Figure 1. Complete two-port network analyzer source uncertainty
First, the first uncertainty is the signal loss caused by the transmission signal and the reflected signal due to the frequency or the forward and reverse tracks respectively. Secondly, the difference between the input impedance of the DUT and the impedance of the network analyzer or system. Similarly, there are similar situations at the output of the DUT, which belong to source matching and load matching respectively.
The efficiency of the directional coupler used for signal separation also needs to be considered. An ideal directional coupler produces an output signal in the coupled arm that is proportional to the standard signal in one direction of the main arm, while producing no output signal in the opposite direction. The difference between the coupler output (coupled arm) and the standard input signal (through arm) is the coupling coefficient. The coupling coefficient is usually between 10 dB and 30 dB, meaning that when the input signal passes through the through arm in the appropriate direction, the output RF power level is 10 to 30 dB less than it is.
Directional couplers do not generate output for signals in the opposite direction. In practice, however, this is difficult to achieve. Although small, signals in the opposite direction passing through an actual coupler will still generate unwanted responses at the output. This unwanted signal is defined as coupler leakage. The difference between the coupling coefficient and the coupling leakage is called the directivity of the coupler.
Finally, there is isolation. The receiver at port 2 detects a small amount of signal radiated or conducted at port 1. In modern network analyzers, this unwanted leakage is usually very small. In general, it does not affect the measurement unless the DUT has high loss. Although recommended, isolation is only an optional operation during calibration in many modern vector network analyzers.
The sources of forward uncertainty for a complete network analyzer include: transmission and reflection tracking; load and source matching; directivity and isolation, which are combined with the reverse 6 error terms, a total of 12 error terms. User calibration needs to fully account for these 12 errors in order to obtain the appropriate correction coefficients to be used in the measured data. This correction is the main reason for the remarkable accuracy of the vector network analyzer.
Calibration of network analysis
Calibration of RF equipment often requires sending the instrument to an accredited instrument calibration laboratory periodically to ensure that the instrument is operating within the manufacturer's specifications. The laboratory also often adjusts the instrument's performance to a standard, such as that specified by the National Institute of Standards and Technology (NIST).
Network analyzers are no exception. They require periodic calibration so often that they are not always accurate enough and user calibration is often required. Calibration of network analyzers is usually done using a set of calibration standards that come with the network analyzer or with user-defined standards. A set of correction parameters are generated by comparing known data stored in the network analyzer with the measured data generated using the calibration standards. These are then applied to the data during the calibration test to compensate for the error sources discussed in the previous section.
Many factors determine how often user calibration needs to be performed. Factors you need to consider include the required test accuracy, environmental factors, and the repeatability of the DUT connection. Typically, network analyzers require user calibration every few hours or days, and you should decide how often calibration is required based on verified standards, identification of the source of test instability, and personal experience. It should be noted that this discussion uses periodic calibration to describe user calibration, not to be confused with the recommended annual certified factory calibration.
Three series of calibrations are often used in calibrating network analyzers:
1. Short circuit, open circuit, load, direct (SOLT)
2. Direct, Reflected, Linear (TRL)
3. Automatic calibration using an external automated calibration model
Since each calibration series has many different requirements, the decision on which method to use depends on the DUT, the test system, and the test requirements. Since SOLT is widely used, we use it to illustrate the changes in a calibration series.
SOLT requires short, open, load, and thru standards in the system (and DUT) and impedance. Accurate standard data, determined by their mechanical characteristics, is loaded into the network analyzer before calibration. The location where you connect the calibration standard (network analyzer port, end of cable, or in the test fixture) is where the test begins and ends. This is the reference platform or test platform.
To further clarify, you must make a straight-through connection with a pluggable connection. For example, a male to female connection, or other connection that does not require external devices or adapters to complete the straight-through connection during SOLT testing. Inserting any device during calibration and not using the device in the calibration measurement will cause measurement errors.
If you cannot make a straight-through connection, it is called non-insertable. There are several ways to deal with non-insertable situations. The simplest is to use a set of adapters of the same phase (included in most calibration kits) and one for each type of short, open, and load, use one adapter to make the straight-through connection during calibration, and swap it with an appropriate adapter for the DUT connection during calibration testing.
Other calibrations in the SOLT range include a response type calibration. This is faster, but not as accurate as removing bandwidth loss over frequency. It only considers the forward and reverse conditions of the 12 error model. You can do a one-port calibration by placing shorts, opens, or loads on port one. This can save time if you only have one port to measure, such as the return loss of an antenna. An enhanced one-port calibration is like a full one-port calibration, but uses a through connection to measure port two, which is common in T/R configurations where there is no source on port two. Finally there is a full two-port SOLT calibration that places shorts, opens, or loads on both ports as specified in the calibration.
There are many variations of SOLT and TRL calibration, and you can use TRL calibration in applications where actual terminals do not exist such as probe nodes or if the DUT is in a test fixture. Since TRL does not require a load, it can be well implemented in these cases.
Automated calibration is a relatively new approach that has quickly gained popularity due to their speed, repeatability, and ease of use. Furthermore, they remove most of the manual intervention, greatly reducing the chance of errors during calibration. These units traditionally consist of an electronic component, such as a diode, terminal, or other marker, and the associated detailed electronic description stored in EEPROM encoded. When connected to a network analyzer, the automated calibration is set to different states. During the calibration process these states are measured and compared to the corresponding states stored in the EEPROM to arrive at the correct correction value.
