Undoubtedly, the signal from the sensor contains very useful information or characteristics of the measured physical quantity, and the test and measurement process is a very complex process of analyzing and processing this information.
How does a virtual instrument achieve measurement and analysis? How is it different from the measurement method of traditional instruments?
In order to better understand the measurement principle of virtual instruments, it is necessary to first make a brief review of the measurement methods of DC voltage and AC voltage of traditional instruments.
For a long time, the improvement of digital instrument measurement performance has basically relied on major breakthroughs in analog-to-digital converters. For example: from dual-integral to multi-slope integral, etc. Although breakthroughs in working principles often significantly improve and enhance the performance of digital instruments, these special designs also significantly increase the cost of the instrument and make the manufacturing and debugging process more and more complicated.
In recent years, with the rapid development of analog-to-digital conversion technology, DSP and digital signal processing technology, a fully digital measuring instrument based on the sampling principle has emerged. Sampling-type full-digital measurement first collects the input signal at a high rate, and the collected data is transmitted to the DSP or processor for analysis and processing and displays the processing results. The
most widely used application of sampling-type full-digital measurement is the integrated single-phase and three-phase electronic watt-hour meter IC chip, which has been integrated. Let's take a look at the schematic diagram of the integrated circuit.
1.3.2 Basic measurement principles of virtual instruments
2. Analog-to-digital converter - the core component of the data acquisition module
After sampling, the function values corresponding to these 32 points are still accurate. When converted by the analog-to-digital converter, due to the limited number of bits of the analog-to-digital converter, only the approximate value of the point can be used to replace the original function value (quantization) Xq(nTs).
The quantization process leads to quantization error. The size of the quantization error is related to the integral error and differential error of the analog-to-digital converter itself, and also to the noise size of the analog-to-digital converter.
Sampling theorem: To effectively sample the input signal, the sampling frequency must be more than twice the highest frequency part of the signal.
This theorem is also called the sampling theorem, Shannon's theorem, Nyquist theorem, etc., but their meanings are the same. The sampling theorem clearly points out a basic principle for sampling the input signal. Violating this principle will lead to signal confusion due to insufficient sampling.
Please note: The highest frequency in the signal refers to: for pure sinusoidal signals, it is the fundamental frequency; for signals containing harmonics, it is the frequency of the highest harmonic expected to be analyzed.
For example: for a pure sinusoidal signal with a frequency of 1000Hz, the theoretical sampling frequency is greater than 2000Hz. For sampling a signal with a fundamental frequency of 1000Hz and 10 harmonics, the theoretical sampling frequency should be greater than 20000Hz.
In practical applications, even for pure sine waves, the sampling frequency is usually greater than 10 times the signal frequency.
The sampling frequency is also called the Nyquist frequency. That is to say, when the sampling frequency is determined, the effective analysis bandwidth of the signal is also determined (less than the Nyquist frequency).
The sampling theorem only explains the deterministic relationship between the sampling frequency and the signal frequency, and does not explain the relationship with the number of bits of the analog-to-digital converter. Theoretically, the higher the number of bits of the analog-to-digital converter, the better, and the closer the conversion result is to the true value. However, this view is not absolute, and there are always exceptions. For example, NI's DSA (dynamic signal analysis) data acquisition module is usually 24 bits, but its measurement accuracy is very low, and it is mainly used for the measurement and analysis of dynamic signals. To be precise, it should be called 24-bit resolution, not 24-bit accuracy. Therefore, when we choose to determine the data acquisition module, we must select the appropriate data acquisition module based on the needs of the measurement object and the manual of the data acquisition module.
Finally, let's go back to the measurement of DC voltage of the double-integral voltmeter. Because the measurement is 2 times/s, the frequency (fluctuation) equivalent to the change of the DC signal is 1Hz/s. In fact, the change of the DC signal is much lower than this, so the DC voltage measurement fully meets the sampling theorem.
It can be said that the sampling theorem is the core theorem of virtual instruments. Computer-based testing, measurement and analysis also rely on the sampling theorem.
Summarizing the measurement principles of virtual instruments can give us this basic understanding. The measurement process of virtual instruments is to collect the data of the measured signal as the original data of the virtual instrument under the condition of satisfying the sampling theorem, and the processing of these original data will rely on software. The results of software processing are precisely based on the user's requirements.
Is there any essential difference between the measurement method of virtual instruments and that of traditional instruments?
1.3.3 Virtual instruments have changed the measurement methods and concepts of traditional instruments
T——the period of the measured signal
n——the number of sampling points in one period of the measured signal, constant
Ts——the sampling time interval
The sampling relationship that satisfies equations 1-3 is called equal-period sampling. The essence of equal-period sampling is that the sampling frequency must be an integer multiple of the signal period (a conventional constant), so that leakage caused by sampling truncation can be avoided.
