This article introduces when electromagnetic compatibility rectification is needed and common electromagnetic compatibility rectification, and introduces how to successfully pass the electromagnetic compatibility test from three aspects: electromagnetic disturbance emission test, harmonic current test and transient pulse immunity test. 1. Overview
1.1 When is electromagnetic compatibility rectification needed and countermeasures
For an electronic or electrical product, its electromagnetic compatibility should be considered in the design stage, so that the possibility of electromagnetic compatibility problems in the product during the production stage can be reduced to a lower level. However, whether it meets the requirements must ultimately be tested for compliance with electromagnetic compatibility standards through electromagnetic compatibility testing.
Due to the complexity of electromagnetic compatibility, even for a product with relatively comprehensive consideration of electromagnetic compatibility design issues, some electromagnetic interference factors are inevitable during the design and manufacturing process, resulting in the final electromagnetic compatibility test failure. This situation is still relatively common in electromagnetic compatibility testing. Of course,
for the problem of electromagnetic compatibility test failure before the product is finalized, we can completely follow the normal electromagnetic compatibility design ideas, follow the electromagnetic compatibility design specification method and system method, and redesign the product for the electromagnetic compatibility problems. Solve the existing electromagnetic compatibility risks from the source. This belongs to the scope of electromagnetic compatibility design.
At present, the common situation of domestic electronic and electrical products is that when the product is undergoing electromagnetic compatibility type testing, the product design has been finalized, the product shell has been molded, the PCB board has been designed and produced, the component board has been processed, and even the product has been produced and is waiting for shipment.
For the electromagnetic compatibility problems of such products, we can only adopt the problem-solving method of "what problems arise, what problems should be solved" to make the smallest changes to the product to make it meet the electromagnetic compatibility requirements. This belongs to the category of electromagnetic compatibility rectification countermeasures, which is the issue we need to discuss in this course.
1.2 Common electromagnetic compatibility rectification measures
For common electromagnetic compatibility problems, we can generally solve most of the problems by comprehensively adopting the following rectification measures: conductive glue can be applied to the assembly surface of the shield, or conductive pads can be added to the assembly surface, or even conductive metal tape can be used for remediation. The conductive pad can be a braided metal wire, a soft metal with low hardness and easy to shape (copper, lead, etc.), rubber for packaging metal layer, conductive rubber, or comb-shaped reed contact fingers.
Under the premise of not affecting the performance, appropriately adjust the direction and arrangement of the equipment cables to isolate different types of cables from each other. Change ordinary small signal or high frequency signal cables to shielded cables, and change ordinary high current signal or data transmission signal cables to symmetrical twisted cables.
Strengthen the mechanical properties of grounding and reduce grounding resistance. At the same time, there should be a separate low impedance grounding for the entire equipment.
Install or connect a power filter in series on the power input line of the equipment.
When possible, shield and isolate important devices, such as installing a well-grounded metal isolation plate or a small shielding cover.
Connect a small capacitor in parallel to the power input end of each device to bypass the high-frequency interference caused by the power supply.
Below, we will discuss with you the more common problems, solutions and remedial measures in the test process of electromagnetic compatibility test items such as conducted emission, radiated emission, harmonic current, electrostatic discharge, electric fast pulse, surge, etc. for electronic and electrical products.
According to the characteristics of each project, we divide these contents into three categories for discussion:
Electromagnetic disturbance emission: conducted emission, radiated emission
Harmonic current
Transient pulse immunity: electrostatic discharge, electric fast pulse, surge impact
2. Countermeasures and rectification measures for common problems in electromagnetic interference emission testing
For countermeasures and rectification of electromagnetic emission testing, we will discuss in detail in the next topic "Common electromagnetic compatibility problems and countermeasures in 3C certification testing of electronic products" using AV and IT products as examples. Here we will only give some outline introductions and will not discuss them in depth.
2.1 Main electromagnetic interference sources in electronic and electrical products
Switching circuit of equipment switching power supply: the main frequency of the interference source is tens of kHz to hundreds of kHz, and the high-order harmonics can extend to tens of MHz.
Rectification circuit of equipment DC power supply: the upper limit of the power frequency rectification noise can extend to hundreds of kHz; the upper limit of the high-frequency rectification noise frequency can extend to tens of MHz.
Brush noise of DC motor of electric equipment: the upper limit of the noise frequency can extend to hundreds of MHz.
Operation noise of AC motor of electric equipment: high-order harmonics can extend to tens of MHz.
Interference emission of variable frequency speed regulation circuit: the interference source frequency ranges from tens of kHz to tens of MHz.
Switching noise of equipment operation state switching: the upper limit of the noise frequency can extend to hundreds of MHz.
Electromagnetic disturbance of crystal oscillator and digital circuit of intelligent control equipment: the main frequency of disturbance source is tens of kHz to tens of MHz, and the higher harmonics can extend to hundreds of MHz.
