A pH meter is a commonly used instrument and equipment, generally used to measure the hydrogen ion concentration in a liquid, and can determine whether it is acidic, neutral or alkaline. Mainly used in environmental protection, sewage treatment, medicine, chemical industry and other fields. However, errors often occur during the pH measurement process, so how to achieve accurate and efficient pH measurement? Galen Zhang, an engineer from Excelpoint, a technical authorized agent, gave a detailed introduction to the ADI pH meter application solution based on the electrode method principle.
pH measurement principle
The pH value is a measure of the relative amounts of hydrogen ions and hydroxide ions in an aqueous solution. In terms of molar concentration, water at 25°C contains 1×10^−7mol/L hydrogen ions, and the hydroxide ion concentration is the same. A neutral solution is a solution in which the concentration of hydrogen ions is exactly equal to the concentration of hydroxide ions. pH is another way of expressing hydrogen ion concentration and is defined as follows:
Therefore, if the hydrogen ion concentration is 1×10^−2mol/L, the pH value is 2.00. PH electrodes are electrochemical sensors used in many industries and are of particular importance to the water treatment and sewage industries. The pH electrode consists of a glass measuring electrode and a reference electrode, similar to a battery. When the electrode is placed in a solution, the measuring electrode generates a voltage that depends on the activity of hydrogen ions in the solution, and this voltage is then compared to the potential of the reference electrode. As the acidity of the solution increases (the pH value becomes lower), the potential of the glass electrode increases positively (+mV) relative to the reference electrode; as the alkalinity of the solution increases (the pH value becomes higher), the potential of the glass electrode becomes positive relative to the reference electrode Negative enhancement (-mV). The difference between these two electrodes is the measured potential. Under ideal conditions, a typical pH electrode would produce 59.154 mV/PH unit at 25°C, which is expressed using the Nernst equation as:
in:
E = Hydrogen electrode voltage, activity unknown
α= ±30 mV, zero point tolerance
T = ambient temperature (unit: °C)
n = 1 (25 °C), valence (number of charges on the ion)
F = 96485 coulombs/mol, Faraday’s constant
R = 8.314 volt-coulomb/°K mol, Avogadro's number
PH = hydrogen ion concentration of unknown solution
PHISO = 7, reference hydrogen ion concentration
The equations show that the voltage produced depends on the acidity and alkalinity of the solution and varies with hydrogen ion activity in a known way. Changes in the temperature of a solution change its hydrogen ion activity. When a solution is heated, the hydrogen ions move faster, resulting in an increase in the potential difference between the two electrodes. Additionally, as the solution cools, the hydrogen activity decreases, causing the potential difference to decrease. By design, the electrode will ideally develop a potential of zero volts when placed in a buffer solution with a pH of 7.
pH calibration
The characteristics of pH electrodes change over time due to electrode coating and aging. Therefore, a calibration procedure is required to obtain the highest accuracy. Calibration is accomplished by measuring the pH of two buffer solutions, each with a known pH. The software includes NIST lookup tables for buffer solutions with different pH values, as well as temperature-corrected pH values from 0°C to 95°C. The solution temperature was measured using a resistance temperature detector (RTD). Use the following linear equation:
Determine the actual slope of the pH sensor transfer function and measure the actual offset voltage. To calculate the slope, solve the following equation:
in:
y1 is the measured voltage at the first point.
y2 is the measured voltage at the second point.
x1 is the known pH value of the first point.
x2 is the known pH value of the second point.
Taking the above measurements and substituting a calibration point into Equation 2, the unknown pH value can be determined according to the following final equation:
in:
x is the unknown pH value.
y is the measured voltage.
b is the measured offset voltage.
m is the slope.
Equation 3 can then be used to adjust the values given by the Nernst equation described previously.
