Korry Electronics uses the power of virtual instrumentation to design the control panel used on the Boeing 787 Dreamliner
"We can quickly develop new test software using LabVIEW and have unlimited control over CAN bus data. The PXI-CAN card is very easy to configure and has a high degree of operational reliability."
- Allen Cutler, Korry Electronics
challenge:
Develop a CAN bus test system to interact with the control panel of intelligent avionics equipment, display switch status, control panel lighting functions, and report panel status data such as part number and serial number.
Solution:
Using NI's LabVIEW for rapid development, the NI PXI-CAN board is equipped with a ready-to-use NI LabVIEW driver library, and NI TestStand is used to manage production test steps and automatically generate reports.
author:
Allen Cutler - Korry Electronics
We at Korry Electronics needed a solution to test a range of control panels for the flight consoles of the new Boeing 787 aircraft. We needed to meet the aggressive timeline for the project - just 16 months, shorter than any previous Boeing aircraft development program. The core of the 787 system uses an open architecture, so it will be simpler than existing aircraft and provide improved functionality. One example is the condition monitoring system, which will monitor itself and report maintenance needs to a computer system on the ground.
In the aviation industry, control panel suppliers are looking for low-cost alternatives to the ARINC-429 bus, and due to the need for high-speed bus bandwidth and data payload, they are gradually turning to CAN-based solutions. We need to communicate with and monitor multiple CAN buses on each device under test to obtain correct CAN data and send control data to adjust lighting and set other panel functions. We chose NI's LabVIEW, which is compatible with NI PXI-CAN boards and easy-to-use NI LabVIEW driver libraries, and can be quickly developed according to project requirements.
The control panel sends discrete digital switch data and a unique data word that represents the position of each switch. For control panels that contain rotary potentiometers and encoders, the data value will increase or decrease depending on the direction of rotation. The CAN data word sets the lighting level of all control panels and uses switch commands to set the control panel indicators. In production testing, we test one control panel at a time. For quality testing, we configure the NI PXI test system to test multiple control panels simultaneously over the CAN bus.
Hardware and system structure
The test system hardware consists of two NI PXI-8461/2 CAN interfaces installed in a PXI chassis along with multiple relay boards, power supplies, and DMM cards. The system can monitor four independent CAN buses and all discrete I/O and DC power simultaneously. Each control panel sends a unique CAN bus ID for use by the LabVIEW program. This allows the test system to simulate a CAN bus data hub used on an aircraft.
The test software was written entirely in LabVIEW, with the NI-CAN driver integrated into a custom subroutine to initialize the CAN port at a specific CAN address and read the CAN bus data frame. We also created a subroutine to compare the received data with the expected data frame. For each CAN bus session, the CAN and object network interfaces are first opened and set, followed by the CAN read operation, and finally the session is closed. For the lighting function, the specified CAN data is sent to the control panel. We also wrote a program to monitor the switch position in real time, while monitoring the CAN data of each panel, and once a change is detected, the timestamp data will be written to the log file.
In production testing, we use NI TestStand to control the test sequence and generate test result reports. The first step is to prompt the operator to set each switch, rotary potentiometer, and encoder to a specified position. The test software panel will graphically display the position of each switch on the UUT. The second step is to create an HTML log file to record the error data during the test. In one scenario, all indicators on the control panel are fully illuminated, allowing the operator to visually check whether the indicators are illuminated correctly. We created a subroutine to send CAN messages to illuminate the control panel, and can use the LabVIEW dial to send CAN data to control the brightness level in real time, from no brightness to full brightness level. In another scenario, the operator clicks on the test software panel to individually command each indicator to light up by sending CAN messages to the control panel.
Conclusion and Outlook
We have successfully developed a series of complex CAN-based control panels for the Boeing 787 aircraft using NI hardware and software. We can quickly develop new test software using LabVIEW and have unlimited control over CAN bus data. The PXI-CAN card is very easy to configure and has a high degree of operational reliability. We will use NI test hardware and software to develop test instruments for those who need to complete development quickly and efficiently in the next few years.
Previous article:NI provides communications test equipment to the U.S. Navy
Next article:Implementing a Customized Functional Circuit Test System with LabVIEW
Recommended ReadingLatest update time:2024-11-16 16:50
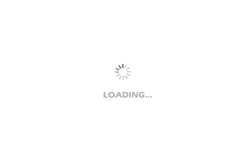
- Popular Resources
- Popular amplifiers
- Keysight Technologies Helps Samsung Electronics Successfully Validate FiRa® 2.0 Safe Distance Measurement Test Case
- From probes to power supplies, Tektronix is leading the way in comprehensive innovation in power electronics testing
- Seizing the Opportunities in the Chinese Application Market: NI's Challenges and Answers
- Tektronix Launches Breakthrough Power Measurement Tools to Accelerate Innovation as Global Electrification Accelerates
- Not all oscilloscopes are created equal: Why ADCs and low noise floor matter
- Enable TekHSI high-speed interface function to accelerate the remote transmission of waveform data
- How to measure the quality of soft start thyristor
- How to use a multimeter to judge whether a soft starter is good or bad
- What are the advantages and disadvantages of non-contact temperature sensors?
- Innolux's intelligent steer-by-wire solution makes cars smarter and safer
- 8051 MCU - Parity Check
- How to efficiently balance the sensitivity of tactile sensing interfaces
- What should I do if the servo motor shakes? What causes the servo motor to shake quickly?
- 【Brushless Motor】Analysis of three-phase BLDC motor and sharing of two popular development boards
- Midea Industrial Technology's subsidiaries Clou Electronics and Hekang New Energy jointly appeared at the Munich Battery Energy Storage Exhibition and Solar Energy Exhibition
- Guoxin Sichen | Application of ferroelectric memory PB85RS2MC in power battery management, with a capacity of 2M
- Analysis of common faults of frequency converter
- In a head-on competition with Qualcomm, what kind of cockpit products has Intel come up with?
- Dalian Rongke's all-vanadium liquid flow battery energy storage equipment industrialization project has entered the sprint stage before production
- Allegro MicroSystems Introduces Advanced Magnetic and Inductive Position Sensing Solutions at Electronica 2024
- Car key in the left hand, liveness detection radar in the right hand, UWB is imperative for cars!
- After a decade of rapid development, domestic CIS has entered the market
- Aegis Dagger Battery + Thor EM-i Super Hybrid, Geely New Energy has thrown out two "king bombs"
- A brief discussion on functional safety - fault, error, and failure
- In the smart car 2.0 cycle, these core industry chains are facing major opportunities!
- The United States and Japan are developing new batteries. CATL faces challenges? How should China's new energy battery industry respond?
- Murata launches high-precision 6-axis inertial sensor for automobiles
- Ford patents pre-charge alarm to help save costs and respond to emergencies
- New real-time microcontroller system from Texas Instruments enables smarter processing in automotive and industrial applications
- Analysis of the three most commonly used communication protocols in single-chip microcomputer systems
- MSP-EXP430F5529LP Development Board 001-GPIO
- Chip type and model
- Several modes of Bluetooth devices
- Acknowledgements | EEWorld’s 15th anniversary, thank you!
- How to set subdivision of stepper motor driver
- LDO and DC-DC Simple Comparison and Selection
- Answer the questions to win prizes! ADI Application Tour - Industrial Large Machine Health Edition
- [2022 Digi-Key Innovation Design Competition] 2. Draw an interface
- IVD in vitro diagnostics + medical beauty products