Introduction
PXI stands for PCI eXtensions for Instrumentation, which is a PC-based platform that provides high-performance, high-rugged, and low-cost configuration solutions for measurement and automation systems. PXI combines the PCI (Peripheral Component Interconnect) electrical bus with the rugged, modular European mechanical package in CompactPCI, and adds a dedicated synchronization bus and some key software features. PXI also adds some mechanical, electrical, and software features to define complete systems for test and measurement, data acquisition, and manufacturing applications. These systems provide services for applications such as production test, military and aerospace, machine monitoring, automation, and industrial testing.
NI developed and released the PXI specification in 1997 and launched it as an open industrial specification in 1998 to meet the growing demand for complex instrument systems. Currently, PXI is managed by the PXI Systems Alliance (PXISA), where more than 50 companies have joined together to promote the development of the standard, ensure interoperability, and maintain the PXI specification. Because PXI is an open standard, any equipment manufacturer can produce PXI products. And because a key feature of the PXI specification is interoperability with CompactPCI (a standard proposed by the PCI Industrial Computer Manufacturers Group (PICMG)), the same PXI system can contain both CompactPCI and PXI modules without any conflicts. In
late 2005, the commercial PC industry's bus technology evolved from PCI to PCI Express, which increased the available bus bandwidth. Similarly, the introduction of PXI Express technology in PXI also significantly increased bus bandwidth. PXI integrates PCI Express into the PXI standard to meet more application requirements. PCI Express technology can be integrated into the backplane while maintaining backward compatibility with existing systems with a broad application base. In addition to x1, x4, and x8 links, the system controller slot also supports up to x16 PCI Express links, providing up to 6GB/s bandwidth to the PXI Express backplane. Using PCI Express technology, PXI Express increases the available bandwidth in PXI by more than 45 times, from 132MB/s to 6GB/s, while maintaining software and hardware compatibility with PXI modules. This performance enhancement enables PXI to be used in many new application areas, many of which could only be achieved with expensive dedicated hardware before.
Hardware Architecture
PXI systems consist of three basic parts - chassis, system controller, and peripheral modules.
Figure 1. A standard 8-slot PXI chassis includes an embedded system controller and seven peripheral modules.
PXI Chassis
PXI chassis provide a rugged, modular package for systems, typically in 3U or 6U chassis with 4, 6, 8, 14, or 18 slots. A rack unit (U) is a unit of measurement used to describe the height of a device mounted in a 19- or 23-inch (width) rack. 1U is equal to 44.45 mm (1.75 inches). The size of the device mounted in the rack is usually described in U. Specialized chassis also offer options for AC or DC power and integrated signal conditioning. Many PXI Express chassis can accommodate both PXI and PXI Express peripherals, and some chassis with hybrid slots, such as the NI PXIe-1075, can accommodate PXI Express peripherals or hybrid-compatible PXI devices. These chassis allow a variety of PXI systems to be configured to meet application needs.
Figure 2. Optional standard chassis include NI PXI-1031 (left) and NI PXIe-1075 (right). NI PXI-1031 can choose DC power supply, and NI PXIe-1075 has 18 slots for plugging system controllers and peripherals. The
chassis has a high-performance PXI backplane, which includes PCI bus, timing bus and trigger bus. The PXI modular instrument system adds a dedicated 10MHz system reference clock, PXI trigger bus, star trigger bus and local bus between slots, so as to meet the needs of applications such as advanced timing, synchronization and direct communication between adjacent slots while maintaining all the advantages of PCI bus.
Figure 3. PXI Timing and Triggering Bus – PXI combines industry-standard PC components (such as the PCI bus) with advanced triggering and synchronization extensions on its backplane.
Building on the capabilities of PXI, PXI Express provides additional timing and synchronization capabilities—a 100MHz differential system clock, differential signaling, and a differential star trigger bus. With differential clocking and synchronization, the noise immunity of instrument clocks in a PXI Express system is further improved, and data can be transmitted at higher rates.
Figure 4. The PXI Express timing and triggering bus extends the PXI bus timing and triggering bus capabilities and adds differential system clocks, differential signaling, and differential star triggers to the backplane.
Using these timing and triggering buses, you can develop systems with precise synchronization to meet your application needs. To learn more about the PXI timing and triggering bus specifications, refer to the NI Developer Zone document "PXI Specification Guide."
