Figure 1 Dead time
When a digital oscilloscope is working, it will always collect data first, and then process and display the data. One thing that must be understood is that the oscilloscope data sampling speed is much faster than the data processing speed, so it has to stop sampling during data processing. This will inevitably lead to the loss of all waveforms in the dead zone t2 due to no collection. The basic principle of the oscilloscope is shown in Figure 2.
Figure 2 Oscilloscope principle
The parameter corresponding to the dead time of the oscilloscope is the waveform refresh rate of the oscilloscope, also called the waveform capture rate. The waveform refresh rate of the oscilloscope at a specific time can be measured through the Trigger Out interface. The higher the waveform refresh rate of the oscilloscope, the better.
Waveform refresh rate F = 1/(t1+t2) (wfms/s)
Under a specific time base, the waveform time t1 is fixed, so the higher the waveform refresh rate, the shorter the waveform dead time and the fewer waveforms are missed. For example, for T company's MSO4054, under a time base of 50ns/div, the waveform refresh rate can reach a maximum of 50kwfms/s, so the waveform time per second is equal to 50*10*50000 = 25ms, and the dead time is 975ms, so the waveform dead zone is as high as 97.5%, and the effective waveform observed by the user only accounts for 2.5% of the total waveform.
Figure 3 Waveform information observed at a waveform refresh rate of 50 kWfms/s
ZLG's ZDS2022 oscilloscope also has a waveform refresh rate of 330,000 wfms/s at a time base of 50ns/div, making the waveform time per second as long as 231ms, about 9.24 times that of T company's MSO4054. When two oscilloscopes are used to observe the same signal, with the time base adjusted to 200ns/div, ZLG's ZDS2022 can detect signal anomalies in a shorter time, but MSO4054 cannot.
Figure 4 Waveform information observed at a waveform refresh rate of 330,000wfms/s
Nowadays, many engineers still continue to use analog oscilloscopes because they do not have waveform dead zones, but they also have other shortcomings, such as the inability to perform data statistical analysis and recording, which is why the number of analog oscilloscope users is decreasing. In order to reduce the impact of waveform dead zones on signal analysis, it is recommended that you choose an oscilloscope with a high waveform refresh rate when purchasing an oscilloscope.
Many oscilloscope users are concerned about the refresh rate of the oscilloscope. Recently, when our FAE was communicating with customers, many customers were very interested in the high refresh rate of 330,000 frames per second of the ZDS2022 oscilloscope. How is such a high refresh rate achieved? [page]
What is the waveform refresh rate?
The waveform refresh rate is also called the waveform capture rate, which refers to the number of times the waveform is refreshed per second, expressed as waveforms per second (wfms/s). In fact, the process from the oscilloscope acquiring the signal to displaying the signal waveform on the screen is composed of several capture cycles. A capture cycle includes sampling time and dead time. The analog signal is converted into a digital signal through ADC sampling and quantization and stored at the same time. The time of the entire sampling and storage process is called the sampling time. The oscilloscope must perform measurement, calculation, display and other processing on the stored data before starting the next sampling. This period of time is called the dead time. During the dead time, the oscilloscope does not perform waveform acquisition. After one capture cycle is completed, it will enter the next capture cycle. The reciprocal of the capture cycle is the waveform refresh rate, as shown in Figure 1.1, waveform refresh rate = 1/(Tacq+Tdeat).
Figure 5 Schematic diagram of oscilloscope sampling process
What are the factors that affect the waveform refresh rate?
Sampling time and dead time
As shown in Figure 5, the waveform refresh rate is the reciprocal of Tacq (sampling time) and Tdeat (dead time), where the sampling time is determined by the sampling pane of the oscilloscope screen. It is calculated by multiplying the horizontal base gear by the number of horizontal grids. Once the horizontal time base is determined, the sampling time will be fixed.
The dead time is determined by the processing capability of the oscilloscope. When the oscilloscope's data processing capability is insufficient, the collected big data cannot be processed in time, the dead time will become longer, and the refresh rate will decrease. When the oscilloscope's data processing capability is strong, the dead time will become shorter, and the corresponding refresh rate will be very high. Therefore, the dead time is an important factor affecting the refresh rate.
Trigger holdoff time
Increasing the trigger holdoff time is equivalent to increasing the dead time in disguise, because during the holdoff period, the trigger circuit is closed and the trigger function is suspended. Even if there is a signal waveform that meets the trigger conditions, the oscilloscope will not trigger, so it will also affect the refresh rate. However, the trigger holdoff time does not refer to the dead time.
When triggering a large-cycle repetitive waveform, there are many waveform points in the waveform that meet the trigger conditions, which makes the triggered waveform unstable. In order to obtain a stable triggered waveform, we can set the trigger holdoff time so that the waveform is triggered at the same point each time and the triggered waveform is displayed stably. As shown in Figure 1.2, the holdoff time can be set to a value of >200ns but <600ns.
Figure 6 Trigger holdoff time
How to calculate dead time?
How is the dead time, which has an important impact on the refresh rate, calculated?
When capturing an abnormal pulse with a pulse width of 40ns~60ns, the appropriate horizontal time base gear can be set at 50ns/grid. At this time, the ZDS2022 oscilloscope has a waveform refresh rate of 330,000 frames/second, which means that the total capture time occupied by each trigger sampling is T=1s/330KHz=3.03us, and the effective sampling time is 50ns/divX14 (ZDS2022 oscilloscope has 14 grids in the horizontal direction) = 700ns. Then the dead time percentage is (3030-700)/3030=76.89%.