In fact, due to the stability of the signal itself and the existence of noise interference, as well as the relationship between the signal frequency and the sampling frequency that is not an integer multiple, it is usually difficult to meet the requirements of equations 1-3. This will lead to measurement errors caused by leakage after sampling truncation [7].
In order to solve this problem, most embedded system designs use windowing and equal-period quasi-synchronous sampling methods (the concept of synchronization here is different from synchronous sampling. Synchronization here refers to the synchronization of the sampling frequency with the period of the measured signal, including hardware synchronization or software synchronization). Of course, whether windowing or using hardware synchronization or software synchronization greatly increases the complexity of the system.
So can such problems be solved or avoided in virtual instruments?
In virtual instrument sampling measurement, since a large number of sampling points can be selected, the impact of leakage caused by sampling truncation can be greatly reduced.
At the same time, the most desirable thing about virtual instrument sampling measurement is that the sampling of virtual instruments is a multi-cycle continuous sampling, which can also reduce the impact of leakage. The combined effect of the two can basically reduce the impact of leakage to a completely negligible level.
For example, in the measurement of 50Hz power frequency signal, if the sampling frequency Fs is set to 50kHz, and the number of data points to be read is set to 50000S/s. It is equivalent to extracting 50 cycles of data for analysis and processing each time, and each cycle contains 1000 data points. With the powerful computing power of commercial computers and the processing advantages of graphical software, this multi-point, multi-cycle measurement can hardly detect the impact of leakage. Practice has verified that its measurement results are stable and accurate.
Obviously, this is a unique advantage of virtual instruments. This is difficult for embedded systems to do due to the huge amount of data processing and complex calculation methods.
These examples show that virtual instrument sampling measurement can simplify the measurement method and change the measurement concept. For example, the hardware of the virtual instrument is a data acquisition module (standard module), which abandons the AC-DC converter and zero-crossing trigger circuit, counter and other dedicated hardware circuits in traditional instruments. Different software processing methods provide measurement analysis results. The ultimate effect is to improve the credibility of the measurement results. The beneficiaries are still the users of virtual instruments.
In other words: the data obtained by sampling does not determine the measurement function. The realization of the measurement function depends on what analysis and processing function (VI) is used. The change of measurement function is realized by software. Therefore, its measurement function can be defined and realized by the user or designer himself.
In fact, virtual instruments have more features.
Reference address:The measurement principle of virtual instrument
How does a virtual instrument achieve measurement and analysis? How is it different from the measurement method of traditional instruments?
In order to better understand the measurement principle of virtual instruments, it is necessary to first make a brief review of the measurement methods of DC voltage and AC voltage of traditional instruments.
1.3.1 Basic measurement principles of traditional instruments
- Analog Instruments

Figure 1-10 Pointer multimeter
Analog measuring instruments are relatively common measuring instruments, most of which are pointer measuring instruments for electrical engineering, so they are also called pointer instruments.
Now let's take the most classic and common pointer multimeter as an example for a brief explanation.
The basic principle of measuring DC voltage with a pointer multimeter is to use a highly sensitive magnetoelectric DC ammeter (microammeter) as the indicator head for voltage measurement. When the small current generated by the measured DC voltage passing through the standard current limiting resistor passes through the head, the pointer will deflect and give the corresponding indication (the scale value of the dial). When measuring
AC voltage, the measured AC voltage is first attenuated and rectified into DC voltage, and then the replacement measurement of AC voltage is achieved through the measurement of DC voltage, and the corresponding AC voltage indication is given according to the scale.
From the perspective of measurement mechanism, the measurement process of analog instruments is a continuous measurement process. In other words: the measurement is carried out continuously throughout the measurement process. That is, the measured signal is always applied to the measuring mechanism, and there is no time discontinuity in the entire measurement process.
Now let's take the most classic and common pointer multimeter as an example for a brief explanation.
The basic principle of measuring DC voltage with a pointer multimeter is to use a highly sensitive magnetoelectric DC ammeter (microammeter) as the indicator head for voltage measurement. When the small current generated by the measured DC voltage passing through the standard current limiting resistor passes through the head, the pointer will deflect and give the corresponding indication (the scale value of the dial). When measuring
AC voltage, the measured AC voltage is first attenuated and rectified into DC voltage, and then the replacement measurement of AC voltage is achieved through the measurement of DC voltage, and the corresponding AC voltage indication is given according to the scale.
From the perspective of measurement mechanism, the measurement process of analog instruments is a continuous measurement process. In other words: the measurement is carried out continuously throughout the measurement process. That is, the measured signal is always applied to the measuring mechanism, and there is no time discontinuity in the entire measurement process.
2. Digital instrument
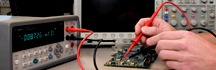
Figure 1-11 Digital multimeter
Digital instruments, such as digital voltmeters and digital multimeters, use specially designed analog-to-digital converters to convert the measured DC voltage into digital values for display, so they are called digital instruments. There are
many types of analog-to-digital converters. The following only takes the most representative dual-integration digital voltmeter as an example to briefly explain the basic measurement methods of DC voltage and AC voltage [5].