To learn more about timing and synchronization concepts, refer to the NI Developer Zone guide "Introduction to Distributed Clock Synchronization and IEEE 1588 Precision Clock Synchronization Protocol." [page]
PXI Controllers
Most PXI chassis include a system controller slot in the left-most slot (Slot 1). When choosing the best system controller for your application, you have several options, including an external controller using a desktop, workstation, server, or laptop computer, or a high-performance embedded controller with a Microsoft operating system (Windows Vista/XP) or a real-time operating system (LabVIEW Real-Time). There are two types of external controllers: controlling PXI from a laptop or controlling PXI from a PC.
PXI Embedded Controllers – Embedded controllers eliminate the need for an external PC, making the PXI chassis a complete system. These embedded controllers have standard features such as an integrated CPU, hard drive, RAM, Ethernet, video output, keyboard/mouse, serial, USB, and other peripherals, as well as Microsoft Windows and all device drivers already installed. These features are included with PXI or PXI Express-based systems; you can also choose your operating system, including Windows Vista/XP or LabVIEW Real-Time.
PXI embedded controllers generally use standard PC components in a small PXI package. For example, the NI PXI-8108 controller has a 2.53 GHz Intel Core 2 Duo T9400 dual-core processor, optional hard drive or solid-state drive, and standard PC peripherals such as high-speed USB, Ethernet, serial, and parallel ports.
Figure 5. The NI PXI-8108 controller includes a 2.53 GHz Intel Core 2 Duo T9400 dual-core processor embedded controller Embedded controllers
are ideal for portable systems and "single box" applications where you want to easily move the system from one location to another. For more information, refer to the NI "PXI Controllers" data sheet.
Controlling PXI from a Laptop – Using the NI ExpressCard MXI (Measurement eXtensions for Instrumentation) and PCMCIA CardBus interface kit, you can control a PXI system directly from a laptop through a software-transparent link connection. When powered on, the laptop assumes that all peripheral modules in the PXI system are PCI boards, and you can then control these devices from the laptop. Controlling PXI from a laptop requires inserting an ExpressCard/PCMCIA CardBus card into the laptop and inserting a PXI/PXI Express link module into slot 1 of the PXI chassis, with copper cables connecting the two.
NI ExpressCard MXI Interface Kit PCMCIA CardBus Interface Kit
Figure 6. Controlling PXI from a Laptop
The NI ExpressCard MXI Interface Kit provides a 110 MB/s PCI Express to PCI bridge between a laptop and a PXI chassis. The PCMCIA CardBus Interface Kit provides a 50 MB/s PCI to PCI bridge between a laptop and a PXI chassis. This allows for mobile/portable PXI systems to be controlled from a laptop. Any NI ExpressCard MXI or PCMCIA CardBus-compatible laptop can be used to remotely control a PXI system. For more information, refer to the NI “Controlling PXI from a Laptop” information sheet.
PC Control of PXI – With the NI MXI-Express and MXI-4 interface kits, you can control a PXI system directly from a desktop, workstation, or server computer. You can control a PXI system from a PC through a software-transparent and driver-transparent link. At power-up, the computer system assumes that all peripheral modules in the PXI system are PCI cards, so you can access these devices through the controller. To control PXI through a PC, you need to insert a PCI/PCI Express board into the computer and a PXI/PXI Express module into the first slot of the PXI chassis. The two are connected with a copper cable or fiber optic cable.
Figure 7a. Remote control using dual-port MXI-Express can control two PXI chassis simultaneously with a total throughput of 160 MB/s.
The MXI-Express interface kit provides a 110 MB/s PCI Express to PCI bridge between the PC and the PXI chassis. Using the NI PXI-PCIe8362 dual-port interface kit, two PXI systems can be controlled simultaneously from the same PC. You can also use the MXI-Express interface to configure a multi-chassis PCI system in a star topology using 3- or 7-meter copper cables. This interface is compatible with x1, x4, x8, and x16 PCI Express slots, making this option suitable for most desktop computers. For more information about MXI-Express, refer to the MXI-Express Family User Manual. [page]
Figure 7b. Remote control using MXI-4 enables PC control of PXI and multi-chassis PXI systems
. The MXI-4 interface kit provides a 78 MB/s PCI-to-PCI bridge between a PC and a PXI system. The MXI-4 interface kit is available with low-cost copper cable links or fiber-optic links for long-distance and electrical isolation applications. As shown in Figure 7b, you can also use MXI-4 to create a multi-chassis PXI system. Using MXI-4 links, you can implement multi-chassis systems in daisy-chain or star topologies. For more information on multi-chassis configuration topologies, refer to the MXI-4 Family User Manual.
