1. With the rapid development of the power supply and distribution industry, the communication industry and electric vehicles, the development of the supporting
power supply
- the battery industry and technological progress and innovation have also been driven. Due to the excellent cost-effectiveness of lead-acid batteries, in addition to batteries for portable electronic products and batteries for aerospace and high-end military use, more than 90% of the energy storage power supplies for electric vehicles, UPS systems, telecommunication facilities (telecommunication centers, satellite ground stations), internal combustion locomotives, automobiles, power stations, substations, emergency power supplies, ships and Guangming projects in power-free areas are using lead-acid batteries. In 2005, the total output of lead-acid livestock batteries in China was 66.45 million kilovolt-amperes, with a total output value of 35 billion yuan; in 2006, the total output rose to 84.57 million kilovolt-amperes, with a total output value of 42 billion yuan, accounting for about one-third of the total output value of the national battery industry (data provided by Dai Jingming, consultant of Jiangsu Shuangdeng Power Group). This shows that the use of lead-acid batteries is very extensive. However, during production, transportation and use, collisions, falls and drops may occur; this may cause the battery shell to rupture to a certain extent. If the temperature of a certain process is not well controlled or the internal stress of the plastic shell is not completely eliminated during the injection molding process of the battery shell cover, the possibility of slight cracks in the shell will increase. Microcracks often appear after a period of use, causing micro-leakage of electrolyte. If the glue is improperly used when sealing the battery pole, or due to external force impact or temperature shock, the sealing of the battery will fail. The slight cracks on the battery shell and the seal at the battery pole can be repaired to restore the battery function.
2 Use bonding technology to repair slightly damaged
lead-acid battery
shells
2.1 Scope of application of bonding technology to repair slightly damaged battery shells
Bonding technology is mainly used to repair damaged lead-acid battery shells that are soluble in solvents. Although there are many solvent-soluble engineering plastics, from the perspective of comprehensive performance, the engineering plastics currently selected for lead-acid battery shell materials are mainly ABS (acrylonitrile-butadiene-styrene copolymer) engineering plastics and SAN (styrene-acrylonitrile copolymer) engineering plastics. The following introduces the repair of minor damage to the shell of the above materials.
2.2 Mechanism of bonding repair
After the solvent contacts the soluble engineering plastic, it quickly penetrates into the inside under the action of affinity, and the surface becomes soft. Under the action of solvent infiltration, the molecules of the engineering plastics of the same material will penetrate and dissolve with each other. After the solvent evaporates, the bonded material becomes a whole. The bonding strength will be higher with the action of external force (adding a certain amount of pressure).
2.2 Preparation of adhesive solution
Prepare the adhesive solution according to the ratio of 100ml of n-butyl ketone + 25g of ABS (or SAN) plastic particles. After weighing, shake the batching container continuously to completely dissolve the solid particles and form a uniform solution for standby use. The adhesive solution can be used for a long time after sealing.
2.3 Preparation of the repaired lead-acid battery shell
The damaged part of the lead-acid battery shell should be cleaned, and there should be no dust, powdery particles, oil stains and electrolyte on the bonding surface and it should be flat.
2..4 Take a clean ABS (or SAN) plastic plate of appropriate size (the size of the plate should be larger than the crack by more than 5mm in all directions, and the thickness should be equivalent to the battery shell wall, and set aside.
2.5 Apply an appropriate amount of glue to the damaged part of the lead-acid battery shell and the surrounding area of more than 5mm, then press the cut plastic plate tightly on the damaged part of the battery shell coated with glue and press it flat. After 12 hours, wait for the glue to completely dry and check if there is no leakage. It can be considered that the repair is complete and can be submitted for use. It should be noted that the bonding surface must be flat and the bonding point must be pressed flat.
2.6 If the repaired battery leaks a lot of electrolyte before repair, sulfuric acid electrolyte with a certain concentration should be added, and it can be submitted for use after charging and activation.
