For beginners, it is necessary to master the detection methods and experience of commonly used components. Component detection is very familiar to power engineers. It can be said that how to accurately and effectively detect the relevant parameters of components and judge whether the components are normal is not a stereotyped thing. Different methods must be used according to different components to judge whether the components are normal or not. For the basic skill of component detection, this is very familiar to power engineers. It can be said that how to accurately and effectively detect the relevant parameters of components and judge whether the components are normal is not a stereotyped thing. Different methods must be used according to different components to judge whether the components are normal or not. Especially for beginners, it is necessary to master the detection methods and experience of commonly used components. The following introduces the detection experience and methods of commonly used electronic components for reference. Methods for detecting
inductors and transformers Here we first explain the detection of color-coded inductors. The detection method here is that we need to set the multimeter to R×1 gear, and connect the red and black test leads to any lead-out end of the color-coded inductor. At this time, the pointer should swing to the right. According to the measured resistance value, the following three situations can be specifically identified: A. The resistance value of the color-coded inductor under test is zero, and there is a short-circuit fault inside it. B. The DC resistance value of the color-coded inductor under test is directly related to the diameter of the enameled wire used to wind the inductor coil and the number of windings. As long as the resistance value can be measured, the color-coded inductor under test can be considered normal. The following is an explanation of the detection of the intermediate-frequency transformer . A. Set the multimeter to the R×1 position, and check the on-off status of each winding one by one according to the arrangement of the pins of each winding of the intermediate-frequency transformer, and then determine whether it is normal. B. Check the insulation performance. Set the multimeter to the R×10k position and perform the following state tests: (1) The resistance value between the primary winding and the secondary winding; (2) The resistance value between the primary winding and the shell; (3) The resistance value between the secondary winding and the shell. The above test results are divided into three situations: (1) The resistance value is infinite: normal; (2) The resistance value is zero: there is a short-circuit fault; (3) The resistance value is less than infinity, but greater than zero: there is a leakage fault. Power transformer detection A Check whether there are obvious abnormalities by observing the appearance of the transformer. For example, whether the coil lead is broken, desoldering, whether the insulating material has traces of burning, whether the core fastening screw is loose, whether the silicon steel sheet is rusted, whether the winding coil is exposed, etc. B Insulation test. Use the multimeter R×10k block to measure the resistance between the core and the primary, the primary and each secondary, the core and each secondary, the electrostatic shielding layer and the secondary, and the secondary windings. The multimeter pointer should point to the infinite position and not move. Otherwise, it means that the transformer insulation performance is poor. C Coil on-off detection. Set the multimeter to R×1 block. During the test, if the resistance value of a winding is infinite, it means that this winding has a short-circuit fault. D Identify the primary and secondary coils. The primary and secondary pins of the power transformer are generally led out from both sides, and the primary winding is often marked with 220V, while the secondary winding is marked with the rated voltage value, such as 15V, 24V, 35V, etc. Identify based on these marks. E. Detection of no-load current. (a) Direct measurement method. Open all secondary windings, set the multimeter to the AC current range (500mA, and connect the primary winding in series. When the primary winding plug is inserted into the 220V AC mains, the multimeter indicates the no-load current value. This value should not be greater than 10% to 20% of the full-load current of the transformer. Common electronic equipmentThe normal no-load current of the power transformer should be around 100mA. If it exceeds too much, it means that the transformer has a short-circuit fault. (b) Indirect measurement method. Connect a 10/5W resistor in series in the primary winding of the transformer, and the secondary is still completely unloaded. Set the multimeter to the AC voltage range. After power on, use two test leads to measure the voltage drop U across the resistor R, and then use Ohm's law to calculate the no-load current Iempty, that is, Iempty = U/R. F Detection of no-load voltage. Connect the primary of the power transformer to 220V AC power, and use a multimeter to measure the no-load voltage value of each winding (U21, U22, U23, U24) in turn. It should meet the required value. The allowable error range is generally: high-voltage winding ≤±10%, low-voltage winding ≤±5%, and the voltage difference between two sets of symmetrical windings with center taps should be ≤±2%. G Generally, the allowable temperature rise of small-power power transformers is 40℃~50℃. If the quality of the insulating material used is good, the allowable temperature rise can be increased. H detects and distinguishes the same-named ends of each winding. When using a power transformer, sometimes in order to obtain the required secondary voltage, two or more secondary windings can be connected in series. When using a power transformer in series, the same-named ends of each winding participating in the series connection must be connected correctly and cannot be mistaken. Otherwise, the transformer