Microwave leakage of microwave equipment: the main frequency of disturbance source is several GHz.
Electromagnetic disturbance emission of electromagnetic induction heating equipment: the main frequency of disturbance source is tens of kHz, and the higher harmonics can extend to tens of MHz.
Local oscillator and its harmonics of high-frequency tuning circuit of television electroacoustic receiving equipment: the main frequency of disturbance source is tens of MHz to hundreds of MHz, and the higher harmonics can extend to several GHz.
Digital processing circuit of information technology equipment and various automatic control equipment: the main frequency of disturbance source is tens of MHz to hundreds of MHz, and the higher harmonics can extend to several GHz.
2.2 Disturbance source positioning
2.2.1 Positioning according to measurement curve:
Basis: excessive disturbance frequency range, excessive disturbance frequency domain distribution, narrowband disturbance or broadband disturbance, etc.
Positioning according to the working mode and internal structure of the equipment under test:
Are half-wave rectification and symmetrical/asymmetrical power supply adjustment circuits not recommended by the standard used?
Is the circuit board layout in the internal structure reasonable?
Is the internal cable routing reasonable? Is
the internal filter (filter circuit) installed reasonably?
Is the grounding and bonding method of the internal circuit reasonable?
Does the chassis shielding meet the requirements of the corresponding product?
2.2.2 According to the composition and functional positioning of the device under test:
Is there a secondary power supply inside the device, and how does it work?
Is there a drive motor in the device, and what type of motor?
Is there a variable frequency speed regulation circuit in the device?
Is there a digital control or intelligent control circuit in the device? Is a crystal oscillator used?
Is there a programmable relay or switch circuit in the device?
Does the normal operation of the device use electromagnetic waves or microwaves?
Is there a working wireless transceiver circuit in the device?
2.2.3 Fault location based on the working status of the functional module:
If the various modules of the device can be suspended and resumed
, the source of the interference can be determined by suspending the work of these modules one by one. If the module cannot be suspended and resumed independently, it can be suspended and resumed together with other functional modules of the device to determine the approximate source of the interference.
If the module cannot be suspended and resumed independently, it can be suspended and resumed together with qualified functional modules of other devices to determine the approximate source of the interference.
For modules suspected of exceeding the interference standard, the interference determination can be performed by replacement.
2.3 Problems and countermeasures of excessive continuous conducted emission of electronic and electrical products
The nominal measurement frequency range of continuous conducted interference of household appliances is 148.5kHz-30MHz (actually 150kHz-30MHz).
The measurement is performed on the power terminals, load terminals and additional terminals respectively.
The main sources of continuous conducted interference:
switching frequency and harmonic interference of switching power supply, rectification noise of power rectification circuit,
running noise of AC motor, brush noise of DC motor,
electromagnetic interference of electromagnetic induction heating equipment,
crystal oscillator and digital circuit electromagnetic interference of intelligent control equipment, etc.
When we find the interference source of the exceeding point through the interference positioning method,
we can adopt the corresponding interference suppression measures.
(Explanation on fault location and conducted disturbance sources respectively)
The general power supply end continuous conducted disturbance can be suppressed by the following circuit:
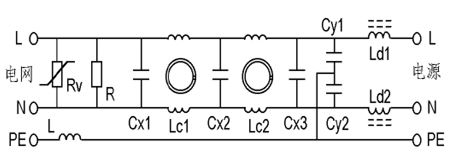
Figure 1: AC power supply filter network
The conducted disturbance of load terminals and additional terminals can be suppressed by the following circuit
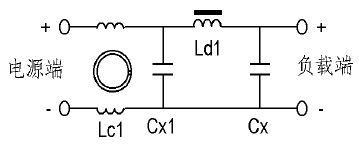
Figure 2: DC output filter network
Whether the suppression measures are taken for the power terminals, load terminals and additional terminals, if independent filters are used, attention should be paid to their installation methods.
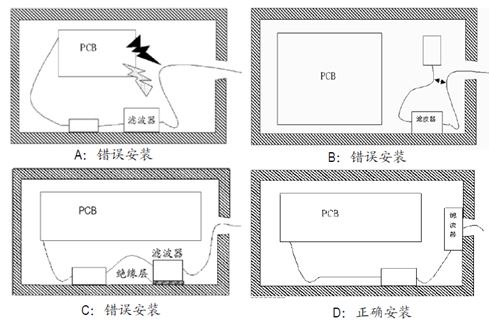
Figure 3: Filter installation method
2.4 Problems and countermeasures of excessive intermittent conducted emissions of electronic and electrical products
The nominal measurement frequency range of intermittent conducted disturbance of household appliances is 148.5kHz-30MHz (actually 150kHz-30MHz).