The dual-integration digital voltmeter divides the DC voltage measurement process into two stages: T1 and T2 (the entire measurement cycle = T1 + T2).
In the T1 time period, the measured DC signal is connected to the integrator to start integrating the measured signal; while in the T2 time period, the internal reference (with the opposite polarity to the measured signal) is connected to the integrator to start integrating the internal reference. At the same time, the T2 time interval is converted into a numerical value (number of pulses) corresponding to the DC voltage for display of the measurement result, and finally the entire measurement cycle is completed.
many types of analog-to-digital converters. The following only takes the most representative dual-integration digital voltmeter as an example to briefly explain the basic measurement methods of DC voltage and AC voltage [5].
The dual-integration digital voltmeter divides the DC voltage measurement process into two stages: T1 and T2 (the entire measurement cycle = T1 + T2).
In the T1 time period, the measured DC signal is connected to the integrator to start integrating the measured signal; while in the T2 time period, the internal reference (with the opposite polarity to the measured signal) is connected to the integrator to start integrating the internal reference. At the same time, the T2 time interval is converted into a numerical value (number of pulses) corresponding to the DC voltage for display of the measurement result, and finally the entire measurement cycle is completed.
The AC measurement of the digital voltmeter is realized by the AC-DC conversion module. The AC-DC conversion module converts the measured AC signal into a DC signal, and then completes the measurement and display of the AC through the DC measurement method. The AC-DC conversion module is divided into rectifier average type, logarithmic/antilogarithmic type, analog operation type and semiconductor thermoelectric conversion type, etc.
Looking back at the DC voltage measurement process of the dual-integration digital voltmeter, we find that its measurement mechanism has undergone some subtle changes. As mentioned earlier, the analog instrument measures the measured signal in real time, and the entire measurement process is continuous and uninterrupted, without any time discontinuity. The dual-integration digital voltmeter has obviously changed the measurement method of the analog instrument. The dual-integration digital voltmeter divides the DC voltage measurement process into two stages, T1 and T2. Obviously, no information in the signal will be reflected in the T2 time interval, because the integrator is integrating the internal reference in this stage. Therefore, from the perspective of time continuity, the dual-integration measurement method has a time discontinuity.
Through the DC measurement process of the dual-integral digital voltmeter, we can get the fact that the measurement process can be a discontinuous measurement process, which depends on the basic characteristics of the signal. Because the DC voltage signal itself has the characteristic of changing very slowly over time, the entire measurement process does not have to be carried out in real time. The DC measurement principle of the dual-integral voltmeter makes full use of this characteristic.
The T1 stage is also called the stage of "sampling" the input DC voltage. The concept of "sampling" should not be unfamiliar to everyone, because human ancestors have long used sampling methods to observe the movement laws of celestial bodies. The
relative positions between celestial bodies in the universe change very slowly, and there is no practical significance in implementing continuous observation. Therefore, ancient people used a period of time, such as one day, one month, and one year to observe their relative positions (equivalent to sampling), so as to calculate the movement laws of celestial bodies.
Looking back at the DC voltage measurement process of the dual-integration digital voltmeter, we find that its measurement mechanism has undergone some subtle changes. As mentioned earlier, the analog instrument measures the measured signal in real time, and the entire measurement process is continuous and uninterrupted, without any time discontinuity. The dual-integration digital voltmeter has obviously changed the measurement method of the analog instrument. The dual-integration digital voltmeter divides the DC voltage measurement process into two stages, T1 and T2. Obviously, no information in the signal will be reflected in the T2 time interval, because the integrator is integrating the internal reference in this stage. Therefore, from the perspective of time continuity, the dual-integration measurement method has a time discontinuity.
Through the DC measurement process of the dual-integral digital voltmeter, we can get the fact that the measurement process can be a discontinuous measurement process, which depends on the basic characteristics of the signal. Because the DC voltage signal itself has the characteristic of changing very slowly over time, the entire measurement process does not have to be carried out in real time. The DC measurement principle of the dual-integral voltmeter makes full use of this characteristic.
The T1 stage is also called the stage of "sampling" the input DC voltage. The concept of "sampling" should not be unfamiliar to everyone, because human ancestors have long used sampling methods to observe the movement laws of celestial bodies. The
relative positions between celestial bodies in the universe change very slowly, and there is no practical significance in implementing continuous observation. Therefore, ancient people used a period of time, such as one day, one month, and one year to observe their relative positions (equivalent to sampling), so as to calculate the movement laws of celestial bodies.
3. Sampling type fully digital measuring instrument
For a long time, the improvement of digital instrument measurement performance has basically relied on major breakthroughs in analog-to-digital converters. For example: from dual-integral to multi-slope integral, etc. Although breakthroughs in working principles often significantly improve and enhance the performance of digital instruments, these special designs also significantly increase the cost of the instrument and make the manufacturing and debugging process more and more complicated.