cannot work properly. I.Comprehensive detection and discrimination of short-circuit faults in power transformers. The main symptoms of short-circuit faults in power transformers are severe heating and abnormal output voltage of the secondary winding. Generally, the more short-circuit points there are between turns in the coil, the greater the short-circuit current and the more severe the heating of the transformer. A simple way to detect and determine whether a power transformer has a short-circuit fault is to measure the no-load current (the test method has been introduced earlier). For a transformer with a short-circuit fault, the no-load current value will be much greater than 10% of the full-load current. When the short circuit is serious, the transformer will heat up rapidly within tens of seconds after being powered on at no load, and the iron core will feel hot when touched by hand. At this time, it is not necessary to measure the no-load current to determine that the transformer has a short-circuit point. The detection method of resistors first describes the method for detecting fixed resistors. In the actual component detection operation steps, first connect the two test leads (regardless of positive and negative) to the two end pins of the resistor to measure the actual resistance value. In order to improve the measurement accuracy, the range should be selected according to the nominal value of the measured resistor. Due to the nonlinear relationship of the ohm scale, its middle section is more finely divided, so the pointer indication value should be as close to the middle section of the scale as possible, that is, within the 20% to 80% arc range of the full scale, so as to make the measurement more accurate. According to the different resistance error levels. The reading and the nominal resistance are allowed to have an error of ±5%, ±10% or ±20% respectively. If they do not match and exceed the error range, it means that the resistance value has changed. It should be noted here: when testing, especially when measuring resistors with a resistance of more than tens of kΩ, do not touch the conductive part of the test lead and the resistor with your hands; the resistor to be tested is welded from the circuit, and at least one head must be welded open to prevent other components in the circuit from affecting the test and causing measurement errors; although the resistance value of the color ring resistor can be determined by the color ring mark, it is best to use a multimeter to test its actual resistance value when using it. The method and precautions for detecting cement resistors are exactly the same as those for detecting ordinary fixed resistors. The second main component to be listed below is about the detection of fuse resistors. In circuit design, when the fuse resistor is blown and the circuit is disconnected, a judgment can be made based on experience: if the surface of the fuse resistor is found to be black or burnt, it can be concluded that it is overloaded and the current passing through it exceeds the rated value many times; if there is no trace on its surface and the circuit is open, it indicates that the current flowing through is just equal to or slightly greater than its rated fuse value. To judge whether a fuse resistor without any trace on the surface is good or bad, it can be measured with the help of the multimeter R×1 gear. To ensure accurate measurement, one end of the fuse resistor should be welded off the circuit. If the measured resistance value is infinite, it means that the fuse resistor has failed and the circuit is open. If the measured resistance value is far different from the nominal value, it indicates that the resistance value has changed and it should not be used again. In maintenance practice, it is found that a small number of fuse resistors are short-circuited in the circuit, and attention should also be paid during detection. The third thing we need to test is the potentiometer. When testing the actual circuit components, first turn the handle to see if the handle turns smoothly, whether the switch is flexible, whether the "click" sound is crisp when the switch is on and off, and listen to the friction sound between the internal contact point of the potentiometer and the resistor body. If there is a "rustling" sound, it means that the quality is not good. When testing with a multimeter, first select the appropriate resistance position of the multimeter according to the resistance value of the potentiometer to be tested, and then you can test it according to the following method. A Use the ohm range of the multimeter to measure the two ends of "1" and "2". The reading should be the nominal resistance value of the potentiometer. If the pointer of the multimeter does not move or the resistance value is very different, it indicates that the potentiometer is damaged. B Check whether the movable arm of the potentiometer is in good contact with the resistor. Use the ohm range of the multimeter to measure the two ends of "1" and "2" (or "2" and "3"), and turn the shaft of the potentiometer counterclockwise to a position close to "off". At this time, the smaller the resistance value, the better. Then slowly rotate the shaft handle clockwise, the resistance value should gradually increase, and the pointer in the meter head should move smoothly. When the shaft handle is rotated to the extreme position "3", the resistance value should be close to the nominal value of the potentiometer. If the pointer of the multimeter jumps during the rotation of the shaft handle of the potentiometer, it means that the movable contact has a poor contact fault. The following is about the detection of positive temperature coefficient thermistors and negative temperature coefficient thermistors. First, when testing the positive temperature coefficient thermistor, use the multimeter R×1 gear, which can be divided into two steps: A normal temperature detection (indoor temperature is close to 25℃); touch the two pins of the PTC thermistor with two test leads to measure