0.6 volts. In this way, even if the Vin value approaches 0.6 volts due to the malfunction of the signal source, it will not cause the transistor to conduct, so the switch can still be in the off state.
The circuit of Figure 6 (b) adds an auxiliary-hold-off resistor R2. The appropriate design of R1, R2 and Vin values can ensure that the switch is turned off at the critical input voltage. As shown in Figure 6 (b), before the base-emitter junction is turned on (IB0), R1 and R2 form a series voltage divider circuit, so R1 must cross a fixed (variable with Vin) divided voltage, so the base voltage must be lower than the Vin value. Therefore, even if Vin is close to the critical value (Vin=0.6 volts), the base voltage will still be pulled down by the auxiliary-hold-off resistor connected to the negative power supply to below 0.6 volts. Due to the deliberate design of R1, R2 and VBB values, as long as Vin is within the high value range, the base will still have enough voltage value to turn on the transistor without being affected by the auxiliary-hold-off resistor.
3.1.1 Speed-up capacitor
In applications that require fast switching, the switching speed of the transistor switch must be accelerated. Figure 7 shows a common method. This method only requires connecting an acceleration capacitor in parallel with the RB resistor. When Vin rises from zero voltage and starts to send current to the base, the capacitor cannot be charged instantly, so it is like a short circuit. However, at this time, a large current flows from the capacitor to the base instantly, thus speeding up the switch conduction. Later, after charging is completed, the capacitor is like an open circuit, which does not affect the normal operation of the transistor.
Figure 7 Circuit with speed-up capacitor
Once the input voltage drops from a high level back to a zero voltage level, the capacitor will cause the base-emitter junction to become reverse biased in a very short time, causing the transistor switch to be quickly cut off. This is because the left end of the capacitor has been charged to a positive voltage. Therefore, at the moment the input voltage drops, the voltage across the capacitor cannot change instantly and will remain at a constant value. Therefore, the drop in input voltage immediately causes the base voltage to drop, causing the base-emitter junction to become reverse biased, and quickly cutting off the transistor. Appropriate selection of the acceleration capacitor value can reduce the switching time of the transistor switch to less than a few tenths of a microsecond. Most acceleration capacitor values are about hundreds of pico-farads (pF).
Sometimes the load of the transistor switch is not directly added between the collector and the power supply, but connected in the way shown in Figure 8. This connection is very similar to the circuit of the small signal AC amplifier, except that there is one less output coupling capacitor. This connection is exactly the opposite of the normal connection. When the transistor is cut off, the load is energized, and when the transistor is turned on, the load is cut off. These two circuit forms are common, so it is necessary to have a clear ability to distinguish.
Figure 8 Improved connection method of connecting the load to the transistor switch circuit
3.1.2 Totem switch
If the transistor switch in Figure 8 is added with a capacitive load (assuming it is connected in parallel with RLD), then after the transistor is turned off, the load voltage must be established by slowly charging the capacitor through the RC resistor. Therefore, the larger the capacitance or resistance value, the larger the time constant (RC), and the slower the rise rate of the load voltage. In some applications, this phenomenon is not allowed, so the improved circuit of Figure 9 must be used.
Figure 9 Totem transistor switch
The totem circuit is formed by directly stacking a transistor on top of another transistor, which is why it gets its name. To energize the load, the Q1 transistor must be turned on and the Q2 transistor must be turned off, so that the load can be connected to VCC through Q1. To de-energize the load, the Q1 transistor must be turned off and the Q2 transistor must be turned on, so that the load will be grounded through Q2. Since the collector of Q1 has almost no resistance except for a very small contact resistance (as shown in Figure 9), the load is almost directly connected to the positive power supply, and therefore when Q1 is turned on, there is no slow charging of the capacitor. Therefore, it can be said that Q1 "pulls up the load" and is called a "pull up transistor", and Q2 is called a "pull down transistor". The input control circuit on the left side of Figure 9 is responsible for the conduction and cutoff control of Q1 and Q2 transistors, but it must ensure that Q1 and Q2 are not turned on at the same time, otherwise the VCC and ground will be short-circuited through Q1 and Q2. If this is the case, the large current of the short circuit will burn at least one transistor. Therefore, the totem transistor switch must not be used in parallel as shown in Figure 6-4, otherwise as long as any one of the transistors in the Q1 group above the totem is turned on, and one of the transistors in the Q2 group below happens to be turned on, the power supply will be short-circuited through the turned-on Q1 and Q2, causing serious consequences.
