While there are many competing protocols based on this physical layer, the current global leader is the ZigBee organization, which has published standards covering everything from home automation and smart energy to retail and telecommunications services to remote controls and input devices. The ZigBee protocol provides a mesh network of devices that supports communication over large areas and hundreds or even thousands of devices. ZigBee-compliant devices from different sources can communicate with each other seamlessly if implemented in a consistent manner.
As you might imagine, a vibrant industry has formed around bare integrated circuits and modules that usually come with antennas and are approved by the FCC or other local agencies. Embedded products are available only with radio circuits that use the IEEE 802.15.4 low-level protocol and require a separate microcontroller or microprocessor to handle the ZigBee software and applications. There are some integrated circuits and modules on the market that have built-in microcontrollers for running ZigBee or other protocol software. Many of these integrated circuits and modules have undetermined I/O pins, so the complete product may require a module with fewer content and sensors and/or actuators and a housing. In addition, these modules can be accompanied by power amplifiers and receiver low-noise amplifiers (LNAs). Power amplifiers and low-noise amplifiers can significantly increase the radio range, although they are more expensive and consume more power.
For any of these choices, a printed circuit test board is needed to support the integrated circuit or module. A power supply with sufficient peak power and immunity to noise is also required. If a chip-level radio is selected, appropriate antenna interface circuitry is also required.
As the ZigBee protocol becomes more common in a variety of embedded systems and applications, engineers need to be able to quickly and efficiently confirm and verify ZigBee module performance. This system-level task is further complicated by the presence of radio frequency (RF) signals and the need to consider the interaction of analog, digital, and RF signals. As described later, a new type of oscilloscope called a mixed domain oscilloscope (MDO, named for its inclusion of spectrum analysis circuitry) can help ease the ZigBee test task. First, let's look at the main design considerations and the associated tradeoffs.
ZigBee Design Considerations
With the wide variety of end applications and thousands of products that can be adapted to ZigBee technology, there is no such thing as a one-size-fits-all approach in the world of ZigBee. ZigBee radio options vary in integration from vendor to vendor, ranging from radio ICs to fully integrated modules with microcontrollers, power amplifiers, antennas and low noise amplifiers. Given this variety, designers must understand the tradeoffs involved. Key areas to consider include:
Cost – Modules have a significant tradeoff between bill of materials and design and regulatory approval costs compared to ICs. Modules cost significantly more than radio ICs, even in high volumes, due to the support components and assembly labor required. Some of the extra cost comes from duplicate printed circuit board material, but much of it comes from module design costs and returns to the module manufacturer. However, the cost of designing a radio module and obtaining the necessary approvals is high. ZigBee Alliance testing and approvals add to the cost of IC-based designs. Experience shows that the cost balance point between integrated ICs and modules is usually around 10,000 - 25,000 units.
Development Time – Pre-certified modules are available for sale as soon as the product is complete. Regulatory approval for IC-level designs can be as quick as one month, but often takes longer. Typically, this time is built into the development process because the product needs to be close to final form and the software needs to be functional before approval testing can begin.
Form Factor – Designing a custom radio starting with an integrated circuit provides flexibility in the configuration of the radio circuitry. With a custom design, the radio circuitry can take advantage of spaces that a module cannot fit into because of the overall configuration of the product. Typically, commercially available modules have all of their parts arranged on the same side of the printed circuit board so the module can be soldered to the motherboard. In a custom design, the parts can be arranged in any configuration or on both sides of the board.
Protocol Flexibility – Many manufacturers of modules and integrated circuits with embedded controllers do not provide source code for ZigBee or other communication software. This greatly limits the designer’s ability to add custom functionality.
Special Requirements – For some applications, the hardware features provided by a module or integrated circuit that integrates the radio and microcontroller may not be sufficient. While there is always the option of adding a second microcontroller, this would increase the total cost beyond the desired level. In other cases, features that are not available on the market may need to be provided. For example, U.S. regulations allow radio output power to reach up to 1 watt, but few modules can reach this level.
Antenna Type and Placement — The module’s PCB may have an antenna in the form of a printed pattern or a “chip” antenna with an external antenna. If the antenna on the module is inside a shielded enclosure or is located too close to other components in the final package design, its performance may be affected. Some modules on the market have connectors for connecting external antennas. However, it is legal to use only antennas that are certified for use with the module. If it is necessary to use an antenna that is not supported by the module manufacturer—for example, because higher gain is required—approval from the appropriate agencies is required (which takes time and incurs costs).