In recent years, with the rapid development of analog-to-digital conversion technology, DSP and digital signal processing technology, a fully digital measuring instrument based on the sampling principle has emerged. Sampling-type full-digital measurement first collects the input signal at a high rate, and the collected data is transmitted to the DSP or processor for analysis and processing and displays the processing results. The
most widely used application of sampling-type full-digital measurement is the integrated single-phase and three-phase electronic watt-hour meter IC chip, which has been integrated. Let's take a look at the schematic diagram of the integrated circuit.

Figure 1-12 Single-phase electronic watt-hour meter IC
In the upper left corner of the above figure, you can see two ADCs that synchronously sample the input voltage and current. The synchronously collected data is transmitted to a DSP dedicated to electric energy measurement for data processing, and the final processing results are sent to the MCU on the chip to complete the display and other communication tasks.
If the reader has a simple understanding of the traditional induction watt-hour meter, he will see the huge benefits brought by the sampling full digital measurement. It not only improves the measurement accuracy of the watt-hour meter, but more importantly, it removes many parts of the induction type, such as coils, turntables and other machined parts. And the digital measurement itself can easily realize modern technologies such as multiple rates and automatic meter reading.
After the above brief review, let's take a look at the basic measurement principles of virtual instruments. [page]
If the reader has a simple understanding of the traditional induction watt-hour meter, he will see the huge benefits brought by the sampling full digital measurement. It not only improves the measurement accuracy of the watt-hour meter, but more importantly, it removes many parts of the induction type, such as coils, turntables and other machined parts. And the digital measurement itself can easily realize modern technologies such as multiple rates and automatic meter reading.
After the above brief review, let's take a look at the basic measurement principles of virtual instruments. [page]
1.3.2 Basic measurement principles of virtual instruments
One of the key components for virtual instrument measurement is the data acquisition module. The essence of data acquisition is to sample the measured signal and then analyze and process the acquired data. Therefore, the basic measurement method of virtual instruments is also based on sampling technology.
In order to better understand the measurement principle of virtual instruments, it is necessary to briefly introduce other concepts.
In order to better understand the measurement principle of virtual instruments, it is necessary to briefly introduce other concepts.
1. Signal - the measurement object of virtual instrument
So far, the signals mentioned and discussed above are all time-varying signals. The classification of these signals is relatively complex. For virtual instrument measurement, the signals can be simply divided into the following types:
- DC signal - We can regard DC signal as a periodic signal with infinite period.
- Periodic signal - A periodic signal is a signal that changes over and over again at a certain time. It is the main signal form faced by virtual instrument measurement. Many data processing and analysis are carried out on periodic signals.
- Random signal - The characteristic of random signal is that there is no definite change pattern, it cannot be expressed by mathematical relationship, and its future change pattern cannot be predicted. Since random signal has certain statistical characteristics, it can usually be evaluated and processed by probability statistics method.
2. Analog-to-digital converter - the core component of the data acquisition module
The core component of the data acquisition module is the analog-to-digital converter. It is responsible for completing the entire process of digitizing the input electrical signal so that the computer can recognize and process it.
The analog-to-digital converter must complete two tasks simultaneously during the digitization of the input signal: sampling and quantization. Let's take the sine signal as an example to simply analyze its entire processing process.
In fact, in the analog-to-digital conversion process, sampling and quantization are basically completed at the same time, but for the convenience of analysis, we will break this process down into two stages: "sampling" and "quantization" to describe them separately.
The analog-to-digital converter must complete two tasks simultaneously during the digitization of the input signal: sampling and quantization. Let's take the sine signal as an example to simply analyze its entire processing process.
In fact, in the analog-to-digital conversion process, sampling and quantization are basically completed at the same time, but for the convenience of analysis, we will break this process down into two stages: "sampling" and "quantization" to describe them separately.
- sampling
In the figure above, the sine-shaped line segment (red) represents an analog sinusoidal input signal x(t), which is a continuous function in the time domain. That is to say, at any time point in the cycle of the signal, the corresponding accurate function value can be found.
The so-called "sampling" is to take N "sampling" points evenly distributed in any cycle of the signal. The vertical line segment (blue) in the sine envelope of Figure 1-13 represents 32 sampling points. The time interval between sampling points is Ts. After sampling, we can only obtain the function value at the sampling point, and discard the function value at other time points. This means that the original continuous sinusoidal signal is represented by only 32 data point values after sampling. The sampled signal is also called a discrete signal Xs(nTs).
The so-called "sampling" is to take N "sampling" points evenly distributed in any cycle of the signal. The vertical line segment (blue) in the sine envelope of Figure 1-13 represents 32 sampling points. The time interval between sampling points is Ts. After sampling, we can only obtain the function value at the sampling point, and discard the function value at other time points. This means that the original continuous sinusoidal signal is represented by only 32 data point values after sampling. The sampled signal is also called a discrete signal Xs(nTs).
