There are several sources of error in the inspection of high-power laser diodes used in telecommunications. These error sources include coupling high current pulses, photodetector coupling, slow response of the detector itself, and errors. By properly handling these problems, the test time can be shortened, the test accuracy can be improved, and the failure rate can be reduced.
LIV curve
The basic test of laser diodes is the light-current-voltage (LIV) curve, which measures the electrical and optical output power characteristics simultaneously. This test can be performed at any stage of production, but is first used for laser diode selection, i.e. to eliminate bad diodes in advance.
Perform a current scan on the device under test and record the voltage at each scan step. At the same time, use an instrument to monitor the optical output power. This test is best performed in pulse mode early in production, before the laser diode is installed into the module. At this point, the diode is still in its original state and pulse detection is necessary because the component has no temperature control circuitry at this point. If tested with direct current it would at least change their characteristics and at worst damage them. In subsequent production, when they are installed in temperature-controlled modules, they can be tested with DC current and the results can be compared with the pulse test. Additionally, some diodes will pass the DC test but not the pulse test.
Analysis of LIV test data can determine the characteristics of the laser, including the critical current to produce laser light, quantum efficiency, and nonlinear characteristics of the output (Figure 1).
Testing laser diodes requires a properly formed current pulse. It should reach full current as quickly as possible and remain stable long enough to ensure accurate results. In the initial stages of testing, pulses with a width of 0.5ms to 1ms are generally used. Current variations range from tens of milliamperes to 5 amps.
?
Figure 1
Impedance matching
To deliver high-speed current pulses to a laser diode while avoiding reflection problems, it is generally believed that a transmission line—such as a length of coaxial cable—can be used. But the most commonly used coaxial cable has an impedance of 50Ω, and the impedance of the diode is about 2Ω, which is a very mismatch. Although a 48Ω resistor can be connected in series, this will create new problems; a 50Ω system will require a voltage of 250V to pass 5A current, which is very dangerous for both people and equipment. In addition, since the dynamic resistance of the laser decreases as the current increases, the test conditions change as the test progresses.
Using low-impedance coaxial cable may be an effective solution, but doing so will change the dynamic resistance of the laser diode. Another way is to connect the laser diode with two 10Ω coaxial cables and apply pulse current to both ends of the cable (Figure 2). In this way, applying a voltage of less than 10V to the diode can produce 5A of current. Because the system has a current source, problems caused by changes in the dynamic resistance of the diode are avoided.
Even the most careful impedance matching is unlikely to be perfect, so it is practical to use the shortest possible transmission lines. This is also to minimize the loop area connecting the laser diode.
?
Figure II
electrical measurement
When high-speed pulses are applied to a laser diode, it is not easy to measure its voltage and current. Measuring voltage with a cathode ray tube detector can also cause problems, one of which is grounding. The frequency range of the detector must reach 1GHz.
Current measurement is a little simpler. The measurement can be made by placing a low value resistor (lower resistance than the laser diode) in series with the diode, but the capacitance and inductance of the resistor are required to be very low. Wirewound resistors have inductance losses, so they are not suitable for high frequency testing.
Choosing a Photodetector
There are three commonly used detector materials: silicon, germanium, and indium gallium arsenide (InGaAs), each with its own advantages and disadvantages. As shown in Figure 3, the choice of detector depends largely on the wavelength it is adapted to. When the wavelength is less than 800nm, silicon is the only option. However, the commonly used wavelengths in the telecommunications field are between 1300nm and 1700nm. Indium gallium arsenide is the best at this time because its response characteristics are very stable in this range. However, there are problems with the response of InGaAs to pulses. To avoid overheating of laser diodes, it is best to test with short enough pulses, but InGaAs detectors need long enough to reach some kind of stable state.
As shown in Figure 4, the InGaAs detector is very unstable even within 10 microsecond pulses. This problem will be more serious if the pulse width is reduced to 1 microsecond. The germanium detector does not have this problem, so it is better suited for short pulses.
Figure 3
?