Testing and Verification of Integrated Radios
After the radio implementation has been decided, the corresponding PCB layout has been decided, and any necessary software has been written, a lot of testing is required to ensure that the communication is good.
For most applications, there is serial communication between the radio system and other parts of the product. For example, many integrated circuits and modules use a four-wire serial peripheral interface (SPI) connection to control the radio integrated circuit and related components, such as power amplifiers. To select the frequency channel, output power level, and many other parameters, internal registers need to be set through SPI commands. The SPI is used to control general-purpose port pins used to control power amplifiers or other devices. SPI is also used to send packets of data to the integrated circuit or module, as well as to send commands to transmit packets of data. Received data is also transmitted over the SPI bus.
Software in the microcontroller (whether integrated or standalone) needs to provide the highest level of protocol (ZigBee or other) as well as control the power of the radio and run other aspects of the product. In many applications, the timing of the radio signal transmission is so important that the radio will not transmit when some other power-consuming parts of the product are in operation and the power supply voltage drops below acceptable levels.
Some of the key tests used to verify radio operation include RF and power measurements, digital commands, spurious signals and interference. To illustrate these tests, a Microchip Technologies IEEE 802.15.4 amplified radio module (MRF24J40MB) is used with the Explorer 16 demonstration board. The screen shot is from the Tektronix MDO4000 Series Mixed Domain Oscilloscope, the world's first oscilloscope to provide simultaneous time-correlated views of RF, analog and digital signals. Setup and data commands are sent through a PC to support manual control. Figure 1 shows the test setup. A direct connection to the radio is used to simplify power and other measurements. RF measurements can also be made using a calibrated antenna.
Figure 1. Test connections between the Microchip Technologies MRF24J40MB and Explorer 16 Demo Board ZigBee radio module/test board and a mixed domain oscilloscope.
RF and power measurements
IEEE 802.15.4(包括ZigBee)标准的信道频率间隔为5 Mhz。20dB信道带宽应当显著小于信道频率间隔。图2所示的2.3 MHz测得被占用带宽完全符合该规格。输出功率大致在20 dBm以内。屏幕显示了输出频谱(屏幕下方)以及带宽和电源的直接测量结果。在此频率范围内,测试电缆衰减约为2 dB,所以电源测量结果在预期范围之内。
图2。在该图中,橙色条代表频域显示相对于时域测量结果的频谱时间。
屏幕上半部底部的橙色条代表频谱迹线的显示时限。频谱时间定义为窗口成形因子除以分辨率宽度的结果。在本例中,使用默认的Kaiser FFT函数(成形因子2.23)和11 kHz的分辨率带宽,频谱时间计算结果约为200 µs。在时域窗口上移动频谱可取得数据包发射期间任何时刻的频谱和测量结果。该采集仅在开启无线电数据包发射后相关。
混合域示波器的射频采集可执行射频信号的功率和被占用带宽测量。由于它也采集射频采集的时间记录,所以可用一个数字降压转换过程来产生I(真实)和Q(假想)数据。每个I和Q数据样点代表射频输入与电流中心频率的偏差。利用该分析可从所记录的数据来计算射频幅度-时间迹线。[page]
Figure 3 shows an additional RF amplitude-versus-time trace added to the display of Figure 4. This demonstrates that the current and voltage measurement events in Figure 5 are related to the turn-on of the RF transmission.
Figure 3. Power and occupied bandwidth measurements, including the associated RF amplitude-versus-time, and supply current and drain voltage measurements.
The green trace (Trace 4) shows the current consumed by the module. During packet transmission, this current consumption is nearly 200 mA (note the direct measurement of 174 mA), so the power supply must be designed to support this load. The yellow trace (Trace 1) shows the effect of this current on the power supply. The voltage drop is only about 70 mV, which should be excellent (note the direct peak-to-peak measurement of 72 mV). The orange trace (Trace A) in the
upper portion of the screen shows the RF signal amplitude-versus-time. The input current rises in two steps. In the first step, the RFIC is turned on. There is then a delay to allow the synthesizer to stabilize before the power amplifier is turned on. The rise in RF power coincides with the second current rise. The turn-on time is about 100 µs.
It is often desirable to understand the performance of a radio transmitter during low battery conditions or supply current limiting conditions in order to understand the margin of radio compliance performance. In Figure 6, a 1.5Ω resistor is placed in series with the module to simulate the effect of a nearly depleted battery. The module consumes only a few milliamps less current, but the voltage drop is around 230 mV. Based on the RF power measurement, the output power is reduced by 1 dB and there is a slight increase in adjacent channel noise as seen in the spectrum display. This lower output power is also evident in the amplitude-time trace (Trace A).