- Quantification
After sampling, the function values corresponding to these 32 points are still accurate. When converted by the analog-to-digital converter, due to the limited number of bits of the analog-to-digital converter, only the approximate value of the point can be used to replace the original function value (quantization) Xq(nTs).
The quantization process leads to quantization error. The size of the quantization error is related to the integral error and differential error of the analog-to-digital converter itself, and also to the noise size of the analog-to-digital converter.
From Figure 1-14, we can see that the discrete signal after sampling and quantization is somewhat similar to a step wave. So can this step wave signal still represent the original sine signal? Obviously, from a mathematical point of view, when the number of sampling points in a cycle increases infinitely and the number of bits of the analog-to-digital converter also increases infinitely, the quantized signal will be infinitely close to the original analog signal.
However, in order to answer the question: Can the discrete quantized signal still represent the original function under finite point sampling and finite number of bits of the analog-to-digital converter? We need to further understand the sampling theorem.
However, in order to answer the question: Can the discrete quantized signal still represent the original function under finite point sampling and finite number of bits of the analog-to-digital converter? We need to further understand the sampling theorem.
- Sampling Theorem
Sampling theorem: To effectively sample the input signal, the sampling frequency must be more than twice the highest frequency part of the signal.
This theorem is also called the sampling theorem, Shannon's theorem, Nyquist theorem, etc., but their meanings are the same. The sampling theorem clearly points out a basic principle for sampling the input signal. Violating this principle will lead to signal confusion due to insufficient sampling.
Please note: The highest frequency in the signal refers to: for pure sinusoidal signals, it is the fundamental frequency; for signals containing harmonics, it is the frequency of the highest harmonic expected to be analyzed.
For example: for a pure sinusoidal signal with a frequency of 1000Hz, the theoretical sampling frequency is greater than 2000Hz. For sampling a signal with a fundamental frequency of 1000Hz and 10 harmonics, the theoretical sampling frequency should be greater than 20000Hz.
In practical applications, even for pure sine waves, the sampling frequency is usually greater than 10 times the signal frequency.
The sampling frequency is also called the Nyquist frequency. That is to say, when the sampling frequency is determined, the effective analysis bandwidth of the signal is also determined (less than the Nyquist frequency).
The sampling theorem only explains the deterministic relationship between the sampling frequency and the signal frequency, and does not explain the relationship with the number of bits of the analog-to-digital converter. Theoretically, the higher the number of bits of the analog-to-digital converter, the better, and the closer the conversion result is to the true value. However, this view is not absolute, and there are always exceptions. For example, NI's DSA (dynamic signal analysis) data acquisition module is usually 24 bits, but its measurement accuracy is very low, and it is mainly used for the measurement and analysis of dynamic signals. To be precise, it should be called 24-bit resolution, not 24-bit accuracy. Therefore, when we choose to determine the data acquisition module, we must select the appropriate data acquisition module based on the needs of the measurement object and the manual of the data acquisition module.
Finally, let's go back to the measurement of DC voltage of the double-integral voltmeter. Because the measurement is 2 times/s, the frequency (fluctuation) equivalent to the change of the DC signal is 1Hz/s. In fact, the change of the DC signal is much lower than this, so the DC voltage measurement fully meets the sampling theorem.
It can be said that the sampling theorem is the core theorem of virtual instruments. Computer-based testing, measurement and analysis also rely on the sampling theorem.
Summarizing the measurement principles of virtual instruments can give us this basic understanding. The measurement process of virtual instruments is to collect the data of the measured signal as the original data of the virtual instrument under the condition of satisfying the sampling theorem, and the processing of these original data will rely on software. The results of software processing are precisely based on the user's requirements.
Is there any essential difference between the measurement method of virtual instruments and that of traditional instruments?
1.3.3 Virtual instruments have changed the measurement methods and concepts of traditional instruments
In fact, the emergence of virtual instruments has broken the traditional measurement methods and concepts. Here are a few examples to illustrate the changes that virtual instruments have brought to the traditional instrument measurement methods and data processing methods.
Example 1-1 Changes in measurement methods - sampling effective value measurement (no AC-DC converter required)
Example 1-1 Changes in measurement methods - sampling effective value measurement (no AC-DC converter required)
Measuring the effective value of a periodic signal generally requires an AC-DC converter. The most common conversion method is [5]:
- Thermoelectric converter - multi-element thermocouple, precision op amp, DC digital voltmeter
- Analog operational converters - precision analog multipliers, precision op amps, DC digital voltmeters
- Logarithmic converter - precision logarithmic converter, precision op amp, DC digital voltmeter
- Semiconductor thermoelectric converter - solid-state semiconductor device (patent), precision operational amplifier, DC digital voltmeter
- Sampling converter - embedded processor, precision ADC converter, specially designed calculation processing software
[page]
In fact, no matter which of the above methods is used to measure the effective value of a periodic signal, it is based on the definition of the effective value. The definition of the effective value is derived from the thermoelectric effect.