Temperature compensation in pH measurement
When measuring the pH of a solution, one of the most important parameters to consider is the temperature change. When the temperature of a solution changes, the pH of the solution also changes appreciably. This changed value is not an error in the pH reading, but the true pH of the solution at the new temperature. Temperature changes can cause changes in the sensitivity of the measuring electrode, causing measurement errors. This error is predictable and can be addressed by electrode calibration over the full temperature range and temperature correction during subsequent measurements. The ideal electrode is an electrode that can be accurately zeroed at pH=7. At pH=7, the effect of temperature on electrode sensitivity is negligible. However, most pH electrodes are not ideal electrodes and have electrode sensitivity issues due to temperature changes. The general temperature error is very close to 0.003 PH/℃/number of PH units away from PH=7. In this case, the pH meter must be calibrated to apply this correction factor of 0.003. This compensation can be achieved using a calibrated temperature sensor. The temperature sensor can then tell you about changes in temperature, if any. If there is a change, enter the correction factor reading of "0.003 pH/℃/number of pH units from pH=7" into the final pH reading, and the pH meter will be able to display a corrected and more accurate reading. This mechanism is able to well compensate for pH errors caused by temperature changes.
pH measurement solution
Figure 1. ADI pH meter solution block diagram
Solution description
pH measurement
In the ADI pH meter solution, the system is divided into two independent measurement front ends: pH value and temperature. After signal conditioning, the 2 channels share a 24-bit Σ-Δ analog-to-digital converter (ADC) AD7124-4 or AD4130-8.
The AD7124-4 is a low power, low noise, fully integrated analog front end suitable for high-precision measurement applications. The device contains a low-noise 24-bit Σ-Δ ADC that can be configured to provide 4 differential inputs or 7 single-ended or pseudo-differential inputs. The on-chip gain stage ensures that small signals can be input directly into the ADC. Current power consumption, output data rate range and rms noise can all be customized through the selected power mode. The device also offers multiple filter options, ensuring greater flexibility for the user. The AD7124-4 achieves simultaneous 50 Hz and 60 Hz rejection at an output data rate of 25 SPS (single cycle settling), and can achieve over 80 dB of rejection at lower output data rates.
The AD7124-4 provides a high level of signal chain integration. The device contains a precision low-noise, low-drift internal bandgap reference, or an internally buffered external differential reference can be used. Other key integrated features include a programmable low-drift excitation current source, open-circuit test current control, and a bias voltage generator that sets the common-mode voltage of a channel to AVDD/2. A low-side power switch allows the user to turn off the bridge sensor between conversions, ensuring low system power consumption. The device also allows the user to operate from an internal or external clock.
The AD4130-8 is an ultra-low power, high-precision measurement solution for applications that operate on low-bandwidth batteries. Fully integrated analog front end (AFE) includes multiplexers for up to 16 single-ended or 8 differential inputs, programmable gain amplifier (PGA), 24-bit Σ-Δ (Σ-Δ) analog-to-digital conversion (ADC), on-chip voltage reference and oscillator, selectable filter options, intelligent timing controller, sensor bias and excitation options, diagnostics, and newly added features to improve battery life (one coin cell battery Available for over 5 years), first-in-first-out (FIFO) buffer and duty cycle.
With the AD4130-8, the user can measure low frequency signals with current consumption of 28.5µA (gain = 1) and 32.5µA (gain = 128) during continuous conversion, and even lower when using one of the duty cycle options. The average current is measured. The AD4130-8 can be configured with 8 differential inputs or 16 single-ended or pseudo-differential inputs, which are connected to a crosspoint multiplexer where any input pair can become a measurement channel input for the PGA and ADC.
The AD4130-8 provides the following key analog features to enable simple and efficient interfacing to sensors used to measure temperature, load, and pressure:
PGA. Due to programmable gain (from 1 to 128) and high input impedance with low input current, PGA allows direct interface with sensors with low output amplitude, such as resistor bridges, thermocouples and resistance temperature detection (RTD).
Capacitive PGAs support a full common-mode input range, giving designers more leeway for widely varying input common modes. The wider common-mode input range improves overall resolution and is very effective in ratiometric measurements.
Low drift precision current source. The IEXC0 and IEXC1 current sources can be used to excite 2-wire, 3-wire, and 4-wire RTDs. Excitation current output options include 100nA, 10µA, 20µA, 50µA, 100µA, 150µA and 200µA.