To capture the same abnormal pulse, at the same time base, if the T oscilloscope has a refresh rate of 50K frames/second, it means that the total time occupied by each trigger sampling is T=1S/50KHz=20us, and the effective sampling time is 50ns/divX10 (the oscilloscope has 10 grids horizontally) = 500ns, then the dead time percentage is (20000-500)/20000=97.5%.
The longer the dead time, the lower the probability of capturing an occasional signal. When a small-probability abnormal waveform appears in the dead time, the oscilloscope will not capture the abnormality, which will have a great impact on signal debugging.
How can the ZDS2022 oscilloscope achieve a high refresh rate?
So why can the ZDS2022 oscilloscope achieve a refresh rate of up to 330,000 frames per second? The dead time is as low as 76.89%, which is 21.13% lower than the 97.5% dead time of ordinary oscilloscopes!
Figure 7 Waveform synthesizer block diagram
The ZDS2022 oscilloscope uses ultra-large-scale FPGA for waveform synthesis, all of which are fully hardware accelerated;
The ZDS2022 oscilloscope uses ultra-large-scale FPGA integrated waveform display memory, high bus bandwidth, which greatly reduces data processing time, and adopts multi-threaded parallel processing;
The waveform synthesis of the ZDS2022 oscilloscope is all processed using optimized algorithms.
Summarize
The refresh rate of the oscilloscope directly determines the ability to capture abnormal glitches. Only by truly understanding the essence of the refresh rate can you correctly understand the refresh rate indicator of the oscilloscope. The ZDS2022 oscilloscope has a refresh rate of 330,000 frames per second, which can quickly capture waveform anomalies. It is efficient and practical! No matter how much you say, it is better to test it yourself!
Previous article:Microprocessor Hardware Design of Practical Digital Oscilloscope
Next article:A great engineer teaches you how to use an oscilloscope!
Recommended ReadingLatest update time:2024-11-16 19:55
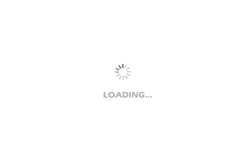
- Keysight Technologies Helps Samsung Electronics Successfully Validate FiRa® 2.0 Safe Distance Measurement Test Case
- From probes to power supplies, Tektronix is leading the way in comprehensive innovation in power electronics testing
- Seizing the Opportunities in the Chinese Application Market: NI's Challenges and Answers
- Tektronix Launches Breakthrough Power Measurement Tools to Accelerate Innovation as Global Electrification Accelerates
- Not all oscilloscopes are created equal: Why ADCs and low noise floor matter
- Enable TekHSI high-speed interface function to accelerate the remote transmission of waveform data
- How to measure the quality of soft start thyristor
- How to use a multimeter to judge whether a soft starter is good or bad
- What are the advantages and disadvantages of non-contact temperature sensors?
- Innolux's intelligent steer-by-wire solution makes cars smarter and safer
- 8051 MCU - Parity Check
- How to efficiently balance the sensitivity of tactile sensing interfaces
- What should I do if the servo motor shakes? What causes the servo motor to shake quickly?
- 【Brushless Motor】Analysis of three-phase BLDC motor and sharing of two popular development boards
- Midea Industrial Technology's subsidiaries Clou Electronics and Hekang New Energy jointly appeared at the Munich Battery Energy Storage Exhibition and Solar Energy Exhibition
- Guoxin Sichen | Application of ferroelectric memory PB85RS2MC in power battery management, with a capacity of 2M
- Analysis of common faults of frequency converter
- In a head-on competition with Qualcomm, what kind of cockpit products has Intel come up with?
- Dalian Rongke's all-vanadium liquid flow battery energy storage equipment industrialization project has entered the sprint stage before production
- Allegro MicroSystems Introduces Advanced Magnetic and Inductive Position Sensing Solutions at Electronica 2024
- Car key in the left hand, liveness detection radar in the right hand, UWB is imperative for cars!
- After a decade of rapid development, domestic CIS has entered the market
- Aegis Dagger Battery + Thor EM-i Super Hybrid, Geely New Energy has thrown out two "king bombs"
- A brief discussion on functional safety - fault, error, and failure
- In the smart car 2.0 cycle, these core industry chains are facing major opportunities!
- The United States and Japan are developing new batteries. CATL faces challenges? How should China's new energy battery industry respond?
- Murata launches high-precision 6-axis inertial sensor for automobiles
- Ford patents pre-charge alarm to help save costs and respond to emergencies
- New real-time microcontroller system from Texas Instruments enables smarter processing in automotive and industrial applications
- SensorTile.box firmware upgrade first experience
- EPLAN P8 Advanced Tutorial (Chinese)
- [ESP32-Audio-Kit Audio Development Board Review] Part 3 play_mp3_control
- PCB manufacturing experience summary (2)
- [Telink B91 Universal Development Kit] Questions about the functions of TX and RX on the burning tool
- FPGA Design Process
- Power supply obstacles + power supply SBC selection and pitfalls
- Sharing of key points on the use of ADI passive components
- Four design considerations for telematics hardware in connected cars
- Wide voltage input USB-C, 5V/3A output adapter reference design