At present, the detection principles adopted by the insulation detection device mainly include the bridge balance principle and the frequency conversion detection principle. The devices based on the two detection principles can solve the DC grounding problem to a certain extent, but there are also shortcomings. The insulation detection device based on the bridge balance principle cannot detect the situation where the insulation of the positive and negative busbars decreases equally, nor can it distinguish between multi-branch faults. The latter is easily affected by the distributed capacitance of the DC system to the ground, and the injected low-frequency AC signal increases the voltage ripple coefficient of the DC system, affecting the quality of the power supply. This paper aims to introduce an online insulation detection method and implement it based on the msp430 microcontroller.
1 Principle Introduction
The schematic diagram is shown in Figure 1. In the figure, CM+ and CM- are positive and negative busbars. U+ and U- are the positive and negative bus voltages. Jk1 and Jk2 are relay switches, and R is a precision resistor. R+ and R- are the resistance to ground when insulation failure occurs in the positive and negative bus. Dt1 and Dt2 are high-precision Hall current sensors, whose output voltage is proportional to the current difference passing through the annular hole and is in a linear relationship. Therefore, the voltage output by the sampling current sensor is converted into current, and then Ohm's law is used to obtain the positive and negative bus voltages U+ and U-, then the power supply voltage U=U+ - U-.
Under normal operation of the DC system, the electronic relay switches Jk1 and Jk2 remain closed. R+ and R- generally approach infinity, at which point U+=-U-. When an insulation grounding fault occurs, R+ or R- is a finite value, at which point U+≠-U-. When R+≤R-, then U+≤-U-, and vice versa. If R+=R- are both finite values, that is, the insulation resistance of the positive and negative busbars decreases equally, at which point U+=-U-, further testing is required. The testing steps are as follows:
1) Disconnect the relay switch Jk2 and keep Jk1 closed. The measured positive and negative busbar voltages to ground are recorded as: U+1, U-1 respectively;
2) Disconnect the relay switch Jk1 and keep Jk2 closed. The measured positive and negative busbar voltages to ground are recorded as: U+2, U-2 respectively;
[page]
It should be noted here that the current range of the Hall current sensor used here is 0-10 mA, so for a general DC 220 V power supply, combined with the accuracy of the current sensor, the precision resistor R is generally selected to be 20-100 kΩ.
2 Hardware Implementation
2.1 Insulation Main Circuit
The specific implementation circuit diagram is shown in Figure 2.
A brief description of the usage of the electronic relay AQW214 is as follows: when pins 1 and 2 of AQW214 are turned on, pins 7 and 8 are also turned on, and the internal resistance of the conduction is very small; similarly, when pins 3 and 4 are turned on, pins 5 and 6 are also turned on. The withstand voltage of AQW214 can reach 400 V, that is, when pins 7 and 8 or pins 5 and 6 are turned on, the two ends can withstand a voltage of 400 V, so the conduction of the electronic relay can be controlled by the P10 and P11 pins of the microcontroller to achieve the control of the on and off of Jk1 and Jk2. The specific control and implementation process has been described in the previous article and will not be repeated here.
It should be noted that the values calibrated in the figure are only applicable to a certain power supply voltage range (24 to 300 V). If the power supply voltage is too low, it is easily affected by the accuracy of the Hall current sensor and the measurement is inaccurate. If it is too high, it will exceed the current range of the Hall sensor and the withstand voltage value of the electronic relay. Therefore, according to the actual situation, appropriate devices can be replaced to meet the requirements.
2.2 Insulated branches
Formula (1) can be used to calculate whether an insulation reduction fault has occurred in the DC system, but it is still necessary to determine whether a grounding fault has occurred in the distribution bus or in one or more feeder branches.
[page]
As shown in Figure 3, when there is no ground fault in the branch, the branch feeder current I0=I1, the current difference through the current sensor is 0, and its output voltage is also 0; when a ground fault occurs, I3=I0-I1 is not 0, and the current sensor output voltage is not 0. Assume that the positive and negative bus voltages are U+ and U- at this time. Then the ground resistance of the nth branch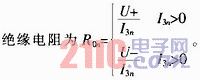
For multiple branches, a multi-way switch such as CD4051 can be used for gating control. As shown in Figure 4, when a branch insulation ground fault occurs, the detection system starts the branch insulation resistance inspection program, sends signals to the A, B, and C pins of the CD4051 chip through the single-chip microcomputer, selects the branches in turn, checks the number of faulty branches, and calculates the ground resistance. (In the figure, the COM end is connected to an analog circuit connected to the AD sampling port of the single-chip microcomputer, which is omitted here).