3 Repair of lead-acid batteries with slightly damaged shells using hot melt bonding technology
3.1 Hot melt bonding
mechanism Because most lead-acid battery shells are molded by injection molding, the raw materials used are thermoplastic engineering plastics. Thermoplastic engineering plastics will melt at a certain temperature and become viscous or molten. The molten adhesive flows to the damaged part of the heated battery shell and penetrates each other. After cooling, it forms a whole to achieve the purpose of bonding and repair.
3.2 Hot melt adhesive repair method
3.2.1 Preparation of the repaired battery
Clean the damaged surface of the lead-acid battery. There should be no acid, dust, oil and granular impurities on the bonding surface. 3.2.2
Repair Use a hot melt gun to heat the hot melt glue stick and heat the repaired part appropriately, so that the hot melt glue stick melts and flows to the damaged part of the battery shell. The glue on the hot melt adhesive bonding surface in all directions should be more than 5mm larger than the damaged gap. The thickness of the adhesive surface of the damaged gap should not be less than the wall thickness of the battery shell. The hot melt bonding surface can be appropriately pressurized to facilitate firm bonding. After natural cooling for 12 hours, check that there is no leakage. It can be considered that the repair is complete and can be submitted for use.
Hot melt adhesive repair can be repaired with a hot melt glue stick or a rod (plate) made of the same material as the battery shell as a hot melt bonding material. The latter will have a better effect.
3.2.3 For batteries that have lost too much liquid before melt adhesive repair, the electrolyte of the used concentration should be added to the middle part of the liquid level line after repair and charged and activated before submission for use.
3.3 Scope of application of hot melt adhesive technology to repair lead-acid battery shells
Hot melt adhesive repair is suitable for repairing battery shells made of all thermoplastic engineering plastics, especially the repair of battery shell cracks made of thermoplastic engineering plastics without solvents, such as PP (polypropylene), modified reinforced PP (Polypropylene reinforced with talcum powder), etc. The slight gap on the cover can also be repaired by the above hot melt adhesive 2007-5-7 bonding method.
4 Repair of lead-acid battery pole seal failure using adhesive bonding technology
4.1 Causes of pole seal failure
4.1.1 The connection seal between the pole and the battery cover of the lead-acid battery mainly uses epoxy adhesives that cure at room temperature. The best use period of the prepared epoxy adhesive is within 45 minutes at room temperature. During the use of the epoxy adhesive, due to gradual curing, the adhesive gradually becomes viscous and wire drawing occurs. At this time, the adhesive should be scrapped. Although the adhesive still has fluidity, it loses its wettability on the bonding surface. At this time, the adhesive should be scrapped if it is not used up. If the operator continues to use it, it will inevitably lead to a decrease in the sealing effect. The problem may not be discovered and tested during the factory inspection, but the seal will fail after a period of use.
4.1.2 During the use of the battery, due to the impact, vibration, bumps and other external forces, the epoxy sealant is broken and the seal fails.
4.1.3 During the use of the battery, due to the hot and cold shock of the ambient temperature, the glue joint surface will produce fine gaps, causing the seal to fail. 4.2 Preparation of epoxy sealant for repairing the pole seal
Here is a low-toxic, tough, impact-resistant, high-strength epoxy sealant formula that cures at room temperature. Some common materials add toluene to some epoxy glue formulas, and use low-molecular amines as curing agents. This kind of epoxy glue formula is highly toxic, pollutes the environment, and has poor strength.