its actual resistance value, and compare it with the nominal resistance value. The difference between the two is within ±2Ω, which is normal. If the actual resistance value is too different from the nominal resistance value, it means that its performance is poor or it is damaged. B. Heating test: On the basis of normal test at room temperature, the second step of test - heating test can be carried out. A heat source (such as a soldering iron) is placed close to the PTC thermistor to heat it, and a multimeter is used to monitor whether its resistance value increases with the increase of temperature. If so, it means that the thermistor is normal. If the resistance value does not change, it means that its performance has deteriorated and it cannot be used. Be careful not to make the heat source too close to the PTC thermistor or directly contact the thermistor to prevent it from being burned. The method of measuring the nominal resistance value Rt of the negative temperature coefficient thermistor using a multimeter to measure the NTC thermistor is the same as the method of measuring ordinary fixed resistors, that is, according to the nominal resistance value of the NTC thermistor, the appropriate resistance block can be selected to directly measure the actual value of Rt. However, because the NTC thermistor is very sensitive to temperature, the following points should be noted during the test: ARt is measured by the manufacturer at an ambient temperature of 25°C, so when measuring Rt with a multimeter, it should also be carried out when the ambient temperature is close to 25°C to ensure the credibility of the test. B The measured power must not exceed the specified value to avoid measurement errors caused by the thermal effect of the current. C Pay attention to correct operation. During the test, do not pinch the thermistor body with your hands to prevent the body temperature from affecting the test. (2) Estimation of temperature coefficient αt First measure the resistance value Rt1 at room temperature t1, then use an electric soldering iron as a heat source, close to the thermistor Rt, measure the resistance value RT2, and use a thermometer to measure the average temperature t2 of the thermistor RT surface at this time before calculating. Detection of varistor and photoresistor. First of all, the varistor needs to use the R×1k block of the multimeter to measure the forward and reverse insulation resistance between the two pins of the varistor. Both are infinite, otherwise, it means that the leakage current is large. If the measured resistance is very small, it means that the varistor is damaged and cannot be used. Photoresistor detection First, use a black paper to cover the light-transmitting window of the photoresistor. At this time, the pointer of the multimeter basically remains motionless, and the resistance value is close to infinity. The larger this value, the better the performance of the photoresistor. If this value is very small or close to zero, it means that the photoresistor has been burned through and damaged, and can no longer be used. Then point a light source at the light-transmitting window of the photoresistor. At this time, the pointer of the multimeter should swing significantly, and the resistance value will be significantly reduced. The smaller this value is, the better the performance of the photoresistor is. If this value is very large or even infinite, it means that the internal open circuit of the photoresistor is damaged and it can no longer be used. Finally, point the light-transmitting window of the photoresistor at the incident light, and shake a small black paper on the upper part of the light-shielding window of the photoresistor to make it receive light intermittently. At this time, the pointer of the multimeter should swing left and right with the shaking of the black paper. If the pointer of the multimeter always stops at a certain position and does not swing with the shaking of the paper, it means that the photosensitive material of the photoresistor has been damaged. The first thing to say about the detection method of capacitors is the detection of commonly used fixed capacitors. When detecting small capacitors below 10pF, because the capacity of fixed capacitors below 10pF is too small, using a multimeter to measure can only qualitatively check whether it has leakage, internal short circuit or breakdown. When measuring, you can use the multimeter R×10k block, and use two test pens to connect the two pins of the capacitor at will. The resistance should be infinite. If the measured resistance (the pointer swings to the right) is zero, it means that the capacitor is leaking or damaged or internally broken down. Detect whether the 10PF~001μF fixed capacitor is charging, and then judge whether it is good or bad. The multimeter uses the R×1k block. The β values of the two transistors are both above 100, and the penetration current should be small. 3DG6 and other types of silicon transistors can be used to form a composite tube. The red and black test pens of the multimeter are connected to the emitter e and collector c of the composite tube respectively. Due to the amplification effect of the composite transistor, the charging and discharging process of the measured capacitor is amplified, so that the swing amplitude of the multimeter pointer is increased, which is convenient for observation. It should be noted that during the test operation, especially when measuring a capacitor with a smaller capacity, it is necessary to repeatedly switch the pins of the measured capacitor to contact points A and B to clearly see the swing of the multimeter pointer. For fixed capacitors above 0.01 μF, the R×10k range of the multimeter can be used to directly test whether the capacitor is in the charging process and whether there is an internal short circuit or leakage, and the capacity of the capacitor can be estimated based on the amplitude of the pointer swinging to the right.The second component detection to be mentioned is the detection of electrolytic