3 Conclusion
The insulation detection method introduced in this article has achieved good results in practical applications. It can not only solve the problem of equal drop of positive and negative busbars, but also does not affect the power quality, meeting the requirements of the initial design. However, after a long period of practice, some shortcomings have been found. The most prominent one is that the current sensor is prone to zero-point drift of leakage current when it is used for a long time and is affected by the electromagnetic environment of the surrounding environment. It needs to be corrected in the software or zero-point calibration is performed after the branch is powered off, otherwise, it is easy to miss or report a false alarm. However, considering that both have certain disadvantages in practical applications, the author is doing further research in the hope of improvement.
Previous article:Application of AD736 in intelligent monitoring of locomotive signals
Next article:How to Use a Radio as a Metal Detector
- Popular Resources
- Popular amplifiers
- Keysight Technologies Helps Samsung Electronics Successfully Validate FiRa® 2.0 Safe Distance Measurement Test Case
- From probes to power supplies, Tektronix is leading the way in comprehensive innovation in power electronics testing
- Seizing the Opportunities in the Chinese Application Market: NI's Challenges and Answers
- Tektronix Launches Breakthrough Power Measurement Tools to Accelerate Innovation as Global Electrification Accelerates
- Not all oscilloscopes are created equal: Why ADCs and low noise floor matter
- Enable TekHSI high-speed interface function to accelerate the remote transmission of waveform data
- How to measure the quality of soft start thyristor
- How to use a multimeter to judge whether a soft starter is good or bad
- What are the advantages and disadvantages of non-contact temperature sensors?
- Innolux's intelligent steer-by-wire solution makes cars smarter and safer
- 8051 MCU - Parity Check
- How to efficiently balance the sensitivity of tactile sensing interfaces
- What should I do if the servo motor shakes? What causes the servo motor to shake quickly?
- 【Brushless Motor】Analysis of three-phase BLDC motor and sharing of two popular development boards
- Midea Industrial Technology's subsidiaries Clou Electronics and Hekang New Energy jointly appeared at the Munich Battery Energy Storage Exhibition and Solar Energy Exhibition
- Guoxin Sichen | Application of ferroelectric memory PB85RS2MC in power battery management, with a capacity of 2M
- Analysis of common faults of frequency converter
- In a head-on competition with Qualcomm, what kind of cockpit products has Intel come up with?
- Dalian Rongke's all-vanadium liquid flow battery energy storage equipment industrialization project has entered the sprint stage before production
- Allegro MicroSystems Introduces Advanced Magnetic and Inductive Position Sensing Solutions at Electronica 2024
- Car key in the left hand, liveness detection radar in the right hand, UWB is imperative for cars!
- After a decade of rapid development, domestic CIS has entered the market
- Aegis Dagger Battery + Thor EM-i Super Hybrid, Geely New Energy has thrown out two "king bombs"
- A brief discussion on functional safety - fault, error, and failure
- In the smart car 2.0 cycle, these core industry chains are facing major opportunities!
- The United States and Japan are developing new batteries. CATL faces challenges? How should China's new energy battery industry respond?
- Murata launches high-precision 6-axis inertial sensor for automobiles
- Ford patents pre-charge alarm to help save costs and respond to emergencies
- New real-time microcontroller system from Texas Instruments enables smarter processing in automotive and industrial applications
- 1. RS232 communication circuit
- macropad keyboard
- DSP Development Trend
- Regarding the built-in pull-up resistor when MSP430 IO is used as input!
- Help, where can I find a high frequency magnetic core that supports 300MHz
- LSM303AH Code and PCB Library
- [ATmega4809 Curiosity Nano Review] Unboxing
- [CY8CKIT-149 PSoC 4100S Review] + Use of Timer/Counter
- The register value returned by the lis25ba operation is incorrect
- About the frequency signal source