Joule's law shows that a resistor dissipates the power generated by the voltage or current on it in the form of heat. The heat generated is proportional to the power.
Equation 1-1 gives the mathematical expression of the effective value derived from the thermoelectric effect.
In fact, no matter which of the above methods is used to measure the effective value of a periodic signal, it is based on the definition of the effective value. The definition of the effective value is derived from the thermoelectric effect.
Joule's law shows that a resistor dissipates the power generated by the voltage or current on it in the form of heat. The heat generated is proportional to the power.
Equation 1-1 gives the mathematical expression of the effective value derived from the thermoelectric effect.
Where: u(t) is the measured signal
T is the period of the measured signal, and the reciprocal is the frequency of the measured signal
The following briefly introduces the basic conversion principle of AC-DC converters using semiconductor thermoelectric converters as an example [6].
Semiconductor thermoelectric converters are also called solid-state true effective value converters, which are based on the principle of thermoelectric conversion. Fluke Corporation of the United States designed and developed this thermoelectric converter based on semiconductor technology in the 1970s. After several improvements, it has reached a practical and perfect level. It is also the core component of the AC measurement part of instruments such as Fluke 8508, Fluke 5790, and Fluke 792A.
T is the period of the measured signal, and the reciprocal is the frequency of the measured signal
The following briefly introduces the basic conversion principle of AC-DC converters using semiconductor thermoelectric converters as an example [6].
Semiconductor thermoelectric converters are also called solid-state true effective value converters, which are based on the principle of thermoelectric conversion. Fluke Corporation of the United States designed and developed this thermoelectric converter based on semiconductor technology in the 1970s. After several improvements, it has reached a practical and perfect level. It is also the core component of the AC measurement part of instruments such as Fluke 8508, Fluke 5790, and Fluke 792A.
This is a very creative invention, which is a patent of Fluke. It uses semiconductor technology to realize a solid-state thermoelectric converter based on the principle of thermoelectric conversion.
Its conversion principle is very simple. The input voltage Vin causes the resistor R1 to generate a certain amount of heat. The Vbe of the transistor Q1, which is integrated with the resistor, will sense this temperature change, causing its output to change, so that the differential amplifier generates a DC output to be added to the resistor R2. R2 has the same function as R1. The heat it generates changes the Vbe of Q2. The final result of automatic adjustment makes Vin=Vout, completing the task of AC-DC conversion.
Please note that during the design, R1 and Q1, R2 and Q2 are placed on two isolated islands with good thermal isolation to ensure the accurate absorption of heat by the PN junction.
This conversion method is actually automatically realized due to the role of the operational amplifier, which should not be difficult to understand. The output of Vout is a DC voltage equal to the effective value of the Vin input. Finally, after the linearization correction of the computer, it can reach the level of the AC conversion standard.
Let's take a look at the measurement method of the virtual instrument. According to formula 1-1, under the premise of satisfying the sampling theorem, if the measured voltage signal u(t) is sampled n times, its discrete sampling value is ui. In this way, it is easy to obtain the mathematical expression of the effective value of the discrete signal:
Its conversion principle is very simple. The input voltage Vin causes the resistor R1 to generate a certain amount of heat. The Vbe of the transistor Q1, which is integrated with the resistor, will sense this temperature change, causing its output to change, so that the differential amplifier generates a DC output to be added to the resistor R2. R2 has the same function as R1. The heat it generates changes the Vbe of Q2. The final result of automatic adjustment makes Vin=Vout, completing the task of AC-DC conversion.
Please note that during the design, R1 and Q1, R2 and Q2 are placed on two isolated islands with good thermal isolation to ensure the accurate absorption of heat by the PN junction.
This conversion method is actually automatically realized due to the role of the operational amplifier, which should not be difficult to understand. The output of Vout is a DC voltage equal to the effective value of the Vin input. Finally, after the linearization correction of the computer, it can reach the level of the AC conversion standard.
Let's take a look at the measurement method of the virtual instrument. According to formula 1-1, under the premise of satisfying the sampling theorem, if the measured voltage signal u(t) is sampled n times, its discrete sampling value is ui. In this way, it is easy to obtain the mathematical expression of the effective value of the discrete signal:
As can be seen from formula 1-2, virtual instrument measurement is based on the sampling measurement principle. By directly sampling the measured signal and then processing it through software calculation, the effective value of the measured signal can be obtained. We need to note that: No AC-DC converter is required in this process (the first four types listed above require different types of AC-DC converters). Obviously, the measurement method based on the sampling principle of virtual instruments not only greatly simplifies the measurement circuit from the test method, but also ensures accurate measurement.
Although the fifth measurement method listed above is also based on sampling. However, the complexity of embedded system hardware design and the difficulty of software development are obviously much greater than virtual instruments.