Regardless of which calibration method you use, random sources of error should be avoided, and reducing the IF bandwidth and using averaging to reduce noise will provide better results. When calibrating a network analyzer, quality components, solid measurement practices, and a thorough understanding of the calibration procedures and instruments are equally important.
Basic principles of network analysis Process requirements
When making accurate measurements with a network analyzer, each step needs to be understood and performed correctly to obtain the best results. Use high-performance components and thorough measurement practices. Consider the RF connection between a well-calibrated network analyzer with correction parameters and a high-performance DUT that requires accurate measurements:
Are there cables, adapters, and other high-performance components?
Did you clean them properly?
Is the proper torque being used?
Even the best network analyzer is of no use if the performance of the RF connected to the DUT does not match the specified system accuracy.
When using a network analyzer, it is very useful to use a process. Processes can enhance the operation and improve the results. Below is an example architecture using a network analyzer.
Prepare
Preparing the Network Analyzer and DUT
Clean, inspect and measure all connectors
If using SOLT calibration, select a method for handling non-intrusive connections
Connect the analyzer cable and adapter to the analyzer
operate
Pre-tuned Network Analyzer
Set source parameters including frequency, power, speed factor and IF bandwidth
Connect the DUT, verify installation, cables, adapters, and operation
Select S-parameter measurement and display format
If possible, set specific measurement targets, such as extension of reference planes
Observe the response
Remove the DUT
calibration
Select appropriate calibration kit or define input calibration standards
Set IF bandwidth and averaging to minimize noise during calibration
Manual calibration or use automatic calibration
Verify calibration quality using known check standards
Save instrument state and calibration
implement
Connecting the DUT
Get the appropriate correction parameters from the calibration step
Measure and save DUT parameters
Network analyzers, when used properly, are some of the most accurate RF instruments available, with typical accuracies of ± 0.1 dB and ± 0.1 degrees. They can make precise, repeatable RF measurements. Modern network analyzers offer configurations and measurement capabilities that are as broad as their applications. Choosing the right instrument, calibration, features, and employing reliable RF measurement methods can optimize your network analyzer results.
Previous article:Agilent near-field electromagnetic interference source detection and location solution
Next article:Analysis on the influence of spectrum analyzer RBW setting on test results
Recommended ReadingLatest update time:2024-11-17 00:22
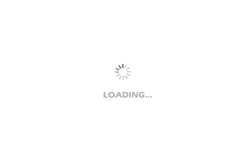
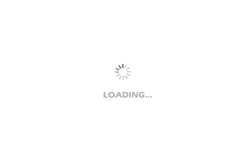
- Popular Resources
- Popular amplifiers
- Keysight Technologies Helps Samsung Electronics Successfully Validate FiRa® 2.0 Safe Distance Measurement Test Case
- From probes to power supplies, Tektronix is leading the way in comprehensive innovation in power electronics testing
- Seizing the Opportunities in the Chinese Application Market: NI's Challenges and Answers
- Tektronix Launches Breakthrough Power Measurement Tools to Accelerate Innovation as Global Electrification Accelerates
- Not all oscilloscopes are created equal: Why ADCs and low noise floor matter
- Enable TekHSI high-speed interface function to accelerate the remote transmission of waveform data
- How to measure the quality of soft start thyristor
- How to use a multimeter to judge whether a soft starter is good or bad
- What are the advantages and disadvantages of non-contact temperature sensors?
- Innolux's intelligent steer-by-wire solution makes cars smarter and safer
- 8051 MCU - Parity Check
- How to efficiently balance the sensitivity of tactile sensing interfaces
- What should I do if the servo motor shakes? What causes the servo motor to shake quickly?
- 【Brushless Motor】Analysis of three-phase BLDC motor and sharing of two popular development boards
- Midea Industrial Technology's subsidiaries Clou Electronics and Hekang New Energy jointly appeared at the Munich Battery Energy Storage Exhibition and Solar Energy Exhibition
- Guoxin Sichen | Application of ferroelectric memory PB85RS2MC in power battery management, with a capacity of 2M
- Analysis of common faults of frequency converter
- In a head-on competition with Qualcomm, what kind of cockpit products has Intel come up with?
- Dalian Rongke's all-vanadium liquid flow battery energy storage equipment industrialization project has entered the sprint stage before production
- Allegro MicroSystems Introduces Advanced Magnetic and Inductive Position Sensing Solutions at Electronica 2024
- Car key in the left hand, liveness detection radar in the right hand, UWB is imperative for cars!
- After a decade of rapid development, domestic CIS has entered the market
- Aegis Dagger Battery + Thor EM-i Super Hybrid, Geely New Energy has thrown out two "king bombs"
- A brief discussion on functional safety - fault, error, and failure
- In the smart car 2.0 cycle, these core industry chains are facing major opportunities!
- The United States and Japan are developing new batteries. CATL faces challenges? How should China's new energy battery industry respond?
- Murata launches high-precision 6-axis inertial sensor for automobiles
- Ford patents pre-charge alarm to help save costs and respond to emergencies
- New real-time microcontroller system from Texas Instruments enables smarter processing in automotive and industrial applications
- Help
- How to use GPIO of TI C55x series DSP
- Introduction to 5G R16 Standard Vertical Industry Extensions
- 【RPi PICO】CircuitPython driver ws2812
- dspIC30f6010a chip CAN communication and data processing
- 【McQueen Trial】McQueen product information
- Solving High-Voltage Current Sensing Design Challenges in HEV/EV
- Has anyone made irregular PCB? Please help
- Car Charger IC
- Several points to note when using SIMD to process multiple data in parallel