capacitors. Since the capacity of electrolytic capacitors is much larger than that of general fixed capacitors, when measuring, the appropriate range should be selected for different capacities. According to experience, under normal circumstances, the capacitance between 1 and 47μF can be measured with the R×1k block, and the capacitance greater than 47μF can be measured with the R×100 block. We connect the red probe of the multimeter to the negative pole and the black probe to the positive pole. At the moment of contact, the multimeter pointer deflects to the right with a large deviation (for the same resistance block, the larger the capacity, the larger the swing), and then gradually turns to the left until it stops at a certain position. The resistance value at this time is the forward leakage resistance of the electrolytic capacitor, which is slightly larger than the reverse leakage resistance. Practical experience shows that the leakage resistance of the electrolytic capacitor should generally be above several hundred kΩ, otherwise it will not work properly. During the test, if there is no charging phenomenon in both the forward and reverse directions, that is, the needle does not move, it means that the capacity has disappeared or the internal circuit is broken; if the measured resistance value is very small or zero, it means that the capacitor has a large leakage or has been broken down and damaged and cannot be used. For electrolytic capacitors with unclear positive and negative pole markings, the above-mentioned method of measuring leakage resistance can be used to distinguish them. That is, first measure the leakage resistance at random, remember its size, and then exchange the test leads to measure another resistance value. The one with the larger resistance value in the two measurements is the forward connection method, that is, the black test lead is connected to the positive pole and the red test lead is connected to the negative pole. Using the resistance block of the multimeter, the method of charging the electrolytic capacitor in the forward and reverse directions can be used to estimate the capacity of the electrolytic capacitor according to the amplitude of the pointer swinging to the right. Finally, let's talk about the detection of variable capacitors. The steps are as follows: first, gently rotate the shaft by hand, it should feel very smooth, and it should not feel sometimes loose and sometimes tight or even stuck. When the carrier shaft is pushed forward, backward, up, down, left, right and other directions, the shaft should not be loose. Use one hand to rotate the shaft, and use the other hand to touch the outer edge of the moving plate group. You should not feel any looseness. The variable capacitor with poor contact between the shaft and the moving plate cannot be used any more. Finally, set the multimeter to the R×10k position, connect the two test leads to the moving plate and the fixed plate of the variable capacitor with one hand, and use the other hand to slowly rotate the shaft back and forth a few times. The multimeter pointer should remain at the infinite position. In the process of rotating the shaft, if the pointer sometimes points to zero, it means that there is a short circuit between the moving plate and the fixed plate; if it touches a certain angle, the multimeter reading is not infinite but a certain resistance value, which means that there is leakage between the moving plate and the fixed plate of the variable capacitor.
Reference address:It is by no means stereotyped, common component detection and debugging steps
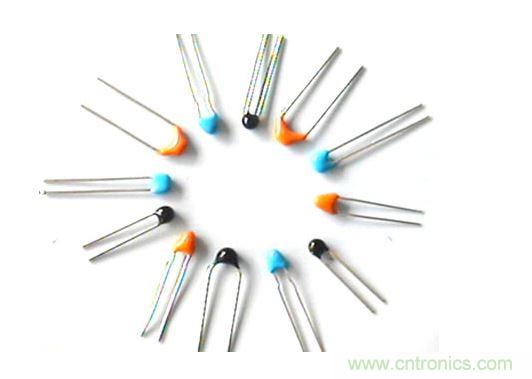
inductors and transformers Here we first explain the detection of color-coded inductors. The detection method here is that we need to set the multimeter to R×1 gear, and connect the red and black test leads to any lead-out end of the color-coded inductor. At this time, the pointer should swing to the right. According to the measured resistance value, the following three situations can be specifically identified: A. The resistance value of the color-coded inductor under test is zero, and there is a short-circuit fault inside it. B. The DC resistance value of the color-coded inductor under test is directly related to the diameter of the enameled wire used to wind the inductor coil and the number of windings. As long as the resistance value can be measured, the color-coded inductor under test can be considered normal. The following is an explanation of the detection of the intermediate-frequency transformer . A. Set the multimeter to the R×1 position, and check the on-off status of each winding one by one according to the arrangement of the pins of each winding of the intermediate-frequency transformer, and then determine whether it is normal. B. Check the insulation performance. Set the multimeter to the R×10k position and perform the following state tests: (1) The resistance value between the primary winding and the secondary winding; (2) The resistance value between the primary winding and the shell; (3) The resistance value between the secondary winding and the shell. The above test results are divided into three situations: (1) The resistance value is infinite: normal; (2) The resistance value is zero: there is a short-circuit fault; (3) The resistance value is less than infinity, but greater than zero: there is a leakage fault. Power transformer detection A Check whether there are obvious abnormalities by observing the appearance of the transformer. For example, whether the coil lead is broken, desoldering, whether the insulating material has traces of burning, whether the core fastening screw is loose, whether the silicon steel sheet is rusted, whether the winding coil is exposed, etc. B Insulation test. Use the multimeter R×10k block to measure the resistance between the core and the primary, the primary and each secondary, the core and each secondary, the electrostatic shielding layer and the secondary, and the secondary windings. The multimeter pointer should point to the infinite position