introduction
Controller Area Network (CAN) is a bus-type serial communication network designed by Bosch of Germany for automobile monitoring systems. It has good networking flexibility, openness, scalability and compatibility, strong anti-interference, self-diagnosis, self-monitoring and error correction capabilities, high reliability, simple protocol model structure, good real-time performance, high cost performance and easy development. It is currently the only field bus with international standards, and its application range has far exceeded automobile monitoring systems. It is suitable for distributed automatic control systems in many fields, such as industrial process control and automation, intelligent structure and distributed management, etc., and has become a field bus with great potential for popularization and application.
In order to facilitate the popularization and application of CAN bus in different fields, a universal simulation platform of the basic component unit of CAN bus system - node is developed. Through simulation, the cost and cycle of research and development of CAN bus system can be reduced, which is of great practical application value.
This simulation platform uses Philips' SJA1000 chip as the CAN controller. In addition to all the functions of the basic CAN PCA82C200 chip standard mode, it adds a new working mode - PeliCAN mode. This mode supports the CAN2.0B protocol with many new features, such as: stronger compatibility and scalability, stronger error detection and correction capabilities, support for hot plugging, etc. The design is more convenient and flexible, and the chip is inexpensive, making it very suitable for use as a general CAN bus system node simulation platform.
In order to meet the needs of automatic control system simulation in various fields, ordinary PCs can be used as simulators for sensors, actuators, human-machine key controls and display interfaces of various automatic control systems to form a simulation platform and improve the versatility, flexibility and scalability of nodes. Various application systems can be simulated through simulation PCs.
Hardware Design of Simulation Platform
The hardware system block diagram of the designed CAN bus system node simulation platform is shown in Figure 1.
Figure 1 CAN bus system node simulation platform
The bus system uses low-cost and easy-to-install twisted pair as the communication medium to connect each node into a network system. Each node consists of four functional modules: CAN controller, CAN transceiver, microprocessor and simulation PC.
The CAN controller SJA1000 is the core and executes the CAN protocol, including data framing and deframing, frame sending and receiving, etc.
Since the bus driving capability of SJA1000 is limited, it is connected to the physical bus through the CAN transceiver PCA82C250 chip. The CAN transceiver converts the logic level signal from the CAN controller into a logic level signal suitable for transmission on the CAN bus and can be received by the CAN transceiver, which plays a role in resisting instantaneous interference and radio frequency interference, increasing the communication distance and protecting the bus. In order to further enhance the anti-interference capability, a high-speed optocoupler 6N137 can be used between SJA1000 and PCA82C250 to achieve level isolation between each CAN node on the bus.
The CAN controller and transceiver work together to complete the communication protocol functions of the physical layer and data link layer in the CAN protocol. The microprocessor 89C51 controls the functions of the SJA1000, including initialization and monitoring management, realizes data transmission and reception communication, and executes application layer functions.
The simulation PC realizes level conversion and communication with the microprocessor through the serial port chip MAX232, thereby realizing communication with the CAN bus. The PC can be used as a simulator for sensors, actuators, and human-machine keying and display interfaces of various automatic control systems to form a simulation platform and improve the versatility, flexibility and scalability of the node. Various application systems can be simulated through the simulation PC. [page]
Software design of simulation platform (Figure 2)
The software design mainly involves application programming of the microprocessor, initialization of SJA1000 (including the setting of initial values of working mode, filter, interrupt enable register, etc.), monitoring management and key display. The microprocessor adopts interrupt working mode to improve the response speed and support the real-time performance of the system. The interrupt flow is shown in Figure 2.
Figure 2 Interrupt flow chart
The core of software design is the data communication between the microprocessor and the CAN controller. Finally, data communication between CAN network nodes is realized. The programming adopts modularization, which is convenient for modification, upgrading and debugging, and supports system flexibility, openness and scalability.
summary
The CAN bus system node simulation platform based on SJA1000 in this paper has been tested and found to be able to correctly send and receive data between two nodes, and realize the communication between the node and the simulation PC, as well as key input, data display and other functions. Its hardware structure is simple and inexpensive, and its software is flexible, easy to modify, upgrade and further develop networking, etc. Various application systems can be simulated through the simulation PC. Through simulation, the cost and cycle of research and development of the CAN bus system are reduced. This simulation platform provides convenient research and development conditions for the promotion and application of the CAN bus system in the automatic control system of automobiles and other different fields, and provides a useful reference example for the popularization and improvement of CAN.
