Real-time testing technology
A common real-time testing technique is to use closed-loop control to automatically manipulate physical variables in the test system, such as temperature, position, torque, or acceleration. For example, to implement an environmental test system, such as a pressure chamber, in addition to providing stimulus to the unit under test (UUT) and observing its response, the test chamber must also achieve these functions when a specific state is reached. Because the pressure in the chamber is affected by many factors, such as chamber leaks or changes in the characteristics of the UUT, test engineers must use a closed-loop control algorithm to monitor the value of the pressure sensor and automatically adjust the control signals of the compressor and safety valve to make the real-time pressure curve consistent with the requirements of the test plan. To achieve such automatic control, the closed-loop control system must detect the system status and adjust the control command within a certain time interval.
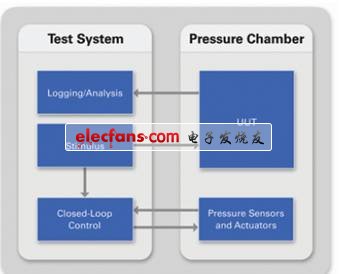
Figure 1 Real-time test systems such as pressure chambers use closed-loop control systems to automatically achieve the pressure conditions required for the test plan.
Another example is hardware-in-the-loop testing. This real-time testing application can more effectively test electronic control systems. An electronic control system consists of an electronic control unit (ECU) and the system or environment it controls.
When testing an electronic control system, it may not be possible to perform all the required tests on a complete system due to considerations such as safety, system realizability or cost. However, due to the closed-loop coupling between the ECU and the rest of the system, it is impossible to fully test the performance of the electronic control unit without using a complete system.
Hardware-in-the-loop simulation uses software models that represent the rest of the system to simulate the interaction of sensors and actuators between the control unit under test and the rest of the system. It can create a virtual environment for the ECU, maintaining the closed-loop coupling within the system. In order to accurately simulate the interaction of sensors and actuators, the test system must perform the calculations of the model with high determinism at continuous or deterministic time intervals.
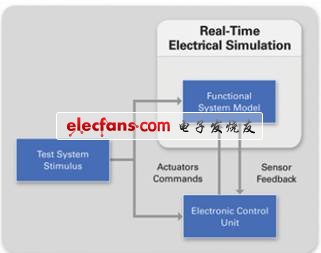
Figure 2 Hardware-in-the-loop testing (HIL) is a real-time testing technique that uses software to simulate missing system components to complete the testing of electronic control equipment.
The evolution of real-time testing (RTT) systems
To meet these challenges, real-time test systems need to integrate multiple functions so that the resulting system can simultaneously meet multiple requirements that were previously implemented by multiple independent real-time test applications.
This trend is best reflected in the emergence of model-based dynamometers. Typically, a dynamometer test system includes a real-time test application that uses a proportional-integral-derivative (PID) control algorithm to generate different load and speed conditions for the UUT. The test system applies static excitation curves to the PID controller and the UUT to exercise and verify the device. Model-based dynamometer systems have evolved from traditional dynamometers and use models to execute advanced control algorithms and generate dynamic excitation curves.
Wineman Technologies engineers used the NI RTT platform to produce a six-wheel independent chassis dynamometer system. In order to fully test their vehicles, the dynamometer needed to be able to generate different test conditions so that it could simulate the vehicle driving on different terrains.
To implement this test system, engineers needed to combine their experience implementing dynamometers and HIL simulators to create a test system that had more features than traditional dynamometer test systems, but that were more common in HIL test systems. Specifically, they had to deterministically implement complex models to provide dynamic excitation to generate six related speed/torque curves and implement advanced control to accomplish this task.
The integration of real-time testing requirements can also be seen in the application of RobotikerTecnalia, a European research institute. In their research and development of hybrid electric vehicle (HEV) powertrain systems, engineers used NI's real-time test platform to build a dedicated HIL test system.
Rather than fully electrically simulating the interaction of the vehicle’s sensors and actuators with the ECU, they replaced the software model of the powertrain’s traction drive with actual electromechanical components. These components were then closed-loop connected to the software model simulating the rest of the vehicle, resulting in a more accurate and flexible test system (see Figure 3).
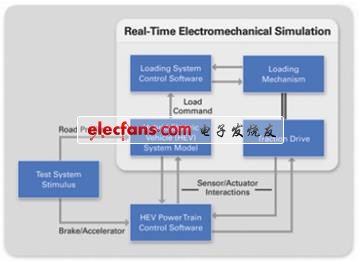
Figure 3. Mechanical components are added to HIL simulation to help more efficiently develop and validate HEV powertrain systems.