Using PXI external controllers, you can remotely control a PXI system from a desktop or laptop computer, thereby achieving the best processor performance at the lowest cost. Because all external control products are software transparent, no additional programming is required. You can purchase multiple desktop, workstation, or server computers and remotely control the PXI system using MXI-Express or MXI-4 serial links over copper or fiber-optic cables. For more information, refer to the NI "Controlling PXI via a PC" data page.
PXI Peripherals
Because PXI is an open industrial standard, there are currently more than 1,500 modules from more than 70 equipment manufacturers, and NI can provide more than 200 different PXI modules.
For more information about NI PXI modules, refer to the NI PXI Modules page. The following PXI pages provide a categorized list of modules provided by NI and its PXI product partners.
PXI provides the industry's highest bandwidth and lowest latency bus and modular I/O for a variety of applications, from high-resolution DC applications to 6 GHz RF applications. Because PXI is mostly compatible with CompactPCI, you can use many 3U or 6U form factor CompactPCI modules in a PXI or PXI Express system. In addition, you can use adapter modules to install CardBus/PCMCIA and PMC (PCI Mezzanine Card) boards in a PXI system. For example, with the NI PXI-8221 PC Card adapter module, you can connect CardBus and PCMCIA devices to a PXI system. NI provides a variety of PXI modules for instrumentation, data acquisition, switching, motion control, machine vision, advanced synchronization, and interfacing with other buses, and you can build a variety of PXI systems based on these modules.
PXI systems also support standard software and hardware for multiple bus communications, protecting your existing investments in stand-alone instruments or VXI systems. For example, there is no difference between connecting GPIB-based instruments to a PXI system using a PXI-GPIB module and directly controlling the instrument using a PCI-GPIB card. The same software is used for both methods. In addition, a variety of PXI and VXI interfacing methods are available. To learn more about hybrid systems, refer to the NI Developer Zone tutorial "Integrating LXI, USB, PXI Express, and Other Standards into a Hybrid Test System."
Software Architecture
Development and operation of Windows-based PXI systems differ little from development and operation of standard Windows-based PC systems. In addition, because the PXI backplane uses the industry-standard PCI bus, software programming for PXI modules is, in most cases, the same as for PCI boards. Therefore, there is no need to rewrite existing applications and sample code when porting PC-based programs to PXI systems.
PXI Express systems are also software compatible, protecting your existing software investments. Because PCI Express uses the same driver and operating system model as PCI, these specifications ensure software compatibility with PCI-based systems. Therefore, neither equipment vendors nor customers need to change drivers or application software to adapt to PCI Express-based systems.
Because PXI and PXI Express systems can use the same drivers as PCI, the software that controls the NI PXI-6251 multifunction data acquisition module is exactly the same as the software that controls the NI PCI-6251 board in a PC.
Figure 8. Two different packages use the same software standards. From a software perspective, communicating with a PXI module (bottom) is the same as communicating with a PCI card (top).
For applications with strict time determinism that require deterministic loop rates and headless operation (that is, without a keyboard, mouse, or monitor), a real-time software architecture can be an alternative to Windows-based systems. A real-time operating system helps you prioritize tasks so that the processor always takes care of the most important tasks when necessary. This results in highly predictable application execution with less jitter. For more information about PXI systems using LabVIEW Real-Time, visit ni.com/realtime. The
PXI specification defines a PXI system software framework based on the Microsoft Windows operating system. As a result, the controller can use industry-standard application programming interfaces such as NI LabVIEW, LabWindows™/CVI, Measurement Studio, Visual Basic, Visual C/C++, and others. PXI components require initialization files to define the system configuration and system functionality. Finally, the Virtual Instrument Software Architecture (VISA), which has been widely adopted in the instrumentation field, is required to configure and control VXI, GPIB, serial ports, and PXI instruments.