3.2 Application of transistor switch
3.2.1 Drive Instructions
One of the most common applications of transistor switches is to drive indicator lights. Indicator lights can indicate the operating status of a specific point in the circuit, or whether a motor controller is energized. In addition, they can also indicate whether a limit switch is turned on or whether a digital circuit is in a high potential state.
For example, Figure 10 (a) uses a transistor switch to indicate the output status of a digital flip-flop. If the output of the flip-flop is high (usually 5 volts), the transistor switch is turned on, and the indicator light is on. Therefore, the operator can know the current working status of the flip-flop by just looking at the indicator light without using an electric meter to detect it.
Sometimes the current capacity of the output circuit of a signal source (such as a flip-flop) is too small to drive the transistor switch. In this case, to avoid malfunction due to overload of the signal source, the improved circuit shown in Figure 10 (b) must be used. When the output is high, the emitter follower transistor Q1 is first driven to amplify the current, and then Q2 is turned on to drive the indicator light. Since the input impedance of the emitter follower stage is quite high, the flip-flop only needs to provide a small amount of input current to achieve satisfactory operation.
Digital Display The circuit of Figure 10(a) is often used in digital displays.
Figure 10 (a) Basic circuit diagram (b) Improved circuit
3.2.2 Interface circuits at different voltage levels
In industrial equipment, solid-state logic circuits are often required to perform control tasks. The principles of digital logic circuits will be introduced in detail in the next chapter. Here, for the purpose of explaining the interface circuit, the control circuit of industrial equipment is divided into three major parts: (1) input part, (2) logic part, and (3) output part.
In order to achieve reliable operation, the input and output parts of industrial equipment usually operate at a higher voltage level, generally 220 volts. The logic part operates at a low voltage level. In order for the system to work properly, it is necessary to enable the two different voltage levels to communicate. This matching work between different voltages is called the interface problem. The circuit that performs the interface matching work is called the interface circuit. Transistor switches are often used to perform this kind of work.
FIG11 is an example of an interface circuit using a transistor switch as a high voltage input to control a low voltage logic. When the micro switch of the input part is closed, the step-down transformer is turned on, and the full-wave rectifier filter circuit sends a low voltage DC control signal. This signal turns on the transistor, and the collector voltage drops to 0 (saturation) volts. This 0 volt signal can be sent to the logic circuit to indicate that the micro switch is in the closed state.
On the contrary, if the micro switch is turned on, the transformer will not be energized, and the transistor will be cut off. At this time, the collector voltage will rise to the VCC value. This VCC signal can be sent to the logic circuit to indicate that the micro switch is in the on state. In Figure 11, the logic circuit is used as the load of the transistor and is connected between the collector and the ground (as shown in Figure 11). Therefore, the R1, R2 and RC values of the transistor switch circuit must be carefully selected to ensure that the transistor only works in the cut-off region and the saturation region, and does not work in the active (linear) region.
Figure 11 Transistor switch as the interface between the input part and the logic part
Previous article:Some Defects of Blue Light Emitting Diode Wafer Preparation Technology
Next article:Faster response with smaller components
Recommended ReadingLatest update time:2024-11-16 17:32
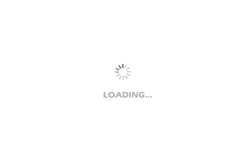
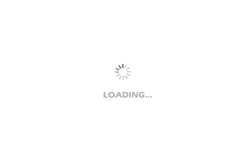
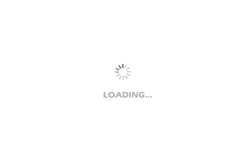
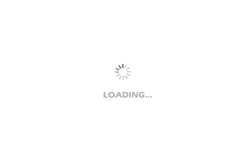
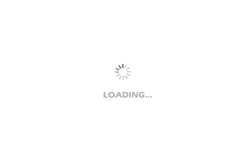
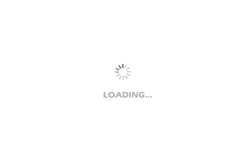
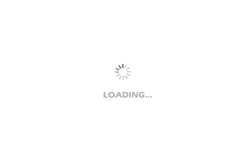
- Popular Resources
- Popular amplifiers
-
Operational Amplifier Practical Reference Handbook (Edited by Liu Changsheng, Zhao Mingying, Liu Xu, etc.)