Previous article:CDMA mobile phone network access test laboratory test requirements and methods
Next article:Solution of intrusion detection system based on data mining technology
Recommended ReadingLatest update time:2024-11-16 18:07
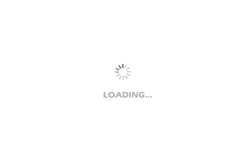
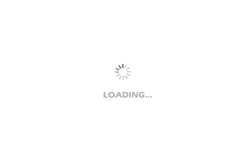
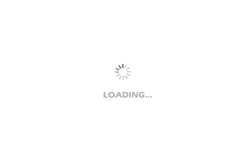
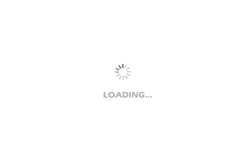
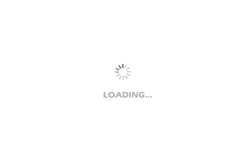
- Popular Resources
- Popular amplifiers
-
New Energy Vehicle Control System Inspection and Maintenance (Edited by Bao Pili)
-
Detailed explanation of big data technology system: principles, architecture and practice (Dong Xicheng)
-
Automotive CAN embedded intrusion detection system based on deep learning
-
Lightweight FPGA-based IDS-ECU architecture for automotive CAN networks
- Keysight Technologies Helps Samsung Electronics Successfully Validate FiRa® 2.0 Safe Distance Measurement Test Case
- From probes to power supplies, Tektronix is leading the way in comprehensive innovation in power electronics testing
- Seizing the Opportunities in the Chinese Application Market: NI's Challenges and Answers
- Tektronix Launches Breakthrough Power Measurement Tools to Accelerate Innovation as Global Electrification Accelerates
- Not all oscilloscopes are created equal: Why ADCs and low noise floor matter
- Enable TekHSI high-speed interface function to accelerate the remote transmission of waveform data
- How to measure the quality of soft start thyristor
- How to use a multimeter to judge whether a soft starter is good or bad
- What are the advantages and disadvantages of non-contact temperature sensors?
- Innolux's intelligent steer-by-wire solution makes cars smarter and safer
- 8051 MCU - Parity Check
- How to efficiently balance the sensitivity of tactile sensing interfaces
- What should I do if the servo motor shakes? What causes the servo motor to shake quickly?
- 【Brushless Motor】Analysis of three-phase BLDC motor and sharing of two popular development boards
- Midea Industrial Technology's subsidiaries Clou Electronics and Hekang New Energy jointly appeared at the Munich Battery Energy Storage Exhibition and Solar Energy Exhibition
- Guoxin Sichen | Application of ferroelectric memory PB85RS2MC in power battery management, with a capacity of 2M
- Analysis of common faults of frequency converter
- In a head-on competition with Qualcomm, what kind of cockpit products has Intel come up with?
- Dalian Rongke's all-vanadium liquid flow battery energy storage equipment industrialization project has entered the sprint stage before production
- Allegro MicroSystems Introduces Advanced Magnetic and Inductive Position Sensing Solutions at Electronica 2024
- Car key in the left hand, liveness detection radar in the right hand, UWB is imperative for cars!
- After a decade of rapid development, domestic CIS has entered the market
- Aegis Dagger Battery + Thor EM-i Super Hybrid, Geely New Energy has thrown out two "king bombs"
- A brief discussion on functional safety - fault, error, and failure
- In the smart car 2.0 cycle, these core industry chains are facing major opportunities!
- The United States and Japan are developing new batteries. CATL faces challenges? How should China's new energy battery industry respond?
- Murata launches high-precision 6-axis inertial sensor for automobiles
- Ford patents pre-charge alarm to help save costs and respond to emergencies
- New real-time microcontroller system from Texas Instruments enables smarter processing in automotive and industrial applications
- Okay, let’s talk about the Internet of Things technology protocol
- On-line debugging method for embedded processors
- PCB issues for switching power supplies
- [Zero-knowledge ESP8266 tutorial] Quick start 21 world clock demo
- A question about the schematic
- National College Student Electronic Design Competition Open Source Flight Control Data Album: APM Learning Materials
- How to modify this PCB
- Annual review: 2019 TI training course highlights, good reviews and gifts!
- Which development environment do I use for C8051F58x/F59x?
- C2000 CLA FAQ: Accessing Peripherals