and not move. Otherwise, it means that the transformer insulation performance is poor. C Coil on-off detection. Set the multimeter to R×1 block. During the test, if the resistance value of a winding is infinite, it means that this winding has a short-circuit fault. D Identify the primary and secondary coils. The primary and secondary pins of the power transformer are generally led out from both sides, and the primary winding is often marked with 220V, while the secondary winding is marked with the rated voltage value, such as 15V, 24V, 35V, etc. Identify based on these marks. E. Detection of no-load current. (a) Direct measurement method. Open all secondary windings, set the multimeter to the AC current range (500mA, and connect the primary winding in series. When the primary winding plug is inserted into the 220V AC mains, the multimeter indicates the no-load current value. This value should not be greater than 10% to 20% of the full-load current of the transformer. Common electronic equipmentThe normal no-load current of the power transformer should be around 100mA. If it exceeds too much, it means that the transformer has a short-circuit fault. (b) Indirect measurement method. Connect a 10/5W resistor in series in the primary winding of the transformer, and the secondary is still completely unloaded. Set the multimeter to the AC voltage range. After power on, use two test leads to measure the voltage drop U across the resistor R, and then use Ohm's law to calculate the no-load current Iempty, that is, Iempty = U/R. F Detection of no-load voltage. Connect the primary of the power transformer to 220V AC power, and use a multimeter to measure the no-load voltage value of each winding (U21, U22, U23, U24) in turn. It should meet the required value. The allowable error range is generally: high-voltage winding ≤±10%, low-voltage winding ≤±5%, and the voltage difference between two sets of symmetrical windings with center taps should be ≤±2%. G Generally, the allowable temperature rise of small-power power transformers is 40℃~50℃. If the quality of the insulating material used is good, the allowable temperature rise can be increased. H detects and distinguishes the same-named ends of each winding. When using a power transformer, sometimes in order to obtain the required secondary voltage, two or more secondary windings can be connected in series. When using a power transformer in series, the same-named ends of each winding participating in the series connection must be connected correctly and cannot be mistaken. Otherwise, the transformer cannot work properly. I.Comprehensive detection and discrimination of short-circuit faults in power transformers. The main symptoms of short-circuit faults in power transformers are severe heating and abnormal output voltage of the secondary winding. Generally, the more short-circuit points there are between turns in the coil, the greater the short-circuit current and the more severe the heating of the transformer. A simple way to detect and determine whether a power transformer has a short-circuit fault is to measure the no-load current (the test method has been introduced earlier). For a transformer with a short-circuit fault, the no-load current value will be much greater than 10% of the full-load current. When the short circuit is serious, the transformer will heat up rapidly within tens of seconds after being powered on at no load, and the iron core will feel hot when touched by hand. At this time, it is not necessary to measure the no-load current to determine that the transformer has a short-circuit point. The detection method of resistors first describes the method for detecting fixed resistors. In the actual component detection operation steps, first connect the two test leads (regardless of positive and negative) to the two end pins of the resistor to measure the actual resistance value. In order to improve the measurement accuracy, the range should be selected according to the nominal value of the measured resistor. Due to the nonlinear relationship of the ohm scale, its middle section is more finely divided, so the pointer indication value should be as close to the middle section of the scale as possible, that is, within the 20% to 80% arc range of the full scale, so as to make the measurement more accurate. According to the different resistance error levels. The reading and the nominal resistance are allowed to have an error of ±5%, ±10% or ±20% respectively. If they do not match and exceed the error range, it means that the resistance value has changed. It should be noted here: when testing, especially when measuring resistors with a resistance of more than tens of kΩ, do not touch the conductive part of the test lead and the resistor with your hands; the resistor to be tested is welded from the circuit, and at least one head must be welded open to prevent other components in the circuit from affecting the test and causing measurement errors; although the resistance value of the color ring resistor can be determined by the color ring mark, it is best to use a multimeter to test its actual resistance value when using it. The method and precautions for detecting cement resistors are exactly the same as those for detecting ordinary fixed resistors. The second main component to be listed below is about the detection of fuse resistors. In circuit design, when the fuse resistor is blown and the circuit is disconnected, a judgment can be made based on experience: if the surface of the fuse resistor is found to be black or burnt, it can be concluded that it is overloaded and the current passing through it exceeds the rated value many times; if there is no trace on its surface and the circuit is open, it indicates that the current flowing through is just equal to or slightly greater than its rated fuse value. To judge whether a fuse resistor without any trace on the surface is good or bad, it can be measured with the help of the multimeter R×1 gear. To ensure accurate measurement, one end of the fuse resistor should be welded off the circuit. If the