Summary
The PXI modular instrumentation system uses advanced technology in mainstream PCs to define a rugged computing platform that can be used for measurement and automation. The system also takes full advantage of standard PCI bus technology and benefits from widely used software and hardware components. The software programs and operating systems in the PXI system have long been used in everyday desktop PCs, so we are also familiar with them. PXI also adds rugged industrial packaging, a large number of I/O slots, and advanced timing and triggering capabilities to fully meet your application needs.
Keywords:PXI
Reference address:What is PXI?
PXI stands for PCI eXtensions for Instrumentation, which is a PC-based platform that provides high-performance, high-rugged, and low-cost configuration solutions for measurement and automation systems. PXI combines the PCI (Peripheral Component Interconnect) electrical bus with the rugged, modular European mechanical package in CompactPCI, and adds a dedicated synchronization bus and some key software features. PXI also adds some mechanical, electrical, and software features to define complete systems for test and measurement, data acquisition, and manufacturing applications. These systems provide services for applications such as production test, military and aerospace, machine monitoring, automation, and industrial testing.
NI developed and released the PXI specification in 1997 and launched it as an open industrial specification in 1998 to meet the growing demand for complex instrument systems. Currently, PXI is managed by the PXI Systems Alliance (PXISA), where more than 50 companies have joined together to promote the development of the standard, ensure interoperability, and maintain the PXI specification. Because PXI is an open standard, any equipment manufacturer can produce PXI products. And because a key feature of the PXI specification is interoperability with CompactPCI (a standard proposed by the PCI Industrial Computer Manufacturers Group (PICMG)), the same PXI system can contain both CompactPCI and PXI modules without any conflicts. In
late 2005, the commercial PC industry's bus technology evolved from PCI to PCI Express, which increased the available bus bandwidth. Similarly, the introduction of PXI Express technology in PXI also significantly increased bus bandwidth. PXI integrates PCI Express into the PXI standard to meet more application requirements. PCI Express technology can be integrated into the backplane while maintaining backward compatibility with existing systems with a broad application base. In addition to x1, x4, and x8 links, the system controller slot also supports up to x16 PCI Express links, providing up to 6GB/s bandwidth to the PXI Express backplane. Using PCI Express technology, PXI Express increases the available bandwidth in PXI by more than 45 times, from 132MB/s to 6GB/s, while maintaining software and hardware compatibility with PXI modules. This performance enhancement enables PXI to be used in many new application areas, many of which could only be achieved with expensive dedicated hardware before.
Hardware Architecture
PXI systems consist of three basic parts - chassis, system controller, and peripheral modules.
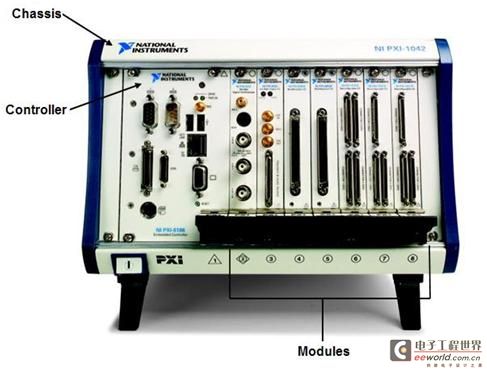
Figure 1. A standard 8-slot PXI chassis includes an embedded system controller and seven peripheral modules.
PXI Chassis
PXI chassis provide a rugged, modular package for systems, typically in 3U or 6U chassis with 4, 6, 8, 14, or 18 slots. A rack unit (U) is a unit of measurement used to describe the height of a device mounted in a 19- or 23-inch (width) rack. 1U is equal to 44.45 mm (1.75 inches). The size of the device mounted in the rack is usually described in U. Specialized chassis also offer options for AC or DC power and integrated signal conditioning. Many PXI Express chassis can accommodate both PXI and PXI Express peripherals, and some chassis with hybrid slots, such as the NI PXIe-1075, can accommodate PXI Express peripherals or hybrid-compatible PXI devices. These chassis allow a variety of PXI systems to be configured to meet application needs.