4.2.1 Low-toxicity epoxy glue formula
E-51 epoxy resin + 651 polyamide resin + benzylenediamine (m-phenylenediamine) + red (or blue) pigment == 100 grams + 25 grams + (9~10) grams + appropriate amount of pigment
在冬天或在较低的环境温度下环氧胶比较粘稠,可以在配方中加入10克左右的501环氧丙烷丁基醚(环氧胶的活性稀釋剂,参与固化聚合反应,比使用非活性稀剂配出胶的强度高)。
注:加一点颜料是为了区分正负极的用胶
4.2.2`环氧胶的配制
按配方比例准确的称取一定量的原料,充分的搅拌均匀。待用。
4.3被修复电池的准备
把密封失效的极柱与盖子连结处旧的环氧胶请除干静,清洗成中性,粘接面洁净,无油污杂物。 4.4修复
把配制好的环氧浇灌到清理准备好的待修电池极柱与电池盖的连接处,灌平。常温下固化24小时,经检查不漏后,(若失电解液较多补充必要的电解液)充电后可以提交使用。
注:环氧胶液只有(30~45)分钟的使用期,若配胶器皿有点发热时说明胶液已大量固化,应停止使用。 4.5环氧胶的适用范围
这个低毒常温固化环氧胶适用于各种环氧胶密封失效的修复,也可以在生产中使用。这可减少对环境的污染,增强环保意识。
铅酸蓄电池 的修复技术是最近几年才发展起来的一项应用技术,是一项绿色环保的修复技术。用胶接粘合或用热熔胶粘合技术修复因碰撞、跌落、摔打造成机械损伤的电池壳体是很有效地修复方法;用低毒常温固化环氧胶修复电池极柱处环氧胶密封失效也是一个很有效的方法。对铅酸蓄电池修复技术的开发和应用体现了对建设环保型社会的理解、贯彻和支持。电池的修复延长了电池的使用壽命,可以为使用者减少购置新电池的支出;减少了供应电池的压力,从而可以减少因铅酸蓄电池的生产产生对环境的汚染;是很有价值并值得推广应用的新技术。
Keywords:Battery
Reference address:Introduction to the repair technology of broken plastic shell of battery
在冬天或在较低的环境温度下环氧胶比较粘稠,可以在配方中加入10克左右的501环氧丙烷丁基醚(环氧胶的活性稀釋剂,参与固化聚合反应,比使用非活性稀剂配出胶的强度高)。
注:加一点颜料是为了区分正负极的用胶
4.2.2`环氧胶的配制
按配方比例准确的称取一定量的原料,充分的搅拌均匀。待用。
4.3被修复电池的准备
把密封失效的极柱与盖子连结处旧的环氧胶请除干静,清洗成中性,粘接面洁净,无油污杂物。 4.4修复
把配制好的环氧浇灌到清理准备好的待修电池极柱与电池盖的连接处,灌平。常温下固化24小时,经检查不漏后,(若失电解液较多补充必要的电解液)充电后可以提交使用。
注:环氧胶液只有(30~45)分钟的使用期,若配胶器皿有点发热时说明胶液已大量固化,应停止使用。 4.5环氧胶的适用范围
这个低毒常温固化环氧胶适用于各种环氧胶密封失效的修复,也可以在生产中使用。这可减少对环境的污染,增强环保意识。
铅酸蓄电池 的修复技术是最近几年才发展起来的一项应用技术,是一项绿色环保的修复技术。用胶接粘合或用热熔胶粘合技术修复因碰撞、跌落、摔打造成机械损伤的电池壳体是很有效地修复方法;用低毒常温固化环氧胶修复电池极柱处环氧胶密封失效也是一个很有效的方法。对铅酸蓄电池修复技术的开发和应用体现了对建设环保型社会的理解、贯彻和支持。电池的修复延长了电池的使用壽命,可以为使用者减少购置新电池的支出;减少了供应电池的压力,从而可以减少因铅酸蓄电池的生产产生对环境的汚染;是很有价值并值得推广应用的新技术。
Previous article:Understanding of battery charging
Next article:The difference between NiMH, NiCd and Lithium batteries
Recommended ReadingLatest update time:2024-11-16 20:54
MATLAB and Simulink R2022b offer new Simscape Battery and updates
MATLAB and Simulink R2022b Deliver New Simscape Battery and Updates to Simplify and Automate Model-Based Design
Platform release also includes new Medical Imaging Toolbox, providing an end-to-end medical image analysis workflow
Beijing, China, September 20, 2022 -
MathWorks today announ
[Embedded]
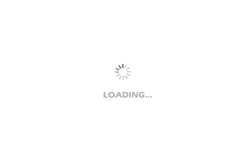
- Popular Resources
- Popular amplifiers
Recommended Content
Latest Power Management Articles
- MathWorks and NXP Collaborate to Launch Model-Based Design Toolbox for Battery Management Systems
- STMicroelectronics' advanced galvanically isolated gate driver STGAP3S provides flexible protection for IGBTs and SiC MOSFETs
- New diaphragm-free solid-state lithium battery technology is launched: the distance between the positive and negative electrodes is less than 0.000001 meters
- [“Source” Observe the Autumn Series] Application and testing of the next generation of semiconductor gallium oxide device photodetectors
- 采用自主设计封装,绝缘电阻显著提高!ROHM开发出更高电压xEV系统的SiC肖特基势垒二极管
- Will GaN replace SiC? PI's disruptive 1700V InnoMux2 is here to demonstrate