measured resistance value is infinite, it means that the fuse resistor has failed and the circuit is open. If the measured resistance value is far different from the nominal value, it indicates that the resistance value has changed and it should not be used again. In maintenance practice, it is found that a small number of fuse resistors are short-circuited in the circuit, and attention should also be paid during detection. The third thing we need to test is the potentiometer. When testing the actual circuit components, first turn the handle to see if the handle turns smoothly, whether the switch is flexible, whether the "click" sound is crisp when the switch is on and off, and listen to the friction sound between the internal contact point of the potentiometer and the resistor body. If there is a "rustling" sound, it means that the quality is not good. When testing with a multimeter, first select the appropriate resistance position of the multimeter according to the resistance value of the potentiometer to be tested, and then you can test it according to the following method. A Use the ohm range of the multimeter to measure the two ends of "1" and "2". The reading should be the nominal resistance value of the potentiometer. If the pointer of the multimeter does not move or the resistance value is very different, it indicates that the potentiometer is damaged. B Check whether the movable arm of the potentiometer is in good contact with the resistor. Use the ohm range of the multimeter to measure the two ends of "1" and "2" (or "2" and "3"), and turn the shaft of the potentiometer counterclockwise to a position close to "off". At this time, the smaller the resistance value, the better. Then slowly rotate the shaft handle clockwise, the resistance value should gradually increase, and the pointer in the meter head should move smoothly. When the shaft handle is rotated to the extreme position "3", the resistance value should be close to the nominal value of the potentiometer. If the pointer of the multimeter jumps during the rotation of the shaft handle of the potentiometer, it means that the movable contact has a poor contact fault. The following is about the detection of positive temperature coefficient thermistors and negative temperature coefficient thermistors. First, when testing the positive temperature coefficient thermistor, use the multimeter R×1 gear, which can be divided into two steps: A normal temperature detection (indoor temperature is close to 25℃); touch the two pins of the PTC thermistor with two test leads to measure its actual resistance value, and compare it with the nominal resistance value. The difference between the two is within ±2Ω, which is normal. If the actual resistance value is too different from the nominal resistance value, it means that its performance is poor or it is damaged. B. Heating test: On the basis of normal test at room temperature, the second step of test - heating test can be carried out. A heat source (such as a soldering iron) is placed close to the PTC thermistor to heat it, and a multimeter is used to monitor whether its resistance value increases with the increase of temperature. If so, it means that the thermistor is normal. If the resistance value does not change, it means that its performance has deteriorated and it cannot be used. Be careful not to make the heat source too close to the PTC thermistor or directly contact the thermistor to prevent it from being burned. The method of measuring the nominal resistance value Rt of the negative temperature coefficient thermistor using a multimeter to measure the NTC thermistor is the same as the method of measuring ordinary fixed resistors, that is, according to the nominal resistance value of the NTC thermistor, the appropriate resistance block can be selected to directly measure the actual value of Rt. However, because the NTC thermistor is very sensitive to temperature, the following points should be noted during the test: ARt is measured by the manufacturer at an ambient temperature of 25°C, so when measuring Rt with a multimeter, it should also be carried out when the ambient temperature is close to 25°C to ensure the credibility of the test. B The measured power must not exceed the specified value to avoid measurement errors caused by the thermal effect of the current. C Pay attention to correct operation. During the test, do not pinch the thermistor body with your hands to prevent the body temperature from affecting the test. (2) Estimation of temperature coefficient αt First measure the resistance value Rt1 at room temperature t1, then use an electric soldering iron as a heat source, close to the thermistor Rt, measure the resistance value RT2, and use a thermometer to measure the average temperature t2 of the thermistor RT surface at this time before calculating. Detection of varistor and photoresistor. First of all, the varistor needs to use the R×1k block of the multimeter to measure the forward and reverse insulation resistance between the two pins of the varistor. Both are infinite, otherwise, it means that the leakage current is large. If the measured resistance is very small, it means that the varistor is damaged and cannot be used. Photoresistor detection First, use a black paper to cover the light-transmitting window of the photoresistor. At this time, the pointer of the multimeter basically remains motionless, and the resistance value is close to infinity. The larger this value, the better the performance of the photoresistor. If this value is very small or close to zero, it means that the photoresistor has been burned through and damaged, and can no longer be used. Then point a light source at the light-transmitting window of the photoresistor. At this time, the pointer of the multimeter should swing significantly, and the resistance value will be significantly reduced. The smaller this value is, the better the performance of the photoresistor is. If this value is very large or even infinite, it means that the internal open circuit of the photoresistor is damaged and it