The measurement is carried out on the power supply terminal, and the frequency points of the click sound measurement are: 150kHz, 500kHz, 1.4MHz, 30MHz.
The main sources of intermittent conducted disturbance:
thermostatic control equipment, program-automatic machines and other electrical control or operation equipment switching operations will produce intermittent disturbance.
Such operations are generally implemented through relays and program-controlled electronic/mechanical switches.
This type of disturbance is generally caused by the contact jitter of relays and switches and the surge shock caused by the switching of non-pure resistance loads.
The corresponding disturbance suppression measures can be adopted mainly for the above two aspects.
2.5 Problems and countermeasures of excessive radiation disturbance of electronic and electrical products
The frequency range of the measurement of radiation disturbance field strength of electronic and electrical products is 30MHz-1000MHz.
The measurement is generally carried out in an open field or a semi-anechoic chamber.
The main sources of radiation disturbance:
switching frequency and harmonic disturbance of
switching power supply Operation noise of AC motor, brush noise of DC motor
Electromagnetic disturbance of electromagnetic induction equipment
Crystal oscillator and digital circuit electromagnetic disturbance of intelligent control equipment, etc.
When we find the disturbance source of the excessive radiation disturbance point through the disturbance positioning method, we can adopt the corresponding disturbance source suppression measures. (Explanation of fault location and disturbance source respectively)
Generally speaking, the first thing to do is to suppress the disturbance source, which can be achieved by optimizing circuit design, circuit structure and layout, strengthening filtering and correct grounding. The second is to cut off the coupling path, which can be achieved through correct housing shielding and transmission line filtering.
3. Common Problems and Corrective Measures for Harmonic Current Testing
For electronic and electrical products powered by AC mains, harmonic current is a very important electromagnetic compatibility measurement item.
The supply voltage of electronic and electrical equipment used in low-voltage mains networks is a sine wave, but its current waveform is not necessarily a sine wave and may have more or less distortion. The application of a large number of such devices will cause the grid voltage waveform to be distorted, which will reduce the quality of grid power.
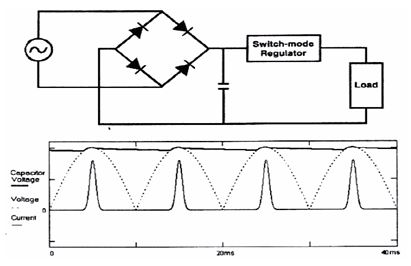
Figure 4: High-voltage rectifier circuit and corresponding distorted current waveform
A periodic function can be decomposed into a Fourier series, expressed as the sum of multiple-level sinusoidal functions, that is, the periodic signal can be regarded as the synthesis of the fundamental wave and higher harmonics of the sinusoidal function.
Therefore, we can decompose the distorted current waveform of the equipment into the fundamental wave and higher harmonics, and measure the higher harmonic content through specific instruments to analyze the degree of distortion of the equipment current waveform. We refer to these higher-order harmonic current components as harmonic currents.
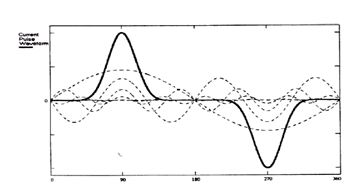
Figure 6: Schematic diagram of Fourier expansion of distorted current waveform
When there is excessive harmonic current in the power grid, it will not only reduce the efficiency of the generator, but also cause damage to the generator and power grid equipment in severe cases. It will also affect the normal operation of the power grid user equipment, such as computer calculation errors and TV screen rollover.
It is precisely for the purpose of protecting the power quality of the shared power grid and ensuring the normal operation of the power grid and user equipment that IEC proposed the harmonic current limit standard.
Harmonic current testing is not suitable for electronic and electrical products powered by low-voltage AC, DC and batteries other than the mains.
3.1 Introduction to measurement standards
The following is a brief introduction to the measurement of harmonic current using the GB17625.1 standard as an example.
Standard name: GB17625.1-2003 idt IEC61000-3-2:2001 "Electromagnetic compatibility limit harmonic current emission limit (equipment input current per phase ≤16A)"
GB17625.1-2003 is an important basis standard for the certification and inspection of many electronic and electrical products. This standard measures and limits the degree of distortion of the power supply current waveform of electronic and electrical products (equipment input current per phase ≤16A) powered by low-voltage mains electricity when in use.
GB17625.1-2003 standard limits the distortion of the equipment current waveform by limiting the size of the high-order harmonic components of the equipment current. GB17625.1 takes into account the 40th harmonic current content.
3.1.1 Scope of application of the standard
This standard only puts forward harmonic current limit requirements for equipment that is connected to a low-voltage power supply system with a frequency of 50Hz/60Hz and a phase voltage of 220V/230V/240V and an input current per phase of no more than 16A.