In fact, this measurement method of virtual instruments is more effective in the process of power and electric energy measurement. Those who have engaged in analog circuit design must have had a deep understanding of how complex and difficult to adjust analog multipliers are, and the accuracy, linearity and bandwidth are difficult to be effectively guaranteed. Digital sampling combined with digital multipliers can improve the technical indicators of analog multiplication by at least one to two orders of magnitude (one order of magnitude generally refers to a 10-fold relationship).
Example 1-2 Change in measurement method - sampling frequency measurement (using digital signal processing software)
Although the fifth measurement method listed above is also based on sampling. However, the complexity of embedded system hardware design and the difficulty of software development are obviously much greater than virtual instruments.
In fact, this measurement method of virtual instruments is more effective in the process of power and electric energy measurement. Those who have engaged in analog circuit design must have had a deep understanding of how complex and difficult to adjust analog multipliers are, and the accuracy, linearity and bandwidth are difficult to be effectively guaranteed. Digital sampling combined with digital multipliers can improve the technical indicators of analog multiplication by at least one to two orders of magnitude (one order of magnitude generally refers to a 10-fold relationship).
Example 1-2 Change in measurement method - sampling frequency measurement (using digital signal processing software)
Frequency measurement of periodic signals has long relied on digital frequency meters. Its measurement principle is to count and fill with the signal frequency in unit time to obtain the frequency value of the measured signal. When the frequency of the measured signal is relatively low, the period measurement method is used. The period measurement method depends on whether the trigger time when the measured signal crosses zero is accurate. This measurement method has no problem measuring pure sine waves. For signals containing harmonic components, filtering must be performed first to avoid the adverse effects of harmonic components on the zero-crossing trigger of the signal. However, when the harmonic components are large, even filtering cannot achieve satisfactory measurement results.
The frequency measurement of virtual instruments still relies on sampling technology, and the only consideration for the signal is whether it can meet the requirements of the sampling theorem. The collected data is analyzed and processed by software and the measurement results are finally obtained. In the LabVIEW signal analysis library, there is a VI called "Extract Single Tone Information.vi", which can be used to extract the frequency value of the signal. Its analysis principle is based on FFT transformation. Therefore, it has a high noise suppression ability and can easily measure and determine the frequency value of harmonic signals.
This is extremely beneficial for sound and vibration signal testing and analysis.
The measurement method of virtual instruments only needs to obtain raw data through acquisition, and the realization of measurement functions depends on the selected analysis and processing functions, thereby realizing multifunctional measurements. For example, the data collected once can realize effective value measurement, frequency measurement, phase or harmonic distortion measurement, etc.
Example 1-3 Changes in measurement concepts - sampling multi-point and multi-cycle measurement (different from the past)
The frequency measurement of virtual instruments still relies on sampling technology, and the only consideration for the signal is whether it can meet the requirements of the sampling theorem. The collected data is analyzed and processed by software and the measurement results are finally obtained. In the LabVIEW signal analysis library, there is a VI called "Extract Single Tone Information.vi", which can be used to extract the frequency value of the signal. Its analysis principle is based on FFT transformation. Therefore, it has a high noise suppression ability and can easily measure and determine the frequency value of harmonic signals.
This is extremely beneficial for sound and vibration signal testing and analysis.
The measurement method of virtual instruments only needs to obtain raw data through acquisition, and the realization of measurement functions depends on the selected analysis and processing functions, thereby realizing multifunctional measurements. For example, the data collected once can realize effective value measurement, frequency measurement, phase or harmonic distortion measurement, etc.
Example 1-3 Changes in measurement concepts - sampling multi-point and multi-cycle measurement (different from the past)
In embedded system design, due to the limitations of CPU computing power and memory size, the measurement of AC signals is basically carried out using equal-period measurement (essentially a single-period measurement method). The sampling of the measured signal needs to satisfy the following formula:
Where: T——the period of the measured signal
n——the number of sampling points in one period of the measured signal, constant
Ts——the sampling time interval
The sampling relationship that satisfies equations 1-3 is called equal-period sampling. The essence of equal-period sampling is that the sampling frequency must be an integer multiple of the signal period (a conventional constant), so that leakage caused by sampling truncation can be avoided.
In fact, due to the stability of the signal itself and the existence of noise interference, as well as the relationship between the signal frequency and the sampling frequency that is not an integer multiple, it is usually difficult to meet the requirements of equations 1-3. This will lead to measurement errors caused by leakage after sampling truncation [7].
In order to solve this problem, most embedded system designs use windowing and equal-period quasi-synchronous sampling methods (the concept of synchronization here is different from synchronous sampling. Synchronization here refers to the synchronization of the sampling frequency with the period of the measured signal, including hardware synchronization or software synchronization). Of course, whether windowing or using hardware synchronization or software synchronization greatly increases the complexity of the system.
So can such problems be solved or avoided in virtual instruments?
In virtual instrument sampling measurement, since a large number of sampling points can be selected, the impact of leakage caused by sampling truncation can be greatly reduced.