Figure 4. Spectrum and measurement results of studying low power performance behavior by placing a resistor in series with the module supply.
Digital Commands
The radio integrated circuit and module need to be set up to meet the operational requirements of the specific application and any protocol-specific settings. A mixed domain oscilloscope allows decoding of SPI commands to the ZigBee module. Figure 5 shows a digital capture of the SPI commands with the same time range as Figure 2. The decode function is enabled but is not readable in this time range. Figure 5.
Packet decode of the SPI digital signals (SPI - MOSI and MISO) is added to the display.
In this example, the trigger condition for analog, digital, and RF acquisitions is that the drain current on trace 4 is above 130 mA. All time domain measurements in the upper left display at center show the events before the current exceeds this level when the RF is turned on. This includes digital decode, analog (voltage and current), and RF-time relationships. From this information, it can be seen that the digital command occurs approximately 600 ms before the RF event. [page] The
purple trace shows the position of the decoded data in the time domain. The pan and zoom functions can be used to read the digital waveform and the decoded data. The readback command and data on the SPI (MISO) can be read or triggered to confirm the command is correct and verify the operation of the radio. The
mixed domain oscilloscope architecture simplifies measurements between triggering on an SPI command and the associated RF event. In Figure 6, the trigger event is now an SPI command {37} - the radio transmit trigger command. The markers on the time domain display show that the SPI command to current draw (at the beginning of the RF transmitter turn on) is now 1.768 ms.
Figure 6. Subsequent triggering on the SPI command shows the delay between the command and the radio turn on.
In the previous example in Figure 5, the command to turn-on delay was approximately 600 µs. The actual event in Figure 6 is nearly three times longer. This demonstrates that the behavior of the ZigBee radio is in fact meeting one of the physical layer performance requirements of IEEE 802.15.4. The ZigBee radio uses a pseudo-random delay between the command and turn-on events to enable the radio to listen for other ZigBee radio transmitters or other radio interference channels.
Registered Signals
When confirming the operation of the radio, it is important to ensure that there are no registered signals that could cause interference. Figure 7 shows that there are no significant registered signals in the ZigBee operating band. Note that the transmit frequency of the associated module in this figure is set to the center frequency of the 2.45 GHz band. The marker function is used here to measure the peak signal. With the resolution bandwidth now set to 100 kHz, the spectrum time is now reduced to just over 20 ms.
图7。2.45 GHz的宽频扫描可提供关于整个ISM频带的信号视野。
寻找频谱其他部分中的信号也很重要。例如,下一步可能是看被发射信号的第二谐波的频率范围(在其仍然与射频传输开启期间的电流消耗的触发水平有关时)。在本例中,我们只在第二谐波中发现一个小信号,其他频率没有任何显著发现。标记所在位置的第二谐波信号比基波约低35 dB,这完全在适用此类无线电发现器的RCC规则的范围之内。
干扰
对于某些应用,使用天线来进行测量,以识别可能干扰所开发无线电的其他无线电来源是很有用的。在图8中,MDO使用了一个干扰天线来寻找可能的干扰无线电来源。中心频率为2.46 MHz的宽频信号来自位于同一座大楼中的Wi-Fi基站。该基站覆盖ZigBee无线电能够使用的大量信道。在针对该无线电模块的应用中,避免使用该频率附近的信道是明智的,因为ZigBee无线电的射程可能受到影响,或者无线电信号被完全阻截。
图8。显示无线局域网干扰信号,以评估互操作性测试期间的影响。
在本例中,射频触发器只使用了MDO的频谱分析仪选项来捕获感兴趣频带中的信号。主要参考标记显示这是一个相当强的信号。手动标记(a)和(b)是干扰源的频率范围的读数。此干扰的频率范围和功率会使ZigBee信道17-19不可用。当然,包括ZigBee在内的大多数协议将会扫描此类干扰并将操作移动到干净的信道。复杂程度稍低一些的协议可能需要对操作信道进行手动调节。
总结
在实现ZigBee或其他IEEE 802.15.4无线电之前有许多选择可供考虑。最佳方案的选择取决于许多因素,包括开发时间、单位成本-设计和批准成本,以及诸多特殊要求,如可用空间、形状因素,另外还有针对无线电的特殊电气要求。
无论选择哪种方案,为了确保无线系统的正常工作,都要进行大量的测量。射频测量包括检查射频输出频率、输出振幅、被占用带宽和寄生输出。数据包定时、电流消耗和电源噪声的确认也很重要。此外,确认无线电设置了正确的数字配置信息以及收到正确的数据也很重要。如本文所示,能够关联模拟、数字和射频信号的混合域示波器非常适用于完成该任务,并可帮助设计人员在确认和验证ZigBee模块的过程中节省时间和减轻工作量。
Previous article:How to accurately measure the signal edge parameters of CAN nodes?