This standard is a general electromagnetic compatibility standard. There are many product categories that are suitable for this standard, such as household appliances, power tools, electrical lighting equipment, information technology equipment, audio-visual equipment, etc.
3.1.2 Classification of equipment
Classification is carried out according to different harmonic current limits.
Class A: balanced three-phase equipment;
household appliances, excluding equipment listed in Class D;
tools, excluding portable tools;
incandescent lamp dimmers;
audio equipment;
and all other equipment except the following categories of equipment.
Class B: portable tools; arc welding equipment that is not a special equipment
Class C: lighting equipment
Class D: active power not more than 600W The following equipment: personal computers and personal computer monitors; television receivers.
The definitions of Class B, Class C and Class D devices are relatively simple, while the distinction of Class A is relatively complex.
3.1.3 Harmonic current limits
The limits for the following types of equipment are not specified in this standard:
equipment with a rated power of 75W or less, excluding lighting equipment (this value may be reduced from 75W to 50W in the future);
special equipment with a total rated power greater than 1kW;
symmetrically controlled heating elements with a rated power of no more than 200W;
independent dimmers for incandescent lamps with a rated power of no more than 1kW.
(Manufacturers usually use this restriction item to achieve the purpose of exemption from harmonic current restrictions)
3.1.3.1 Harmonic current limits for Class A devices The
harmonic current limits for Class A devices are shown in the corresponding table of the standard. The limits are effective values in amperes. This limit is a fixed value and is not related to the power and fundamental current of the product.
3.1.3.2 Harmonic current limits for Class B devices
The harmonic current limits for Class B devices are 1.5 times the limits for Class A devices.
3.1.3.3 Harmonic current limits for Class C devices
a) Active input power greater than 25W
For lighting appliances with active input power greater than 25W, the harmonic current should not exceed the relevant limits for Class C devices. This limit is not related to the fundamental current of the product.
b) Active input power not greater than 25W
For discharge lamps with active power not greater than 25W, the standard specifies specific eligibility criteria.
3.1.3.4 Harmonic current limits for Class D devices
a) Only odd harmonic currents are limited.
b) Odd harmonic currents must not only comply with the maximum allowable harmonic current, but also comply with the "maximum allowable harmonic current per watt of power".
It can be said that the requirements for Class D devices are relatively strict, but the actual situation is that the harmonic currents of Class D devices are often relatively large.
This regulation is based on the fact that Class D devices are widely used, often run continuously, and are often used simultaneously. With so many Class D devices working at the same time, the impact of the harmonic currents they generate on the power quality of the power grid after synthesis (vector synthesis) cannot be ignored.
3.1.4 Harmonic current measuring instrument
Harmonic measuring equipment generally consists of two parts: a precision power supply unit and a measuring instrument unit.
The power supply unit is required to provide a voltage source with a good waveform, load capacity and flat impedance characteristics to the device under test.
The standard stipulates that the measuring instrument unit must be a discrete Fourier transform (FFT) time domain measuring instrument that can continuously and accurately measure the amplitude, phase angle and other required quantities involved in all harmonics at the same time.
At present, most laboratories use harmonic measuring instruments based on the FFT spectrum analysis principle. The front stage of the measuring instrument is a sampling circuit and an analog-to-digital converter, and the back stage is an FFT analyzer (which can be implemented using a PC).
3.1.5 Test conditions
Reference address:Electromagnetic compatibility testing in design and manufacturing
1.1 When is electromagnetic compatibility rectification needed and countermeasures
For an electronic or electrical product, its electromagnetic compatibility should be considered in the design stage, so that the possibility of electromagnetic compatibility problems in the product during the production stage can be reduced to a lower level. However, whether it meets the requirements must ultimately be tested for compliance with electromagnetic compatibility standards through electromagnetic compatibility testing.
Due to the complexity of electromagnetic compatibility, even for a product with relatively comprehensive consideration of electromagnetic compatibility design issues, some electromagnetic interference factors are inevitable during the design and manufacturing process, resulting in the final electromagnetic compatibility test failure. This situation is still relatively common in electromagnetic compatibility testing. Of course,
for the problem of electromagnetic compatibility test failure before the product is finalized, we can completely follow the normal electromagnetic compatibility design ideas, follow the electromagnetic compatibility design specification method and system method, and redesign the product for the electromagnetic compatibility problems. Solve the existing electromagnetic compatibility risks from the source. This belongs to the scope of electromagnetic compatibility design.
At present, the common situation of domestic electronic and electrical products is that when the product is undergoing electromagnetic compatibility type testing, the product design has been finalized, the product shell has been molded, the PCB board has been designed and produced, the component board has been processed, and even the product has been produced and is waiting for shipment.
For the electromagnetic compatibility problems of such products, we can only adopt the problem-solving method of "what problems arise, what problems should be solved" to make the smallest changes to the product to make it meet the electromagnetic compatibility requirements. This belongs to the category of electromagnetic compatibility rectification countermeasures, which is the issue we need to discuss in this course.