can no longer be used. Finally, point the light-transmitting window of the photoresistor at the incident light, and shake a small black paper on the upper part of the light-shielding window of the photoresistor to make it receive light intermittently. At this time, the pointer of the multimeter should swing left and right with the shaking of the black paper. If the pointer of the multimeter always stops at a certain position and does not swing with the shaking of the paper, it means that the photosensitive material of the photoresistor has been damaged. The first thing to say about the detection method of capacitors is the detection of commonly used fixed capacitors. When detecting small capacitors below 10pF, because the capacity of fixed capacitors below 10pF is too small, using a multimeter to measure can only qualitatively check whether it has leakage, internal short circuit or breakdown. When measuring, you can use the multimeter R×10k block, and use two test pens to connect the two pins of the capacitor at will. The resistance should be infinite. If the measured resistance (the pointer swings to the right) is zero, it means that the capacitor is leaking or damaged or internally broken down. Detect whether the 10PF~001μF fixed capacitor is charging, and then judge whether it is good or bad. The multimeter uses the R×1k block. The β values of the two transistors are both above 100, and the penetration current should be small. 3DG6 and other types of silicon transistors can be used to form a composite tube. The red and black test pens of the multimeter are connected to the emitter e and collector c of the composite tube respectively. Due to the amplification effect of the composite transistor, the charging and discharging process of the measured capacitor is amplified, so that the swing amplitude of the multimeter pointer is increased, which is convenient for observation. It should be noted that during the test operation, especially when measuring a capacitor with a smaller capacity, it is necessary to repeatedly switch the pins of the measured capacitor to contact points A and B to clearly see the swing of the multimeter pointer. For fixed capacitors above 0.01 μF, the R×10k range of the multimeter can be used to directly test whether the capacitor is in the charging process and whether there is an internal short circuit or leakage, and the capacity of the capacitor can be estimated based on the amplitude of the pointer swinging to the right.The second component detection to be mentioned is the detection of electrolytic capacitors. Since the capacity of electrolytic capacitors is much larger than that of general fixed capacitors, when measuring, the appropriate range should be selected for different capacities. According to experience, under normal circumstances, the capacitance between 1 and 47μF can be measured with the R×1k block, and the capacitance greater than 47μF can be measured with the R×100 block. We connect the red probe of the multimeter to the negative pole and the black probe to the positive pole. At the moment of contact, the multimeter pointer deflects to the right with a large deviation (for the same resistance block, the larger the capacity, the larger the swing), and then gradually turns to the left until it stops at a certain position. The resistance value at this time is the forward leakage resistance of the electrolytic capacitor, which is slightly larger than the reverse leakage resistance. Practical experience shows that the leakage resistance of the electrolytic capacitor should generally be above several hundred kΩ, otherwise it will not work properly. During the test, if there is no charging phenomenon in both the forward and reverse directions, that is, the needle does not move, it means that the capacity has disappeared or the internal circuit is broken; if the measured resistance value is very small or zero, it means that the capacitor has a large leakage or has been broken down and damaged and cannot be used. For electrolytic capacitors with unclear positive and negative pole markings, the above-mentioned method of measuring leakage resistance can be used to distinguish them. That is, first measure the leakage resistance at random, remember its size, and then exchange the test leads to measure another resistance value. The one with the larger resistance value in the two measurements is the forward connection method, that is, the black test lead is connected to the positive pole and the red test lead is connected to the negative pole. Using the resistance block of the multimeter, the method of charging the electrolytic capacitor in the forward and reverse directions can be used to estimate the capacity of the electrolytic capacitor according to the amplitude of the pointer swinging to the right. Finally, let's talk about the detection of variable capacitors. The steps are as follows: first, gently rotate the shaft by hand, it should feel very smooth, and it should not feel sometimes loose and sometimes tight or even stuck. When the carrier shaft is pushed forward, backward, up, down, left, right and other directions, the shaft should not be loose. Use one hand to rotate the shaft, and use the other hand to touch the outer edge of the moving plate group. You should not feel any looseness. The variable capacitor with poor contact between the shaft and the moving plate cannot be used any more. Finally, set the multimeter to the R×10k position, connect the two test leads to the moving plate and the fixed plate of the variable capacitor with one hand, and use the other hand to slowly rotate the shaft back and forth a few times. The multimeter pointer should remain at the infinite position. In the process of rotating the shaft, if the pointer sometimes points to zero, it means that there is a short circuit between the moving plate and the fixed plate; if it touches a certain angle, the multimeter reading is not infinite but a certain resistance value, which means that there is leakage between the moving plate and the fixed plate of the variable capacitor.