Next article:Software-defined radio requires advanced testing
Recommended ReadingLatest update time:2024-11-16 13:48
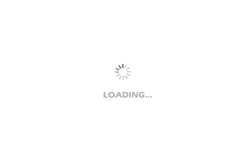
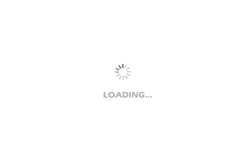
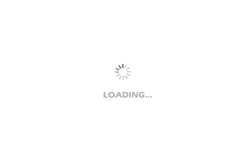
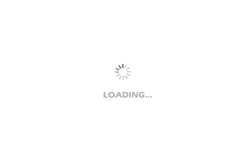
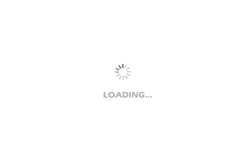
- Popular Resources
- Popular amplifiers
-
Wireless Sensor Network Technology and Applications (Edited by Mou Si, Yin Hong, and Su Xing)
-
Detailed explanation and engineering practice of unmanned monitoring technology (Xie Jianbin, Li Peiqin, Yan Wei, Liu Tong, Lin Chenglong, Hong Quanyi, Zhou Hongfei, Cui Yibing)
-
Introduction to Wireless Sensor Networks (Edited by Ma Sasa et al.)
-
Introduction to the Internet of Things (Liu Yunhao)
- Keysight Technologies Helps Samsung Electronics Successfully Validate FiRa® 2.0 Safe Distance Measurement Test Case
- From probes to power supplies, Tektronix is leading the way in comprehensive innovation in power electronics testing
- Seizing the Opportunities in the Chinese Application Market: NI's Challenges and Answers
- Tektronix Launches Breakthrough Power Measurement Tools to Accelerate Innovation as Global Electrification Accelerates
- Not all oscilloscopes are created equal: Why ADCs and low noise floor matter
- Enable TekHSI high-speed interface function to accelerate the remote transmission of waveform data
- How to measure the quality of soft start thyristor
- How to use a multimeter to judge whether a soft starter is good or bad
- What are the advantages and disadvantages of non-contact temperature sensors?
- Innolux's intelligent steer-by-wire solution makes cars smarter and safer
- 8051 MCU - Parity Check
- How to efficiently balance the sensitivity of tactile sensing interfaces
- What should I do if the servo motor shakes? What causes the servo motor to shake quickly?
- 【Brushless Motor】Analysis of three-phase BLDC motor and sharing of two popular development boards
- Midea Industrial Technology's subsidiaries Clou Electronics and Hekang New Energy jointly appeared at the Munich Battery Energy Storage Exhibition and Solar Energy Exhibition
- Guoxin Sichen | Application of ferroelectric memory PB85RS2MC in power battery management, with a capacity of 2M
- Analysis of common faults of frequency converter
- In a head-on competition with Qualcomm, what kind of cockpit products has Intel come up with?
- Dalian Rongke's all-vanadium liquid flow battery energy storage equipment industrialization project has entered the sprint stage before production
- Allegro MicroSystems Introduces Advanced Magnetic and Inductive Position Sensing Solutions at Electronica 2024
- Car key in the left hand, liveness detection radar in the right hand, UWB is imperative for cars!
- After a decade of rapid development, domestic CIS has entered the market
- Aegis Dagger Battery + Thor EM-i Super Hybrid, Geely New Energy has thrown out two "king bombs"
- A brief discussion on functional safety - fault, error, and failure
- In the smart car 2.0 cycle, these core industry chains are facing major opportunities!
- The United States and Japan are developing new batteries. CATL faces challenges? How should China's new energy battery industry respond?
- Murata launches high-precision 6-axis inertial sensor for automobiles
- Ford patents pre-charge alarm to help save costs and respond to emergencies
- New real-time microcontroller system from Texas Instruments enables smarter processing in automotive and industrial applications