A low-side power switch (PDSW) can be used to turn off the bridge sensor between transitions. PDSW can be controlled within the timing controller on a per-channel basis, allowing the overall system to achieve optimal timing and energy savings. PDSW also supports the use of higher power analog sensors in low power systems.
Previous article:Event preview press release: imc advanced measurement technology helps evaluate vehicle dynamics
Next article:FLIR launches acoustic imager to help quickly locate gas leaks and mechanical failures
Recommended ReadingLatest update time:2024-11-22 14:30
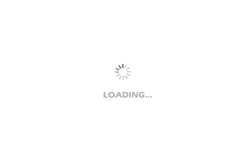
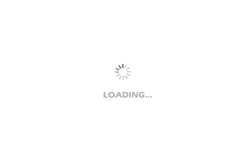
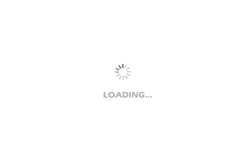
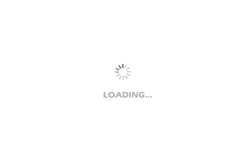
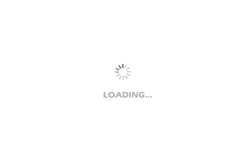
- New IsoVu™ Isolated Current Probes: Bringing a New Dimension to Current Measurements
- Modern manufacturing strategies drive continuous improvement in ICT online testing
- Methods for Correlation of Contact and Non-Contact Measurements
- Keysight Technologies Helps Samsung Electronics Successfully Validate FiRa® 2.0 Safe Distance Measurement Test Case
- From probes to power supplies, Tektronix is leading the way in comprehensive innovation in power electronics testing
- Seizing the Opportunities in the Chinese Application Market: NI's Challenges and Answers
- Tektronix Launches Breakthrough Power Measurement Tools to Accelerate Innovation as Global Electrification Accelerates
- Not all oscilloscopes are created equal: Why ADCs and low noise floor matter
- Enable TekHSI high-speed interface function to accelerate the remote transmission of waveform data
- Intel promotes AI with multi-dimensional efforts in technology, application, and ecology
- ChinaJoy Qualcomm Snapdragon Theme Pavilion takes you to experience the new changes in digital entertainment in the 5G era
- Infineon's latest generation IGBT technology platform enables precise control of speed and position
- Two test methods for LED lighting life
- Don't Let Lightning Induced Surges Scare You
- Application of brushless motor controller ML4425/4426
- Easy identification of LED power supply quality
- World's first integrated photovoltaic solar system completed in Israel
- Sliding window mean filter for avr microcontroller AD conversion
- What does call mean in the detailed explanation of ABB robot programming instructions?
- RAQ #223: How to measure and determine soft-start timing without a soft-start equation?
- RAQ #223: How to measure and determine soft-start timing without a soft-start equation?
- GigaDevice's full range of automotive-grade SPI NOR Flash GD25/55 wins ISO 26262 ASIL D functional safety certification
- GigaDevice's full range of automotive-grade SPI NOR Flash GD25/55 wins ISO 26262 ASIL D functional safety certification
- New IsoVu™ Isolated Current Probes: Bringing a New Dimension to Current Measurements
- New IsoVu™ Isolated Current Probes: Bringing a New Dimension to Current Measurements
- Infineon Technologies Launches ModusToolbox™ Motor Kit to Simplify Motor Control Development
- Infineon Technologies Launches ModusToolbox™ Motor Kit to Simplify Motor Control Development
- STMicroelectronics IO-Link Actuator Board Brings Turnkey Reference Design to Industrial Monitoring and Equipment Manufacturers
- Melexis uses coreless technology to reduce the size of current sensing devices
- EEWORLD University - How to draw a high-end PCB ruler with Altium20
- A very good article, those who learn Verilog can take a good look at it
- Atmel introduces first product in ARM9 microcontroller family
- How to turn off MPLAB XIDE's code optimization function
- Let's take a look at the application of TI products in Meizu fast charging mobile power bank
- IoT Smart Parking Solutions
- Small and exquisite screenshot software
- EPWM1 A and B pulses are not complementary
- Find the parameters of the low-pass filter
- Bone vibration sensor and high-quality voice calls (including working principles)