-
A Complete Illustrated Guide to Operational Amplifier Applications (Written by Wang Zhenhong)
-
Design of isolated error amplifier chip for switching power supply_Zhang Rui
-
DAM medium wave transmitter high frequency power amplifier module test platform_Tian Tian
- MathWorks and NXP Collaborate to Launch Model-Based Design Toolbox for Battery Management Systems
- STMicroelectronics' advanced galvanically isolated gate driver STGAP3S provides flexible protection for IGBTs and SiC MOSFETs
- New diaphragm-free solid-state lithium battery technology is launched: the distance between the positive and negative electrodes is less than 0.000001 meters
- [“Source” Observe the Autumn Series] Application and testing of the next generation of semiconductor gallium oxide device photodetectors
- 采用自主设计封装,绝缘电阻显著提高!ROHM开发出更高电压xEV系统的SiC肖特基势垒二极管
- Will GaN replace SiC? PI's disruptive 1700V InnoMux2 is here to demonstrate
- From Isolation to the Third and a Half Generation: Understanding Naxinwei's Gate Driver IC in One Article
- The appeal of 48 V technology: importance, benefits and key factors in system-level applications
- Important breakthrough in recycling of used lithium-ion batteries
- Innolux's intelligent steer-by-wire solution makes cars smarter and safer
- 8051 MCU - Parity Check
- How to efficiently balance the sensitivity of tactile sensing interfaces
- What should I do if the servo motor shakes? What causes the servo motor to shake quickly?
- 【Brushless Motor】Analysis of three-phase BLDC motor and sharing of two popular development boards
- Midea Industrial Technology's subsidiaries Clou Electronics and Hekang New Energy jointly appeared at the Munich Battery Energy Storage Exhibition and Solar Energy Exhibition
- Guoxin Sichen | Application of ferroelectric memory PB85RS2MC in power battery management, with a capacity of 2M
- Analysis of common faults of frequency converter
- In a head-on competition with Qualcomm, what kind of cockpit products has Intel come up with?
- Dalian Rongke's all-vanadium liquid flow battery energy storage equipment industrialization project has entered the sprint stage before production
- Allegro MicroSystems Introduces Advanced Magnetic and Inductive Position Sensing Solutions at Electronica 2024
- Car key in the left hand, liveness detection radar in the right hand, UWB is imperative for cars!
- After a decade of rapid development, domestic CIS has entered the market
- Aegis Dagger Battery + Thor EM-i Super Hybrid, Geely New Energy has thrown out two "king bombs"
- A brief discussion on functional safety - fault, error, and failure
- In the smart car 2.0 cycle, these core industry chains are facing major opportunities!
- The United States and Japan are developing new batteries. CATL faces challenges? How should China's new energy battery industry respond?
- Murata launches high-precision 6-axis inertial sensor for automobiles
- Ford patents pre-charge alarm to help save costs and respond to emergencies
- New real-time microcontroller system from Texas Instruments enables smarter processing in automotive and industrial applications
- Analog circuit knowledge: basic usage of triodes
- Intelligent car infrared tracking problem
- What is Ferroelectric RAM (FRAM)?
- EEWorld invites you to disassemble (sixth issue): disassemble the car wireless charger
- [HPM-DIY] has launched a visual configuration code generation tool.
- A newbie who can only repair adapters and charging heads wants to upgrade to engineering.
- The greatest equation
- CH583 Evaluation Serial Port Download
- A chart to understand China Telecom's "5G SA Deployment Guide"
- Please tell me how to dig out a small piece of the board from Altium