1.2 Common electromagnetic compatibility rectification measures
For common electromagnetic compatibility problems, we can generally solve most of the problems by comprehensively adopting the following rectification measures: conductive glue can be applied to the assembly surface of the shield, or conductive pads can be added to the assembly surface, or even conductive metal tape can be used for remediation. The conductive pad can be a braided metal wire, a soft metal with low hardness and easy to shape (copper, lead, etc.), rubber for packaging metal layer, conductive rubber, or comb-shaped reed contact fingers.
Under the premise of not affecting the performance, appropriately adjust the direction and arrangement of the equipment cables to isolate different types of cables from each other. Change ordinary small signal or high frequency signal cables to shielded cables, and change ordinary high current signal or data transmission signal cables to symmetrical twisted cables.
Strengthen the mechanical properties of grounding and reduce grounding resistance. At the same time, there should be a separate low impedance grounding for the entire equipment.
Install or connect a power filter in series on the power input line of the equipment.
When possible, shield and isolate important devices, such as installing a well-grounded metal isolation plate or a small shielding cover.
Connect a small capacitor in parallel to the power input end of each device to bypass the high-frequency interference caused by the power supply.
Below, we will discuss with you the more common problems, solutions and remedial measures in the test process of electromagnetic compatibility test items such as conducted emission, radiated emission, harmonic current, electrostatic discharge, electric fast pulse, surge, etc. for electronic and electrical products.
According to the characteristics of each project, we divide these contents into three categories for discussion:
Electromagnetic disturbance emission: conducted emission, radiated emission
Harmonic current
Transient pulse immunity: electrostatic discharge, electric fast pulse, surge impact
2. Countermeasures and rectification measures for common problems in electromagnetic interference emission testing
For countermeasures and rectification of electromagnetic emission testing, we will discuss in detail in the next topic "Common electromagnetic compatibility problems and countermeasures in 3C certification testing of electronic products" using AV and IT products as examples. Here we will only give some outline introductions and will not discuss them in depth.
2.1 Main electromagnetic interference sources in electronic and electrical products
Switching circuit of equipment switching power supply: the main frequency of the interference source is tens of kHz to hundreds of kHz, and the high-order harmonics can extend to tens of MHz.
Rectification circuit of equipment DC power supply: the upper limit of the power frequency rectification noise can extend to hundreds of kHz; the upper limit of the high-frequency rectification noise frequency can extend to tens of MHz.
Brush noise of DC motor of electric equipment: the upper limit of the noise frequency can extend to hundreds of MHz.
Operation noise of AC motor of electric equipment: high-order harmonics can extend to tens of MHz.
Interference emission of variable frequency speed regulation circuit: the interference source frequency ranges from tens of kHz to tens of MHz.
Switching noise of equipment operation state switching: the upper limit of the noise frequency can extend to hundreds of MHz.
Electromagnetic disturbance of crystal oscillator and digital circuit of intelligent control equipment: the main frequency of disturbance source is tens of kHz to tens of MHz, and the higher harmonics can extend to hundreds of MHz.
Microwave leakage of microwave equipment: the main frequency of disturbance source is several GHz.
Electromagnetic disturbance emission of electromagnetic induction heating equipment: the main frequency of disturbance source is tens of kHz, and the higher harmonics can extend to tens of MHz.
Local oscillator and its harmonics of high-frequency tuning circuit of television electroacoustic receiving equipment: the main frequency of disturbance source is tens of MHz to hundreds of MHz, and the higher harmonics can extend to several GHz.
Digital processing circuit of information technology equipment and various automatic control equipment: the main frequency of disturbance source is tens of MHz to hundreds of MHz, and the higher harmonics can extend to several GHz.
2.2 Disturbance source positioning
2.2.1 Positioning according to measurement curve:
Basis: excessive disturbance frequency range, excessive disturbance frequency domain distribution, narrowband disturbance or broadband disturbance, etc.
Positioning according to the working mode and internal structure of the equipment under test:
Are half-wave rectification and symmetrical/asymmetrical power supply adjustment circuits not recommended by the standard used?
Is the circuit board layout in the internal structure reasonable?
Is the internal cable routing reasonable? Is
the internal filter (filter circuit) installed reasonably?
Is the grounding and bonding method of the internal circuit reasonable?
Does the chassis shielding meet the requirements of the corresponding product?
2.2.2 According to the composition and functional positioning of the device under test:
Is there a secondary power supply inside the device, and how does it work?
Is there a drive motor in the device, and what type of motor?
Is there a variable frequency speed regulation circuit in the device?
Is there a digital control or intelligent control circuit in the device? Is a crystal oscillator used?
Is there a programmable relay or switch circuit in the device?
Does the normal operation of the device use electromagnetic waves or microwaves?