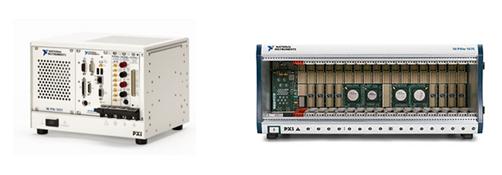
Figure 2. Optional standard chassis include NI PXI-1031 (left) and NI PXIe-1075 (right). NI PXI-1031 can choose DC power supply, and NI PXIe-1075 has 18 slots for plugging system controllers and peripherals. The
chassis has a high-performance PXI backplane, which includes PCI bus, timing bus and trigger bus. The PXI modular instrument system adds a dedicated 10MHz system reference clock, PXI trigger bus, star trigger bus and local bus between slots, so as to meet the needs of applications such as advanced timing, synchronization and direct communication between adjacent slots while maintaining all the advantages of PCI bus.
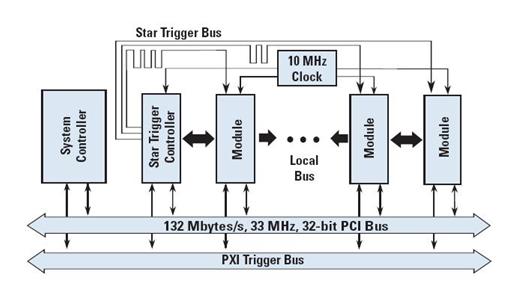
Figure 3. PXI Timing and Triggering Bus – PXI combines industry-standard PC components (such as the PCI bus) with advanced triggering and synchronization extensions on its backplane.
Building on the capabilities of PXI, PXI Express provides additional timing and synchronization capabilities—a 100MHz differential system clock, differential signaling, and a differential star trigger bus. With differential clocking and synchronization, the noise immunity of instrument clocks in a PXI Express system is further improved, and data can be transmitted at higher rates.
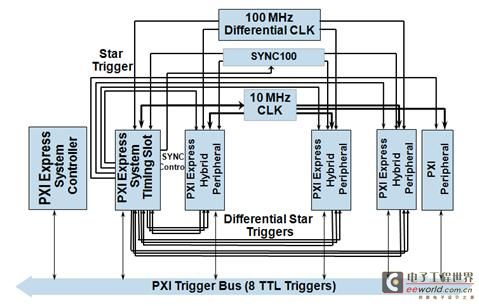
Figure 4. The PXI Express timing and triggering bus extends the PXI bus timing and triggering bus capabilities and adds differential system clocks, differential signaling, and differential star triggers to the backplane.
Using these timing and triggering buses, you can develop systems with precise synchronization to meet your application needs. To learn more about the PXI timing and triggering bus specifications, refer to the NI Developer Zone document "PXI Specification Guide."
To learn more about timing and synchronization concepts, refer to the NI Developer Zone guide "Introduction to Distributed Clock Synchronization and IEEE 1588 Precision Clock Synchronization Protocol." [page]
PXI Controllers
Most PXI chassis include a system controller slot in the left-most slot (Slot 1). When choosing the best system controller for your application, you have several options, including an external controller using a desktop, workstation, server, or laptop computer, or a high-performance embedded controller with a Microsoft operating system (Windows Vista/XP) or a real-time operating system (LabVIEW Real-Time). There are two types of external controllers: controlling PXI from a laptop or controlling PXI from a PC.
PXI Embedded Controllers – Embedded controllers eliminate the need for an external PC, making the PXI chassis a complete system. These embedded controllers have standard features such as an integrated CPU, hard drive, RAM, Ethernet, video output, keyboard/mouse, serial, USB, and other peripherals, as well as Microsoft Windows and all device drivers already installed. These features are included with PXI or PXI Express-based systems; you can also choose your operating system, including Windows Vista/XP or LabVIEW Real-Time.
PXI embedded controllers generally use standard PC components in a small PXI package. For example, the NI PXI-8108 controller has a 2.53 GHz Intel Core 2 Duo T9400 dual-core processor, optional hard drive or solid-state drive, and standard PC peripherals such as high-speed USB, Ethernet, serial, and parallel ports.