- From Isolation to the Third and a Half Generation: Understanding Naxinwei's Gate Driver IC in One Article
- The appeal of 48 V technology: importance, benefits and key factors in system-level applications
- Important breakthrough in recycling of used lithium-ion batteries
MoreSelected Circuit Diagrams
MorePopular Articles
- Innolux's intelligent steer-by-wire solution makes cars smarter and safer
- 8051 MCU - Parity Check
- How to efficiently balance the sensitivity of tactile sensing interfaces
- What should I do if the servo motor shakes? What causes the servo motor to shake quickly?
- 【Brushless Motor】Analysis of three-phase BLDC motor and sharing of two popular development boards
- Midea Industrial Technology's subsidiaries Clou Electronics and Hekang New Energy jointly appeared at the Munich Battery Energy Storage Exhibition and Solar Energy Exhibition
- Guoxin Sichen | Application of ferroelectric memory PB85RS2MC in power battery management, with a capacity of 2M
- Analysis of common faults of frequency converter
- In a head-on competition with Qualcomm, what kind of cockpit products has Intel come up with?
- Dalian Rongke's all-vanadium liquid flow battery energy storage equipment industrialization project has entered the sprint stage before production
MoreDaily News
- Allegro MicroSystems Introduces Advanced Magnetic and Inductive Position Sensing Solutions at Electronica 2024
- Car key in the left hand, liveness detection radar in the right hand, UWB is imperative for cars!
- After a decade of rapid development, domestic CIS has entered the market
- Aegis Dagger Battery + Thor EM-i Super Hybrid, Geely New Energy has thrown out two "king bombs"
- A brief discussion on functional safety - fault, error, and failure
- In the smart car 2.0 cycle, these core industry chains are facing major opportunities!
- The United States and Japan are developing new batteries. CATL faces challenges? How should China's new energy battery industry respond?
- Murata launches high-precision 6-axis inertial sensor for automobiles
- Ford patents pre-charge alarm to help save costs and respond to emergencies
- New real-time microcontroller system from Texas Instruments enables smarter processing in automotive and industrial applications
Guess you like
- MSP430F5438+DTH11 Example Code
- [Project source code] Altera Altium format device library and package including Cyclone V
- Several parameter issues of audio playback equipment
- [NXP Rapid IoT Review] + Use offline IDE to build an application that displays sensor information
- 4412 Development Board Qt Timer - Experimental Steps and Partial Code
- LNA Design Based on ADS
- When I wrote the program, I saw TMOD=1, but I didn't see any operation on each bit. What's the meaning of these 8 bits? And some...
- Download Keysight Technologies e-books and get gifts!
- Simulating Microstrip Elliptical Low-Pass Filter Using ADS Software
- STM32L151 low power consumption problem