Is there a working wireless transceiver circuit in the device?
2.2.3 Fault location based on the working status of the functional module:
If the various modules of the device can be suspended and resumed
, the source of the interference can be determined by suspending the work of these modules one by one. If the module cannot be suspended and resumed independently, it can be suspended and resumed together with other functional modules of the device to determine the approximate source of the interference.
If the module cannot be suspended and resumed independently, it can be suspended and resumed together with qualified functional modules of other devices to determine the approximate source of the interference.
For modules suspected of exceeding the interference standard, the interference determination can be performed by replacement.
2.3 Problems and countermeasures of excessive continuous conducted emission of electronic and electrical products
The nominal measurement frequency range of continuous conducted interference of household appliances is 148.5kHz-30MHz (actually 150kHz-30MHz).
The measurement is performed on the power terminals, load terminals and additional terminals respectively.
The main sources of continuous conducted interference:
switching frequency and harmonic interference of switching power supply, rectification noise of power rectification circuit,
running noise of AC motor, brush noise of DC motor,
electromagnetic interference of electromagnetic induction heating equipment,
crystal oscillator and digital circuit electromagnetic interference of intelligent control equipment, etc.
When we find the interference source of the exceeding point through the interference positioning method,
we can adopt the corresponding interference suppression measures.
(Explanation on fault location and conducted disturbance sources respectively)
The general power supply end continuous conducted disturbance can be suppressed by the following circuit:
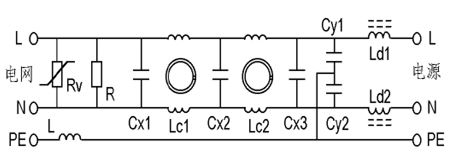
Figure 1: AC power supply filter network
The conducted disturbance of load terminals and additional terminals can be suppressed by the following circuit
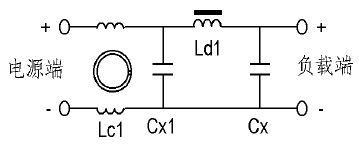
Figure 2: DC output filter network
Whether the suppression measures are taken for the power terminals, load terminals and additional terminals, if independent filters are used, attention should be paid to their installation methods.
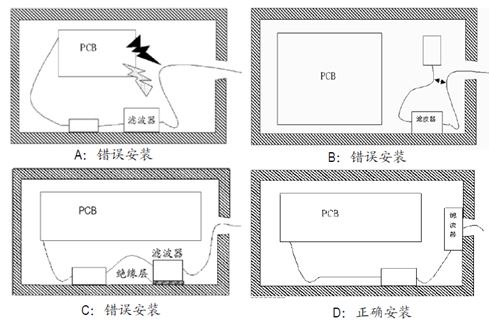
Figure 3: Filter installation method
2.4 Problems and countermeasures of excessive intermittent conducted emissions of electronic and electrical products
The nominal measurement frequency range of intermittent conducted disturbance of household appliances is 148.5kHz-30MHz (actually 150kHz-30MHz).
The measurement is carried out on the power supply terminal, and the frequency points of the click sound measurement are: 150kHz, 500kHz, 1.4MHz, 30MHz.
The main sources of intermittent conducted disturbance:
thermostatic control equipment, program-automatic machines and other electrical control or operation equipment switching operations will produce intermittent disturbance.
Such operations are generally implemented through relays and program-controlled electronic/mechanical switches.
This type of disturbance is generally caused by the contact jitter of relays and switches and the surge shock caused by the switching of non-pure resistance loads.
The corresponding disturbance suppression measures can be adopted mainly for the above two aspects.
2.5 Problems and countermeasures of excessive radiation disturbance of electronic and electrical products
The frequency range of the measurement of radiation disturbance field strength of electronic and electrical products is 30MHz-1000MHz.
The measurement is generally carried out in an open field or a semi-anechoic chamber.
The main sources of radiation disturbance:
switching frequency and harmonic disturbance of
switching power supply Operation noise of AC motor, brush noise of DC motor
Electromagnetic disturbance of electromagnetic induction equipment
Crystal oscillator and digital circuit electromagnetic disturbance of intelligent control equipment, etc.
When we find the disturbance source of the excessive radiation disturbance point through the disturbance positioning method, we can adopt the corresponding disturbance source suppression measures. (Explanation of fault location and disturbance source respectively)
Generally speaking, the first thing to do is to suppress the disturbance source, which can be achieved by optimizing circuit design, circuit structure and layout, strengthening filtering and correct grounding. The second is to cut off the coupling path, which can be achieved through correct housing shielding and transmission line filtering.
3. Common Problems and Corrective Measures for Harmonic Current Testing
For electronic and electrical products powered by AC mains, harmonic current is a very important electromagnetic compatibility measurement item.