Picture 4
detector coupling
There are several ways to couple the output of a laser diode to a detector. One approach is to shine the laser directly onto the detector, but this approach has several drawbacks. First, there is no guarantee that all light will hit the detector. For example, the cross-section of the emitted beam is elliptical, or the diameter of the beam is larger than the effective receiving area of the detector, or the emitted beam is not aligned with the detector, which will cause part of the light to be lost. Second, some detectors are polarization sensitive, which can lead to more errors. Third, the output of some high-power laser diodes will cause many detectors to reach saturation and fail.
The integrating sphere is usually the best solution. It is a hollow sphere with an inner surface coated with highly reflective material and two ports. One end is fixed on the detector and the other end is used to input the measured light (Figure 5). The integrating sphere can receive all the light emitted from the light source and distribute the light evenly on the inner surface after scattering. The detector installed on the side of the integrating sphere can "see" a fixed proportion (about 1%) of the input light. In this way, the power of all incident light can be calculated, and very high-power light can be measured without worrying about the detector being damaged.
Figure 5
Detection speed
There was a time when demand for fiber optic communications equipment exceeded supply and manufacturer efficiency became a secondary concern. Today, however, testing must be as fast, accurate and cheap as anything else. This indicates that an optical power meter is not a good choice and the detection time of this instrument is too long.
To avoid this problem, standard practice is to use an instrumentation suite that includes a pulse source, a light measurement component (photodiode detector, etc.), a pair of high-speed current-to-voltage converters, and a high-speed multi-channel digital sampling oscilloscope (DSO). Pulsed sources generate pulses and other instruments measure electrical and optical responses.
This process may require thousands of pulses. Sometimes there are hundreds of pulses per level. This seems to improve sensitivity, accuracy and precision, but it masks the problem of waveform distortion. This is also a long process, taking tens of seconds to several minutes for each device under test. This system can test approximately 2,500 parts per day, and each set of inspection equipment costs approximately US$150,000.
A newer approach is to include all functions in a single instrument. This instrument is essentially a pulse source measurement unit whose output impedance and cable are closely matched to the impedance of the laser diode. The measurement part of the system integrates multi-channel data acquisition, specialized timing circuits, high-speed current-to-voltage converters, and a digital signal processor (DSP) that emulates the functionality of a DSO and controls the measurement program.
This instrument is programmed by the internal DSP according to the detection sequence given by the GPIB bus to determine the sequence of LIV scanning. Once programmed, the digital signal processor alone performs the pulsed LIV scan without the need for instructions or computer control from other devices. In fact, the instrument directly provides control signals to various components through digital I/O ports.
Quick analysis of pulse measurement results is achieved through DSP, which is no longer as time-consuming as before. This reduces pulse current and voltage detection time to a few seconds and minimizes software complexity.
Because it only takes a few seconds to test a single unit, 15,000 diodes can still be tested every day even when the system utilization rate is only 85%. Purchasing such a system costs only a fraction of the original price, but results in higher production capabilities.
Such systems can be designed in both pulsed and non-pulsed modes. Both functions can be used on the same platform to scan both types of LIV through the same detection channel. Comparing pulsed and non-pulsed test results can provide more complete information about the performance of the device under test.
The 3rd generation LIV detection system combines all relevant functions into one instrument to greatly increase detection capabilities.