Consumer expectations, regulatory agencies, and competitive pressures are driving products to achieve more and more complex functionality at an increasingly rapid pace. As companies try to balance the surging complexity requirements with shorter development cycles, higher reliability requirements, and unchanged or even reduced budgets, real-time testing technology is becoming increasingly important in the development process.
The development of advanced technology is changing with each passing day, and precision testing technology should adapt to this development. The role of precision testing technology in mechanical disciplines is to serve the advanced manufacturing industry and shoulder the heavy responsibility of quality technology assurance. This requires that we must first take improving product quality as the starting point, which is also the most important goal to be achieved. Secondly, real-time testing technology should improve the production efficiency of products. Therefore, the detection method must be able to adapt to the requirements of rapid development of production, and cannot be tested simply for the sake of detection, and the production efficiency must not be affected by the requirements of detection. From a more positive perspective, it should be due to the good service of precision testing technology to promote the improvement of production capacity. According to the requirements of the development of advanced manufacturing technology and the development laws of precision testing technology itself, new measurement principles and testing methods are constantly being expanded.
Previous article:DS1620 pin diagram and temperature measurement principle
Next article:The whole process of designing and making the voltmeter + ammeter LCD panel
- Popular Resources
- Popular amplifiers
- Keysight Technologies Helps Samsung Electronics Successfully Validate FiRa® 2.0 Safe Distance Measurement Test Case
- From probes to power supplies, Tektronix is leading the way in comprehensive innovation in power electronics testing
- Seizing the Opportunities in the Chinese Application Market: NI's Challenges and Answers
- Tektronix Launches Breakthrough Power Measurement Tools to Accelerate Innovation as Global Electrification Accelerates
- Not all oscilloscopes are created equal: Why ADCs and low noise floor matter
- Enable TekHSI high-speed interface function to accelerate the remote transmission of waveform data
- How to measure the quality of soft start thyristor
- How to use a multimeter to judge whether a soft starter is good or bad
- What are the advantages and disadvantages of non-contact temperature sensors?
- Innolux's intelligent steer-by-wire solution makes cars smarter and safer
- 8051 MCU - Parity Check
- How to efficiently balance the sensitivity of tactile sensing interfaces
- What should I do if the servo motor shakes? What causes the servo motor to shake quickly?
- 【Brushless Motor】Analysis of three-phase BLDC motor and sharing of two popular development boards
- Midea Industrial Technology's subsidiaries Clou Electronics and Hekang New Energy jointly appeared at the Munich Battery Energy Storage Exhibition and Solar Energy Exhibition
- Guoxin Sichen | Application of ferroelectric memory PB85RS2MC in power battery management, with a capacity of 2M
- Analysis of common faults of frequency converter
- In a head-on competition with Qualcomm, what kind of cockpit products has Intel come up with?
- Dalian Rongke's all-vanadium liquid flow battery energy storage equipment industrialization project has entered the sprint stage before production
- Allegro MicroSystems Introduces Advanced Magnetic and Inductive Position Sensing Solutions at Electronica 2024
- Car key in the left hand, liveness detection radar in the right hand, UWB is imperative for cars!
- After a decade of rapid development, domestic CIS has entered the market
- Aegis Dagger Battery + Thor EM-i Super Hybrid, Geely New Energy has thrown out two "king bombs"
- A brief discussion on functional safety - fault, error, and failure
- In the smart car 2.0 cycle, these core industry chains are facing major opportunities!
- The United States and Japan are developing new batteries. CATL faces challenges? How should China's new energy battery industry respond?
- Murata launches high-precision 6-axis inertial sensor for automobiles
- Ford patents pre-charge alarm to help save costs and respond to emergencies
- New real-time microcontroller system from Texas Instruments enables smarter processing in automotive and industrial applications
- for(i=0;i<120;i++)---What does i mean? Why did the LED stay on after changing from 120 to 500?
- Looking for the library file of 74LS245 in AD9
- Program error please advise
- Qiming Cloud Sharing | What are the differences between Espressif's newly released ESP32-C2 and the ESP32-C3 that went into mass production in May this year?
- TrueStudio flashes STM32 project and prompts Verify failed, and now I am helpless
- Dynamic Near Field Communication (NFC) Type 4B Tag
- [GD32E231 Work Submission] Environmental Radiation Dose Monitoring Equipment Design
- [RVB2601 Creative Application Development] 7. IoT Control
- DM6446 DSP end program optimization
- MPXV2202DP connected to IN132 output abnormality, I don't know how to deal with it