The supply voltage of electronic and electrical equipment used in low-voltage mains networks is a sine wave, but its current waveform is not necessarily a sine wave and may have more or less distortion. The application of a large number of such devices will cause the grid voltage waveform to be distorted, which will reduce the quality of grid power.
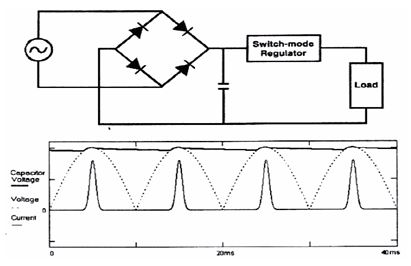
Figure 4: High-voltage rectifier circuit and corresponding distorted current waveform
A periodic function can be decomposed into a Fourier series, expressed as the sum of multiple-level sinusoidal functions, that is, the periodic signal can be regarded as the synthesis of the fundamental wave and higher harmonics of the sinusoidal function.
Therefore, we can decompose the distorted current waveform of the equipment into the fundamental wave and higher harmonics, and measure the higher harmonic content through specific instruments to analyze the degree of distortion of the equipment current waveform. We refer to these higher-order harmonic current components as harmonic currents.
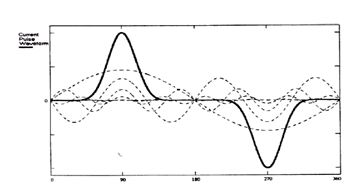
Figure 6: Schematic diagram of Fourier expansion of distorted current waveform
When there is excessive harmonic current in the power grid, it will not only reduce the efficiency of the generator, but also cause damage to the generator and power grid equipment in severe cases. It will also affect the normal operation of the power grid user equipment, such as computer calculation errors and TV screen rollover.
It is precisely for the purpose of protecting the power quality of the shared power grid and ensuring the normal operation of the power grid and user equipment that IEC proposed the harmonic current limit standard.
Harmonic current testing is not suitable for electronic and electrical products powered by low-voltage AC, DC and batteries other than the mains.
3.1 Introduction to measurement standards
The following is a brief introduction to the measurement of harmonic current using the GB17625.1 standard as an example.
Standard name: GB17625.1-2003 idt IEC61000-3-2:2001 "Electromagnetic compatibility limit harmonic current emission limit (equipment input current per phase ≤16A)"
GB17625.1-2003 is an important basis standard for the certification and inspection of many electronic and electrical products. This standard measures and limits the degree of distortion of the power supply current waveform of electronic and electrical products (equipment input current per phase ≤16A) powered by low-voltage mains electricity when in use.
GB17625.1-2003 standard limits the distortion of the equipment current waveform by limiting the size of the high-order harmonic components of the equipment current. GB17625.1 takes into account the 40th harmonic current content.
3.1.1 Scope of application of the standard
This standard only puts forward harmonic current limit requirements for equipment that is connected to a low-voltage power supply system with a frequency of 50Hz/60Hz and a phase voltage of 220V/230V/240V and an input current per phase of no more than 16A.
This standard is a general electromagnetic compatibility standard. There are many product categories that are suitable for this standard, such as household appliances, power tools, electrical lighting equipment, information technology equipment, audio-visual equipment, etc.
3.1.2 Classification of equipment
Classification is carried out according to different harmonic current limits.
Class A: balanced three-phase equipment;
household appliances, excluding equipment listed in Class D;
tools, excluding portable tools;
incandescent lamp dimmers;
audio equipment;
and all other equipment except the following categories of equipment.
Class B: portable tools; arc welding equipment that is not a special equipment
Class C: lighting equipment
Class D: active power not more than 600W The following equipment: personal computers and personal computer monitors; television receivers.
The definitions of Class B, Class C and Class D devices are relatively simple, while the distinction of Class A is relatively complex.
3.1.3 Harmonic current limits
The limits for the following types of equipment are not specified in this standard:
equipment with a rated power of 75W or less, excluding lighting equipment (this value may be reduced from 75W to 50W in the future);
special equipment with a total rated power greater than 1kW;
symmetrically controlled heating elements with a rated power of no more than 200W;
independent dimmers for incandescent lamps with a rated power of no more than 1kW.
(Manufacturers usually use this restriction item to achieve the purpose of exemption from harmonic current restrictions)
3.1.3.1 Harmonic current limits for Class A devices The
harmonic current limits for Class A devices are shown in the corresponding table of the standard. The limits are effective values in amperes. This limit is a fixed value and is not related to the power and fundamental current of the product.
3.1.3.2 Harmonic current limits for Class B devices
The harmonic current limits for Class B devices are 1.5 times the limits for Class A devices.
3.1.3.3 Harmonic current limits for Class C devices
a) Active input power greater than 25W
For lighting appliances with active input power greater than 25W, the harmonic current should not exceed the relevant limits for Class C devices. This limit is not related to the fundamental current of the product.
b) Active input power not greater than 25W
For discharge lamps with active power not greater than 25W, the standard specifies specific eligibility criteria.