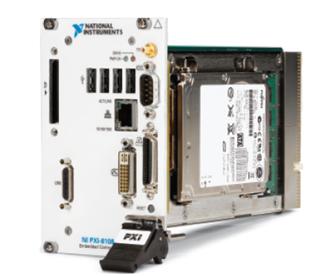
Figure 5. The NI PXI-8108 controller includes a 2.53 GHz Intel Core 2 Duo T9400 dual-core processor embedded controller Embedded controllers
are ideal for portable systems and "single box" applications where you want to easily move the system from one location to another. For more information, refer to the NI "PXI Controllers" data sheet.
Controlling PXI from a Laptop – Using the NI ExpressCard MXI (Measurement eXtensions for Instrumentation) and PCMCIA CardBus interface kit, you can control a PXI system directly from a laptop through a software-transparent link connection. When powered on, the laptop assumes that all peripheral modules in the PXI system are PCI boards, and you can then control these devices from the laptop. Controlling PXI from a laptop requires inserting an ExpressCard/PCMCIA CardBus card into the laptop and inserting a PXI/PXI Express link module into slot 1 of the PXI chassis, with copper cables connecting the two.
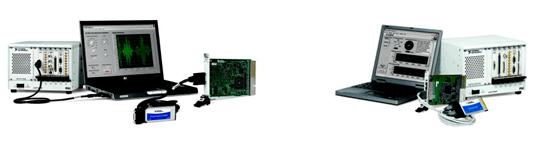
NI ExpressCard MXI Interface Kit PCMCIA CardBus Interface Kit
Figure 6. Controlling PXI from a Laptop
The NI ExpressCard MXI Interface Kit provides a 110 MB/s PCI Express to PCI bridge between a laptop and a PXI chassis. The PCMCIA CardBus Interface Kit provides a 50 MB/s PCI to PCI bridge between a laptop and a PXI chassis. This allows for mobile/portable PXI systems to be controlled from a laptop. Any NI ExpressCard MXI or PCMCIA CardBus-compatible laptop can be used to remotely control a PXI system. For more information, refer to the NI “Controlling PXI from a Laptop” information sheet.
PC Control of PXI – With the NI MXI-Express and MXI-4 interface kits, you can control a PXI system directly from a desktop, workstation, or server computer. You can control a PXI system from a PC through a software-transparent and driver-transparent link. At power-up, the computer system assumes that all peripheral modules in the PXI system are PCI cards, so you can access these devices through the controller. To control PXI through a PC, you need to insert a PCI/PCI Express board into the computer and a PXI/PXI Express module into the first slot of the PXI chassis. The two are connected with a copper cable or fiber optic cable.
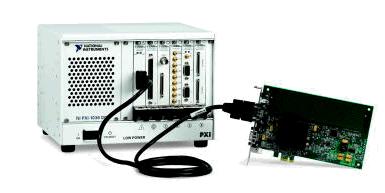
Figure 7a. Remote control using dual-port MXI-Express can control two PXI chassis simultaneously with a total throughput of 160 MB/s.
The MXI-Express interface kit provides a 110 MB/s PCI Express to PCI bridge between the PC and the PXI chassis. Using the NI PXI-PCIe8362 dual-port interface kit, two PXI systems can be controlled simultaneously from the same PC. You can also use the MXI-Express interface to configure a multi-chassis PCI system in a star topology using 3- or 7-meter copper cables. This interface is compatible with x1, x4, x8, and x16 PCI Express slots, making this option suitable for most desktop computers. For more information about MXI-Express, refer to the MXI-Express Family User Manual. [page]
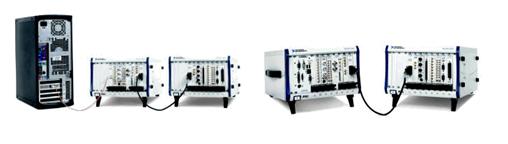
Figure 7b. Remote control using MXI-4 enables PC control of PXI and multi-chassis PXI systems
. The MXI-4 interface kit provides a 78 MB/s PCI-to-PCI bridge between a PC and a PXI system. The MXI-4 interface kit is available with low-cost copper cable links or fiber-optic links for long-distance and electrical isolation applications. As shown in Figure 7b, you can also use MXI-4 to create a multi-chassis PXI system. Using MXI-4 links, you can implement multi-chassis systems in daisy-chain or star topologies. For more information on multi-chassis configuration topologies, refer to the MXI-4 Family User Manual.