At the same time, the most desirable thing about virtual instrument sampling measurement is that the sampling of virtual instruments is a multi-cycle continuous sampling, which can also reduce the impact of leakage. The combined effect of the two can basically reduce the impact of leakage to a completely negligible level.
For example, in the measurement of 50Hz power frequency signal, if the sampling frequency Fs is set to 50kHz, and the number of data points to be read is set to 50000S/s. It is equivalent to extracting 50 cycles of data for analysis and processing each time, and each cycle contains 1000 data points. With the powerful computing power of commercial computers and the processing advantages of graphical software, this multi-point, multi-cycle measurement can hardly detect the impact of leakage. Practice has verified that its measurement results are stable and accurate.
Obviously, this is a unique advantage of virtual instruments. This is difficult for embedded systems to do due to the huge amount of data processing and complex calculation methods.
These examples show that virtual instrument sampling measurement can simplify the measurement method and change the measurement concept. For example, the hardware of the virtual instrument is a data acquisition module (standard module), which abandons the AC-DC converter and zero-crossing trigger circuit, counter and other dedicated hardware circuits in traditional instruments. Different software processing methods provide measurement analysis results. The ultimate effect is to improve the credibility of the measurement results. The beneficiaries are still the users of virtual instruments.
In other words: the data obtained by sampling does not determine the measurement function. The realization of the measurement function depends on what analysis and processing function (VI) is used. The change of measurement function is realized by software. Therefore, its measurement function can be defined and realized by the user or designer himself.
In fact, virtual instruments have more features.
Previous article:LabVIEW Notes
Next article:Virtual Instrument Composition
Recommended Content
Latest Test Measurement Articles
- Keysight Technologies Helps Samsung Electronics Successfully Validate FiRa® 2.0 Safe Distance Measurement Test Case
- From probes to power supplies, Tektronix is leading the way in comprehensive innovation in power electronics testing
- Seizing the Opportunities in the Chinese Application Market: NI's Challenges and Answers
- Tektronix Launches Breakthrough Power Measurement Tools to Accelerate Innovation as Global Electrification Accelerates
- Not all oscilloscopes are created equal: Why ADCs and low noise floor matter
- Enable TekHSI high-speed interface function to accelerate the remote transmission of waveform data
- How to measure the quality of soft start thyristor
- How to use a multimeter to judge whether a soft starter is good or bad
- What are the advantages and disadvantages of non-contact temperature sensors?
MoreSelected Circuit Diagrams
MorePopular Articles
- Innolux's intelligent steer-by-wire solution makes cars smarter and safer
- 8051 MCU - Parity Check
- How to efficiently balance the sensitivity of tactile sensing interfaces
- What should I do if the servo motor shakes? What causes the servo motor to shake quickly?
- 【Brushless Motor】Analysis of three-phase BLDC motor and sharing of two popular development boards
- Midea Industrial Technology's subsidiaries Clou Electronics and Hekang New Energy jointly appeared at the Munich Battery Energy Storage Exhibition and Solar Energy Exhibition
- Guoxin Sichen | Application of ferroelectric memory PB85RS2MC in power battery management, with a capacity of 2M
- Analysis of common faults of frequency converter
- In a head-on competition with Qualcomm, what kind of cockpit products has Intel come up with?
- Dalian Rongke's all-vanadium liquid flow battery energy storage equipment industrialization project has entered the sprint stage before production
MoreDaily News
- Allegro MicroSystems Introduces Advanced Magnetic and Inductive Position Sensing Solutions at Electronica 2024
- Car key in the left hand, liveness detection radar in the right hand, UWB is imperative for cars!
- After a decade of rapid development, domestic CIS has entered the market
- Aegis Dagger Battery + Thor EM-i Super Hybrid, Geely New Energy has thrown out two "king bombs"
- A brief discussion on functional safety - fault, error, and failure
- In the smart car 2.0 cycle, these core industry chains are facing major opportunities!
- The United States and Japan are developing new batteries. CATL faces challenges? How should China's new energy battery industry respond?
- Murata launches high-precision 6-axis inertial sensor for automobiles
- Ford patents pre-charge alarm to help save costs and respond to emergencies
- New real-time microcontroller system from Texas Instruments enables smarter processing in automotive and industrial applications
Guess you like
- Byte alignment for 32-bit embedded systems
- Layman asks questions about ZigBee
- [Bluesun AB32VG1 RISC-V board "encountered" RTT] Encountered a problem, please solve it
- Analysis of common reasons for howling in switching power supplies
- Pressure sensor temperature compensation
- 【e-Network Alliance e-Select】Show your order
-
" [Youliao-ADI Instrumentation]">
A collection of wonderful resources such as "Instrumentation Collection
" [Youliao-ADI Instrumentation] - PID regulation problem
- E2lite emulator connection failed
- Miniaturized millimeter wave sensors enabled by CMOS technology