3.1.3.4 Harmonic current limits for Class D devices
a) Only odd harmonic currents are limited.
b) Odd harmonic currents must not only comply with the maximum allowable harmonic current, but also comply with the "maximum allowable harmonic current per watt of power".
It can be said that the requirements for Class D devices are relatively strict, but the actual situation is that the harmonic currents of Class D devices are often relatively large.
This regulation is based on the fact that Class D devices are widely used, often run continuously, and are often used simultaneously. With so many Class D devices working at the same time, the impact of the harmonic currents they generate on the power quality of the power grid after synthesis (vector synthesis) cannot be ignored.
3.1.4 Harmonic current measuring instrument
Harmonic measuring equipment generally consists of two parts: a precision power supply unit and a measuring instrument unit.
The power supply unit is required to provide a voltage source with a good waveform, load capacity and flat impedance characteristics to the device under test.
The standard stipulates that the measuring instrument unit must be a discrete Fourier transform (FFT) time domain measuring instrument that can continuously and accurately measure the amplitude, phase angle and other required quantities involved in all harmonics at the same time.
At present, most laboratories use harmonic measuring instruments based on the FFT spectrum analysis principle. The front stage of the measuring instrument is a sampling circuit and an analog-to-digital converter, and the back stage is an FFT analyzer (which can be implemented using a PC).
3.1.5 Test conditions
Previous article:Testing and Inspection in Lead-Free Manufacturing
Next article:S-parameter measurement based on TDR
Recommended Content
Latest Test Measurement Articles
- Keysight Technologies Helps Samsung Electronics Successfully Validate FiRa® 2.0 Safe Distance Measurement Test Case
- From probes to power supplies, Tektronix is leading the way in comprehensive innovation in power electronics testing
- Seizing the Opportunities in the Chinese Application Market: NI's Challenges and Answers
- Tektronix Launches Breakthrough Power Measurement Tools to Accelerate Innovation as Global Electrification Accelerates
- Not all oscilloscopes are created equal: Why ADCs and low noise floor matter
- Enable TekHSI high-speed interface function to accelerate the remote transmission of waveform data
- How to measure the quality of soft start thyristor
- How to use a multimeter to judge whether a soft starter is good or bad
- What are the advantages and disadvantages of non-contact temperature sensors?
MoreSelected Circuit Diagrams
MorePopular Articles
- Innolux's intelligent steer-by-wire solution makes cars smarter and safer
- 8051 MCU - Parity Check
- How to efficiently balance the sensitivity of tactile sensing interfaces
- What should I do if the servo motor shakes? What causes the servo motor to shake quickly?
- 【Brushless Motor】Analysis of three-phase BLDC motor and sharing of two popular development boards
- Midea Industrial Technology's subsidiaries Clou Electronics and Hekang New Energy jointly appeared at the Munich Battery Energy Storage Exhibition and Solar Energy Exhibition
- Guoxin Sichen | Application of ferroelectric memory PB85RS2MC in power battery management, with a capacity of 2M
- Analysis of common faults of frequency converter
- In a head-on competition with Qualcomm, what kind of cockpit products has Intel come up with?
- Dalian Rongke's all-vanadium liquid flow battery energy storage equipment industrialization project has entered the sprint stage before production
MoreDaily News
- Allegro MicroSystems Introduces Advanced Magnetic and Inductive Position Sensing Solutions at Electronica 2024
- Car key in the left hand, liveness detection radar in the right hand, UWB is imperative for cars!
- After a decade of rapid development, domestic CIS has entered the market
- Aegis Dagger Battery + Thor EM-i Super Hybrid, Geely New Energy has thrown out two "king bombs"
- A brief discussion on functional safety - fault, error, and failure
- In the smart car 2.0 cycle, these core industry chains are facing major opportunities!
- The United States and Japan are developing new batteries. CATL faces challenges? How should China's new energy battery industry respond?
- Murata launches high-precision 6-axis inertial sensor for automobiles
- Ford patents pre-charge alarm to help save costs and respond to emergencies
- New real-time microcontroller system from Texas Instruments enables smarter processing in automotive and industrial applications
Guess you like
- Improved logging
- [Image recognition classification & motion detection & analog signal processing system based on Raspberry Pi 400, fifth post] Project conclusion & documentation - 11.0...
- EEWORLD University Hall----Live Replay: ADI - Inertial MEMS Applications
- Using FreeRTOS notification functions to speed up application execution
- 【AT-START-F425 Review】First Look at AT32F425
- Circuit analysis, please help me
- Personal income tax
- Interpretation for you | Introduction to the second version of 5G standard specification R16
- bq4050 protection recovery problem
- Reflections and how to handle them in high-speed systems