Using PXI external controllers, you can remotely control a PXI system from a desktop or laptop computer, thereby achieving the best processor performance at the lowest cost. Because all external control products are software transparent, no additional programming is required. You can purchase multiple desktop, workstation, or server computers and remotely control the PXI system using MXI-Express or MXI-4 serial links over copper or fiber-optic cables. For more information, refer to the NI "Controlling PXI via a PC" data page.
PXI Peripherals
Because PXI is an open industrial standard, there are currently more than 1,500 modules from more than 70 equipment manufacturers, and NI can provide more than 200 different PXI modules.
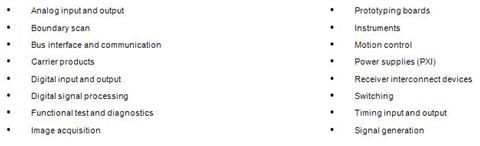
For more information about NI PXI modules, refer to the NI PXI Modules page. The following PXI pages provide a categorized list of modules provided by NI and its PXI product partners.
PXI provides the industry's highest bandwidth and lowest latency bus and modular I/O for a variety of applications, from high-resolution DC applications to 6 GHz RF applications. Because PXI is mostly compatible with CompactPCI, you can use many 3U or 6U form factor CompactPCI modules in a PXI or PXI Express system. In addition, you can use adapter modules to install CardBus/PCMCIA and PMC (PCI Mezzanine Card) boards in a PXI system. For example, with the NI PXI-8221 PC Card adapter module, you can connect CardBus and PCMCIA devices to a PXI system. NI provides a variety of PXI modules for instrumentation, data acquisition, switching, motion control, machine vision, advanced synchronization, and interfacing with other buses, and you can build a variety of PXI systems based on these modules.
PXI systems also support standard software and hardware for multiple bus communications, protecting your existing investments in stand-alone instruments or VXI systems. For example, there is no difference between connecting GPIB-based instruments to a PXI system using a PXI-GPIB module and directly controlling the instrument using a PCI-GPIB card. The same software is used for both methods. In addition, a variety of PXI and VXI interfacing methods are available. To learn more about hybrid systems, refer to the NI Developer Zone tutorial "Integrating LXI, USB, PXI Express, and Other Standards into a Hybrid Test System."
Software Architecture
Development and operation of Windows-based PXI systems differ little from development and operation of standard Windows-based PC systems. In addition, because the PXI backplane uses the industry-standard PCI bus, software programming for PXI modules is, in most cases, the same as for PCI boards. Therefore, there is no need to rewrite existing applications and sample code when porting PC-based programs to PXI systems.
PXI Express systems are also software compatible, protecting your existing software investments. Because PCI Express uses the same driver and operating system model as PCI, these specifications ensure software compatibility with PCI-based systems. Therefore, neither equipment vendors nor customers need to change drivers or application software to adapt to PCI Express-based systems.
Because PXI and PXI Express systems can use the same drivers as PCI, the software that controls the NI PXI-6251 multifunction data acquisition module is exactly the same as the software that controls the NI PCI-6251 board in a PC.
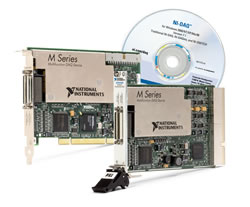
Figure 8. Two different packages use the same software standards. From a software perspective, communicating with a PXI module (bottom) is the same as communicating with a PCI card (top).
For applications with strict time determinism that require deterministic loop rates and headless operation (that is, without a keyboard, mouse, or monitor), a real-time software architecture can be an alternative to Windows-based systems. A real-time operating system helps you prioritize tasks so that the processor always takes care of the most important tasks when necessary. This results in highly predictable application execution with less jitter. For more information about PXI systems using LabVIEW Real-Time, visit ni.com/realtime. The
PXI specification defines a PXI system software framework based on the Microsoft Windows operating system. As a result, the controller can use industry-standard application programming interfaces such as NI LabVIEW, LabWindows™/CVI, Measurement Studio, Visual Basic, Visual C/C++, and others. PXI components require initialization files to define the system configuration and system functionality. Finally, the Virtual Instrument Software Architecture (VISA), which has been widely adopted in the instrumentation field, is required to configure and control VXI, GPIB, serial ports, and PXI instruments.