Previous article:Ten diagnostic methods for instruments and meters are "gifted" to you. Read them early and benefit early.
Next article:Design circuit of a power supply for an intelligent electricity meter
- Popular Resources
- Popular amplifiers
Recommended Content
Latest Test Measurement Articles
- Keysight Technologies Helps Samsung Electronics Successfully Validate FiRa® 2.0 Safe Distance Measurement Test Case
- From probes to power supplies, Tektronix is leading the way in comprehensive innovation in power electronics testing
- Seizing the Opportunities in the Chinese Application Market: NI's Challenges and Answers
- Tektronix Launches Breakthrough Power Measurement Tools to Accelerate Innovation as Global Electrification Accelerates
- Not all oscilloscopes are created equal: Why ADCs and low noise floor matter
- Enable TekHSI high-speed interface function to accelerate the remote transmission of waveform data
- How to measure the quality of soft start thyristor
- How to use a multimeter to judge whether a soft starter is good or bad
- What are the advantages and disadvantages of non-contact temperature sensors?
MoreSelected Circuit Diagrams
MorePopular Articles
- Innolux's intelligent steer-by-wire solution makes cars smarter and safer
- 8051 MCU - Parity Check
- How to efficiently balance the sensitivity of tactile sensing interfaces
- What should I do if the servo motor shakes? What causes the servo motor to shake quickly?
- 【Brushless Motor】Analysis of three-phase BLDC motor and sharing of two popular development boards
- Midea Industrial Technology's subsidiaries Clou Electronics and Hekang New Energy jointly appeared at the Munich Battery Energy Storage Exhibition and Solar Energy Exhibition
- Guoxin Sichen | Application of ferroelectric memory PB85RS2MC in power battery management, with a capacity of 2M
- Analysis of common faults of frequency converter
- In a head-on competition with Qualcomm, what kind of cockpit products has Intel come up with?
- Dalian Rongke's all-vanadium liquid flow battery energy storage equipment industrialization project has entered the sprint stage before production
MoreDaily News
- Allegro MicroSystems Introduces Advanced Magnetic and Inductive Position Sensing Solutions at Electronica 2024
- Car key in the left hand, liveness detection radar in the right hand, UWB is imperative for cars!
- After a decade of rapid development, domestic CIS has entered the market
- Aegis Dagger Battery + Thor EM-i Super Hybrid, Geely New Energy has thrown out two "king bombs"
- A brief discussion on functional safety - fault, error, and failure
- In the smart car 2.0 cycle, these core industry chains are facing major opportunities!
- The United States and Japan are developing new batteries. CATL faces challenges? How should China's new energy battery industry respond?
- Murata launches high-precision 6-axis inertial sensor for automobiles
- Ford patents pre-charge alarm to help save costs and respond to emergencies
- New real-time microcontroller system from Texas Instruments enables smarter processing in automotive and industrial applications
Guess you like
- EEWORLD University ---- Digi-Key: Accelerated Application of Graph Algorithms in Deep Learning
- Echo Cancellation - How to solve the serious problem of sound swallowing during dual talk in WebRTC AEC algorithm
- [TI millimeter wave radar evaluation]_2_1243Problems encountered in BOOST debugging
- FPGA Timing Constraints Practice: Sorting Out the Clock Tree
- A constant and adjustable output power electronic cigarette power supply solution based on TPS61022
- Sales of new energy vehicles have skyrocketed, how should we deal with used batteries?
- E-ON China Online Cloud Sharing Laboratory——"Microcomputer Principles and Applications"
- Improving Power Supply Network Efficiency Using Fixed Ratio Converters
- Large amplitude sine wave signal frequency acquisition circuit
- 【Share】Output adjustable