Previous article:Measuring ballistic parameters from an acoustic perspective using PC and long baseline time recording methods
Next article:Design of duty cycle measurement circuit based on differential voltage amplifier
Recommended ReadingLatest update time:2024-11-16 20:50
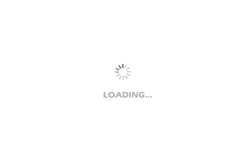
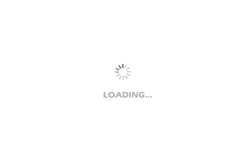
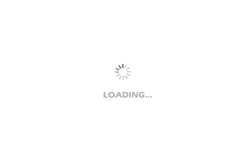
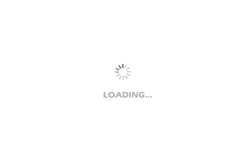
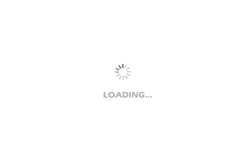
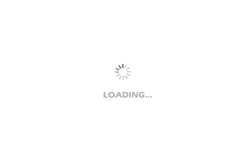
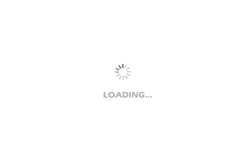
- Popular Resources
- Popular amplifiers
-
Modern Electronic Technology Training Course (Edited by Yao Youfeng)
-
Sensor Principle and Application Circuit Design (Edited by Chen Shuwang, Song Lijun, Xu Yunfeng)
-
Single-chip microcomputer C language programming and simulation
-
100 Examples of Microcontroller C Language Applications (with CD-ROM, 3rd Edition) (Wang Huiliang, Wang Dongfeng, Dong Guanqiang)
- Keysight Technologies Helps Samsung Electronics Successfully Validate FiRa® 2.0 Safe Distance Measurement Test Case
- From probes to power supplies, Tektronix is leading the way in comprehensive innovation in power electronics testing
- Seizing the Opportunities in the Chinese Application Market: NI's Challenges and Answers
- Tektronix Launches Breakthrough Power Measurement Tools to Accelerate Innovation as Global Electrification Accelerates
- Not all oscilloscopes are created equal: Why ADCs and low noise floor matter
- Enable TekHSI high-speed interface function to accelerate the remote transmission of waveform data
- How to measure the quality of soft start thyristor
- How to use a multimeter to judge whether a soft starter is good or bad
- What are the advantages and disadvantages of non-contact temperature sensors?
- Innolux's intelligent steer-by-wire solution makes cars smarter and safer
- 8051 MCU - Parity Check
- How to efficiently balance the sensitivity of tactile sensing interfaces
- What should I do if the servo motor shakes? What causes the servo motor to shake quickly?
- 【Brushless Motor】Analysis of three-phase BLDC motor and sharing of two popular development boards
- Midea Industrial Technology's subsidiaries Clou Electronics and Hekang New Energy jointly appeared at the Munich Battery Energy Storage Exhibition and Solar Energy Exhibition
- Guoxin Sichen | Application of ferroelectric memory PB85RS2MC in power battery management, with a capacity of 2M
- Analysis of common faults of frequency converter
- In a head-on competition with Qualcomm, what kind of cockpit products has Intel come up with?
- Dalian Rongke's all-vanadium liquid flow battery energy storage equipment industrialization project has entered the sprint stage before production
- Allegro MicroSystems Introduces Advanced Magnetic and Inductive Position Sensing Solutions at Electronica 2024
- Car key in the left hand, liveness detection radar in the right hand, UWB is imperative for cars!
- After a decade of rapid development, domestic CIS has entered the market
- Aegis Dagger Battery + Thor EM-i Super Hybrid, Geely New Energy has thrown out two "king bombs"
- A brief discussion on functional safety - fault, error, and failure
- In the smart car 2.0 cycle, these core industry chains are facing major opportunities!
- The United States and Japan are developing new batteries. CATL faces challenges? How should China's new energy battery industry respond?
- Murata launches high-precision 6-axis inertial sensor for automobiles
- Ford patents pre-charge alarm to help save costs and respond to emergencies
- New real-time microcontroller system from Texas Instruments enables smarter processing in automotive and industrial applications
- 【i.MX6ULL】Driver Development 11——LCD Driver Practice
- Microcontroller interview question collection
- HEF4051 is easy to damage
- Microchip Automotive Innovation Series Online Seminar Invites You to Attend!
- [STM32WB55 review]——by damiaa
- pt2262/pt2272 codec
- 【DIY Creative LED】WS2812 test successful
- RISC-V MCU Development (XII): Command Line Operations
- [Qinheng RISC-V core CH582] CH582 wired keyboard to Bluetooth keyboard
- GD32 pin PWM output stops level issue