Summary
The PXI modular instrumentation system uses advanced technology in mainstream PCs to define a rugged computing platform that can be used for measurement and automation. The system also takes full advantage of standard PCI bus technology and benefits from widely used software and hardware components. The software programs and operating systems in the PXI system have long been used in everyday desktop PCs, so we are also familiar with them. PXI also adds rugged industrial packaging, a large number of I/O slots, and advanced timing and triggering capabilities to fully meet your application needs.
Previous article:Software and hardware design based on grating sensor displacement measurement
Next article:Design of a high-precision digitally controlled bipolar constant current source circuit
Recommended ReadingLatest update time:2024-11-16 20:24
Developing Instruments to Analyze Energy Storage Device Characteristics Using PXI Hardware
Renewable energy is one of the fastest growing markets in the world today. Energy storage technologies play a key role in “green” energy generation sources such as wind, solar and biomass. Public and private funding for energy storage is skyrocketing, driving an unprecedented amount of research into new batteries, c
[Test Measurement]
Recommended Content
Latest Test Measurement Articles
- Keysight Technologies Helps Samsung Electronics Successfully Validate FiRa® 2.0 Safe Distance Measurement Test Case
- From probes to power supplies, Tektronix is leading the way in comprehensive innovation in power electronics testing
- Seizing the Opportunities in the Chinese Application Market: NI's Challenges and Answers
- Tektronix Launches Breakthrough Power Measurement Tools to Accelerate Innovation as Global Electrification Accelerates
- Not all oscilloscopes are created equal: Why ADCs and low noise floor matter
- Enable TekHSI high-speed interface function to accelerate the remote transmission of waveform data
- How to measure the quality of soft start thyristor
- How to use a multimeter to judge whether a soft starter is good or bad
- What are the advantages and disadvantages of non-contact temperature sensors?
MoreSelected Circuit Diagrams
MorePopular Articles
- Innolux's intelligent steer-by-wire solution makes cars smarter and safer
- 8051 MCU - Parity Check
- How to efficiently balance the sensitivity of tactile sensing interfaces
- What should I do if the servo motor shakes? What causes the servo motor to shake quickly?
- 【Brushless Motor】Analysis of three-phase BLDC motor and sharing of two popular development boards
- Midea Industrial Technology's subsidiaries Clou Electronics and Hekang New Energy jointly appeared at the Munich Battery Energy Storage Exhibition and Solar Energy Exhibition
- Guoxin Sichen | Application of ferroelectric memory PB85RS2MC in power battery management, with a capacity of 2M
- Analysis of common faults of frequency converter
- In a head-on competition with Qualcomm, what kind of cockpit products has Intel come up with?
- Dalian Rongke's all-vanadium liquid flow battery energy storage equipment industrialization project has entered the sprint stage before production
MoreDaily News
- Allegro MicroSystems Introduces Advanced Magnetic and Inductive Position Sensing Solutions at Electronica 2024
- Car key in the left hand, liveness detection radar in the right hand, UWB is imperative for cars!
- After a decade of rapid development, domestic CIS has entered the market
- Aegis Dagger Battery + Thor EM-i Super Hybrid, Geely New Energy has thrown out two "king bombs"
- A brief discussion on functional safety - fault, error, and failure
- In the smart car 2.0 cycle, these core industry chains are facing major opportunities!
- The United States and Japan are developing new batteries. CATL faces challenges? How should China's new energy battery industry respond?
- Murata launches high-precision 6-axis inertial sensor for automobiles
- Ford patents pre-charge alarm to help save costs and respond to emergencies
- New real-time microcontroller system from Texas Instruments enables smarter processing in automotive and industrial applications
Guess you like
- 2020 Global Engineering Survey: Better understanding of engineers at work (first World Engineering Day)
- The college entrance examination is over, but we are still in the "high-school" mode
- 【Arduino】168 Sensor Series Experiments (211) --- WS2812B Ring 93 Light Module
- The dry goods in the jar are worth the quick surfing ANT series
- Matching of vivado version and modelsim version
- I have some questions about project handover (software) at work. I hope experienced seniors can give me some guidance.
- Learn about RF MEMS switches in one article
- CC2541 Bluetooth Learning-Clock Setting
- Dismantle ABC and CCB U-Shield
- How to view MSP430 technical data